by Imperial Systems | Oct 26, 2016 | Uncategorized
OSHA just released the first guidelines and recommended practices list in more than twenty years. Is it something you need to know about? Probably. But you probably don’t have a few hours to spend browsing their website for information. Save yourself some time. Here’s a summary of the important parts, and links to get you to the ones you want to know more about.
OSHA Guidelines and Recommended Practices
Getting Started
First off, here’s a quick guide to the process of implementing recommended practices:
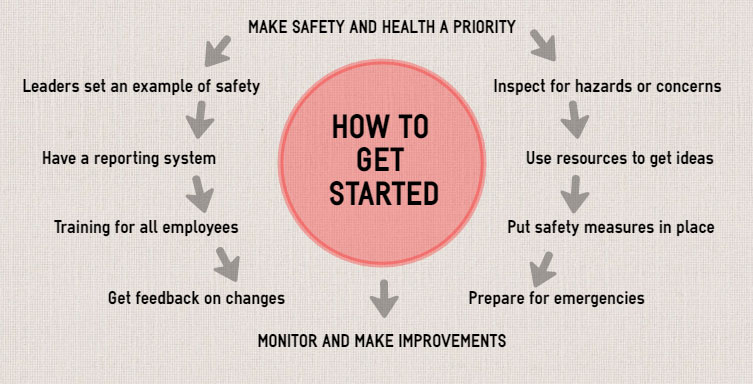
There are two areas of focus here: preparing and training people, and inspecting and improving facilities, equipment, and practices. If you need some more details, head to this link: https://www.osha.gov/shpguidelines/ten-easy-things.html
Getting Management to Work With You
You’re going to have a hard time getting a safety program off the ground if management isn’t buying in. The OSHA guidelines recommend four basic steps below to make sure they’re with you:
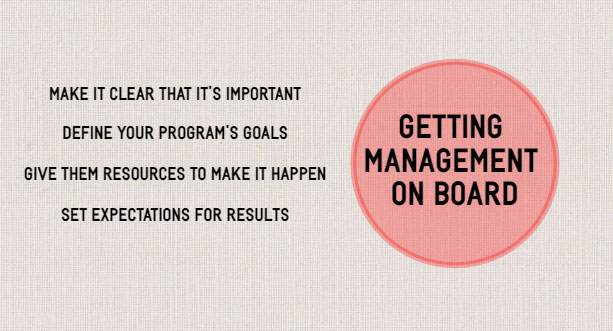
If you need more details about things you should do to get management and leadership engaged, this is your place to look: https://www.osha.gov/shpguidelines/management-leadership.html
Getting Workers Involved
If getting your workers to be involved and serious about your safety program is a concern, here are suggested steps in the OSHA guidelines to make sure you have genuine worker investment:
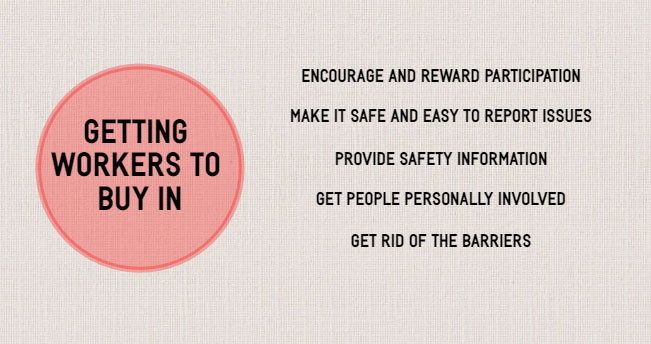
So what does it take to get workers to care about and want to participate in your safety program? And what are some of the barriers to their participation? If this is a topic you’re interested in, here’s the place to go: https://www.osha.gov/shpguidelines/worker-participation.html
Hazard Identification, Control, and Prevention
Before you can do anything about hazards in your workplace, you have to find them. Not just the obvious ones, either: there may be hazards that only people who use a particular machine or work in a particular area are aware of, for example.
Once you’ve identified the hazards that need to be addressed, what do you do about them? You look for ways to control them, starting with the most dangerous or the ones that can be easily eliminated. Getting workers involved in deciding what controls you’ll use is also a great step to get them more active in the program.
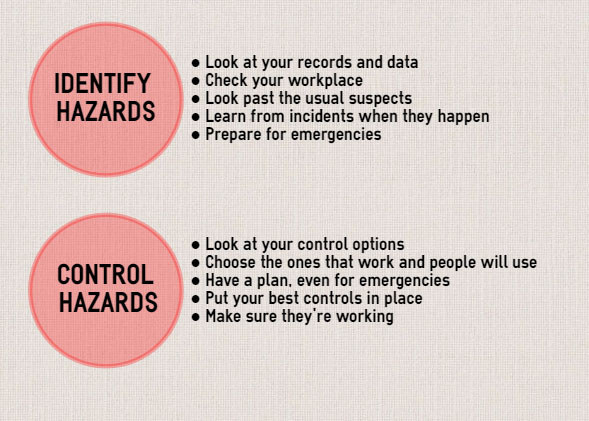
These are obviously the nuts and bolts of a safety program, but they don’t work if you haven’t gotten managers and workers on board and involved. Workers are probably the people most likely to know where the real hazards are and where things might go wrong, but they’re not likely to want to talk about it with management you’ve established a program where reporting a hazard is encouraged, not punished.
If hazard identification is your topic, check here: https://www.osha.gov/shpguidelines/hazard-Identification.html
If you’re moving past identification and ready to tackle prevention and control, this is your destination: https://www.osha.gov/shpguidelines/hazard-prevention.html
Education and Training
You can have a great program, but if nobody knows what to do or who should handle what part, you’re not going to get anywhere. Here’s the very basic breakdown:
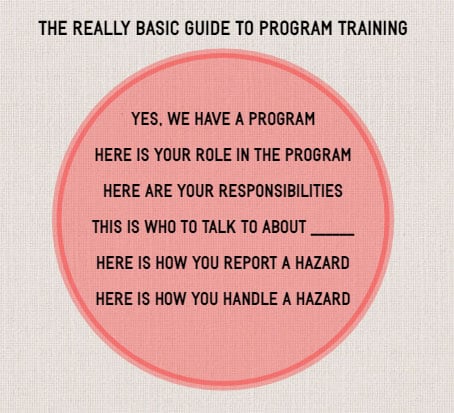
OK, you’re probably going to need to get a little more in-depth than this. Fortunately, OSHA has some handy resources available, including training tools to help people get better at spotting hazards: https://www.osha.gov/shpguidelines/education-training.html
Program Evaluation and Improvement
So you started a program, and you got everyone to participate, and things seem to be going really well. Or perhaps your program, for whatever reason, isn’t doing what you hoped it would do. Evaluation is the part where you figure out what’s going well and what’s not. And improvement is the part where you do more of what’s working and less of what isn’t.
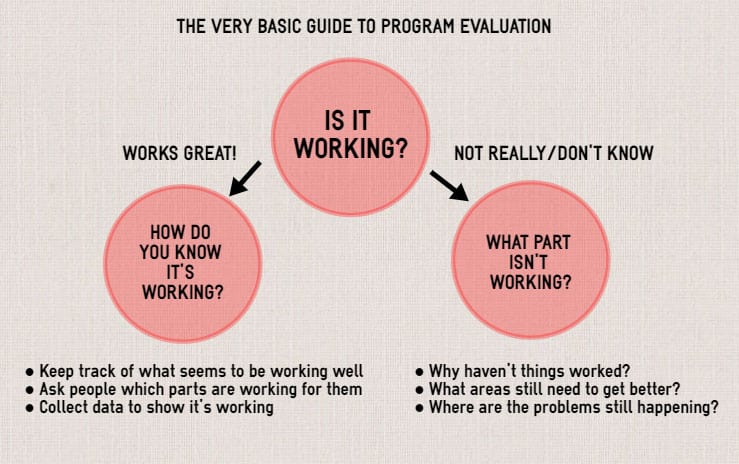
If you’re working on a safety program and need to be able to report on how it’s going and what it’s doing for the company, check out OSHA’s suggestions and tools for figuring it out: https://www.osha.gov/shpguidelines/program-evaluation.html
Additional OSHA Guidelines Information and Assistance
There’s your very quick summary of OSHA Guidelines and Recommended Practices! If you need lots and lots more information, OSHA makes sure you have tons of links and helpful tools to check out on their “additional resources” page here: https://www.osha.gov/shpguidelines/program-evaluation.html.
As always, if you are looking for dust and fume collection or fire and explosion safety controls, we are here to help you with any information you need. Using this equipment is a best practice for dealing with combustible dust, including spark arrestors, abort gates, and fire retardant dust collector filters.
DISCLAIMER: This guide is not intended to be used in place of OSHA guidelines or actual recommendations. We hope it helps you get an overview of what’s available, but while we are dust and fume collection experts, we defer to those more knowledgeable when it comes to safety program design.
Read more
by Imperial Systems | Oct 24, 2016 | Uncategorized
Extinguish the Threat of Explosions with a Spark Arrestor
It’s imperative that every metalworking facility have highly efficient dust collection systems. Also, it’s crucial that metalworking facilities utilize a spark arrestor to provide even greater protection from these combustible hazards. Here’s why a Spark Trap safety system by Imperial Systems is the best choice.
We have dedicated over 15 years to preventing and reducing fires and explosions in metalworking and manufacturing facilities. We also continually strive to meet and exceed the standards recommended by the Occupational Safety and Health Administration. Our company also meets NFPA guidelines with our highly efficient dust collection systems and replacement cartridge filters.
If you’re asking yourself if a spark arrestor is really necessary, the answer is yes! First of all, consider the findings of OSHA’s National Emphasis Program. It shows that metal dust accounts for 20% of explosions nationwide. Also, 7% of ignition sources are ignited by fabricated metals. Further, another 8% of ignition sources are caused by primary metals. So, if you want to reduce the possibility of an accident at your metalworking facility, you MUST invest in spark arrestors!
How can Spark Trap safety systems reduce explosions?
Adding a spark arrestor to your industrial dust collection system is like adding a security system to your home. That is, you already have the proper amount of protection with locks. But installing a security system in your home provides another line of defense. Above all, it keeps you and your family safe.
Our spark arrestor, named Spark Trap, is the first line of defense in protecting your metal fabricators and your metalworking facility from explosions. Spark Traps extinguish nearly every spark before it enters the main containment unit where combustible dust and other flammable material collect. When you choose our Spark Traps, you’ll receive a quality product. We make it with heavy-duty materials and it’s highly effective at keeping sparks from entering your industrial dust collector.
Here are some key features you’ll receive when you invest in our Spark Trap safety system:
- Maintenance free components
- Fully welded construction
- Easy install for any system
- No moving parts
- Available in carbon steel or stainless steel
- Can be installed in horizontal or vertical configurations
- Available in 6 to 40 inches
- Clean-out door
- Doesn’t require water
Spark Trap optional features include:
- Raw inlet and outlet edges
- A clamp together function for clamping duct
- Rolled angle flange for bolt-together duct
Want to know more about the Spark Trap? Check out our FAQ sheet to learn all of the benefits of our Spark Trap safety system.
Read more
by Imperial Systems | Oct 19, 2016 | Uncategorized
When Water Turns a Fire Into an Explosion
A combustible dust explosion is an ever-present danger for workers in many industries. These two examples show that despite increased awareness, explosive dust still puts lives at risk. One thing they both have in common: water may have actually made them much worse.
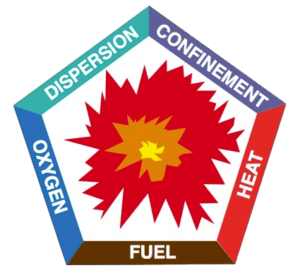
Case #1: Grain Dust
The first example shows how even things that seem like safe and practical fire-fighting measures can lead to disaster. In May, a grain dust explosion occurred in a silo. It injured a worker who was attempting to put out a dust fire with water.
Because the very fine dust was contained in the silo, all the criteria for an explosion were present… except for one. The dust provided fuel for a fire, and the open silo hatch provided oxygen. With the material confined in the closed space of the silo and an ignition source in the form of a grain dryer, the dust explosion danger was high.
Ironically, it was the worker spraying water onto the fire that created the explosion by adding the last element: dispersal of the dust. Water hitting the dust added more air and also raised a cloud of dust. Dust suspended in the air turns the situation from a fire into an explosion. In this case, it blew the roof off the silo and caused serious injuries.
Case #2: Fish Meal Dust
The second example is in some ways a classic industrial dust explosion, except that the material isn’t one you’d expect. In September, a seafood processing plant was seriously damaged and had to be shut down because of an explosion caused by the ignition of fish meal dust.
Fish meal is a fine, dry powder that manufacturers often make into fish food. A local official noted that this is the third time he knows of that fish meal has caused an explosion at a local plant. In this case, a burst pipe may have created an explosion by causing dust to become airborne.
While people don’t think of fish as being explosive, they usually don’t think of metal as being explosive either. Both of them pose an explosion danger when in dust form.
While we talk a lot about combustible metal dust and fumes because many of the industries we work with use metals, organic dusts like grain, spices, powdered milk and egg, sugar, tobacco, and yes, even fish are dangerously explosive if all the right elements are present.
Secondary Explosions from Airborne Dust
While many places that produce metal dust are aware of the risks, some places that produce organic dust don’t realize the danger it poses, or how important a dust collection system is for controlling and handling dust. The most catastrophic damage is often done by secondary explosions: a small dust explosion causes accumulated dust to be dispersed in the air, causing a much larger explosion. Spraying water on a dust fire can do the same thing, sending dust into the air.
Minimize Dust Explosion Danger
Removing dust from the facility and collecting it with a dust collection system designed to prevent or safely control explosions is an important safety strategy. Making sure that dust will not disperse in the air is another key to explosion prevention. In any situation with combustible dust, equip the system with safety features. Spark arrestors, explosion vent panels, and chemical suppressors can curtail the dust explosion danger in your factory.
Reference:
http://www.ktoo.org/2016/09/20/explosion-westward-seafoods-sparks-police-investigation/
http://www.adn.com/alaska-news/rural-alaska/2016/09/21/official-blames-fish-meal-dust-in-100k-explosion-at-dutch-harbor-seafood-plant/
https://www.commerce.wa.gov.au/sites/default/files/atoms/files/5-2016_grain_fire_and_dust_explosion_in_silo.pdf
http://content.safetyculture.com.au/news/index.php/10/safety-alert-issued-grain-fire-dust-explosion-silo/#.V_-WMugrKM-
Read more
by Imperial Systems | Oct 17, 2016 | Uncategorized
As of 2016, the Department of Justice (DOJ) and the Department of Labor (which includes OSHA) partnered to bring federal charges against companies who expose workers to dangerous materials and carcinogens. Hazardous fume and dust exposure in the workplace is indeed a serious offense.
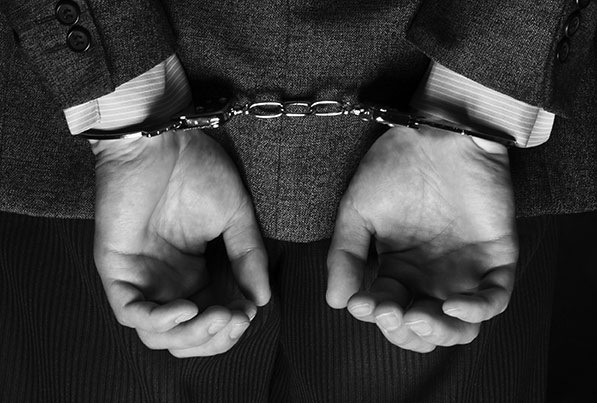
Environmental Protection Laws Facilitate Prosecution
This partnership is to enable prosecutors to use powerful environmental protection laws. With these laws, they can prosecute companies for worker safety violations involving exposure to dangerous substances. This will allow prosecutors working on OSHA worker exposure cases to work with the Environmental Crimes Section of the DOJ to maximize penalties and criminal charges.
In many cases, environmental protection laws are stricter and have stronger punishments than OSHA regulations. Environmental protection has wide public support and considerably more funding than occupational health and safety. There is an entire division of the DOJ that handles environmental crimes. More effectively, these crimes may carry a much heavier fine or more serious criminal charges.
OSHA’s ability to level criminal charges is usually limited to certain situations. This is where an employer willfully and knowingly violates safety standards which cause the death of a worker. These cases can be difficult to prove and even more difficult to prosecute. Under laws regulating environmental crimes, releasing or failing to control any workplace hazard exposure to dangerous substances is a crime. This applies even if the exposure does not result in death or serious injury.
Just like with OSHA fines, the most serious criminal charges will go to employers who repeatedly violate the rules or who fail to correct problems even when they know about them. Bringing in the DOJ and their regulation of environmental laws is likely to affect companies who aren’t following the rules for controlling or cleaning up their hazardous materials.
Identifying Hazardous Fume and Dust in the Workplace
Workplace hazard exposure includes materials such as fumes and dust from many types of industrial processes. Some examples are welding, plasma or laser cutting, manufacturing of plastics and resins, printing inks and pigments, as well as production of chemicals or fertilizers.
OSHA usually sets exposure limits for employees. Environmental regulations set limits for material release into the environment, regardless of the exposure to individual employees. Under the DOJ, environmental laws can handle hazardous material release amounts inside a facility.
For metalworking facilities, hexavalent chromium, manganese, and other components of cutting and welding fumes are heavily regulated as environmental toxins. Exposing people to these materials, inside or outside, can be an environmental crime. Hexavalent chromium often contaminates drinking water, and it’s a major environmental concern.
For companies that use or produce hazardous dust or fumes, a dust collection system is very important for limiting exposure. The system will not only keep the materials away from workers but also collects them safely and allows you to dispose of them properly. A dust and fume collection system that’s maintained and used correctly is a necessary tool for controlling hazardous airborne particles or fumes. Contact us for more information.
References:
www.justice.gov
www.justive.gov
www.justice.gov
Read more
by Imperial Systems | Oct 13, 2016 | Uncategorized
Phosgene gas became infamous during its use in chemical warfare in World War I. In numerous welding forums and opinion pieces, people share concerns about phosgene gas produced while welding.
Is this a fact or a myth?
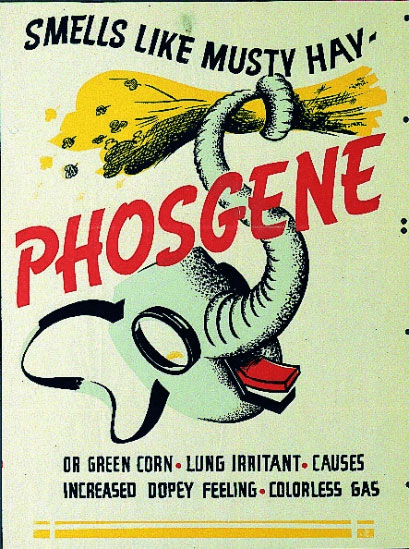
Some industrial processes use phosgene gas. It can also occur as a breakdown product from chemicals called chlorinated hydrocarbon solvents. These have names like trichloroethylene and methylene chloride.
These are very common chemicals. Pesticides, degreasing chemicals, and solvents are all examples. Older refrigerators also still contain coolants that can convert to phosgene when heated. According to the available information, welding a metal that has a solvent or degreaser (like brake cleaner) on it produces phosgene gas as a component of the welding fumes.
In one example, while repairing a refrigerator a man heating the coolant with a welding torch suffered exposure to phosgene. He endured extreme shortness of breath and irritation to his throat and lungs. He was admitted to intensive care and recovered. There are many other stories of people reporting that they or someone they know suffered exposure or injury by phosgene welding fumes.
So what are the facts about phosgene gas?
Some brake cleaners, degreasers, and solvents do contain chlorinated hydrocarbons. These products carry a warning label about toxic gases and fumes, and some of them specifically mention phosgene gas. Even though they are unexciting reading, always follow warning labels. So it’s absolutely possible to poison yourself with phosgene if using these chemicals incorrectly.
Is it a real danger for welders?
There doesn’t seem to be much solid information about that. The example of the man who was injured while using a welding torch to work on an old refrigerator is true (Journal of Accident and Emergency Medicine, 12 pp212-213 (1995)). Many people report that they or someone else suffered exposure to phosgene gas while welding something that had been cleaned with brake cleaner. There doesn’t seem to be a lot of reliable information about this problem, though. It’s definitely something that could happen, but there’s not much information about how often it actually does happen.
Do you know someone to whom this has happened, or has it happened to you? Have you ever experienced dangerous fumes while welding? Do you have any information about welding, phosgene gas, and brake cleaner that people should know about?
Check out our infographic on phosgene gas!
References:
Read more