by Imperial Systems | Feb 16, 2017 | Uncategorized
Hydraulic fracturing (“fracking”) is a process used to extract oil and gas by high-pressure fracturing of rock or shale. Exposure to respirable crystalline silica is a major hazard in this industry. Massive amounts of sand are used in the process, and silica exposure is a constant issue.
NIOSH has identified silica exposure as the single biggest health issue in hydraulic fracturing. Their research also demonstrated that silica levels on these sites are so high that standard respirators are not sufficient for protection. With a 2018 deadline for hydraulic fracturing sites to comply with new OSHA limits for silica exposure, new tactics for silica dust control are needed.
SILICA IN THE HYDRAULIC FRACTURING PROCESS
The hydraulic fracking industry uses huge amounts of sand (silica). Most grains are 2 mm or smaller in size. By some estimates, the average site requires somewhere between 1 and 7 million pounds of sand over its lifetime.
After high-pressure water and chemicals are pumped into the rocks to create fractures, the spaces must be filled with sand to keep them open and allow oil and gas to flow. So much sand is used in this industry that mining and production of “frac sand” has become a major industry of its own.
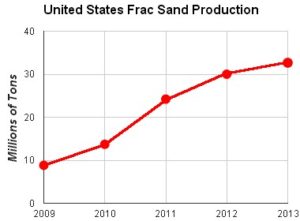
(Frac sand production: This chart illustrates the spectacular rise in the production of frac sand in the United States. Data from the United States Geological Survey Minerals Yearbook, Silica, 2011)
AREAS OF HIGH SILICA EXPOSURE
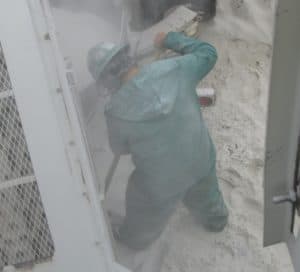
image: National Institute for Occupational Safety and Health/Centers for Disease Control and Prevention/OSHA/CDC
Massive amounts of silica move around a hydraulic fracturing site. NIOSH has identified several points in the silica moving process that create the largest amount of silica dust. These areas are:
- Open hatches on sand movers
- Through side ports on sand movers during refilling
- Depositing sand onto transfer belts
- Sand moving on transfer belts between movers, hoppers, and blenders
- Blender hoppers that mix sand
- Accumulated dust stirred up by vehicles driving around the site
NIOSH strongly recommends that engineering controls be put in place to control silica exposure at these points. They emphasize that the silica exposure at these points in the process is so heavy that respirators do not provide enough protection.
HYDRAULIC FRACTURING SILICA EXPOSURE; CONTROLLING DUST ON SITE
In some situations, newer equipment has been designed to minimize silica dust release. In other situations, older equipment can be modified or rebuilt to these designs.
For many companies, especially with the industry still recovering from the severe drop in oil prices several years ago, these expensive modifications aren’t reasonable.
Another option is to install dust collectors directly on the equipment. A collector specially designed for hydraulic fracturing equipment can be fitted on sand movers, transfer belts, and blenders. With these systems installed, the amount of silica dust released is much lower.
Controlling silica release at these points of capture can decrease silica exposure all over the site. With less silica dust escaping, the overall amount of fugitive silica dust around the site is more manageable. This helps with the amount of dust raised by vehicles or wind all over the site.
https://blogs.cdc.gov/niosh-science-blog/2012/05/23/silica-fracking/
http://geology.com/articles/frac-sand/
https://www.osha.gov/dts/hazardalerts/hydraulic_frac_hazard_alert.html
Read more
by Imperial Systems | Feb 8, 2017 | Uncategorized
Lung disease from inhaling sand or rock dust is one of the oldest occupational hazards. The health risks of silica were identified as early as 1700. Silicosis, the incurable lung disease caused by inhaling silica dust, causes hundreds of deaths every year. Other health effects also include liver and immune system diseases. OSHA concluded that the current silica exposure limits were too high after studying the research. So, they needed to set a new silica exposure limit to protect workers.
Some silica exposure still comes from well-known occupations like stone cutting, mining, and drilling. Abrasive blasting with sand is especially dangerous. However, newer industries have created new sources of exposure. One example of this is hydraulic fracturing, or fracking, for oil and gas. Another example is the popularity of natural and manufactured stone countertops. All of these industries must achieve compliance with OSHA’s new silica law to keep workers safe.
How does silica hurt you?
Silica is one of the most common elements on earth. It makes up a major part of sand, rocks, and all products made from those things, like concrete.
The major health risks of silica happen when one inhales it into the lungs. Silica that is small enough to be inhaled is called “respirable crystalline silica” in formal OSHA language. Drilling or grinding creates fine silica dust, and sand is already a form of crystalline silica that can become airborne, especially during blasting or fracking operations.
Developing Silicosis
Silicosis is a disease that causes the biggest concern with silica. The American Lung Association warns about the permanent lung damage that happens with this disease.
Silicosis happens when silica dust damages the lining of the tiny air sacs in the lungs. This injury causes scarring and makes it harder for the air sacs to get oxygen into your body.
Acute silicosis can occur within weeks or months of very heavy exposure. In this case, the lungs respond to the injury by swelling up and filling with fluid. This can be very dangerous and make it very hard to breathe.
Chronic silicosis is the most common kind. The swelling and scarring of the lungs happen over years. Symptoms include coughing, chest pain, and sometimes tiredness and weight loss. The scarring can progress to a condition called progressive massive fibrosis, where the lungs become stiff and full of scar tissue. When the disease is severe, people may need oxygen support to be able to breathe. Silicosis can cause death.
The health risks of silica include other deadly conditions. Silica is a known carcinogen, meaning it causes lung cancer. It also makes you more likely to get lung diseases like emphysema, tuberculosis or bronchitis. NIOSH, the research arm of OSHA, reviewed all of the studies on silica exposure and wrote a detailed report on it.
How can the health risks of silica be controlled?
OSHA recommends that the first line of defense is replacing silica with safer materials. This isn’t always an option. Replacement products may be expensive or just not available. Silica is common, cheap, and stable, which makes it hard to replace.
The second line of defense, and usually the best option when possible, is using engineering controls. A popular engineering control is a dust collector. A dust collection system removes silica dust from the work area and safely captures it for reuse or disposal. Just venting the dust out of the work area means that it ends up somewhere else, and that can be a problem.
A dust collector filters silica dust from the air. The dust drops into a hopper for safe handling. The air can be returned to the work area. The system can clean a large area and keep an entire facility free of silica dust.
Dust collectors can also be installed on equipment such as sand trucks or conveyors to control silica dust when moving sand around. This is important in fracking applications.
In situations like construction or drilling, the best solution may be a NIOSH-certified respirator. Because respirators are uncomfortable and difficult to fit correctly, they are not the ideal solution. Sometimes, though, they are the only option. If you must wear a respirator to protect you from the health risks of silica, make sure it is NIOSH-certified for the job you’re doing, and make sure it fits correctly.
Read more