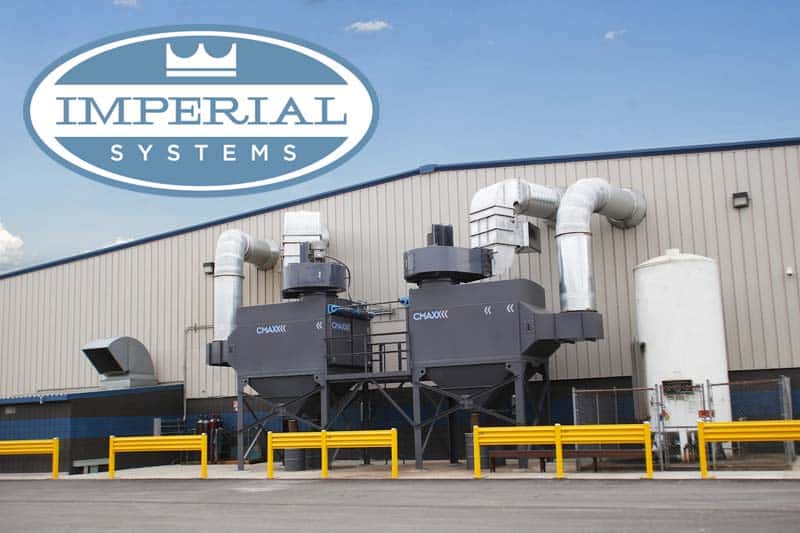
Combustible Dust Regs Off Osha’s Agenda, But Danger Remains
Part of the Trump administration’s push to support American manufacturers has involved cutting back on regulations. Several OSHA regulations in progress, including the new silica and beryllium exposure limits, have had their start dates pushed back so they can be reviewed. For industries that deal with the risk of combustible dust, one of the biggest changes may be that the administration has removed the proposed combustible dust regulations from OSHA’s agenda.
What was the plan for combustible dust regulations?
The delayed silica and beryllium regulations had already been put in place before the Trump administration requested review of them, and you can expect that they will still be implemented at some point. The combustible dust regulations, though, had been discussed, debated, and delayed for a long time before the current president took office.
The Chemical Safety Board (CSB) is an independent federal agency that investigates industrial accidents, including dust explosions. They have been pushing for combustible dust regulations for years, with one major push coming after the disastrous Imperial Sugar dust explosion in 2008, where one smaller explosion ignited sugar dust that had accumulated all over the building, killing 14 people and completely destroying the facility.
Another incident that prompted the CSB to push for combustible dust regulations was a titanium dust explosion in West Virginia that killed three workers in 2010. Throughout the next several years, the CSB kept combustible dust regulations on its “most wanted list” of new rules it considered necessary to prevent industrial accidents and deaths.
There are already combustible dust regulations for the grain industry, where explosions from dust in silos, elevators, conveyors, and mills is a constant hazard. The CSB and other safety organizations hoped to push this type of regulation to cover all types of combustible dust.
What kept the combustible dust regulations from happening?
Every year OSHA reviews laws and regulations they want to work on. Combustible dust regulations have been on that list for several years, but have been delayed or not decided on. The main problem is that such a regulation would affect nearly any industry that produces dust, since almost all dust is potentially explosive, and every process that causes dust to be produced.
With uncountable numbers of different types of dust and different processes, making combustible dust regulations that could cover all of these was a very difficult task from the beginning. This kind of regulation would have to cover industries from food to metalworking to plastics to pharmaceuticals. It would be a huge job to figure it all out and make it enforceable.
Does that mean OSHA can’t fine you for combustible dust problems?
Except for the grain industry, OSHA does not have combustible dust regulations that they can use to fine violators. However, they have issued many guidelines and recommendations for combustible dust safety. These are not enforceable. However, that does not mean combustible dust can be ignored. OSHA does have enforceable regulations for fire protection, ventilation, general environmental controls, and hazardous materials. Uncontrolled dust in your facility may be a violation of any of these.
In addition to these rules, OSHA can enforce serious fines in situations where workers are injured or killed on the job because employers did not correct a dangerous situation. In the event of a combustible dust explosion with injuries or deaths, serious penalties could be enforced for letting a hazardous situation occur.
Even without concern for combustible dust regulations, lawsuits against a company for injuries or deaths in a dust explosion are quite likely, and they could cost much more than any OSHA fine.
What guidelines should you follow to prevent combustible dust hazards?
The National Fire Protection Association (NFPA) does not make combustible dust regulations. However, they do set standards for managing combustible dust and preventing dust fires and explosions. NFPA standards are often considered the industry standard, and many local and state building codes require that facilities meet NFPA standards. NFPA 652 and 645 deal specifically with combustible dust.
Even though OSHA does not have combustible dust regulations, state and local safety administrations or building codes may have regulations that are much stricter than OSHA’s. NFPA standards are the gold standard by which many state and local governments set their safety regulations.
Why are engineering controls such as dust collectors so important?
The only good way to keep combustible dust from creating an explosion hazard is to get it out of your facility. Since blowing industrial waste into the surrounding atmosphere tends to be frowned upon, a dust collection system that filters the combustible particles out of the air can be the best solution.
Even if a fire does occur in a dust collector, properly designed systems will have safety features such as fire suppression, explosion venting, and abort gates to safely control or divert a combustible dust explosion. While OSHA does not have a regulation to enforce dust collectors for combustible dust, they do strongly recommend them, and the NFPA also strongly recommends a well-designed dust control system as a key safety feature.
Read more