by Imperial Systems | Nov 8, 2016 | Uncategorized
Your dust and fume collector can save you money on heating this winter. But to make the most of those savings, your system might need some winter maintenance. It’s that time of year when your dust collector system needs a little attention to make sure it’s ready for the demands of colder weather.
Winter Maintenance Checklist
Replace Those Filters
Winter maintenance means starting the new year with clean new filters… and you’re not going to want to change them in the middle of a snowstorm.
Changing the Magnahelic Gauge Filter
It’s easy to forget about this little filter, but it’s necessary to keep the gauge readings accurate. You should replace it whenever you replace your other filters.
Check for Accumulated Dust
If you’ve been working with the doors open during the warmer months and not running the dust collector as much, you might have dust accumulated, especially in high places or flat surfaces. For safety, try to remove as much of it as possible.
Check Airlock Wipers and Bearings
Usually, you should change airlock wipers once a year. Worn-out wipers don’t do their job properly. Winter maintenance is a good time to check them. When you replace wipers, you should also plan to replace the bearings.
Check Heaters on Pulse Valves
If you’re in a cold area and your pulse valves have heaters to keep them from freezing up, make sure they’re working. Frozen pulse valves are an inconvenience nobody needs to deal with in frigid weather.
Check Solenoid and Diaphragm Valves
Again, these are not things you want to have broken in the middle of nasty cold weather. A quick check and some preventative maintenance if necessary can save you a headache later during winter.
Check Compressed Air Hoses
Cold can make hoses more brittle and likely to break. If your compressed air hoses have any weak spots or look worn or damaged, now is a good time to make sure they get fixed or replaced.
Check Seals and Gaskets
As with the hoses, cold can make seals and gaskets crack or develop leaks. If needed, replacing them before the weather gets cold can save you from dealing with downtime from an unexpected leak.
Calibrate Differential Pressure Gauge
If you have the tools to do it, this is a good time to calibrate the differential pressure gauge and make sure you’re getting accurate readings. These gauges need to be calibrated occasionally to give you the most accurate information
Check Your Dust Collector Roof
If you’re a CMAXX owner, lucky you! Your domed CrownTech roof will keep snow or ice from piling up on top of the collector. If you don’t have a CMAXX, make sure you keep an eye on the amount of snow or ice buildup, since that can cause leaks into the collector.
Read more
by Imperial Systems | Oct 24, 2016 | Uncategorized
Extinguish the Threat of Explosions with a Spark Arrestor
It’s imperative that every metalworking facility have highly efficient dust collection systems. Also, it’s crucial that metalworking facilities utilize a spark arrestor to provide even greater protection from these combustible hazards. Here’s why a Spark Trap safety system by Imperial Systems is the best choice.
We have dedicated over 15 years to preventing and reducing fires and explosions in metalworking and manufacturing facilities. We also continually strive to meet and exceed the standards recommended by the Occupational Safety and Health Administration. Our company also meets NFPA guidelines with our highly efficient dust collection systems and replacement cartridge filters.
If you’re asking yourself if a spark arrestor is really necessary, the answer is yes! First of all, consider the findings of OSHA’s National Emphasis Program. It shows that metal dust accounts for 20% of explosions nationwide. Also, 7% of ignition sources are ignited by fabricated metals. Further, another 8% of ignition sources are caused by primary metals. So, if you want to reduce the possibility of an accident at your metalworking facility, you MUST invest in spark arrestors!
How can Spark Trap safety systems reduce explosions?
Adding a spark arrestor to your industrial dust collection system is like adding a security system to your home. That is, you already have the proper amount of protection with locks. But installing a security system in your home provides another line of defense. Above all, it keeps you and your family safe.
Our spark arrestor, named Spark Trap, is the first line of defense in protecting your metal fabricators and your metalworking facility from explosions. Spark Traps extinguish nearly every spark before it enters the main containment unit where combustible dust and other flammable material collect. When you choose our Spark Traps, you’ll receive a quality product. We make it with heavy-duty materials and it’s highly effective at keeping sparks from entering your industrial dust collector.
Here are some key features you’ll receive when you invest in our Spark Trap safety system:
- Maintenance free components
- Fully welded construction
- Easy install for any system
- No moving parts
- Available in carbon steel or stainless steel
- Can be installed in horizontal or vertical configurations
- Available in 6 to 40 inches
- Clean-out door
- Doesn’t require water
Spark Trap optional features include:
- Raw inlet and outlet edges
- A clamp together function for clamping duct
- Rolled angle flange for bolt-together duct
Want to know more about the Spark Trap? Check out our FAQ sheet to learn all of the benefits of our Spark Trap safety system.
Read more
by Imperial Systems | Oct 19, 2016 | Uncategorized
When Water Turns a Fire Into an Explosion
A combustible dust explosion is an ever-present danger for workers in many industries. These two examples show that despite increased awareness, explosive dust still puts lives at risk. One thing they both have in common: water may have actually made them much worse.
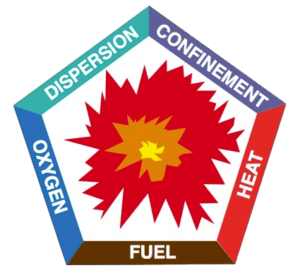
Case #1: Grain Dust
The first example shows how even things that seem like safe and practical fire-fighting measures can lead to disaster. In May, a grain dust explosion occurred in a silo. It injured a worker who was attempting to put out a dust fire with water.
Because the very fine dust was contained in the silo, all the criteria for an explosion were present… except for one. The dust provided fuel for a fire, and the open silo hatch provided oxygen. With the material confined in the closed space of the silo and an ignition source in the form of a grain dryer, the dust explosion danger was high.
Ironically, it was the worker spraying water onto the fire that created the explosion by adding the last element: dispersal of the dust. Water hitting the dust added more air and also raised a cloud of dust. Dust suspended in the air turns the situation from a fire into an explosion. In this case, it blew the roof off the silo and caused serious injuries.
Case #2: Fish Meal Dust
The second example is in some ways a classic industrial dust explosion, except that the material isn’t one you’d expect. In September, a seafood processing plant was seriously damaged and had to be shut down because of an explosion caused by the ignition of fish meal dust.
Fish meal is a fine, dry powder that manufacturers often make into fish food. A local official noted that this is the third time he knows of that fish meal has caused an explosion at a local plant. In this case, a burst pipe may have created an explosion by causing dust to become airborne.
While people don’t think of fish as being explosive, they usually don’t think of metal as being explosive either. Both of them pose an explosion danger when in dust form.
While we talk a lot about combustible metal dust and fumes because many of the industries we work with use metals, organic dusts like grain, spices, powdered milk and egg, sugar, tobacco, and yes, even fish are dangerously explosive if all the right elements are present.
Secondary Explosions from Airborne Dust
While many places that produce metal dust are aware of the risks, some places that produce organic dust don’t realize the danger it poses, or how important a dust collection system is for controlling and handling dust. The most catastrophic damage is often done by secondary explosions: a small dust explosion causes accumulated dust to be dispersed in the air, causing a much larger explosion. Spraying water on a dust fire can do the same thing, sending dust into the air.
Minimize Dust Explosion Danger
Removing dust from the facility and collecting it with a dust collection system designed to prevent or safely control explosions is an important safety strategy. Making sure that dust will not disperse in the air is another key to explosion prevention. In any situation with combustible dust, equip the system with safety features. Spark arrestors, explosion vent panels, and chemical suppressors can curtail the dust explosion danger in your factory.
Reference:
http://www.ktoo.org/2016/09/20/explosion-westward-seafoods-sparks-police-investigation/
http://www.adn.com/alaska-news/rural-alaska/2016/09/21/official-blames-fish-meal-dust-in-100k-explosion-at-dutch-harbor-seafood-plant/
https://www.commerce.wa.gov.au/sites/default/files/atoms/files/5-2016_grain_fire_and_dust_explosion_in_silo.pdf
http://content.safetyculture.com.au/news/index.php/10/safety-alert-issued-grain-fire-dust-explosion-silo/#.V_-WMugrKM-
Read more
by Imperial Systems | Oct 17, 2016 | Uncategorized
As of 2016, the Department of Justice (DOJ) and the Department of Labor (which includes OSHA) partnered to bring federal charges against companies who expose workers to dangerous materials and carcinogens. Hazardous fume and dust exposure in the workplace is indeed a serious offense.
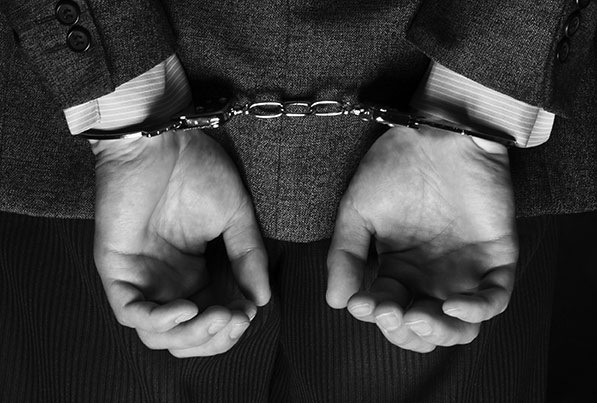
Environmental Protection Laws Facilitate Prosecution
This partnership is to enable prosecutors to use powerful environmental protection laws. With these laws, they can prosecute companies for worker safety violations involving exposure to dangerous substances. This will allow prosecutors working on OSHA worker exposure cases to work with the Environmental Crimes Section of the DOJ to maximize penalties and criminal charges.
In many cases, environmental protection laws are stricter and have stronger punishments than OSHA regulations. Environmental protection has wide public support and considerably more funding than occupational health and safety. There is an entire division of the DOJ that handles environmental crimes. More effectively, these crimes may carry a much heavier fine or more serious criminal charges.
OSHA’s ability to level criminal charges is usually limited to certain situations. This is where an employer willfully and knowingly violates safety standards which cause the death of a worker. These cases can be difficult to prove and even more difficult to prosecute. Under laws regulating environmental crimes, releasing or failing to control any workplace hazard exposure to dangerous substances is a crime. This applies even if the exposure does not result in death or serious injury.
Just like with OSHA fines, the most serious criminal charges will go to employers who repeatedly violate the rules or who fail to correct problems even when they know about them. Bringing in the DOJ and their regulation of environmental laws is likely to affect companies who aren’t following the rules for controlling or cleaning up their hazardous materials.
Identifying Hazardous Fume and Dust in the Workplace
Workplace hazard exposure includes materials such as fumes and dust from many types of industrial processes. Some examples are welding, plasma or laser cutting, manufacturing of plastics and resins, printing inks and pigments, as well as production of chemicals or fertilizers.
OSHA usually sets exposure limits for employees. Environmental regulations set limits for material release into the environment, regardless of the exposure to individual employees. Under the DOJ, environmental laws can handle hazardous material release amounts inside a facility.
For metalworking facilities, hexavalent chromium, manganese, and other components of cutting and welding fumes are heavily regulated as environmental toxins. Exposing people to these materials, inside or outside, can be an environmental crime. Hexavalent chromium often contaminates drinking water, and it’s a major environmental concern.
For companies that use or produce hazardous dust or fumes, a dust collection system is very important for limiting exposure. The system will not only keep the materials away from workers but also collects them safely and allows you to dispose of them properly. A dust and fume collection system that’s maintained and used correctly is a necessary tool for controlling hazardous airborne particles or fumes. Contact us for more information.
References:
www.justice.gov
www.justive.gov
www.justice.gov
Read more
by Imperial Systems | Aug 2, 2016 | Uncategorized
Whether you are a new manufacturing business or just branching out into new territory, if you are going to get into the metalworking field, addressing industrial dust control solutions demand some serious consideration. Not only do you have the safety of your work space to think about, but unchecked dust and fumes can also pose health hazards to those working in it. We’ve spent nearly 15 years considering the challenges of industrial dust accumulation and control, and we have developed the solutions our customers need. Discover the facts you need about dust control for your business so things run safely and smoothly.
Meet Safety Standards
An accumulation of dust in any industrial setting poses a threat to the health and safety of those working there. This is especially true in the world of metalworking where the fine dust particles may be especially toxic. In light of this threat, the Occupational Safety and Health Administration (OSHA) has established standards of safety that must be followed in any such industrial setting. These address not only inhaled dust but also the threat of combustibility through its accumulation. Check out the latest combustible dust update HERE. When you look for an industrial dust control system, begin by ensuring that it meets these and other industry standards.
Anticipate Dust And Fumes
As you consider a system to provide dust control for your workspace, make sure you take fumes into account as well. In many metalworking processes, noxious fumes are created which are more than unpleasant; they can be increasingly harmful when inhaled. Not all industrial dust control systems are created to handle this dual threat, so it is vital to choose a collector that can manage both dust and fume generated by metalwork manufacturing.
Your Industrial Dust Control Solutions Experts
Whether you need dust and fume filtration or just a dust collection system, Imperial Systems is your industrial dust control headquarters. We manufacture the most efficient, strongest, and longest-lasting systems and filters in the industry. Through these products, we have become well-known for our dedication to quality, value, and safety. Our outstanding line of equipment includes:
- CMAXX™ Dust Collector System
- DeltaMAXX™ Cartridge Filters
- CMAXX™ Laser Fume Extraction System
- Spark Arrestor
- Explosion Isolation Valve
- Custom Ductwork & Fittings
- Heavy Duty Abort Gates
- and more!
Most of our products are available to ship within 24 hours. For more information about our products and how we can support your metalworking business, contact us today.
Read more