by Imperial Systems | Oct 19, 2016 | Uncategorized
When Water Turns a Fire Into an Explosion
A combustible dust explosion is an ever-present danger for workers in many industries. These two examples show that despite increased awareness, explosive dust still puts lives at risk. One thing they both have in common: water may have actually made them much worse.
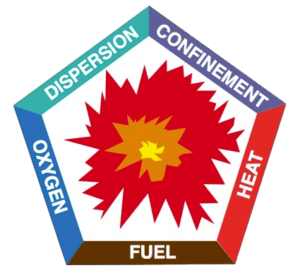
Case #1: Grain Dust
The first example shows how even things that seem like safe and practical fire-fighting measures can lead to disaster. In May, a grain dust explosion occurred in a silo. It injured a worker who was attempting to put out a dust fire with water.
Because the very fine dust was contained in the silo, all the criteria for an explosion were present… except for one. The dust provided fuel for a fire, and the open silo hatch provided oxygen. With the material confined in the closed space of the silo and an ignition source in the form of a grain dryer, the dust explosion danger was high.
Ironically, it was the worker spraying water onto the fire that created the explosion by adding the last element: dispersal of the dust. Water hitting the dust added more air and also raised a cloud of dust. Dust suspended in the air turns the situation from a fire into an explosion. In this case, it blew the roof off the silo and caused serious injuries.
Case #2: Fish Meal Dust
The second example is in some ways a classic industrial dust explosion, except that the material isn’t one you’d expect. In September, a seafood processing plant was seriously damaged and had to be shut down because of an explosion caused by the ignition of fish meal dust.
Fish meal is a fine, dry powder that manufacturers often make into fish food. A local official noted that this is the third time he knows of that fish meal has caused an explosion at a local plant. In this case, a burst pipe may have created an explosion by causing dust to become airborne.
While people don’t think of fish as being explosive, they usually don’t think of metal as being explosive either. Both of them pose an explosion danger when in dust form.
While we talk a lot about combustible metal dust and fumes because many of the industries we work with use metals, organic dusts like grain, spices, powdered milk and egg, sugar, tobacco, and yes, even fish are dangerously explosive if all the right elements are present.
Secondary Explosions from Airborne Dust
While many places that produce metal dust are aware of the risks, some places that produce organic dust don’t realize the danger it poses, or how important a dust collection system is for controlling and handling dust. The most catastrophic damage is often done by secondary explosions: a small dust explosion causes accumulated dust to be dispersed in the air, causing a much larger explosion. Spraying water on a dust fire can do the same thing, sending dust into the air.
Minimize Dust Explosion Danger
Removing dust from the facility and collecting it with a dust collection system designed to prevent or safely control explosions is an important safety strategy. Making sure that dust will not disperse in the air is another key to explosion prevention. In any situation with combustible dust, equip the system with safety features. Spark arrestors, explosion vent panels, and chemical suppressors can curtail the dust explosion danger in your factory.
Reference:
http://www.ktoo.org/2016/09/20/explosion-westward-seafoods-sparks-police-investigation/
http://www.adn.com/alaska-news/rural-alaska/2016/09/21/official-blames-fish-meal-dust-in-100k-explosion-at-dutch-harbor-seafood-plant/
https://www.commerce.wa.gov.au/sites/default/files/atoms/files/5-2016_grain_fire_and_dust_explosion_in_silo.pdf
http://content.safetyculture.com.au/news/index.php/10/safety-alert-issued-grain-fire-dust-explosion-silo/#.V_-WMugrKM-
Read more
by Imperial Systems | Jul 26, 2016 | Uncategorized
Dust explosions are bad to begin with, but what do you know about secondary explosions? There are many factors that determine how likely a particular type of dust causes deflagration. When you think of combustible dust, do you think of the explosions you’ve heard about at grain handling facilities? Maybe you think of the explosive potential of aluminum dust.
Secondary Dust Explosion Incidents
Three dust explosions occurred in 2003. They demonstrate how many different types of production and manufacturing can produce a deflagration risk, including a secondary dust explosion. In a North Carolina plant, the application of a polyethylene coating to rubber caused accumulation of the dust. As the material dried, dust formed and accumulated above the work area. The work area was clean. But a layer of dust 1/4″ thick was enough to cause an explosion that killed six people. In this situation, a dust collection system in the production area could have captured the dust particles before they circulated through the facility.
The explosion in Kentucky was caused by combustible dust that resulted from a resin used to treat fiberglass. Workers were aware of the large quantities of dust. But cleaning processes often just caused more of the dust to become airborne. So, it accumulated in the ductwork and in dust collection equipment. There were no safeguards in place to prevent a flame front from traveling through the ductwork or getting into the dust collector. An abort gate with spark or flame detection could have identified and stopped the fire from spreading, and dust collectors designed to stop deflagration fronts could have prevented the dust collectors from becoming sites of secondary explosions.
Aluminum dust from scrap processing fueled the explosion in Indiana. The dust collector in this case was the source of the explosion. It did not have explosion vent panels, and instead of being directed safely, the explosion traveled back into the building and ignited dust in the ductwork. A secondary explosion occurred when dust accumulated on surfaces inside the facility ignited. A dust collector designed to isolate and redirect a deflagration could have prevented this accident.
NFPA Recommendations
The National Fire Protection Association, which establishes many of the codes and standards for handling potential fire hazards recommends that all dust collection systems should have explosion venting to redirect explosions and abort gates or other equipment to stop flame fronts from spreading. It also recommends improved housekeeping measures to prevent dust from accumulating. Accomplish this by collecting dust at the source so there’s no accumulation in difficult-to-reach places.
It’s often this accumulated dust, hidden on high surfaces, in corners, or inside ductwork, that ignites to cause a secondary explosion that’s far more dangerous than the original one. Witness reports of dust explosions often include descriptions of a smaller explosion followed by one or more larger ones; this is secondary ignition. Dust control throughout the facility, along with fire prevention equipment such as abort gates, spark arrestors, and explosion venting, can control a potential explosion and prevent a small fire from becoming a fatal disaster.
Read more