by Erin Long | Jan 21, 2025 | Uncategorized
When it comes to maintaining a dust collection system, one of the most important tasks is keeping the filters clean. Over time, filters become clogged with dust, which can reduce the system’s efficiency and impact air quality. A common question many people ask is whether it’s okay to take filters out of the dust collector and manually clean filters using compressed air. While this method might seem like a quick fix, we do not recommend it for several important reasons.
The Risks of Cleaning Filters with Compressed Air
Using compressed air nozzles to clean your dust collector filters may seem like a convenient option. However, it poses several risks that could ultimately damage your filters and compromise system performance.
1. Risk of Physical Damage
When loading up filters with dust and debris, they can become quite heavy and awkward to handle. If you remove the filter from your dust collector to clean it with compressed air nozzle, you run the risk of inadvertently dropping or mishandling the filter. This can lead to physical damage such as tears or dents in the filter media. A compromised filter may no longer function effectively. This leads to dust leakage that can affect the clean air side of your system.
2. Creating Tiny Holes in the Media
One of the most significant dangers of using compressed air nozzles is the potential to create tiny holes or punctures in the filter material. Even a small hole in the filter, easily missed by the naked eye, can allow dust to bypass the filtration process. This defeats the purpose of having the dust collector in the first place. As dust particles slip through, they will be released into the air, potentially causing air quality issues and health hazards. Over time, this can also put additional strain on your dust collection system. As a result, it will work harder and use more energy.
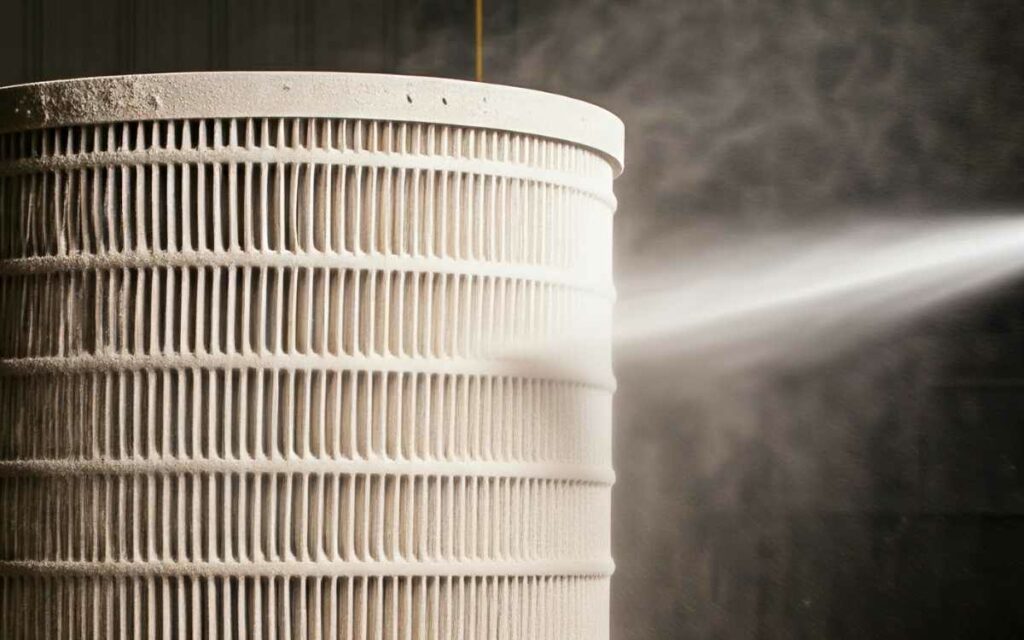
3. Compromising Filter Efficiency
Most dust collector filters are designed to trap particles of specific sizes. Directing compressed air at the filter can forcefully dislodge particles. However, this action can also disrupt the structure of the filter material. By doing so, you may alter the filter’s ability to capture smaller dust particles. Once the structure is compromised, the filter’s effectiveness diminishes, which can result in less efficient dust collection.
What You Should Do Instead of Cleaning Filters with Compressed Air
Rather than relying on compressed air nozzles for cleaning, it’s important to recognize that even well-maintained filters will eventually need replacement. Over time, dust particles accumulate and begin to clog the filter, reducing its ability to function properly. Here’s how you can determine when it’s time to replace your filters:
1. Monitor Differential Pressure
One of the best ways to know when your filters need replacing is by monitoring the differential pressure across the filter. Differential pressure is the difference in air pressure on the dirty side and clean side of the filter. As the filter becomes clogged, this pressure difference will increase. If the differential pressure reading rises above 5, it’s a sign. This means that the filter is no longer performing effectively and needs replacement.
2. Signs of Physical Damage
Even if the filter’s pressure readings are normal, it’s important to check the filter for physical signs of wear and tear. If you notice any tears, holes, or obvious damage, it’s time to replace the filter. Small imperfections in the filter material can lead to air quality issues by allowing dust to bypass the filtration system.
3. Reduced Airflow
Another indicator that your filters may need replacement is reduced airflow in your dust collection system. If the system isn’t pulling air as efficiently as it used to, the filters may be too clogged or damaged to function properly.
While using compressed air nozzles to clean dust collector filters might seem like an efficient solution, it’s not worth the potential risks. The damage that can occur from mishandling or creating holes in the filter media far outweighs the temporary benefit of a cleaner filter. Instead, allow your dust collector to handle the cleaning. Regularly monitor your system’s performance, keep an eye on differential pressure, and replace filters when necessary. Keeping your dust collector filters in good condition will help ensure the long-term efficiency and safety of your system.
Read more
by Erin Long | Jan 17, 2025 | Uncategorized
Combustible dust has long been a safety concern across industries, with its potential to cause devastating fires and explosions. To address these risks, the National Fire Protection Association (NFPA) has developed NFPA 660, a consolidated standard that provides clear, unified guidance for managing combustible dust hazards.
So, What is NFPA 660?
NFPA 660 is a new, comprehensive standard that merges several existing NFPA standards related to combustible dust. These include NFPA 61 (agricultural dusts), NFPA 484 (combustible metals), NFPA 652 (fundamentals of combustible dust), NFPA 654 (general dust hazards), NFPA 655 (sulfur dusts), and NFPA 664 (wood processing dust). By merging these standards, NFPA 660 offers a streamlined approach to dust safety, eliminating redundancies and ensuring consistency across industries.
This unified standard covers all aspects of combustible dust hazard management, including dust hazard analysis, engineering controls, equipment design, housekeeping, explosion protection, and more.
Why NFPA 660 on Combustible Dust Matters
The creation of NFPA 660 is a significant step forward for industrial safety. By consolidating multiple standards into a single document, it simplifies compliance for industries that handle combustible dust. As a result, this unified approach ensures that facilities of all types can follow consistent and comprehensive guidelines.
Additionally, NFPA 660 reflects the latest advancements in technology and knowledge regarding combustible dust hazards, ensuring that facilities are equipped with the most effective tools and strategies for managing these risks.
Key Components of NFPA 660
1. Dust Hazard Analysis (DHA):
NFPA 660 emphasizes the importance of performing a Dust Hazard Analysis, a process that helps facilities identify areas where combustible dust presents risks of fire, deflagration, or explosion. This step is critical for developing effective mitigation strategies.
2. Hazard Mitigation Strategies:
The standard provides detailed guidance on engineering controls, such as dust collection systems, explosion venting, and spark detection systems. It also addresses administrative controls, like proper housekeeping practices and employee training.
3. Industry-Specific Considerations:
NFPA 660 recognizes that different industries face unique challenges with combustible dust. By integrating knowledge from the previously separate standards, it ensures that industry-specific hazards—such as those related to wood dust or metal shavings—are addressed effectively.
4. Consistency in Compliance:
A key benefit of NFPA 660 is the elimination of conflicting or redundant requirements across industries. Facilities that previously had to consult multiple standards now have a single, comprehensive document to guide their safety practices.
Who Needs to Comply with NFPA 660?
NFPA 660 applies to any facility where combustible dust is generated, processed, or handled. This includes industries such as agriculture, food processing, metalworking, pharmaceuticals, woodworking, and chemical manufacturing as well as others. Compliance with NFPA 660 is essential not only for meeting regulatory requirements but also for protecting employees, equipment, and the surrounding community from the devastating consequences of dust-related incidents.
How Do I Know If My Dust Is Combustible?
Understanding whether the dust generated in your facility is combustible is a critical step in complying with NFPA 660. Combustible dust is not always obvious, as materials that seem benign in solid form—such as wood, sugar, or metals—can become hazardous when turned into fine particles. The only definitive way to know if your dust is combustible is to have it tested by a certified laboratory. Testing can reveal properties such as ignition sensitivity, combustibility, and explosion potential, enabling you to design effective safety and mitigation strategies tailored to your specific operations.
The Path Forward
NFPA 660 is a game-changer for industrial safety. Its unified approach simplifies compliance, enhances safety, and ensures consistency across industries. By adopting NFPA 660, facilities can certainly mitigate combustible dust risks effectively, fostering a safer work environment for everyone.
If your facility handles combustible dust, now is the time to familiarize yourself with NFPA 660 and ensure your operations are in full compliance with its guidelines.
Read more
by Erin Long | Jan 15, 2025 | Uncategorized
Maintaining industrial dust collectors is crucial to ensure peak performance and safety. One question that frequently arises is whether the cartridge filters used in these systems are washable. While the concept of washable dust collector filters might seem cost-effective at first, there are several important factors to consider before purchasing. Washing your filters might end up costing you more in the long run and even compromise the functionality of your dust collection system.
Why Washable Dust Collector Filters Are Problematic
- System Design Limitations – Your dust collection system was designed with specific filter specifications, including air-to-cloth ratio, surface area, and airflow requirements. Washable filters typically have less surface area than standard filters. Using them alters the airflow dynamics, which can affect the system’s performance. This could result in reduced dust collection efficiency and potentially harm your equipment.
- Reduced Filtration Efficiency – Washable filters often have a lower MERV (Minimum Efficiency Reporting Value) rating compared to standard industrial filters. A lower MERV rating means these filters are less effective at capturing fine particulates. Over time, more dust may bypass the filters, leading to issues with air quality, equipment performance, and safety compliance.
- Limited Wash Durability – Although marketed as washable, these filters are not designed for repeated washing. After one or two washes, the material often begins to degrade, causing holes and tears. Using high-pressure cleaning methods can further damage the filters, reducing their lifespan and efficiency. Essentially, you’ll still need to replace these filters sooner than expected, nullifying any cost-saving benefits.
- Inaccurate Differential Pressure Readings – Damaged filters from repeated washing can lead to inaccurate differential pressure readings. Differential pressure is a key indicator in monitoring the health of your filters and system. If using compromised filters, the readings may fail to alert you to necessary maintenance, potentially leading to system malfunctions or unsafe operating conditions.
The Better Alternative
Instead of using washable filters, invest in high-quality filters designed specifically for your industrial dust collection system. These filters are engineered for optimal performance, providing effective dust capture and maintaining system efficiency over time. Regularly replacing filters with the correct type ensures compliance with safety standards, protects your equipment, and minimizes downtime.
While the idea of washing industrial dust collector filters might seem appealing, it’s not a practical or cost-effective solution. The potential risks to system performance, filtration efficiency, and safety outweigh any perceived benefits.
Always use filters that are compatible with your dust collection system and replace them as needed to ensure optimal performance and long-term savings. Be sure to select high-quality filters with a good efficiency rating. By sticking to proper maintenance practices, you’ll keep your operations running smoothly and efficiently.
Read more
by Erin Long | Jan 7, 2025 | Blog Posts, Uncategorized
Welding and grinding are two essential processes in many industrial operations. Both generate dust and fumes that must be safely controlled. A common question in these environments is whether the same filtration system can be used for both processes. It is technically possible to use a single dust collection system. However, there are several critical considerations to address to ensure safety and efficiency. Simply combining welding fumes and grinding dust without proper design could lead to significant risks.
Understanding the Differences Between Welding Fumes and Grinding Dust
Welding and grinding produce very different types of contaminants:
- Welding Fumes: These consist primarily of fine metal oxides generated as a result of the welding process. Welding fume particles are typically very small (sub-micron size). Inhaling them is hazardous as they often contain materials such as iron oxide, manganese, or chromium, depending on the welded metal.
- Grinding Dust: Grinding produces larger particulates and can include a mix of materials. This dust may contain metal shavings, abrasives from grinding wheels, and other byproducts. The composition and size of grinding dust can vary significantly. It depends on the materials being worked on and the tools being used.
Mixing these two types of particulates in the same dust collection system can lead to unintended consequences. For example, combining metal fumes with abrasive grinding dust may alter the dust’s characteristics, potentially making it more combustible or flammable. This risk is amplified because sparks are often present in both processes.
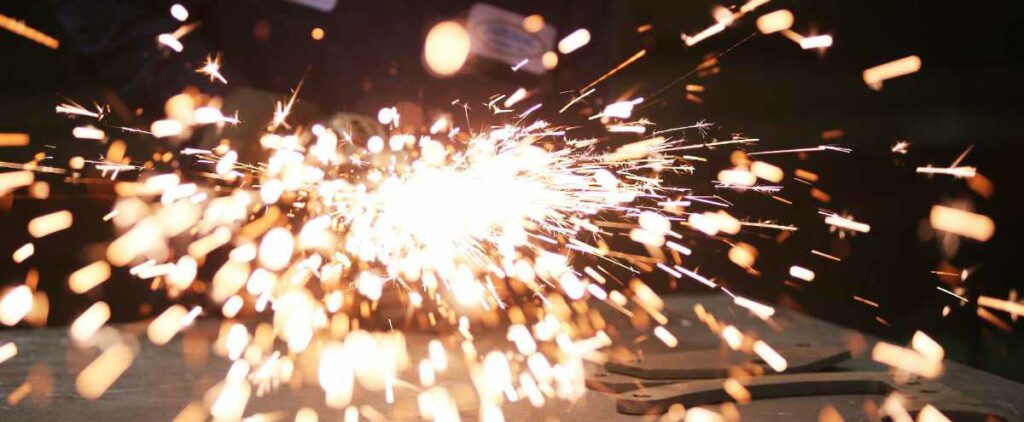
Fire and Explosion Risks in Combined Systems
Sparks are a major fire hazard when combined with combustible dust. Both welding and grinding produce sparks that have the potential to travel through the extraction system and ignite flammable particulates.
If mixing welding and grinding dust, the potential for combustion increases because the dust characteristics are unpredictable. This requires careful design of the dust collection system to include features like spark arrestors and fire suppression systems. Ignoring these precautions could lead to catastrophic fires or explosions in the workplace.
Sizing the Dust Collection System Properly
Another important consideration when using the same system for welding and grinding is the sizing of the dust collector. The efficiency of a dust collection system depends heavily on the air-to-cloth ratio—the volume of air passing through a square foot of filter media.
Welding fumes, being fine and lightweight, allow for a higher air-to-cloth ratio. In contrast, grinding dust, which includes larger and heavier particles, requires a lower air-to-cloth ratio to ensure proper filtration. If using the same system for both processes, it’s critical to size it conservatively to accommodate the demands of grinding dust. A system designed solely for welding fumes may not effectively handle grinding dust. This leads to reduced efficiency, increased filter wear, and higher maintenance costs.
To safely extract both welding and grinding contaminants, the dust collector should have a low enough air-to-cloth ratio to handle the larger grinding particulates without compromising on the capture of fine welding fumes.
Designing a Safe, Effective Solution for Welding and Grinding Dust and Fumes
While using a single dust collection system for both welding and grinding is feasible, it must be carefully designed to address the specific challenges of each process:
- Dust Hazard Analysis: Conduct a thorough analysis to understand the composition, combustibility, and volume of the dust and fumes produced.
- Proper Filtration: Select filter media that can suitably handle both fine welding fumes and larger grinding particulates.
- Spark Control: Incorporate spark arrestors, fire suppression systems, and explosion vents to mitigate fire hazards.
- Sizing and Airflow: Design the system with an appropriately low air-to-cloth ratio to accommodate grinding dust while still effectively filtering welding fumes.
- Segregation (Optional): In high-risk environments, consider separate extraction systems for welding and grinding to minimize safety concerns.
While welding and grinding can share the same dust and fume extraction system, it is not always the recommended solution. Mixing welding fumes with grinding dust poses risks related to combustibility, fire hazards, and filtration efficiency. If you choose to use a common system, it’s essential to design it with care—accounting for the specific needs of both processes, ensuring proper sizing, and implementing safety features like spark control systems.
Ultimately, a well-designed dust collection system will not only keep your facility safe and compliant but also improve air quality, protect equipment, and enhance overall productivity. If you are unsure whether a shared system is appropriate for your operation, consulting with dust collection experts can help you make the best decision for your facility’s needs.
Read more
by Erin Long | Jan 7, 2025 | Uncategorized
When it comes to industrial operations, air quality management is a crucial aspect of maintaining compliance with environmental regulations and protecting the surrounding community. A common question arises for facility managers and safety coordinators: Do I need to filter air before ventilating it outdoors? In most cases, the answer is yes—but the specifics depend on the type of operation, the nature of the contaminants in the air, and regulatory requirements in your region.
Understanding Emissions Regulations
In the United States, the Environmental Protection Agency (EPA) and local Department of Environmental Protection (DEP) agencies regulate air emissions to ensure that pollutants released into the atmosphere do not harm human health or the environment. For many industrial facilities, exhausting air outdoors requires obtaining an emissions permit from the DEP. These permits outline specific conditions under which air can be discharged. These include limitations on the types and amounts of contaminants present in the exhaust air.
If the air your facility exhausts contains harmful particulates, fumes, or chemical vapors, filtration will likely be required to meet regulatory standards. But failure to comply with these standards can result in hefty fines, legal consequences, and potential harm to the environment or nearby communities.
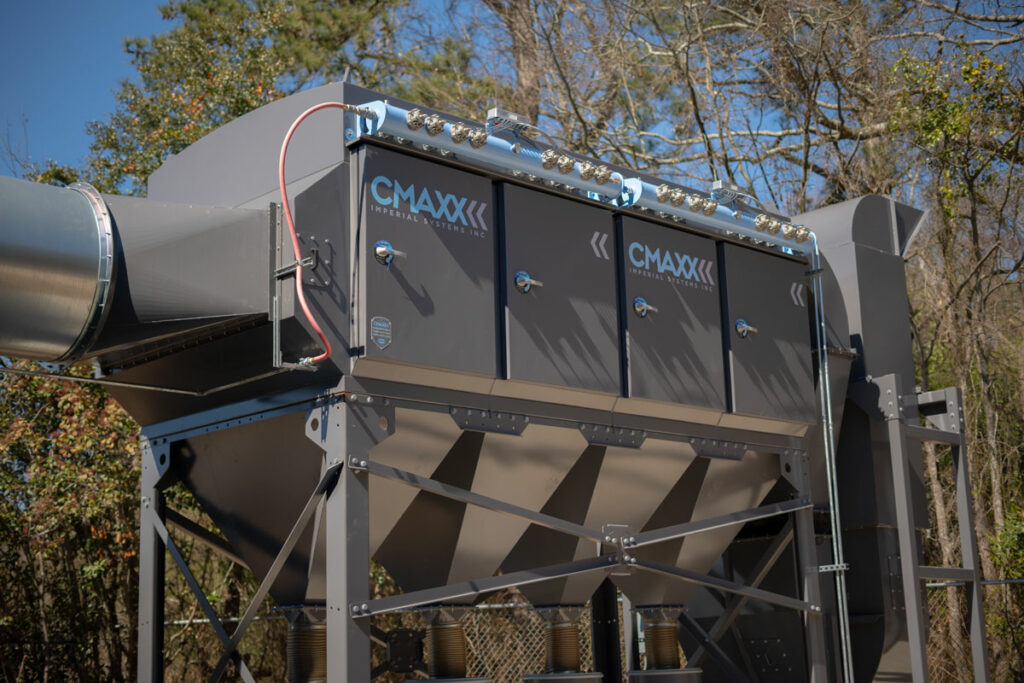
Why Filtration Is Necessary
Ventilating air outdoors may contain a range of contaminants, depending on your industrial processes. These can include dust, smoke, fumes, volatile organic compounds (VOCs), and hazardous air pollutants (HAPs). Releasing unfiltered air can pose serious risks to both public health and the environment. For example:
- Public Health Risks: Harmful particulates and chemical fumes can cause respiratory issues and other health problems for people living or working near your facility.
- Environmental Impact: Airborne contaminants can contribute to smog, acid rain, and other environmental issues.
- Odor Control: Even if the contaminants in your air do not pose a direct health risk, strong odors can be a nuisance to the local community.
By implementing proper filtration systems, you can significantly reduce these risks while also ensuring compliance with emissions regulations.
When Filtration Is Required
The following situations typically require filtration::
- Presence of Harmful Contaminants: If your operations generate pollutants like dust, fumes, or chemical vapors, filtration is necessary to remove or reduce these contaminants before the air is released.
- Permit Requirements: Most emissions permits issued by the DEP will specify allowable levels of contaminants in exhausted air. Filtration helps ensure your facility meets these thresholds.
- Community and Environmental Impact: Even if your facility is not strictly required to filter air under specific regulations, doing so can help maintain good relationships with the surrounding community and minimize environmental harm.
Choosing the Right Filtration System
Selecting the right filtration system depends on the type of contaminants present in your air stream. Common solutions include:
- Dust Collectors: These systems, such as baghouses or cartridge collectors, are effective at removing particulate matter from exhaust air.
- Fume Extractors: Ideal for capturing welding fumes, smoke, and fine particulates.
- Activated Carbon Filters: Used to capture VOCs and other chemical vapors.
- HEPA Filters: Provide high-efficiency filtration for very fine particles, ensuring clean air discharge.
Benefits of Filtering Air Before Ventilating It Outdoors
Filtration not only ensures regulatory compliance but also offers several additional benefits:
- Avoiding Fines: Compliance with emissions permits prevents costly penalties for violations.
- Protecting Public Health: Proper filtration minimizes the impact of harmful air contaminants on nearby communities.
- Reducing Environmental Damage: By filtering pollutants, your facility contributes to cleaner air and a healthier planet.
- Maintaining Reputation: Proactive air quality management demonstrates your commitment to responsible operations, fostering trust with regulators and the public.
In most cases, filtering air before ventilating it outdoors is not just a good idea—it’s a necessity. So whether required by an emissions permit or driven by a desire to protect public health and the environment, filtration systems play a critical role in responsible industrial operations. But are you unsure about your facility’s specific requirements? Then consult with an air quality professional or the DEP as a prudent first step. Investing in proper filtration ensures compliance, reduces risk, and helps create a cleaner, safer future for everyone.
Read more