by Erin Long | Jan 24, 2020 | Hidden from Archive
Bob has been in metalworking for 44 years. In his spare time he enjoys going to the dirt track and hunting. He also enjoys spending time with his grandkids and dogs.
Q: How long have you been at Imperial Systems?
Nine years. I’ve been doing metalworking for 44 years.
Q: Where did you start?
I started at a place in Sandy Lake, doing welding and fabrication. I was there for about 20 years, but then I got laid off there. I went to work at a place in Grove City that made testing equipment, and I was there for about 15 years. Got laid off again, found out this place was hiring, and filled out an application.
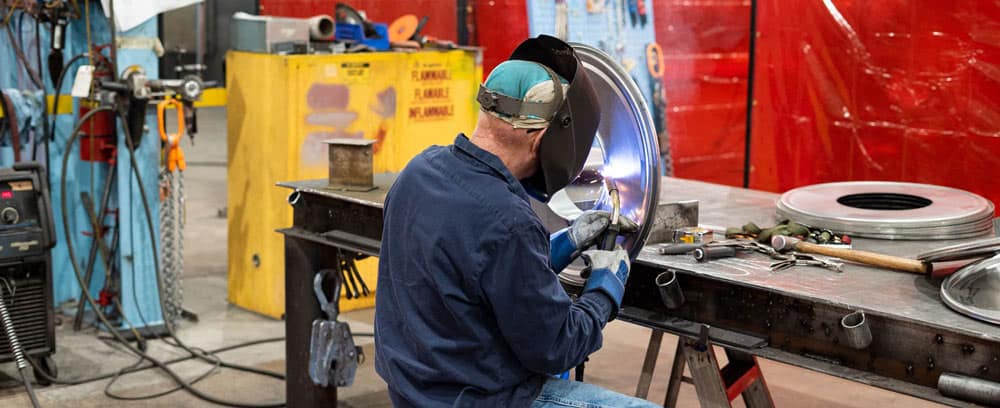
Q: What do you do when you’re not at work?
Watch my grandkids, cut wood, split wood… I like to go out to the dirt track and watch the races. My wife got me into that. Her father used to race.
Q: Anything else?
Well, I go hunting, like pretty much everybody around here. Didn’t see anything this year. Sometimes a couple of the neighbors will stop up and we’ll sit on the porch and talk.
Q: How many grandkids do you have?
I have three kids and four grandkids. The oldest is 22. Two of them are in the same class at school and people think they’re cousins, but people think they’re brother and sister.
Q: Any pets?
Yeah, I have three dogs.
Q: What else do you like to do?
That’s pretty much it. My life’s not very exciting. When I get home from work I mostly just feel like taking a nap. Especially when we get overtime and I come in early. That’s a little rough, but I’d rather come in early than stay late. I don’t like watching other people leave while I’m still here.
How do you like it here?
I like it. It’s a good place. It seems kind of crazy that this whole place is owned by one person. Most places, it’s a big corporation that owns it. Makes it kind of different here.
Read more
by Erin Long | Jan 24, 2020 | Hidden from Archive
Tony Bennet is into his nineties and still performing. He credits his popularity with the younger generation to the fact he wears a necktie. According to Tony, “You have to be different”. He always was a sharp dresser. Dhani Jones, retired NFL linebacker, likes to rock a bow tie. He said, “Just because you wear a bow tie doesn’t mean you’re a Nerd”. After his NFL career, Jones found a charity organization called “Bow Tie Cause” to raise money for various charitable causes. And Rick Kaplan of “The Kaplan Report” says, “Wearing a bow tie is a statement, almost an act of defiance.” These three men, all successful in unrelated fields, have something in common. They all like to wear neckties. But I fear this is no longer the norm today. The tie has gone the way of the Fedoras and Homburgs. In my younger days, a sharp-dressed man would never think of leaving home without one. Today they have been replaced with a ball cap. It makes me fear the haberdashers are becoming extinct.
When I began my career as a draughtsman there was a dress code. We all wore ties at the drawing boards. The only problem was, I didn’t know how to properly tie a necktie. My tie knots always looked half done. Then one of the older draftsmen took me aside and showed me the proper way to tie a Windsor knot. I’m still grateful to him today for teaching me that life skill. Button-down shirts, neckties, and dress slacks were the mandatory dress code for much of my career. Later, when I moved into engineering sales, a sports jacket was also required on sales calls. It didn’t matter if it was the hottest day of the year, it was mandatory to wear a jacket when meeting with a client. I can remember one client visit made with my boss. When we arrived, he donned a Navy-Blue Blazer that was pulled from beneath the seat of his car. He called it his “Power Jacket”. He was the boss. Who was I to doubt the sales energy emitting from his garb? Although it was not required in the office, many of the older sales engineers wore a sports jacket out of habit to work every day.
But somewhere in the mid-1980s, the dress codes changed. Jackets and ties were replaced by knit polo shirts with funny little logos embroidered on the left breast. Little griffins, or guys riding polo horses became the new norm. Neckwear became passé. A new generation was taking over the business world and with it, the dress codes were changing. And I changed right along with them. The comfort of polo shirts can seduce you, especially on hot summer days. Today neckties seem to be reserved for weddings, funerals, and maybe a holiday or two. I see a few older men like me that wear neckties to Sunday service. And except for a few individuals at the annual company Christmas party, I don’t think I have ever seen any of my coworkers wear a necktie.
A few years back I was feeling nostalgic and wanted to change my persona. I wanted to turn back time to the early days. I started to wear a necktie into the office every day. At the time I only had a few ties that I wore to weddings, funerals, and the occasional special event. But then I started to collect them. One of my favorite comedians was the late Harry Anderson. He once said, “Neckties satisfy man’s desire to dress in artwork”. This I can agree with. I’ve collected ties over the last several years and their designs range from the beautiful to the truly bizarre. I now have over 400 neckties and a few bowties as well. They cover just about any gambit you can imagine. I acquired most of these in used clothing stores. I rarely pay more than a dollar or two for a necktie. There is a special thrill to score a Jerry Garcia original in mint condition for .99 cents at Goodwill. My wife also scouts out unusual neckties for me. She has a flair for colors and patterns and when she finds something she knows I would like she picks it up. I even have a few friends who know of my fetish and occasionally bring me an unusual necktie they found.
Doctor Donald Wright, MD, MPH, is the former Head of Health Care Quality for OSHA. He is also a fan of wearing neckties. He said, “The more you look like an executive the better treated you are. It catches people by surprise.” Dhani Jones says, “When you wear a (bow) tie, doors open for you. Your posture is a little more erect. Your shoulders a little further back. It is all about the reestablishment of a gentleman.” I don’t disagree with either of these two men. I believe wearing a necktie adds to your professionalism. People notice you more when you wear a tie. This may be because tie-wearing has become so uncommon in today’s business environment.
But it could be that things are swinging back. I’m noticing more young boys wearing neckties to Sunday Services. Some high school athletic coaches are enforcing a dress code including neckties worn when their teams travel to other schools to compete. And I know of one young lad who liked to be a sharp-dressed tie wearer in his grade school years. When I see young boys wearing ties, I always comment on them because it makes you feel good to be complimented on your tie.
Of course, it is a personal preference to wear a tie. Going tieless does not diminish your skills in any way. Tiger Woods’ father once told him, “Just because you dress in a coat and tie doesn’t influence your intelligence”. That is true. You can be very successful in life and never wear a tie. But I would leave you with the wisdom of ZZ Top, “Every girl is crazy about a sharp dressed man”. If you don’t agree, well, good luck with that!
Read more
by Erin Long | Jan 24, 2020 | Hidden from Archive
This year at FABTECH, the new Shadow Compact Fume Extractor made its debut. With a huge demand in the market for a compact, low profile option for noncombustible dust, the Shadow definitely got a lot of attention. People looking for Imperial Systems quality at a lower price point are paying attention.
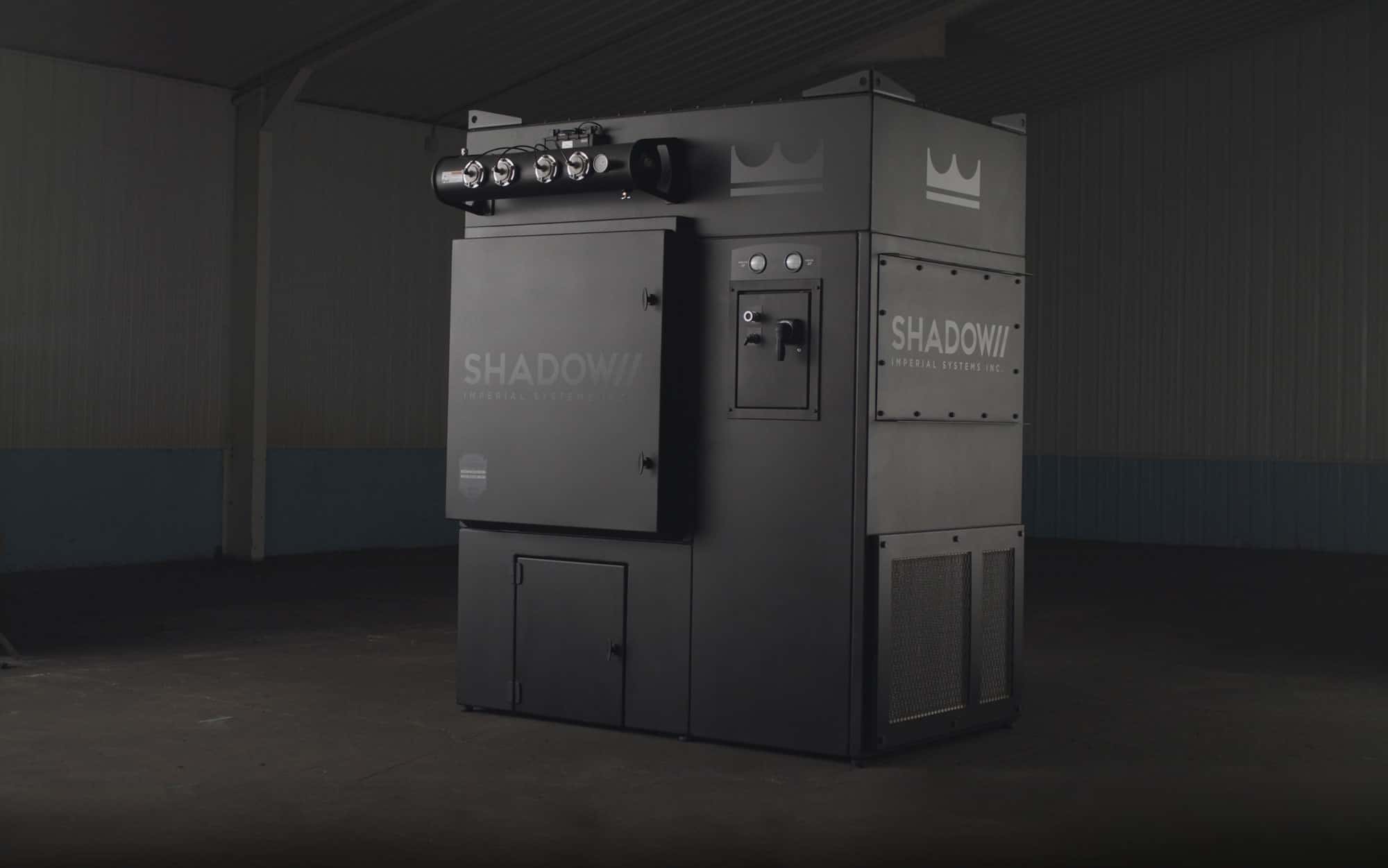
The Shadow is appropriate for indoor use only and for noncombustible dust. With premium filters it is equipped to handle applications like laser cutting, light loading weld fumes, and robotic welding. The Shadow may also be available for other applications; talk to us about your dust and we can determine whether this is a good choice for you.
Because the Shadow has been specifically designed for noncombustible dust, it is safe to install inside your facility. It doesn’t require any of the extra safety devices that are needed for combustible dust. Some applications will require a fully equipped CMAXX with fire protection. Feel free to get in touch to find out if your application is suitable for a Shadow.
Like the CMAXX, the Shadow will feature the new DeltaMAXX Prime filters. The Shadow includes anti‑ramp lift rails, which prevent filters from ramping over each other during installation. It also features a lift rail door stop system. This prevents the door from being closed unless the lift rails are locked in position. The Sure-Stop System adds an extra layer of protection, with a door indexing bar that interacts with the filter pans so the door can only be closed with filters in place.
Many of the features on the Shadow have been perfected on the CMAXX and now appear on its new, smaller cousin. The high quality DeltaMAXX Prime filters and the on-demand pulse cleaning make sure the Shadow runs just as efficiently and protects your facility from harmful dust and fumes.
The Shadow is backed by our 15 year limited warranty, and support is provided by our experienced ServiceMAXX team.
To learn more about the Shadow Compact Fume Collector, click here.
Read more
by Erin Long | Jan 24, 2020 | Hidden from Archive
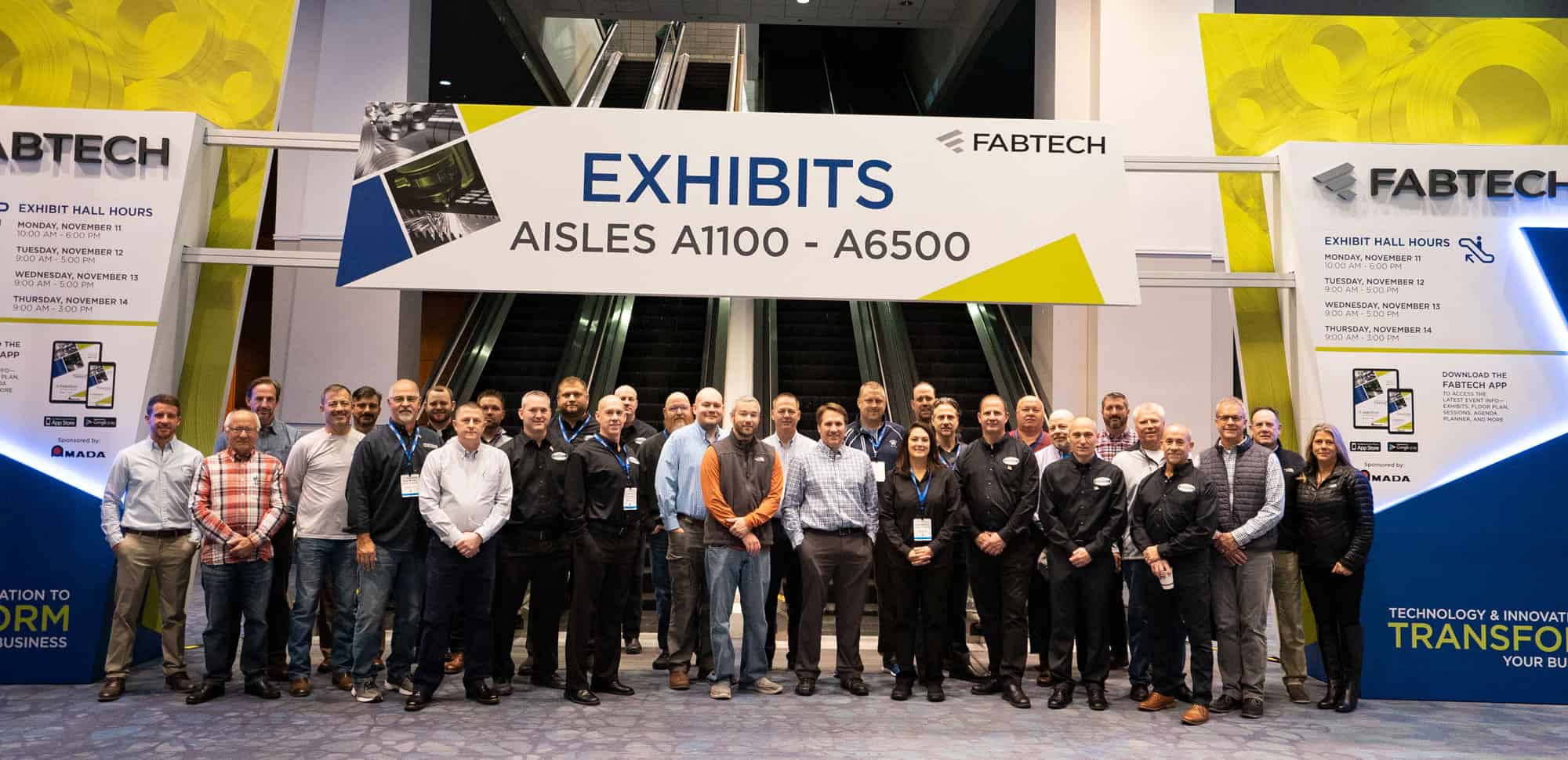
FABTECH is exciting every year, but 2019 was a special one for all of us. First, this year we invited all of our Imperial Systems representatives to join us in Chicago for a yearly sales meeting, after which many of them joined us in the booth to meet potential customers.
Second, this year we introduced two brand new products, the Shadow Compact Fume Extractor and the DeltaMAXX Prime filter. Along with these new products, the booth also included two CMAXXs and several other products on display.
Despite Chicago unleashing some unpleasant weather on the first day of the show, everyone who attended agreed that FABTECH and the sales meeting were both great successes. Reps from all over the country joined us in the booth, and we met people from all over the industry and all over the world.
One of our team noted it was a great learning experience, getting to see industry products and innovations from around the world.
“Fabtech is always a great opportunity to see what other companies are doing in comparison to what we are,” aftermarket salesman Donovan Karki reported. “I felt that the best part was seeing all of our competitors crawling all over our innovation on our equipment because theirs is just the same as last year.”
Competitors and potential customers alike took note of the innovations. Tomm Frungillo, Director of Sales and Marketing, noted that the reps at the sales meeting were also excited about the new products, and about the direction of the company in general. Due to growth during the year, several new faces were present at the meeting, and everyone seemed to find it beneficial.
South Central Territory Manager Justin Ferrainola observed that “there was a lot of buzz from the new Shadow unit. People seemed to really like the overall design and look of it.”
The DeltaMAXX Prime also impressed people by fitting 400 square feet of media into a cartridge that’s still light and easy to handle. The Safety Pentagon drew attention by preventing any errors or accidents in filter installation. Redundant features prevent the doors from closing on incorrectly installed filters, making it nearly impossible for someone to install them in an unsafe manner.
Erin Long, Graphic Designer, appreciated the chance to see the products being offered by our competitors, and to get a feel for how they are marketing themselves. As we move forward as a company with our marketing efforts, knowing the competition will help us stay ahead of the game.
With so much attention and interest drawn to our booth this year, we feel like FABTECH 2019 was a great success and another step toward establishing ourselves as one of the industry’s most innovative manufacturers.
Read more
by Erin Long | Jan 13, 2020 | Uncategorized
If you have a cartridge dust collector, you’re probably aware of the compressed air pulses that clean the filters. Although our header tank design controls noise levels, the cleaning mechanism isn’t exactly silent. If the dust collector pulse cleans the cartridge filters during normal operation, why would you need to run an offline filter cleaning?
Offline cleaning of your cartridge filters can remove extra dust from the filters, improve efficiency, and increase filter life. Keep reading to learn how offline cleaning works and what it can do to keep those expensive cartridge filters in service longer.
What is offline filter cleaning?
Offline cleaning means cleaning the filters while the dust collector is not in operation. For some baghouses, the fan can only clean the bags when they are offline. These baghouses have separate sections, and one section goes offline for cleaning at a time. Because this means part of the baghouse needs to shut down often, the system operates less efficiently. Some baghouse designs to avoid this and clean all the filters while still in operation.
For cartridge dust collection systems, offline cleaning means pulsing the filters with compressed air while the system fan is shut off. With no air moving through the system, equal pressure exists on the clean air and dirty air side of the filters. No air is pulling through the filters.
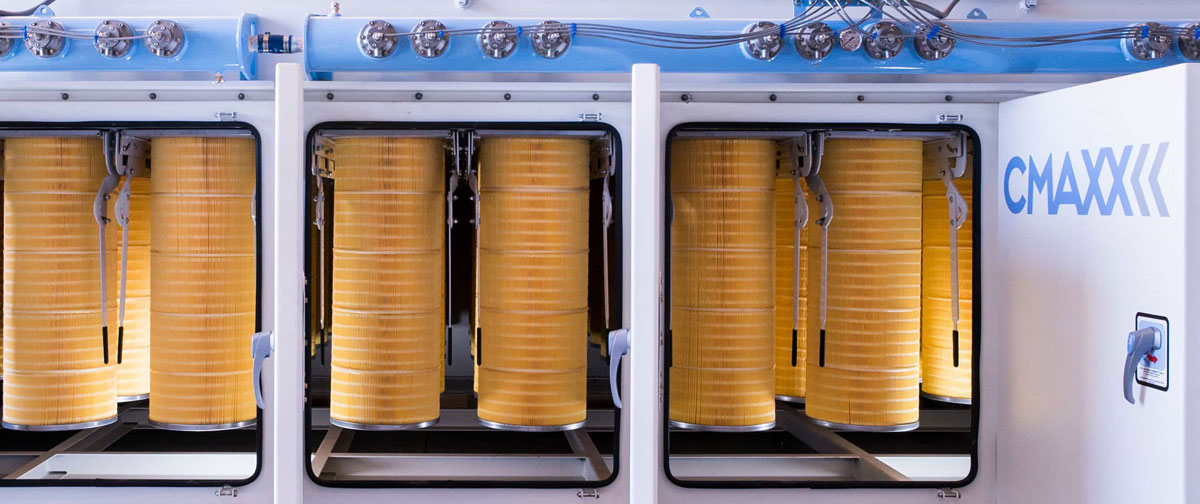
Why is offline cleaning good for cartridge filters?
With the dust collection system online, the pulses of compressed air blow down through the cartridge filters to remove dust. At the same time, however, the air being cleaned moves in the opposite direction, upwards through the filters.
Online pulse cleaning keeps the filters working well while the dust collector operates. However, the compressed air pulse and the system airflow move in opposite directions. To get maximum cleaning power from the compressed air pulses, run a quick offline cleaning.
With the system shut down, no airflow blows back against the compressed air pulse. This lets it release more dust from the filters. Regular offline cleaning can extend filter life significantly by removing this extra dust.
What if we don’t have time for offline filter cleaning?
Taking your dust collection system offline for filter cleaning doesn’t have to take a lot of time. Our service technicians recommend that for offline cleaning, you manually pulse the filters twice. Often, you can do this in less than ten minutes of downtime.
Employee break time or lunchtime can allow you to shut your dust collector down for a short time. On a dust collector with an integrated control panel, manually running two compressed air pulses just takes the push of a button.
After a short offline cleaning, the cartridge filters should work more efficiently. While online cleaning will keep filters working, regular offline cleaning makes them last longer. Also, keeping the filters at maximum efficiency helps to protect HEPA or other expensive after-filters.
Need some personal advice about offline cartridge filter cleaning?
You can contact us here at Imperial Systems for advice on keeping your filters performing well. If you need more help or would like a hands-on education in dust collector maintenance, our ServiceMAXX team can pay a visit and help you establish a maintenance schedule.
If you take the time to run offline filter cleaning, you should see it pay off in longer filter life. Not only does this save money, but it also cuts down on the much longer downtime needed to replace old filters. If you have questions about how often you should run offline cleaning or any other questions about your dust and fume collection system, please contact us.
Read more