by Erin Long | Oct 29, 2019 | Uncategorized
You’ve made the investment in a new Imperial Systems dust collection system. Now our technicians have arrived to help supervise the startup. While they’re there, is it time to invest in dust collector maintenance training?
Our experienced startup technicians know our products. They know how to maintain them to avoid problems. In addition, they know where to start troubleshooting if something goes wrong. Having this preventative maintenance training can save money on repairs or a service visit later.
While a dust collector maintenance manual guides you through the basics of system upkeep, many of us learn better with hands-on training for maintenance rather than by reading a manual. Our startup technicians certainly give you that hands-on experience with your system from the first day.
Why Get Training
You’ve made a major investment in your dust collection system. If you’ve purchased a CMAXX, you can expect many years of reliable service from it. However, no system runs forever without maintenance. Dust collector training teaches you how to keep your dust collection system working as it should.
Without proper maintenance, a dust collection system can run into many problems. For instance, some of these problems might shut down the system completely, causing downtime for your processes that rely on it. Further, other problems affect the system’s performance or increase the risk of a fire.
Preventative maintenance training is the best way to prevent expensive downtime and performance issues. A one-time training teaches you what to look for and how to address common dust collector problems. Many of our service calls address problems due to improper maintenance.
How Does Our Dust Collector Maintenance Training Work?
When you purchase a CMAXX, Imperial Systems startup technicians will usually perform or assist with installation. While that person is onsite, you may choose to have them provide training for your staff. With their help, you can develop a dust collector maintenance checklist. As a result, this will allow staff to feel confident performing preventative maintenance and keep the system running.
At your request, we will schedule industrial maintenance training for your dust collector when technicians are onsite for installation. The procedures covered in the training will depend on the details of your system. The training may include:
- Monitoring differential pressure and when to change filters
- Correct filter changeout procedures
- Checking solenoid and diaphragm valves for leaks
- Making sure compressed air is pulse cleaning filters correctly
- Checking door and filter seals
- Checking the function of fire and explosion safety devices
- Troubleshooting common problems
The startup technicians provide this training to the staff responsible for the system maintenance. If you choose to have this training provided, discuss this with your Imperial Systems sales representative. The training almost always pays for itself by preventing expensive problems and repairs.
How to Sign Up for Maintenance Training
Talk to the Imperial Systems representative who works with you on your dust collector project. They can add preventative maintenance training as an option. They can also tell you about our dust collector startup service.
If you are the current owner of a CMAXX or BRF dust collector from Imperial Systems, you can schedule a ServiceMAXX visit. One of our experienced technicians will come to your facility. They can perform repairs, troubleshooting, or scheduled preventative maintenance on your dust collector.
Many of our customers schedule ServiceMAXX visits on a yearly or quarterly basis. The technician provides preventative maintenance. Contact your Imperial Systems sales representative to schedule a ServiceMAXX visit or to discuss a dust collector maintenance training program.
Related:
Blog post: 7-Step Dust Collector Maintenance Checklist
Downloadable PDF of Preventative Maintenance Checklist
Read more
by Erin Long | Oct 24, 2019 | Uncategorized
When your facility has a problem with accumulated dust, general housekeeping can take up a lot of valuable time. An industrial central vacuum system greatly cuts down on dust cleanup time. This type of system is also more NFPA compliant and safer. Instead of brooms and shop vacs, look at a central dust collector to keep your facility clean.
Central Systems for NFPA and OSHA Compliance
OSHA’s National Dust Emphasis Program has been on the scene since 2007. Two years after implementing it, OSHA reported that poor housekeeping made up a large percentage of the violations. Other violations included accumulated dust on surfaces, visible dust clouds, and using compressed air to blow the dust off surfaces.
The most recent NFPA standards for combustible dust handling recommend dust control equipment like central industrial vacuum systems. You may not use compressed air to get rid of accumulated dust. You also may not use any types of vacuums or other industrial suction machines unless they are designed for industrial, combustible dust use.
If your facility has dust accumulation, you may need an industrial vacuum dust collector. Other signs include visible dust or smoke in the air. If you use compressed air to blow the dust off surfaces, you need a safer way to deal with this problem.
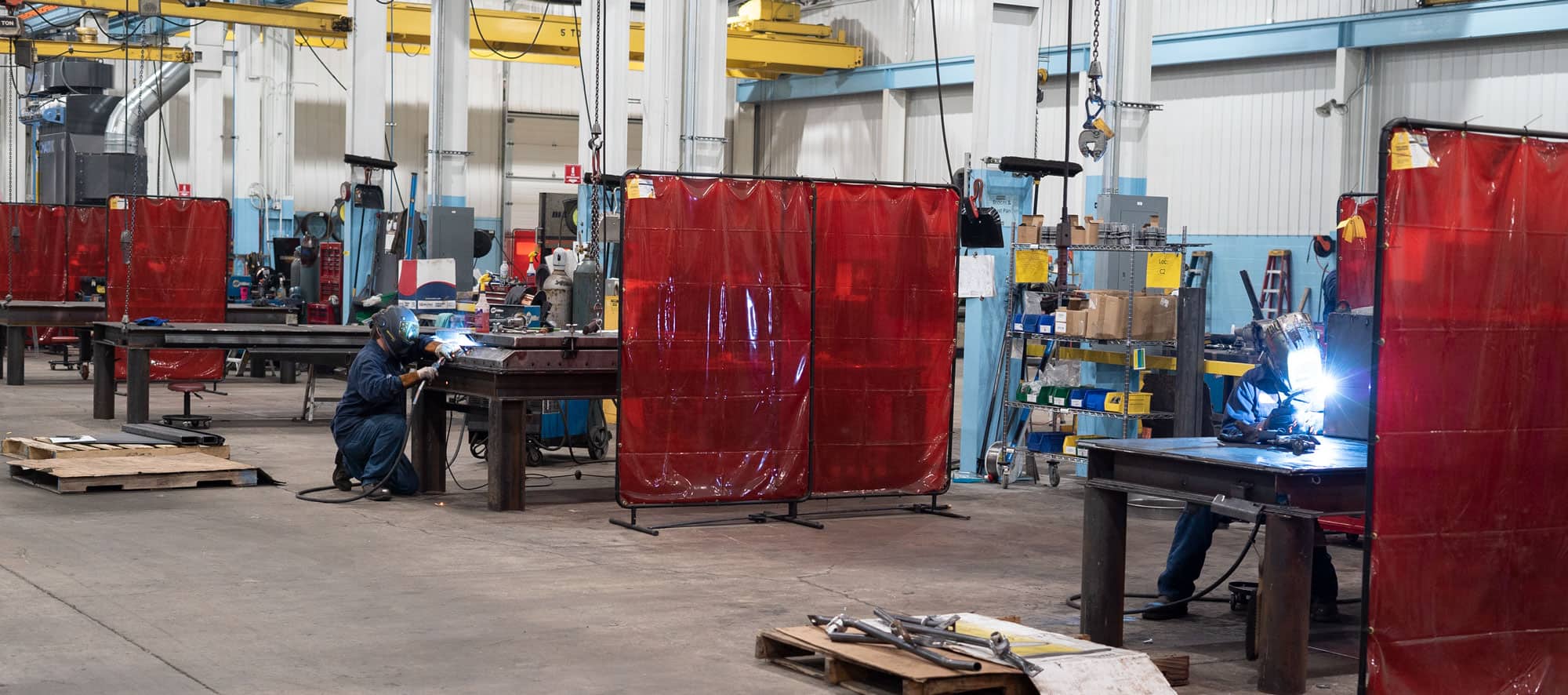
Saving Time and Money with an Industrial Central Vacuum System
Housekeeping tasks take workers away from their regular jobs. Sweeping, vacuuming, and clearing dust eats up hours of useful work time. Also, since most people don’t like housekeeping tasks, they are often neglected.
Dust can build up quickly inside a facility. In many cases, an easily controlled equipment fire ignites accumulated dust. These secondary explosions kill and injure more people than the first, smaller one. Dust built up on overhead structures can ignite and fall on people as they try to escape.
An industrial central vacuum system will remove dust from the air before it can settle. Without dust all over the floor and floating around, you’ll spend much less time on housekeeping tasks. In our shop, where we use central industrial vacuum systems, there’s no dust built up in corners or overhead. Housekeeping requires a quick sweep under some of the workstations at the end of the day.
When workers can spend more time doing their jobs and less time cleaning up dust, your business works more efficiently. A central dust and fume extraction system can work constantly to clean the air. This eliminates the need for constant sweeping and vacuuming. It also greatly decreases the risk of an accident, preventing harm to workers and damage to buildings and equipment.
Choosing and Installing a Central Vacuum System
Several factors will affect which industrial dust collection system you need. While you will certainly consider the cost, don’t make the choice based just on saving money. Some companies deliberately design an undersized system that can’t handle the necessary airflow.
An undersized central vacuum system costs less, but it cannot move enough air to keep your work area clean. Also, a low-budget system may use cheap filters that need replacing more often. Filters have a much longer life in a well-designed system.
Installing an industrial central vacuum system usually requires installing ductwork or vents that pull the air through the dust collector filters and return it to the building. Often, this is set up as a “push-pull” system where vents on one side of the building push clean air in, while on the other side they pull dirty air out.
The type of dust in your facility is another important factor. Some materials produce toxic or harmful dust that must be removed at the source. This requires a source capture system, which captures dust and fumes at the spot where they’re produced.
Call and ask one of our experienced system designers to assess your facility. They will help you decide if an industrial central vacuum system will work for you. Many factories produce a lot of dust, and they rely on this kind of system to maintain air quality.
Read more
by Erin Long | Oct 16, 2019 | Uncategorized
Need to make sure your dust collector startup goes smoothly? System startup service from Imperial Systems lets you have a technician on hand to manage the process. Even the best dust collection systems can experience minor glitches on startup. With our startup service, you’ll have someone onsite to keep everything on track.
Advantages of Our Dust Collector Startup Service
- System startup technician onsite through the startup process
- Help from someone who knows the details of your system
- Up and running quicker saves money and downtime
- Minor issues fixed before they become problems
- All wiring and compressed air hookups checked and running
- Experienced technician to walk you through your system functions
During your startup service, the Imperial Systems technician will walk you through the startup procedure. They will also guide you through the important parts of your system. They will help you feel more confident that your dust collection system is hooked up and running correctly.
Customers might run into minor problems or have questions during the dust collector startup. Our technicians can be on hand to get things back on track. Even better, they’re there in person, so they can teach you how to solve problems yourself in the future.
If you have questions about your dust collection system, the startup is a great time to ask. Schedule a system startup service and our experienced technician will answer your questions. They’ll show you where things are, and also give you some guidance for keeping your system running smoothly.
Other Dust Collector Services
If you already have a dust collection system, consider a visit from our ServiceMAXX team. This team of experienced technicians can do routine maintenance, troubleshooting, or repairs. Many of our customers rely on ServiceMAXX visits to help them:
- A company’s toxic dust requires full-body safety suits to change filters. This makes filter changes time-consuming and difficult. They have regularly scheduled ServiceMAXX maintenance visits so our team can do the dirty work.
- A facility that struggled with short filter life called in a ServiceMAXX team. Our technicians performed troubleshooting and recommended a different filter material. This solved the problem.
- A company in a state with strict air quality standards has a ServiceMAXX team visit yearly to inspect the system and check for leaks. This keeps them in compliance and prevents future issues.
- After a fire in their dust collector, a company called in the ServiceMAXX team to assess the damage. The team made repairs and recommended safety equipment that will prevent future fires.
- Changing hundreds of bags in a large baghouse can be a huge, time-consuming task. That’s why one of our customers has a ServiceMAXX team come to do the dirty work instead of wasting their employees’ time doing it.
You Don’t Have to Be a Dust Collection Expert
Our customers do many different jobs, but most of them aren’t dust collection professionals. Fortunately, you don’t have to be.
With any new system, you can run into problems. Having a dust collector startup service team onsite means you have a professional to make everything run smoothly. We offer a dust collector system startup so you can get up and running with minimal downtime.
An existing dust collection system needs maintenance to keep working well. You can schedule regular ServiceMAXX visits to handle your preventative maintenance. If your dust collector isn’t running as well as it should be, our technicians can troubleshoot and fix the problem.
Dust Collector Startup Service FAQs
Q: How far will your team travel?
A: Our technicians travel all over the country. If necessary, they will schedule an overnight trip.
Q: What kind of equipment or supplies do we need to provide to your team?
A: Any equipment that our technicians can’t travel with, you will have to provide. If they will need personal protective equipment, please make them aware of this before their visit.
Q: How much does the service cost?
A: The cost of a visit depends on the services provided, among other things. If you call to set up a visit, we will review the expected costs with you before scheduling.
Q: Do you provide service for other manufacturers’ dust collectors?
A: We can provide service for any dust collector, not just our own. Our technicians have experience working on a wide variety of systems.
If you’re purchasing an Imperial Systems dust collection system, talk to us about the system startup service option. We can also add dust collector maintenance training as another option. If you already have a system and it needs maintenance or repairs, call us to schedule a ServiceMAXX visit!
Read more
by Erin Long | Oct 3, 2019 | Uncategorized
Every time a combustible dust accident happens, you can make two assumptions. Firstly, preventing the accident could have been done with a combustible dust safety program. Secondly, the accident, or one just like it, probably happened before. Maybe at a different company or in another place, but some things stay the same. With combustible dust accidents, history does repeat itself.
Your Dust Safety Program Needs to Learn From the Past
The U.S Chemical Safety Board (CSB) has investigated several combustible dust incidents. They analyze failures in procedures, awareness, training, and equipment. They also make recommendations for how to prevent similar incidents.
However, companies often make the same mistakes, especially in developing a combustible dust safety program. Certainly, no business wants employees harmed. Furthermore, it’s not greed or disregard for human life that causes these incidents. Lack of awareness poses the greatest danger.
The best way to make your combustible dust safety program strong is to learn from others’ mistakes. Just because nothing has happened yet doesn’t mean the risk can be ignored.
The Imperial Sugar explosion is often cited as the most destructive incident in recent history. But there have been many others.
Lessons Learned: What Your Dust Safety Program Must Address
This facility made rubber components for the medical industry. Their process included dipping the rubber into a tank of polyethylene and water. Killing six people, the building blew apart when accumulated polyethylene dust exploded.
The facility had a housekeeping plan, and they kept the areas around the machines clean. The process had switched from a zinc stearate powder to the polyethylene powder several years previously.
Despite good housekeeping practices, dust escaped into the air and traveled through the ventilation systems. Unfortunately, the facility’s drop ceiling provided a space for the dust to accumulate, unseen. Some maintenance workers reported an inch or more of dust in this space.
This accumulated dust exploded. The building suffered so much damage that they could not determine the ignition source. The explosion ignited other flammable materials, causing even more damage.
- Lesson 1: Combustible dust can accumulate in unseen or unexpected places, even when the machine area looks clean.
- Lesson 2: Process change management could have determined that the new polyethylene dip created a new risk. Changes in a process must be assessed for any new hazards.
- Lesson 3: Dust testing saves lives. The polyethylene dust was more combustible than anyone realized. Even safety inspectors had not addressed combustible dust risks.
This facility made fiberglass insulation for automotive industries. Resin applied to the fiberglass accumulated in dust form. Seven people died when this resin dust exploded, starting secondary fires.
The plant ran several production lines. A baghouse collected dust from these lines. Manually pushing a button to blast compressed air through the bags is what cleaned them. But this required shutting down the lines. The more common method involved employees opening the baghouse and hitting the bags with a stick.
Because of a process change a few years previously, debris from the baghouse fell into a cardboard box on the production floor. Large ovens operated inside the facility, and compressed air cleaning also led to accumulated dust. Debris from other areas was dumped on the roof for disposal. Dumped debris for disposal was on the roof.
The baghouse needed to be replaced, and management knew this but chose not to budget for new baghouses at the time they were requested. A new baghouse, put in place in 2002, was not operational at the time of the accident.
The initial explosion appears to have occurred in or around one of the ovens, igniting secondary explosions and spreading to other ovens. Flame also traveled into the baghouse, causing another explosion.
The lessons here are:
- Lesson 1: A poorly operating dust collector puts the entire facility at risk. Overloaded, dirty bags and unsafe dust disposal (keeping the material inside the building) led to this incident.
- Lesson 2: When dealing with combustible dust, compressed air should never be used for general cleaning. It raises clouds of dust that can settle out of reach overhead. NFPA standards warn against compressed air cleaning in work areas.
- Lesson 3: A combustible dust safety plan did not exist. Many employees didn’t know the dust was combustible. The danger of storing combustible dust in cardboard boxes and on the roof was not addressed.
- Warning signs went unrecognized. The employees commonly put out small fires in the furnaces, considering them a minor problem. However, each fire could have ignited a dust explosion.
The facility produced wheels made of aluminum alloys for the automotive industry. One person died in the explosion of aluminum dust. Despite dealing with highly explosive aluminum dust, the company lacked a combustible dust safety plan. Aluminum chips and dust could be found in piles several inches deep.
The explosion occurred in part of the plant where a processing system melted down aluminum chips and scrap. A cyclone filtered out the aluminum chips, while dust and particles traveled into a dust collector. On the day of the incident, chips had backed up in the dust collection system and started backing up into the ducts.
An explosion ignited inside the dust collector, blowing back through the ductwork into the building. The venting on the dust collector did not meet NFPA standards, and the collector sustained major damage. The building also lacked mechanisms to prevent fire or explosion from entering the building. The explosion blew out of duct hoods and burned people standing nearby. Secondary explosions followed.
- Lesson 1: A combustible dust safety plan must include housekeeping. When interviewed, employees and management told investigators they didn’t realize the buildup of dust could be dangerous.
- Lesson 2: The dust collector did not meet NFPA standards. It could not withstand the force of the explosion or vent it safely. It also had no prevention to keep flame from traveling back into the building.
- Lesson 3: The facility drastically underestimated the flammability of their dust. It’s impossible to make a safety plan without understanding the materials being handled.
Preventing Gaps in Your Combustible Dust Safety Program
These are just a few of the examples that the CSB has collected over the past 20 years. In another incident, a newly installed dust collector failed. The resulting flash fire burned 7 people. In a facility with a history of accidents, accumulated iron dust exploded when an employee struck a dusty tank with a metal tool.
These injuries and property damage are preventable.
A combustible dust safety program should include:
- A dust collector designed for your application
- Fire and explosion safety features in the dust collection system
- Housekeeping to remove dust, even in hidden places
- Maintenance of machines that handle dust
- Control of ignition sources
- Dust testing and employee awareness of dust hazards
- Combustible dust training, including how to manage a combustible dust incident
Your process may require other precautions. A hazard analysis can identify areas of concern.
Learning From the Past to Prevent Future Harm
“We’ve always done it this way,” or “We’ve never had a problem before,” is not a reason to ignore combustible dust issues. You may never have an accident that tests your dust safety controls.
However, if an accident happens, it can cause facility damage, injuries, and loss of life.
Previous incidents point to mistakes in safety processes. We can prevent these mistakes from happening again. A full dust hazard analysis will identify potential problems before they become accidents. If you need help addressing dust problems in your facility, contact us for help.
Read more
by Erin Long | Oct 2, 2019 | Uncategorized
Here it is! Dusty Jobs 10 takes a look at the 2019 AWFS Fair in Las Vegas as well as a recent CMAXX installation for a high school wood shop. Charlie talks about the difference between blue boxes, green boxes, red boxes, and our boxes. Lastly, we bid a retirement farewell to Carl Callen, a twelve and a half year employee with Imperial Systems. If you would like a printed hard copy of this issue, contact your Imperial Systems, Inc. representative.
Click the cover to download and print the newsletter.
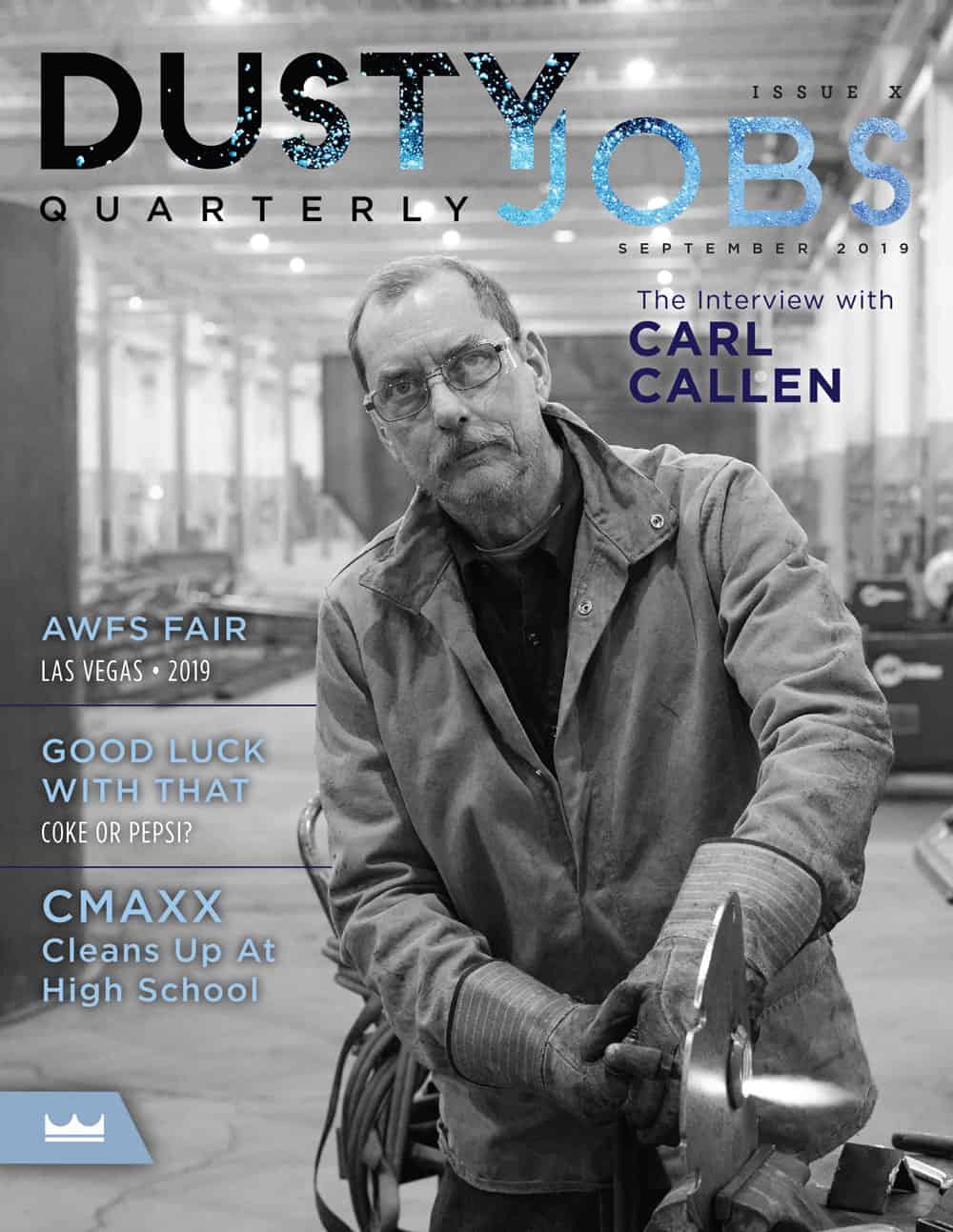
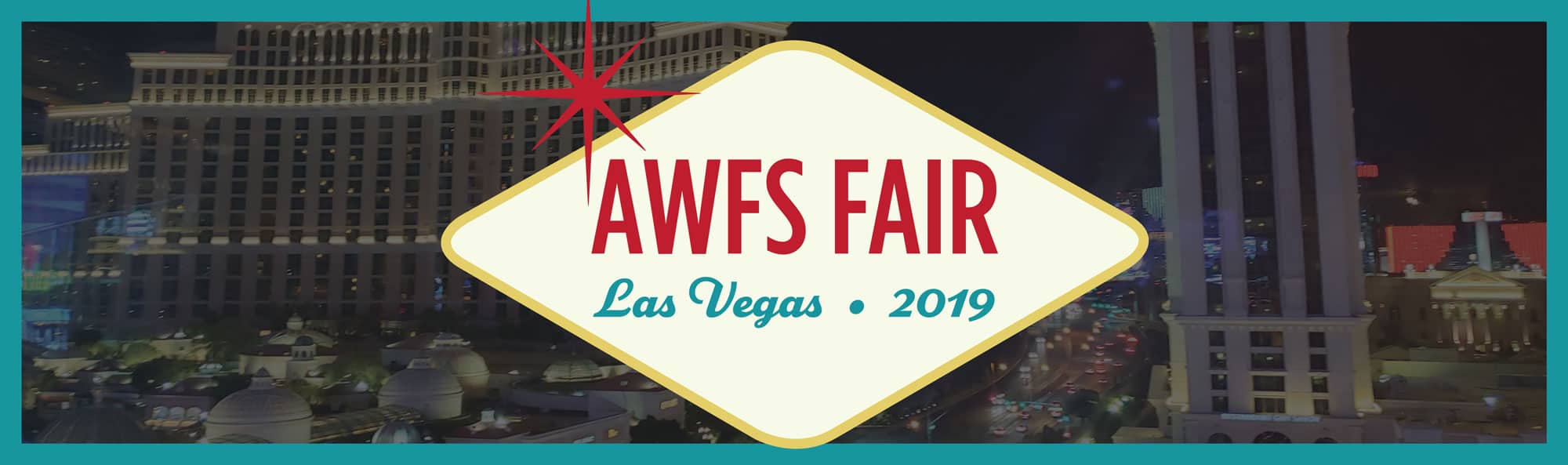
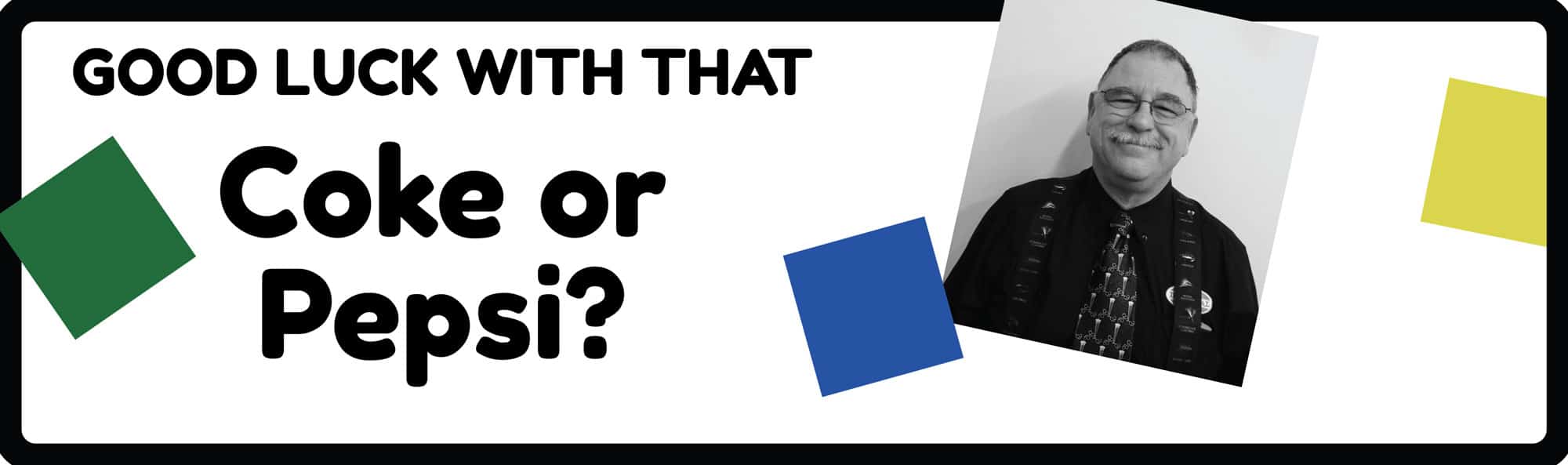
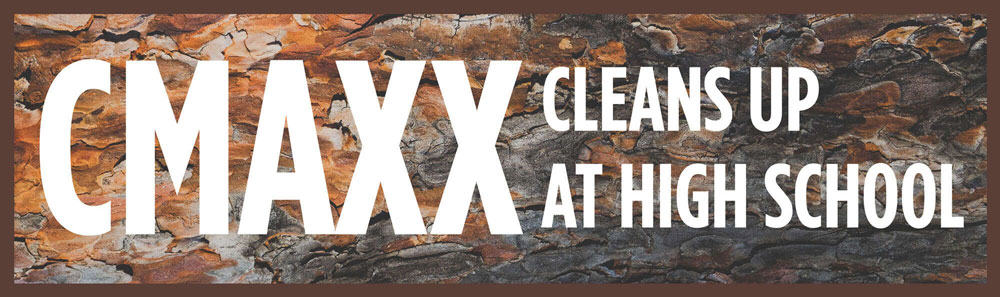

A Letter from the Supply Chain Manager
About six years ago, I was presented two job opportunities at the same time. The first was a local company that was about a 5 minute drive from home, well established and had a decent reputation to work for. The second opportunity was Imperial Systems. This was at least a 35 minute drive. I had never heard of them, and they were offering less money than my first opportunity. Now, in a simplistic world this would have been an easy decision to make.
I sat and discussed this with my wife, all the pros and cons from each establishment and what would be the best long-term decision for my family and myself. The decision was pretty easy on what I had to do, but it wasn’t easy. There was something about the Imperial Systems interviews that had me thinking this would be a good company, one that I want to be a part of and want to work for. As I told my wife what my decision was, she was kind of shocked but 100% supportive of my decision.
As life progressed forward with Imperial, I noticed this was a special place to be working and different than any other companies I have worked for in the past. Being in the supply chain field for over 25 years, I realized how the company operates fundamentally, and the integrity standards that need to be upheld takes priority over the so called “bottom line”. I have worked for a few different companies, some large and some small. This was the first time in my career I ever felt they have the same beliefs as I do on how people and challenges in the everyday work place should be addressed. Every once in a while I do sit back and think to myself on how I actually made the decision to choose Imperial over the other place. It is beyond me, and it basically comes down to two things: (1) willing to take the chance and (2) faith. And this without a doubt is one of the best decisions I have ever made. I know companies will say “we are like family” but never actually do anything when an employee is in need. Personally, I had to deal with some extended family medical issues in the past and Imperial Systems has always treated me and the situation as if it was their own while not even thinking twice about it. When I say Imperial Systems is “a different place to work for” or “special” they are not words just being spoken but actual actions that were taken that leads to this.
The experiences, thought processes, and knowledge from the owner to the vice president and all the team members are valuable lessons we learn together and practice together. I will never forget the challenges we had when we were discussing our plan on moving to the new building. Some of us just looked at each and wondered how we were going to do this. The plan, moving a complete facility in about a weeks’ time from manufacturing to the administration offices without shutting down and not missing ship dates, seemed insurmountable. As this started there would be meetings, plans, and goals that were set which to some companies would be nearly impossible. Long story short, we did it, and that’s when you will sit back and realize you are working for a special place with great team members and have the attitude that you “want to” and never feel you “have to”.
To work at Imperial Systems is something to be proud of. We take great pride in what we do and how we do it, so at the end of the day we can look another person straight in the eye and tell them “we are the best”.
– Mark Ranelli, Supply Chain Manager
Read more