by Erin Long | Sep 19, 2019 | Uncategorized
Performing regular maintenance keeps your dust collector working properly. When something goes wrong with it, you can lose money in repairs and system downtime. Some of the tips in this dust collector maintenance checklist take only a minute or two. But some do take a bit longer. Keeping up with this basic maintenance certainly prevents future problems.
Fortunately, all these maintenance steps can be performed by almost anyone with an owner’s manual. Set a schedule and check off these tasks when finished. Not only does this keep your dust collector working well, but it also provides documentation that you performed regular inspections.
Dust Collector Maintenance Checklist
1. Record your differential pressure.
Differential pressure measures the difference in pressure between the dirty and clean air sides of the collector. High differential pressure indicates that the filters are creating a lot of resistance. When the differential pressure reaches about 5” WG, filters need to be replaced.
By monitoring differential pressure regularly, you’ll notice any changes. For example, if differential pressure suddenly drops a lot, you may have a hole in a filter or a leaking gasket. Consequently, this lets air get through more easily by bypassing the filters.
2. Check drums and hopper.
Overflowing your dust collection drum can create a mess. Worse, it can also seriously damage your dust collector. Drums must be emptied before the dust reaches the top. Fortunately, installing a dust level sensor can help monitor this.
If drums overfill, the dust can back up into the hopper and into the dust collector. Firstly, this may damage the filters. Secondly, it creates a dangerous situation where dust could ignite inside the dust collector.
3. Inspect valves and hoses.
Diaphragm and solenoid valves control the pulses of compressed air that clean your filters. These valves can become damaged or leak. This causes a loss of compressed air. It also means that filters may not get cleaned effectively.
Check these valves regularly. First, make sure that when the cleaning system pulses, all the valves work at the same time. Second, make sure that the valves open all the way and close all the way. Check that all hoses are attached and inspect them for leaks.
4. Examine door seals and gaskets.
Dust collector doors have a seal that keeps air and dust inside. This gasket around the edges of the door can become worn out or cracked. If this happens, the door will not seal properly.
Open the dust collector doors and inspect the gaskets. If they appear to be damaged, they should be replaced. Air leaks can allow dust to escape. They can also allow air to be pulled into the dust collector. This can keep the system from moving air properly.
5. Check compressed air pressure.
Pulse-jet dust collectors clean their filters with compressed air. This removes dust from the filters to keep them working well. If the compressed air pressure is too low, the pulse jet cleaning system can’t clean the filters efficiently.
If compressed air pressure is too high, filters could be damaged. Check the pressure of the compressed air regularly. It should be at the setting specified in your owner’s manual.
In addition, never take your filters out and blow them off with compressed air. This damages the filters, causing holes and tears in the material. Let the dust collector cleaning system do its job and change filters when needed.
6. Inspect airlock wipers.
Many dust collection systems include an airlock. NFPA standards often require airlocks to isolate a fire in the dust collection system. You must replace the wipers inside the airlock when they are worn out.
We recommend that you replace airlock wipers once a year, or sooner if needed. Damaged wipers will reduce the airlock’s performance. We also recommend that when you inspect and replace wipers, you also replace the wiper bearings. These wear out with use and can be damaged during wiper changes.
7. Lubricate fan bearings.
Your fan motor will normally come with an owner’s manual. This specifies which bearings need lubrication and how often. Make sure your maintenance schedule includes time to keep these bearings lubricated.
If your fan stops working or must be shut down for repairs, the dust collection system will be out of operation. As a result, you may not be able to keep up with normal production. Maintenance of the fan, including bearing lubrication, takes less downtime than a broken fan.
Your Maintenance Schedule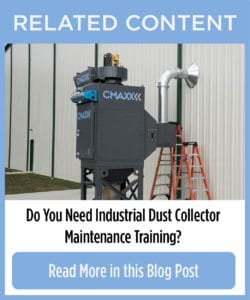
Like any other industrial equipment, your dust collection system requires regular maintenance. Fortunately, you can perform this maintenance using the above Dust Collector Maintenance Checklist without wasting too much time.
Maintenance also helps you identify problems. For example, if you notice the differential pressure getting high, you can order a new set of filters and have them ready for a changeout. If you notice issues with a diaphragm valve, you can replace it quickly instead of wasting compressed air.
Download PDF Checklist
ServiceMAXX Maintenance: Help for Your Dust Collector
An Imperial Systems ServiceMAXX technician can perform routine maintenance on any manufacturer’s dust collector. Nobody likes dirty work like changing filters, but you can schedule a ServiceMAXX visit and have someone else do it.
ServiceMAXX saves time so your own team can keep working while we deal with your dust collector. And if you do have a problem, the ServiceMAXX team specializes in finding and fixing dust collection system problems.
Industrial dust collection systems can run into problems. You can prevent many of them with a good preventative maintenance plan. Others may require a visit from an experienced service team to troubleshoot and make repairs.
Please contact us to schedule your ServiceMAXX visit today for help with your dust collector maintenance or repairs.
Read more
by Erin Long | Sep 12, 2019 | Uncategorized
This infographic looks at various coal mine disasters in the US through history and the changes that were made to standards as a result of these issues. It highlights the advancements made in Pittsburgh that lead to innovations in miner safety across the nation. It also takes a look at the effects that coal dust can have on the health of both miners and their families.

Coal dust has been the cause of some of the worst mining disasters in American history. Whether it has combusted on its own or propagated a methane explosion, coal dust can be dangerous and potentially deadly.
Upper Big Branch Mine Disaster – Raleigh County, WV • April 5, 2010 • Twenty-nine miners died
Benwood Mine Disaster – Benwood, WV • April 28, 1924 • One hundred and nineteen miners died
Castle Gate Mine Disaster – Castle Gate, UT • March 8, 1924 • One hundred and seventy-one miners died
Stag Canon No. 2 Explosion – Dawson, NM • October 22, 1913 • Two hundred and sixty-three miners died
Monongah Mine Disaster – Monongah, WV • December 6, 1907 • Three hundred and sixty-seven miners died and it is considered the worst mining disaster in American history.
Harwick Mine Disaster – Cheswick, PA • January 25, 1904 • One hundred and eighty-one miners died
Working Towards Mine Safety in Pittsburgh
In 1910, the United States Bureau of Mines purchased land in Bruceton, PA, just south of Pittsburgh. It was purchased from the Pittsburgh Coal Company for research and testing purposes. There were three main focuses at this facility: Mine Health, Mine Safety, and Disaster Prevention.
National Mine Safety Demonstration – Forbes Field, Pittsburgh • October 30th, 1911 • 15,000 attendees
International Conference of Representatives of Mining Experiment Stations – Pittsburgh, PA • September 14-21, 1912 • Attendees included representatives from Austria-Hungary, Belgium, German, and Great Britain.
Coal Dust in Post-WWII America
Coal dust explosion research expanded to industrial and agricultural dust after WWII with the National Defense Research Committee. In 1969, the Federal Coal Mine Health and Safety Act:
- Required more inspections of mines
- Strengthened safety standards and adopted health standards for the first time
- Provided compensation for miners with black lung
- Was signed by Nixon
In 1970, mine owners began taking dust samples. By the end of that year, the Bureau of Mines had issued 714 excessive violation levels and 1,589 failure-to-initiate sampling notices.
Later in the seventies, the 1969 Coal Act:
- Mandated further research on occupational lung disease factors
- Provided information on pneumoconiosis and other respiratory ailments
- Improved mandatory health standards
From 1973 to 1999, Coal Workers’ X-Ray Surveillance Program showed the prevalence of pneumoconiosis in miners with 25 or more years on the job had fallen by 31%.
Read more about mining dust collection.
Read more
by Erin Long | Aug 30, 2019 | Uncategorized, Woodworking
Choosing the right type of dust collector for your industrial woodworking application can improve safety and save money. Wood dust is highly combustible, and as a result, it causes many accidental fires and explosions. Industrial woodworking applications may include cutting, planing, sanding, routing, and sawing. The process and the type of wood help determine your dust collector options.
Wood Dust Filtration Challenges
Many industrial woodworking facilities use several different machines for wood processing. As a result, they produce dust that contains a variety of particle sizes and characteristics. This makes each woodworking dust collection system a unique project.
Because wood dust can absorb water, in a moist environment it can become sticky and start to form clumps of material. Also, wood particles can be sharp-edged and abrasive. The most serious challenge, however, is the highly combustible nature of wood dust. Regardless of the type of dust collection system, it must always include appropriate fire and explosion safety devices.
What Are Your Choices?
Wood dust collection may use any type of dust control system. This includes cyclones, baghouses, and cartridge collectors. Often, a woodworking application may use more than one type of dust collector.
For example, a company that produces large pieces of wood and fine sawdust may use a cyclone to drop out the large material. Then the airflow may proceed to a cartridge collector for the capture of the fine dust. Another company may use a baghouse for wood dust because the material is sticky or fibrous.
The Cyclone
First option: a cyclone, which removes large pieces of wood or clumps of sticky material. Because a cyclone doesn’t use any filters, it can handle abrasive or other harsh materials. A cyclone only handles material heavy enough to fall out of the air stream. Lighter dust will pass through.
As part of a wood dust collection system, a cyclone works to remove the rougher materials that might cause problems in a baghouse or cartridge collector. With finer dust, however, you need a dust collector that captures small particles. This means using filters.
The Baghouse
One option for a dust collector with filters is baghouse. Baghouses use long cloth bags as filters. These collect dust on the surface. To keep them working efficiently, the baghouse cleans its bags by using fans or compressed air. Older baghouses may shake the bags to clean them, but this is a messy and high maintenance method.
Baghouses excel at capturing fibrous or sticky dust. They can handle very heavy dust loading, and they also handle high temperatures. One serious downside of a baghouse is the work required to change the bags. One baghouse may have hundreds of bags, and nobody wants the job of replacing all of them in a tight, dirty space.
Size can be another issue with baghouses. To provide the needed surface area, baghouses need lots of bags, making them very large. Not all facilities may have any issue with this, but some may seek a smaller, more compact option.
The Cartridge Collector
That smaller option is a cartridge dust collector. The pleated cartridges provide much more surface area in a smaller space. The woodworking industry uses cartridge collectors more often as they prove their usefulness. Woodworking applications such as sanding dry wood produce very fine sawdust.
A cartridge dust collector efficiently captures this fine dust. Pulses of compressed air clean the filters. This gives them a longer filter life, especially in vertical cartridge collectors. Cartridge collectors work well for fine sawdust, but they also work well for dust that contains contaminants that need to be captured.
Some contaminants in wood dust may include resins, adhesives, and dye pigments. Since any of these could cause illness or harm if released into the air, a dust collection system must control these materials. A cartridge collector has the highest filter efficiency for small particles. This means that it captures even very fine dust. With added after-filters, the efficiency goes even higher. Spunbond filter material with PTFE coating will resist most materials, even sticky or damp dust.
What to Consider Before Choosing a Dust Collector for Woodworking
These factors will affect what type of dust collection system you may need. However, this is not a substitute for having your facility assessed by a dust collection professional. Factors include:
- Particle size
- Abrasiveness of dust
- Type of woodworking process
- The moisture content of the material
- Contaminants
- Space and cost considerations
- High-temperature conditions
- Amount of dust loading required
- Filter and maintenance costs
For example, a baghouse will require more downtime and maintenance labor to change out filter bags. Cartridge collector filters take less time and effort to replace. On the other hand, bags withstand high temperatures and harsher materials.
Industrial Woodworking Dust Control
Whatever type of dust collection system you choose for your wood dust, make sure the system meets NFPA standards for fire and explosion safety.
Wood dust fires are very common and can spread very quickly. A well-designed system will have safety features to protect people and property. All types of woodworking dust collection require these controls.
Wood dust can easily escape and accumulate around work areas. You can control this fire hazard by using source capture dust collection, where the system captures dust at the source. For example, hoods located over woodworking machines can pull the dust away before it gets loose in the facility.
The best way to find out which type of dust collector is right for your application is to contact one of our dust collection experts. We can discuss your woodworking processes and help you choose the type of system that will work best to control your wood dust.
Read more
by Erin Long | Aug 28, 2019 | Uncategorized
In the past, we have been asked if our dust collectors are OSHA compliant. The truth is that there is no specific standard for an OSHA compliant dust collector. OSHA standards cover many different aspects of your dust collector, from electrical wiring to ladder safety. However, we assume that what most people are asking is “Will your dust collector give us OSHA compliant air quality?”.
OSHA Regulations for Dust Collectors
OSHA does not currently have a standard that regulates the function of a dust collector. But it does have housekeeping standards, which limit how much dust can accumulate in the facility. Failure to remove accumulated dust can result in an OSHA fine.
OSHA also has a National Emphasis Program for combustible dust. This program means that OSHA inspectors will be investigating facilities that might have dust problems. OSHA does not have a specific standard for how the dust needs to be removed, except the General Duty Clause. Specifically, this requires that employers take all reasonable precautions to protect workers from harm.
Further, OSHA considers dust collectors to be a form of engineering control. For control hazards, the preferred OSHA method is to remove the hazard. This would mean removing the process that makes dust. Since most facilities can’t do this, the next preferred method is an engineering control. This means a solution that is part of the process to control the hazard.
As an engineering control, a dust collector is one of OSHA’s preferred methods for controlling dust hazards. However, this does not mean it is an OSHA compliant dust collector. OSHA does not have a standard for exactly how a dust collector must be built or how it must work. The only rule is the General Duty Clause to keep employees safe.
NFPA Standards for Dust Collectors
When many people think of OSHA regulations for dust collection, they actually mean NFPA standards. Our dust collectors, when fitted with appropriate fire and explosion control methods, meet all NFPA standards for dust collection.
NFPA standards specify how fires should be safely vented (NFPA 68) and controls for explosion prevention (NFPA 69). More recently, the NFPA has established standards for the control and safe handling of combustible dust (NFPA 652 and 654). NFPA 484 also specifically deals with combustible metals.
While there is no OSHA compliant dust collector, a dust collector may or may not meet NFPA standards. These are not OSHA regulations, and you cannot be fined for them. However, many insurance companies and local regulations use NFPA as their legal standard. OSHA may also use NFPA standards to determine if employers are providing a safe environment.
Exposure Limits Do Require OSHA Compliance
OSHA regulations do cover exposure to dust. Many types of dust certainly cause harmful effects with too much exposure. OSHA has a set exposure limit for most types of dust. While the dust collector itself may not have an OSHA regulation to meet, it helps companies meet the OSHA exposure limits.
OSHA usually regulates exposure by how much dust the person is exposed to over a typical workday. Dust collectors can remove dust from the spot where it is created (source capture) or from the entire workspace (ambient).
By removing dust from the work area, a dust collector keeps the exposure levels within OSHA compliance. Different types of dust may require different system designs to achieve this compliance. A system designer will assess each dust-producing process.
So, is there an OSHA compliant dust collector?
If you are referring to the removal of dust, there really isn’t an OSHA compliant dust collector. OSHA does not have specific regulations for dust collectors. In contrast, NFPA does have standards for dust collection systems. Therefore, most employers will need to meet these standards.
A dust collection system is a tool to help you achieve OSHA compliance with many other standards. Dust collection systems can achieve compliance with safety, housekeeping, and exposure control. Imperial Systems’ dust collectors are designed to help you achieve compliance.
A dust collector like a CMAXX needs proper safety features to help achieve this goal. This may include explosion vent panels, abort gates, explosion isolation valves, spark traps, and fire suppression. NFPA standards usually require these features for combustible dust.
To find out if you are meeting OSHA regulations in your facility, you can hire a safety consultant to review all your potential hazards. If you need to know whether your dust collector is working correctly, a ServiceMAXX visit can assess and make any needed repairs. Contact us today to schedule a ServiceMAXX visit.
Read more
by Erin Long | Aug 22, 2019 | Uncategorized
Welding trade school programs offer students an opportunity to pursue a career in a necessary, important field. Not everyone wants or needs a college degree. Many young people want a successful career without the burden of huge student loan debt. Some people prefer to work with their hands and like a job that challenges their skills.
People have different reasons for attending a trade school program. However, they all want a quality education that prepares them for the future. They also all want to learn in a safe environment with clean air and no health hazards.
Trade school programs often struggle to balance tight budgets. Welding trade school programs need the same type of safety equipment that welders on the job need. This includes effective fume extraction. Obviously, trade schools take the safety of their students very seriously. But with shrinking budgets, some schools can’t get approval for many things, including updated weld fume extraction.
Suggestions for Welding Trade Schools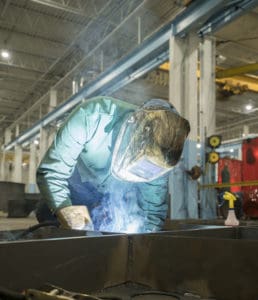
Since extra money doesn’t usually appear in school budgets, trade school programs have to think about efficiency and the best value for their money. So, here are some suggestions for getting the best fume extraction with the funds available.
- Firstly, invest in high-quality dust collector filters. Bargain filters don’t work as well, and they don’t last as long. Trade schools for welding will end up saving money by using a DeltaMAXX nanofiber filter that won’t need replacing all the time. Conversely, bargain hunting for filters may lead to wasting money on frequent replacements.
- Secondly, keep up with system maintenance. A service visit can replace worn out parts and identify problems. Without maintenance, failing parts can cause a fume extraction system to lose efficiency or break down. While welding trade schools might struggle to find the money for maintenance and replacement parts, a total system breakdown could shut things down completely.
- Finally, make sure hoods or fume arms are being used correctly. Welders, or students in welding trade school programs, often don’t use these as they should. A hood can get in the way or a fume arm might need to be adjusted often. While these fume extraction tools might be a minor inconvenience, they also keep weld fumes from escaping. Training welding trade school students to work with a hood or fume arm is good for safety and fume extraction efficiency.
Time to Invest in a New Fume Extraction System?
Eventually, any trade school for welding may have to invest in a new system for weld fume extraction. Budget limits will always be a consideration. However, money saved on a cheaper solution might be money spent on repairs when bargain parts break down.
Also, cutting corners on the quality of the fume extraction system may lead to poor performance. Welding tech school programs are responsible for the safety of students. A system that won’t remove weld fumes efficiently is not a bargain.
Worst of all, a cheap system may not have the fire and explosion protection that a weld fume extraction system needs. A fire inside the system could burn up your filters, damage the building, and require evacuation because of smoke.
How do trade school programs convince administrators to approve funding for a more expensive system when there are cheaper ones available?
Contact us at Imperial Systems Inc and let one of our dust and fume collection experts help. We have years of experience working with welding school trade programs all over the country. We can show you why CMAXX is the best long-term value for the money. Students entering welding vocational schools make an investment in their futures, and a CMAXX is an investment in the future of your program.
Learn more about welding fume extraction.
Read more