by Erin Long | Aug 21, 2019 | Uncategorized
Indoor shooting ranges are popular across the country. Many law enforcement professionals and private gun owners use these ranges to practice their target shooting. However, in an enclosed space like this, lead dust exposure can become a dangerous problem.
OSHA has cited gun ranges in the past for failure to control lead dust. Specifically, excessive lead dust can accumulate on surfaces and in the air. This can quickly exceed the permissible exposure limit. The OSHA limits for exposure to lead are very low because it is so toxic.
Lead Dust Exposure at Indoor Gun Ranges
In 2019 OSHA cited an indoor shooting range for exposure of lead dust. Because they often don’t have proper ventilation, lead dust levels in indoor gun ranges can be very high. Consequently, the penalties for the 2019 case in Texas totaled over $200,000. One of the major issues the company faced was using brooms to sweep up dust and lead debris. Another issue is the company’s failure to address damaged personal protective equipment or do medical testing.
Lead dust exposure at indoor gun ranges can be higher than many people realize. A review of several scientific studies found that people who spend time in indoor gun ranges have blood lead levels up to 40 times higher than the average person (Lead Exposure at Firing Ranges – A Review).
This elevated exposure even applied to people who only attended one shooting event. It took days to weeks for lead levels to return to normal after just one event. People who regularly use an indoor shooting range, with regular exposure, may have unsafe lead levels.
Another issue noted by OSHA and the same scientific studies found that a major risk is lead dust was accumulating around the facility. People using or working in an indoor gun range can pick up lead dust on their clothes or bodies. This dust then goes home with them and can affect others with lead exposure.
Lead Dust Control in Gun Ranges
Gun ranges usually have a strong focus on safety and proper gun handling. However, they need a dust control system to prevent shooters and workers from lead dust exposure. The OSHA-cited facility in Texas attempted to clean up their dust and debris with brooms. This does not remove the dust. Instead, it pushes it into the air, where it settles onto surfaces.
The employees doing the sweeping are at high risk, but anyone inside the gun range will experience exposure. Even without stirring up dust on the floor, shooting produces airborne lead dust around the shooting area. Even if employees take precautions during cleaning the area, shooters wear no respiratory protection. This means that only a dust collection system can control lead dust exposure.
Simple ventilation will not solve the problem. The EPA regulates emissions of toxic materials like lead. The best solution is an industrial dust collection system. You can use a cartridge dust collector as an ambient system. This type of system cleans lead dust out of all the air in the facility on a continuous basis.
Rather than venting lead dust into the environment, a dust collector will capture the dust. Cartridge dust collector filters are highly efficient for small particles. If needed, after-filters can be added to make sure all the lead dust is captured.
Advantages of a Dust Collector for Shooting Ranges
A dust collection system will help a shooting range control lead dust exposure in several ways.
- Remove lead dust from the air around the shooters, keeping their exposure under control during shooting.
- Continuous dust removal prevents lead dust from accumulating, limiting the exposure that happens when workers sweep or clean up lead dust.
- The efficient filtration prevents the outside release of lead dust and keeps it from getting back into the building.
- Cartridge dust collectors are easy to maintain. Pulses of compressed air clean the filters, unlike HVAC filters in a regular ventilation system.
- Safely contain lead dust. It can be disposed of according to local regulations. Material contaminated with lead is less likely to end up in the environment.
A properly designed dust collection system will clear the gun range of most lead dust. This lowers exposure and makes cleanup easier and safer. Lead exposure in gun ranges could cause health problems. Protecting workers and shooters should be a priority. A CMAXX dust collection system offers an efficient way to decrease lead exposure and remove lead dust.
Read more
by Erin Long | Jul 31, 2019 | Case Studies
PROBLEM:
A company in Ohio produces parts for the aerospace industry using a salt bath. The modern aerospace industry relies on salt baths to treat metals for corrosion resistance. However, the high heat and particulate from this process caused serious problems for the company’s dust collector.
The company used a baghouse for their dust collection. However, the fumes, heat, and corrosive material caused rusting. The baghouse itself rusted, but so did the cages inside that support the bags. Corroded and damaged cages made changing the bags a challenge.
In addition, the facility produced such a fine dust that some of it escaped the baghouse. The fugitive dust often ended up in the building’s parking lot. The baghouse could not filter out this very fine particulate.
SOLUTION:
The company contacted Cardinal Air Design, an Imperial Systems representative in their area of Ohio. The dust collection system professionals at Cardinal Air Design developed a new system for the company. The new system uses a CMAXX cartridge collector, a CM006.
The cartridge filters provide the efficiency to capture the very fine particles from the salt bath application. In addition, the new system included special design features for this tough application. Insulation helps the ductwork withstand the heat. The CMAXX collector itself has an epoxy-coated interior and a stainless steel tube sheet. These features allow the collector to resist corrosion in this difficult salt bath application.
Because cartridge filters do not rely on metal cages for support, a cartridge dust collector avoids the issues of bag cages rusting. The higher efficiency of the cartridge filters also allows the capture of the very fine particulate, which had been a problem for the bags.
FEEDBACK:
With the new system in place, the company now has a reliable solution for its salt bath dust collection. The DeltaMAXX filters prevent dust from escaping, putting an end to the accumulation of fugitive dust outside the building. With the epoxy coating and stainless steel tube sheet, the company expects the CMAXX to hold up to the corrosive conditions.
In addition, the company appreciates the work of Cardinal Air Design, who assisted through the process. The specially designed dust collector and duct work solved some difficult problems. While a dust collector for a corrosive salt bath application posed a challenge, the company now has a good solution.
Read more
by Erin Long | Jul 24, 2019 | Uncategorized
Companies hold responsibility for their air pollution control and management. The EPA lists its “Big Six” air pollutants. Above all, the two of these that concern our customers the most are lead and other particulate matter. This can include many kinds of industrial air pollution. The EPA certainly enforces limitations on these.
In addition to the EPA, many companies are hit with negative publicity when news sources call them out as major polluters. For example, these companies in Pittsburgh have been accused of failing to develop or maintain air pollution controls. To make things worse, the report lists the proximity of the companies to local schools. Thus, it highlights that they are endangering children.
No company wants to be in violation of the EPA’s Air Pollution Control Act. You also don’t want the bad name and harmful attention that comes with being named as a major pollution source. So how do we control air pollution? Let’s focus on dust emissions.
Dust Collection for Control of Air Pollution
A dust collection system can help manage air pollution, especially the release of lead and other particulates. The EPA recognizes two types of particles: PM10 and PM2.5.
Particulates rated as PM10 measure around 10 microns or smaller. Meanwhile, PM2.5 particles are the most dangerous. They are 2.5 microns or smaller. The lungs will deeply inhale these. Many industries produce particles this small. So they all need strategies to curb industrial emissions.
Welding and plasma cutting are common processes. For most metalworking applications, a dust collector with DeltaMAXX NanoFiber filters will provide control for air pollution. This is important whether you circulate the air back into the facility or release it outside.
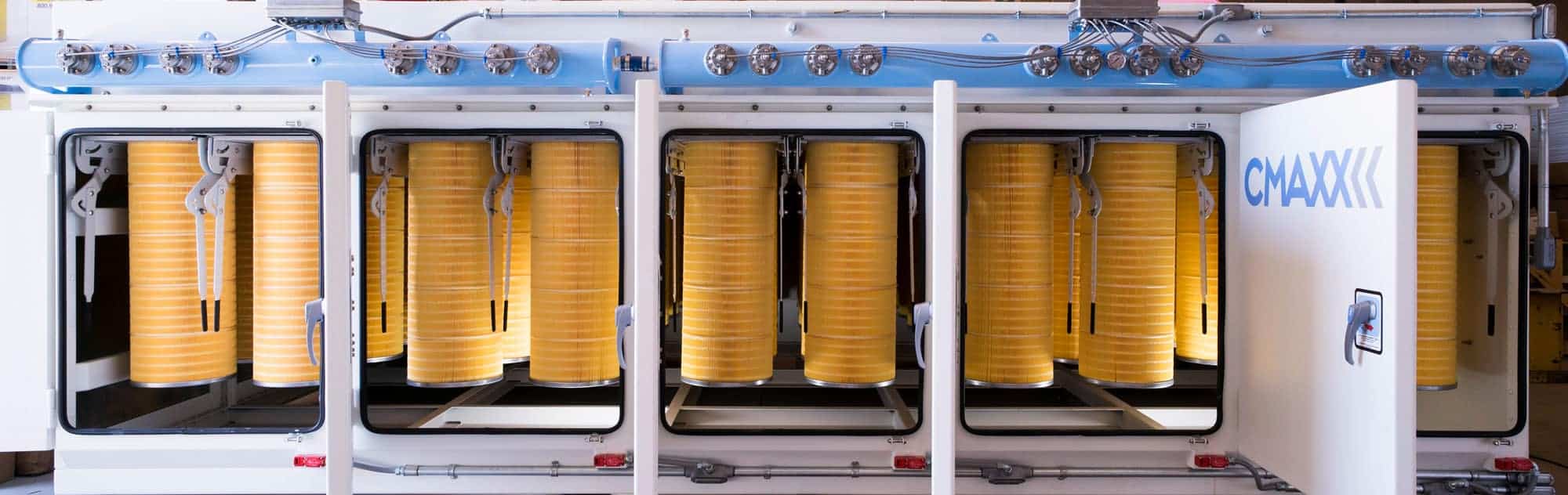
Nanofiber material is efficient down to 0.3 microns. This much smaller than the EPA’s 2.5 micron size range. If your application is producing dust that isn’t especially toxic, this type of air filtration should be sufficient.
Some materials, however, are more toxic and might need an additional level of filtering. For these applications, add HEPA filters after the main filters to increase efficiency. HEPA filters can be up to 99.99% efficient. “Clean rooms” that must be completely dust and germ-free often use them.
Materials that create a serious health hazard include hexavalent chromium. This dangerous chemical is produced from working on stainless steel or chrome-plated metal. Lead, often the product of battery manufacturing is a major hazard. Beryllium, the subject of new OSHA regulations, causes fatal lung disease.
Occupational and Environmental Agencies
Most companies are aware of OSHA and EPA regulations. They are regulatory agencies and can both issue fines for noncompliance. However, they regulate different things. So you can be compliant with one and not the other. (Learn more in our blog post: Is There an OSHA Compliant Dust Collector?)
OSHA regulates occupational hazards or ones that happen during work. They would be concerned with air pollution management and control in the workplace. This might be silica exposure on a construction site or metal fumes from a cutting table.
The EPA regulates environmental hazards. These are exposures that could harm people and the environment. Not all of them come from industrial air pollution. Many states, especially California and several states in New England, have adopted standards much stricter than the EPA’s rules. In California, the San Joaquin Valley Air Pollution Control District, Placer County Air Pollution Control District, San Diego Air Pollution Control District, and Ventura County Air Pollution Control District outline their tough standards on their websites.
In 2012, the Association of Air Pollution Control Agencies was formed. Its purpose is to create a technical forum where ideas, information, and best practices could be shared among state air quality agencies. You can visit this website for more information about the EPA in your own state.
OSHA measures limits for indoor industrial air pollution as a time-weighted exposure. This means that the limit considers the exposure an employee has over a specific time. The EPA usually measures air pollution in parts per million. In other words, the number of dangerous particles in the air.
Let’s Do Our Part
We need to clean up dirty air by reducing air pollution from many places. Industries are one major source of air pollution, but power plants, large forest fires, and heavy car traffic are other important sources.
Clean air inside and outside your facility isn’t just a way to avoid fines. It’s every company’s responsibility to its workers, their neighbors, and the world around us.
Read more about Imperial System’s efforts towards clean air.
Read more
by Erin Long | Jul 23, 2019 | Case Studies
Problem:
A precision tooling manufacturer needed help managing their welding and cutting fumes. This company manufactures high quality, precision machined parts for many different industries. Their priorities are customer satisfaction, quality workmanship, and quick turnaround times.
The company also prioritizes employee health and safety. So they understood the need to control the welding and cutting fumes from their precision tooling processes. Their facility had problems with fumes in the air during production. Because of this, they began researching dust and fume collection companies.
Solution:
The company contacted Imperial Systems via our website. Above all, they needed a high-efficiency system designed by a company that understood the needs of a precision tooling facility. They also needed quick and efficient installation to minimize downtime in production.
The company chose Imperial Systems based on our extensive engineering experience and the knowledgeable, professional sales team. To streamline the process, Imperial Systems designed a system with a CMAXX CM006 dust and fume collector. The system had hoods for all welding and cutting stations, and it also included all ductwork and fittings.
The Imperial Systems field team installed the entire system. During the process, they were able to complete the installation with minimal downtime for the facility. As a result, the company was pleased with the installation process. They were also happy with the performance of their new system.
Feedback From the Precision Tooling Manufacturer
The plant manager reports that after one month of continuous operation, the CMAXX is performing beyond expectations. The DeltaMAXX filters are maintaining high efficiency. Imperial Systems achieved the company’s goal of providing a clean, safe working environment free of welding and cutting fumes.
The plant manager of the precision tooling manufacturer stated, “The installation went very smooth. The Imperial Systems field crew is fully dependable and always clean and neat. All around good people.”
At Imperial Systems, we strive to provide a quality experience for customers. This starts with their first interactions with the sales team. Then it continues through engineering, delivery, installation, and support.
Contact us to learn more about this case study or how we can help solve your own welding or metal cutting fume collection problem.
Read more
by Erin Long | Jul 23, 2019 | Case Studies
This company is the largest lead fabrication company in the United States. They are second only to battery manufacturers in the amount of lead-based products they manufacture. Examples of these include drywall, plywood, lead strips, discs, and sheets.
Problem: Lead Fabrication Process Heat Melted Inferior Filters
Because of the stress that lead fabrication dust puts on filters, this company had filters failing every few months. They reported that this was due to the filters they were using, which were “very poor quality.” As a result, the filters overheated inside the dust collector, melting the filter media.
Due to the health and safety hazards presented by lead dust, the company needed efficient and reliable filters. But the filters they purchased from the manufacturer of their dust collector continued to melt down and fail within months of install. In other words, hard chunks of media fell off the filters as they broke down.
Solution:
The company researched filter manufacturers and spoke to a sales representative at Imperial Systems. We were able to find a match for their current manufacturer’s filters. The company decided to replace its current filters with DeltaMAXX oval nanofiber filters.
The new filters proved to be much more durable. Above all, they handled the challenges of lead fabrication without falling apart. They also lasted much longer than the original manufacturer’s filters. As a result, the company no longer experienced filter meltdowns or chunks of filter material falling off.
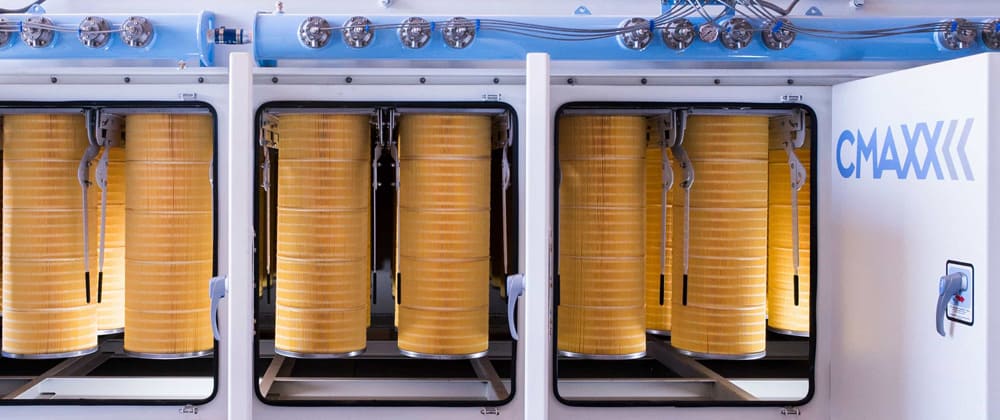
Feedback:
The company continues to purchase DeltaMAXX filters from Imperial Systems. As a customer for years, they are still happy with the quality and pricing of the filters. The filters continue to perform well in their dust collector and hold up to the demands of their lead fabrication work.
“The cost has been great per unit when we compare to other companies,” our contact reported. “The cost has been more competitive and the quality has been much better. The cartridge itself is much more durable compared to what we used in the past. Every time we have asked for a quote or response, we have always gotten a fast response. The information we got from Imperial about their DeltaMAXX filters has been as advertised. The product is less expensive and the quality is better.”
Contact us to learn more about this case study, DeltaMAXX filters, or how we can help solve your own dust collection problem.
Read more