by Erin Long | Jul 23, 2019 | Plasma Cutting
As one of the world’s largest manufacturers of wood chipping and grinding equipment, this company constantly faces high demand. A switch to a vertical cartridge dust collector helped them to solve a serious problem.
Problem:
With logging and sawmill industries relying on them, the company employs over 350 welders working ten-hour days, five days a week. The company had purchased a dust collector with horizontal cartridges to handle their welding and plasma cutting fumes.
Unfortunately, the horizontal filter design created serious problems. The arrangement of the filters trapped sparks and embers, causing multiple fires inside the dust collector. Fires like this are dangerous and expensive, requiring replacement of damaged filters.
In addition, OSHA regulations continued to limit what types of dust could be blown outside. So the company needed a better dust and fume collector. The new system would have to handle plasma fumes, meet OSHA standards, and be easier to use than the current one.
Solution: A Vertical Cartridge Dust Collector Design
Dave, the maintenance manager, began researching dust collector manufacturers. He had three goals in mind: easier filter change-outs, decreasing the risk of fires and reducing company downtime. He found out about Imperial Systems through the company’s cutting table manufacturer.
The company decided to make the replace the collector with horizontal filters with a vertical cartridge dust collector. Their new system, a CMAXX CM010, met Dave’s requirements. It also promised to handle the company’s need for efficient filtration of their welding and plasma cutting fumes.

“When changing the filters on our old dust collector, there were twelve different holes I had to unbolt just to change one filter,” Dave said after working with the CMAXX. He added, “The simplicity of maintenance was huge and the CMAXX has delivered.”
In addition, the vertical filters do not allow embers or sparks to sit on them and start fires. Without dust collector fires, the company no longer had to waste work time replacing fire-damaged filters. To reduce the risk of fires even more, Imperial Systems recommended a Spark Trap. This prevented most of the burning embers from getting to the collector in the first place.
Feedback:
The company reported that they have not experienced any more issues with fires since switching to the vertical cartridge CMAXX and Spark Trap. Also, Dave reported that maintenance takes much less time and is much easier. In addition, the efficiency of the DeltaMAXX filters allows the company to be compliant with all their OSHA air quality regulations.
The company has since purchased another CMAXX, a CM006, for another cutting table. They are using DeltaMAXX fire-retardant filters in their dust collectors. They continue to work with Imperial Systems for their filters and dust collector service needs.
Contact us to learn more about this case study or how we can help solve your own problem with welding or plasma cutting fumes.
Read more
by Erin Long | Jul 23, 2019 | Case Studies
Problem: Fugitive Cement Dust
This facility is part of a worldwide company. They manufacture chemicals and building products for many different industries. For example, waterproofing, roofing, and flooring products contain their chemicals. Their customers include home improvement stores, contractors, automakers, and construction companies. The problem this facility had, though, was cement dust.
The company was having issues with the reliability of its dust collection system. To the point, the system was not maintaining a clean atmosphere in the plant and could not manage the dust load. Further, the company struggled to find a dust collector provider who had the knowledge and quality product they needed.
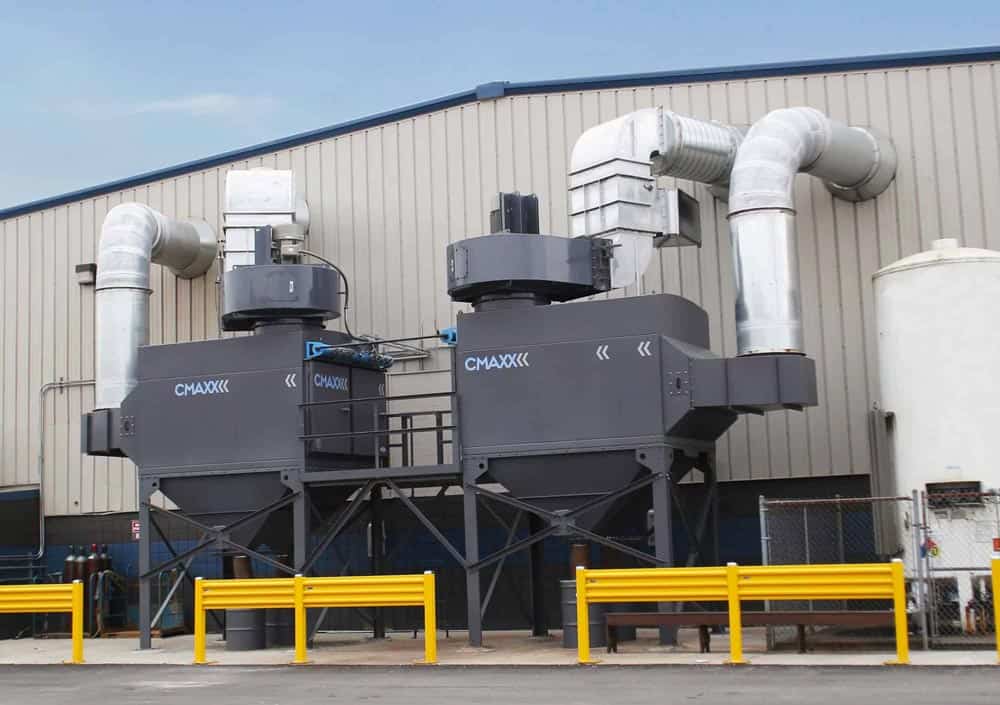
Solution:
The company reached out to a seller they were familiar with. Fortunately, they introduced them to Imperial Systems’ products, including the CMAXX cartridge dust collector. Because of Imperial Systems and their sales rep, they now have a company that can be their ongoing partner in dust collection.
The CMAXX model CM016 easily handled the company’s cement dust issues. In addition, the DeltaMAXX filters provided good filter life and easy filter changes. The CMAXX certainly didn’t have any of the reliability or maintenance problems their old collector had.
Feedback:
The CMAXX continues to impress the company with how well it handles its cement dust. Also, responsiveness and personal service continue to please them. When asked about working with Imperial Systems, they said, “We got improved operations and an ongoing partner. The CMAXX is easy to use, reliable, and is saving us energy costs while enhancing our clean air recovery.”
The company continues to be a customer of Imperial Systems, purchasing DeltaMAXX replacement filters. They report that they are still happy with the performance of their CMAXX. Above all, they have not experienced any of the failures or issues they had with other dust collectors.
Contact us today to learn more about this case study or how we can help solve your own dust collection problem.
Read more
by Erin Long | Jul 23, 2019 | Case Studies
Problem:
A PVC recycling company planned an expansion project in Nevada. This company pulverizes, then recycles PVC products. However, they encountered air quality standards much more rigid than those they had dealt with before.
“Our main concern was a blue smoke emitting during this process,” said Kurt, Director of West Coast Operations. The company needed a guarantee that its new dust and fume collection system would meet air quality standards at their new location. Other dust collector manufacturers could not offer them the guarantees that they required for their expansion project.
Solution: Tailored Baghouse for PVC Recycling Process
When they contacted Imperial Systems, President and CEO Jeremiah Wann was willing to make the guarantee and stand behind it. Imperial Systems designed a BRF baghouse for the company. To make sure the PVC recycling process met air quality standards, the system also included an after-filter plenum. The after-filters made sure that even traces of the dust and smoke could be captured.
As required by Nevada law, the company had a licensed mechanical contractor onsite during installation. Imperial Systems also sent a technical supervisor to oversee the process. Kurt noted that the installation process went very smoothly.
After connecting and running the system, Kurt knew Imperial Systems was living up to their guarantee. “There’s no visible smoke, and the odor is gone.” The system managed the larger particles and the fine dust produced in the PVC recycling process. The PVC pulverizers no longer emitted fumes or odors into the atmosphere.
Feedback:
The new dust and fume collection system meets the company’s needs. It also meets all their air quality requirements. Kurt felt that Imperial Systems stood behind their guarantee. “It is performing exactly as we were told it would,” he said. “The system has been in operation for over a year now, and there’s no hint of dust or fumes from the system’s discharge.”
Kurt recommends Imperial Systems to anyone struggling with dust and fume collection challenges. “Our collector is doing exactly what Imperial said it would do, and in business, that’s the bottom line,” he said. The proof is always in the results, and Imperial Systems delivered.
Kurt also expressed satisfaction with the service received from the Imperial Systems team. “I’m very satisfied. Everyone I had dealings with has been helpful, knowledgeable, and pleasant. Imperial worked everything out to my satisfaction, which made it a good experience overall.”
Contact us to learn more about this case study or how we can help solve your own dust or fume collection problem.
Read more
by Erin Long | Jul 23, 2019 | Case Studies
Problem:
Masaba is a metalworking fabrication company. They manufacture bulk handling equipment for mining, agriculture, and other industries. Because of the size of the equipment, the facility has high ceilings and large open workspaces. This allowed weld smoke and fumes to accumulate in the air. They needed an effective shop exhaust system.
The company used an old, roof-mounted HVAC unit as their shop exhaust system to pull weld fumes from the facility. But the amount of weld smoke produced during daily production overwhelmed the air extraction unit. Consequently, the unit was returning dirty air back into the facility. The president of Masaba, Jerad Higman, certainly knew that his employees needed clean air to breathe. Further, they needed and a clean working environment.
Solution:
Jerad contacted representatives from several of the industry’s biggest names in dust and fume collection. All offered their industrial exhaust systems for the weld fume problem. However, Jerad met Jeremiah Wann, president and CEO of Imperial Systems. The two developed a strong working relationship. Jerad trusted Jeremiah with producing a shop exhaust system for his weld smoke.
As a solution, Jeremiah and Jerad chose an ambient system. This type of system circulates all the air in the facility through the filters and returns clean air. The company installed three CM020 units, CMAXX units with 20 cartridges each. The system also included hoods over each welding bay. These would capture weld smoke before it could escape into the rest of the facility.
Feedback on New Shop Exhaust System:
With the new system installed, the company quickly saw the weld smoke start to vanish. Circulating all the air in the facility six times per hour, the new system had the power to get rid of the lingering smoke and fumes. Instead of a modified HVAC system, Masaba now had one designed to handle large-scale weld smoke extraction.
“I was very impressed at how effective the CMAXX collectors were operating,” Jerad said. “To this day, I have not experienced any problems with them. I would highly recommend Imperial Systems products to anyone that has issues with the air quality in their shop. Their level of expertise and service is just outstanding.”
Imperial Systems prides itself on developing strong relationships with customers. We meet customers’ needs by listening and understanding their unique problems. While Jerad and Masaba could have chosen any major dust and fume collection company, they found that the personal service from Imperial Systems helps us stand out.
Confused over all the shop exhaust systems available? Contact us at Imperial for a tailored solution if you need an indoor exhaust system, whether it’s an ambient or source capture exhaust system – or both!
Read more
by Erin Long | Jul 23, 2019 | Case Studies
The electrostatic powder coating method of dry finishing metal parts is a fantastic technology and process. There are so many advantages over liquid coating for manufacturers, but it does present a challenge for dust collection. Bobby owns a small shop in rural Alabama that has an electrostatic powder coating line. He faced this inherent challenge but found the solution.
Problem: Dust Build-up from Electrostatic Powder Coating
Bobby had installed a dust collector on his paint booth. However, the company would regularly experience small flash ignitions inside the collector. Above all, his concern was that one of these flash ignitions might harm one of his employees.
Electrostatic powder coating technology creates a charge on the powder material, which was making it stick to the filters. Therefore, Bobby wanted to find grounded filters to prevent static build-up. However, his current filter supplier couldn’t provide him with a grounded filter that would work in his collector.
Solution:
An Imperial Systems sales representative helped Bobby find a match for his current filters. Unlike his previous filter company, we were also able to provide him with the grounded filters he needed. The recommended solution was a DeltaMAXX aluminum spunbond filter with a connected ground wire.
Standard filter media cannot solve all dust collection problems. Sometimes customers and dust collection professionals need to work together to find an unusual solution. As a result, the filter chosen for Bobby’s electrostatic powder coating application was not a standard one but solved his problem.
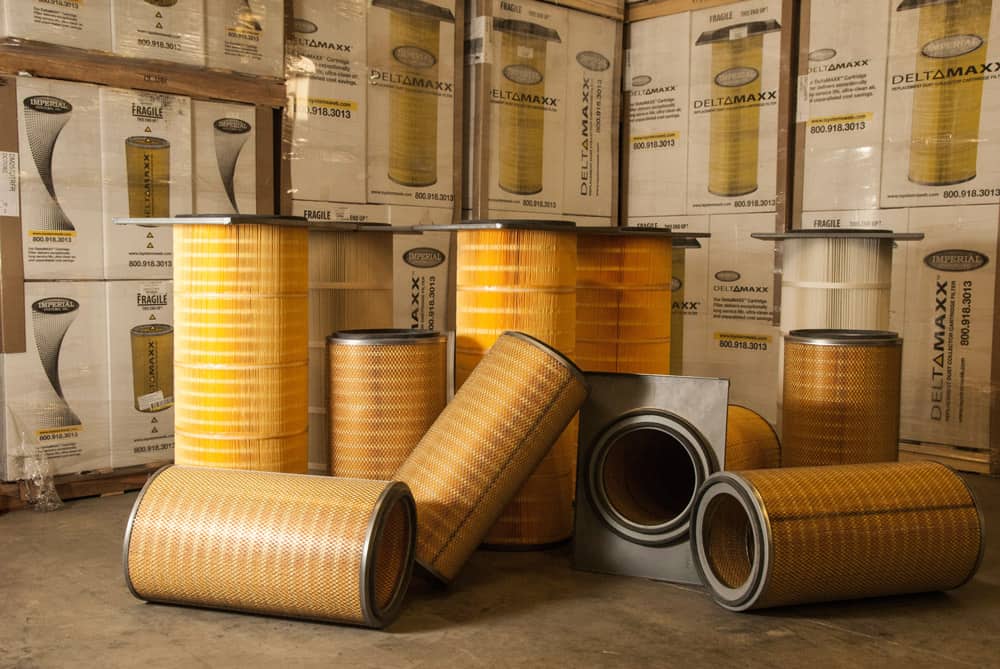
Feedback:
Bobby reports that he had a very positive experience working with Imperial Systems. “They helped me find what I needed. I’ll definitely come back for filters again when I need them,” he said. The company finally stopped experiencing flash ignitions with the new filters installed.
“We’ve had no more problems with static, and the filters are doing exactly what they’re supposed to do,” Bobby said. With properly grounded filters, the company no longer deals with static build-up or the risk of injury to workers.
Imperial Dust Collection for Electrostatic Powder Coating
Even if your problem is unusual or requires a special solution, Imperial Systems will work with you to solve it. No matter how many filters you’re buying, we will do our best to solve your problem. Because we have a huge library of filters, we can match almost any filter with a DeltaMAXX replacement. Contact us to learn more about this case study, DeltaMAXX filters, or how we can help solve your own dust collection problem.
Read more