by Erin Long | Jul 19, 2019 | Uncategorized
Take a look at Dusty Jobs 9! We talk about the GEAPS show in New Orleans earlier this year as well as discussing safety in grain processing facilities. Charlie is back for an extended version of ‘Good Luck With That’, and we interview our plant manager, Joe Hoffman. If you would like a printed hard copy of this issue of Dusty Jobs, contact your Imperial Systems, Inc. representative.
Click the cover to download and print the newsletter.
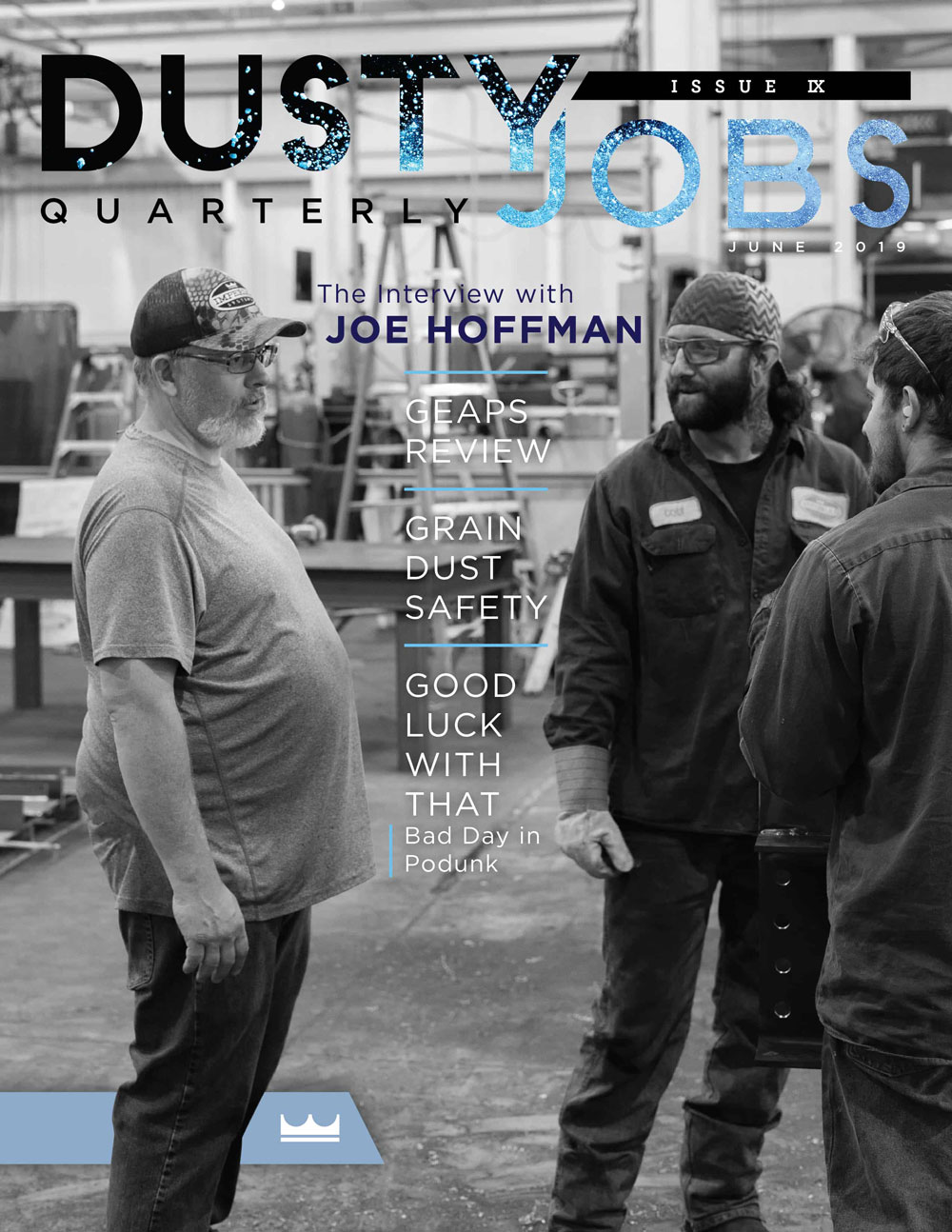
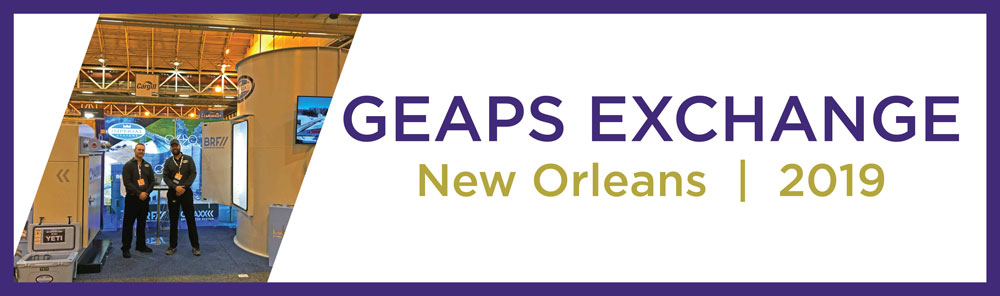
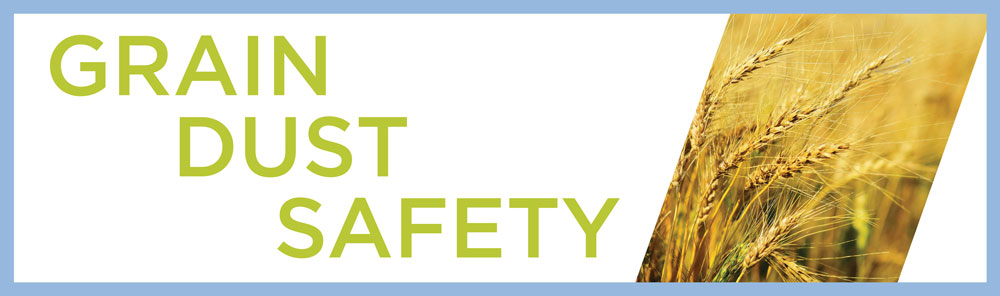
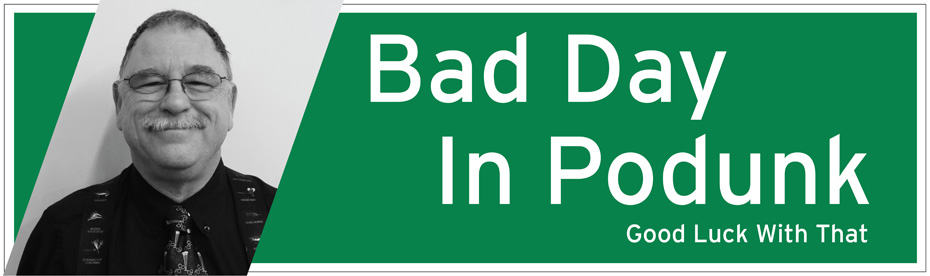
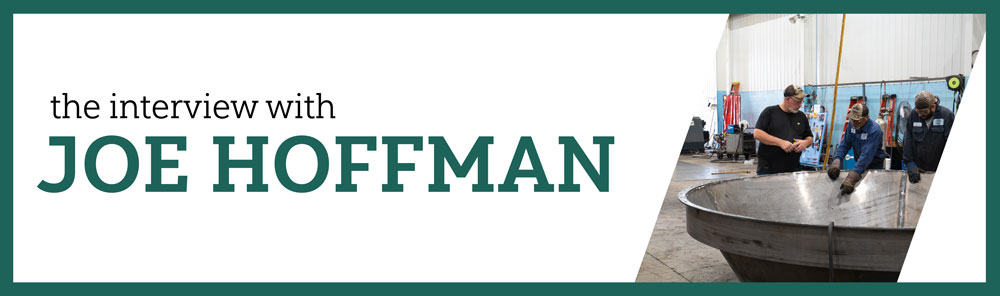
A Letter from the Production Control Manager
I started working at Imperial Systems in February 2015 as an Accounting Clerk. As the company grew over the next few years, I started taking on more responsibilities. I started helping with coordinating production, keeping information flowing between accounting and the shop. I worked with them to set schedules for shipping, hours planned for each job, and exactly where the job was with current hours.
As of last year, I moved into a new role as Production Control Manager. This takes the production control responsibilities I already had and kicks them up a notch. I’m still transitioning into this role, since I’ve been helping with accounting while someone was out on leave. Now, I’m looking forward to diving in and getting a good grasp on all the new responsibilities in front of me.
With the company growing, I’m going to be responsible for handling our shop schedule and keeping production on track. I’ll help solve problems and coordinate any changes that need to be made. I’ll keep track of the shop’s capacity and monitor when we’re over or under capacity. There’s a lot to manage with so many projects being scheduled, in production, and shipping out.
As a young girl, I would go to take-your-daughter-to-work events with my dad, and I always finished the day with the feeling that his company and co-workers were like part of his family. The company made sure to take care of their employees and truly cared about the employees’ success.
Since then, I have always wanted to find that in an employer and until Imperial Systems, I had not found my home in the business world. Shortly after starting, though, and with each additional day I work here, I realize just how much Jeremiah cares about this company as well as everyone who works here. Each day I am excited to wake up and come to work to help this team reach its goals. I love that I am challenged each day to come up with something that will better myself, which will directly lead to our company’s success.
I am just so thankful every day to be able to say I found my “work” home and gained 50-some “family” members, and I do not know if I would have been able to find this working anywhere else.
– Kaylee Smead, Production Control Manager
Read more
by Erin Long | Jul 19, 2019 | Hidden from Archive
Joe has been with Imperial Systems for twelve years. In his spare time he enjoys fishing and hunting. He also enjoys spending time with his wife, four children, and three dogs.
Q: How long have you been here?
Twelve years. I started off welding duct in the old building in Jackson Center, working second shift. I built the first CMAXX, and after that they paired me up with Higby and we built them together after that.
Q: When did you move up to management?
That was about four or five years ago. I was already a manager, overseeing all the guys, and then when the plant manager left I just kind of took over all of that too. I’ve been a supervisor for a while. I like it. It’s a challenge, keeping all the guys in line, making sure everything is done right. You can’t check everything… you could look at the same piece ten times and still not see everything. But usually things move really smoothly.
Q: You like what you do now?
Yeah, I like it. There’s a lot to do, keeping track of all the shipping dates and where everything is in production, keeping an eye on everything, teaching the new guys when they come in.
Q: What’s it been like since we moved over to the new building?
A lot busier. It went smoother than you’d think, though. Not many hiccups, considering all the changes. The powder coating was new and we had some glitches with that, but we learned a lot about it, and now it usually goes smoothly too.
Q: How many kids do you have?
Four, two boys and two girls. The youngest one is sixteen. The other ones are out of school now, and the one works here now.
Q: What’s it been like having your son working here?
He’s been here about two years. He’s still learning. He graduated from high school and was looking for a job, and this is a good place to work. He works just like everybody else.
Q: What do you do when you’re not here?
If I’ve got free time I do some fishing, either the Allegheny or at Pymatuning. I take the boys with me, but the girls don’t want to go. I’ll go camping sometimes. My family has a cabin, and my wife’s family has a cabin that’s just a few minutes from the river.
Q: Any sports you follow?
I watch the Steelers, but I wouldn’t say I’m a die‑hard fan. I’ll just watch football, whoever is playing. I’m not a serious sports fan. My son played football in school.
Q: Other hobbies?
I go hunting. I got a couple of doe this past season. Got most of the meat ground up. I used to do all the cutting up myself, but it takes forever, so I just take them to get done now. I’ve got three dogs. One of them is a beagle, but he never turned out to be a hunting dog. Just didn’t want to hunt. We ended up bringing him in the house. He got housebroken really easy, just followed the other dogs.
Q: So after twelve years, what can you say about working here?
It’s a good place. It’s definitely the best place I’ve ever worked. I’ve learned a lot working here. I’ve gotten to build pretty much everything we make here. I get to teach all the new guys, and I like doing that.
Q: It’s a good work environment?
It’s a really good bunch of guys. We all get along. We joke around a lot. It’s a good group to work with.
Q: Everything usually flows pretty smoothly?
Usually, it goes well. Sometimes dates change because the customer keeps changing details on the project, and engineering has to do a new drawing for approval… everything has to go from sales to engineering to production, so sometimes it takes time to get to us. Even when we get really busy, we keep things moving.
Q: Any good stories you want to tell?
Absolutely, but not any of them that I can tell you!
Read more
by Erin Long | Jul 19, 2019 | Hidden from Archive
The following story is true. The town names have been changed to protect the innocent.
Did you ever have one of those days when things went all wrong? Let me share with you the worst sales call of my career. The day began well. It was a beautiful mid-spring morning. The early flowers were in full bloom and the birds were harmonizing their mating songs. The air smelled sweet and the sunrise was glorious. The morning ride to the office wasn’t hot enough to have the A/C on, but warm enough to have the windows down and enjoy the fresh morning air. It was just one of those mornings that made you happy to be alive. That was before it all went sideways.
I arrived at the office around 7:30 AM, happy as a lark. It was a big day. I was making a sale call to one of my largest clients and fully expected to close on the deal. Since this customer’s location was roughly 100 miles north, I decided to take a design tech with me to field measure and gather any necessary information. I wanted to hit the ground running and avoid a second costly field measure trip. The appointment was set for 10 AM and if we got on the road by 8:30 there was plenty of time to make the appointment. That is when things began to sour. I had just gotten off the phone with the design tech telling him to meet me at the front door when my phone rang. It was one of our field mechanics needing some information for a job he was installing. I had to look up the information for him or it would be a costly delay for his install. Ten Minutes later I was ready to go when the phone rang again. My boss this time needing me to do something for him before I left. By now Steve, the design tech, was standing in my office door taping his wrist watch. Once my boss was satisfied, I grabbed my brief case to leave as the phone rang again. We ignored it and left.
We were behind. It was time to give the client a call to let him know we got a late start and were running about 30 minutes behind. They are understanding and told me there is no rush, we could meet when I arrived. Steve and I were now heading north on the Interstate on this beautiful sunny day. The windows were down, the radio was blaring, and Steve and I were adding our musical talent to Wild Cherry singing “Play-That-Funky-Music-White-Boy”, when my Chevy Tahoe gave a lurch and a sputter. My heart sunk into my stomach as I suddenly remembered I was going to fill the gas tank on the way into the office that morning. When my Tahoe’s gas gauge was just a sliver above the red empty line, the tank was bone dry. I dared to glance at the fuel gauge and shouted, “OH SUGAR”. Only it wasn’t sugar I shouted. The needle was sitting on the redline. We were still moving but the engine sputtered a second time. I did some quick thinking and remembered the last exit was about 15 miles back. Then I saw hope. We were passing a big green interstate sign saying, “Podunk, 1/2 mile”. The engine sputtered a third time and I took my foot off the gas to coast as much as possible. We reached the exit ramp. I did not brake at the stop sign but continued to roll on through as far as possible toward Podunk. The engine sputtered one last time and finally died about 500 yards beyond the exit ramp. I rolled over onto the shoulder of the most desolate two-lane highway you ever saw. We had come to a stop next to a grassy knoll and a farmer’s corn field with young plants about six inches high for as far as the eye could see.
There was a mileage sign that said, “Podunk 3 miles”. It was time to call the client again and tell them it would be even later. I didn’t want to say I ran out of gas, so I just said we were having some car issues. The next call was to AAA. That was when my cell phone died. Now we were in trouble. We had been there for 15 minutes and not a single car had passed by. I was an avid bicyclist back then, and my trusty Trek road bike was always in the back of my Tahoe. I told Steve not to worry, I would ride my bike into Podunk to get some gas. The six miles round trip should not take more than a half hour and I would be back with some gas. Normally I would ride in my bike shorts, cool wicking riding jersey and clip in bike shoes. For this ride I had to settle for dress slacks, button down shirt, neck tie, and hard dress shoes. I was uncomfortable and sweating within a half mile. When I made it into Podunk, I found it was at a cross road with US‑22. There was a small post office, three or four paint peeling houses, and an Amoco gas station with attached diner. A sign in the grimy windows read, “Eat Here and Get Gas!” All the windows were dirty with age and it was obvious this place had been closed for at least 30 years. A mangy, one-eyed dog stared at me from a front yard that had not been mowed in recent history and gave me a low warning growl. Then I noticed a sign on US-22 that said, “Salvation, 5 miles”. I’ve been through salvation several times and I knew it to be a larger community that supported a super Walmart and several gas stations. It seemed my adventure just got five miles longer as I pointed my bike up Route 22. About a half mile from the Salvation city limits there was a road crew doing repair work. I was forced onto the shoulder of the road where my high-pressure road bike tire immediately got a flat…”SUGAR!” I had to push my bike into Salvation. Not only did I have to get gas but also repair my flat tire, and I had stupidly left my spare innertube and bike tools in the Tahoe. It was also about this time I realized I was limping. My hard-soled dress shoes where not meant to wear while riding a bicycle, and I developed a blister on my toe.
The first concern was to fix the flat tire. I soon learned that Salvation did not have a decent bike shop where I could purchase an innertube for my bike, and Walmart just doesn’t sell items for better quality road bikes. I also discovered that Walmart didn’t have a single gas can I could purchase. Two hardware stores later and I gave up on any hope of fixing the flat tire, and even finding a gas can to buy. On the third stop I asked the store clerk what was going on with the gas cans? He told me the federal government had passed new legislation on gas can safety that went into effect that very day. They had plenty of the gas cans, but they were pulled from the shelves and could not be sold because they did not meet the new safety requirement. I was in despair. What was I going to do? I told Steve I would be back in a half hour and I’d been gone at least two hours now. I could not go on pushing the bike and I asked if I could leave it at the last hardware store until I could get back for it. They were kind enough to put it into safe keeping for me.
I started trudging back, wondering what I was going to do, when I noticed an Auto Zone store. I gave it a shot and found that they did have the new federally approved safe gas cans in one, two, and five-gallon sizes. My Tahoe would suck one gallon of gas just trying to crank over and I knew I would never be able to carry five gallons of gas for eight miles. I bought the two gallon can and filled it up at the station next door. I began my walk limping up US 22 to Podunk lugging two gallons of gas with my thumb out. I was thirsty, hot, tired, hurting, and probably looked like a wild man in a neck tie with my dress shirt half untucked from my slacks. I could not blame the first 500 cars that passed me by. I gave up all hope of catching a ride. I also realized it was at least three hours since I last called my client. They probably thought I just stood them up and awarded the order to my competitor. I lamented over the lost sale as I continue to limp along. SUGAR! SUGAR! SUGAR! I also worried about Steve who has now been waiting on the side of the road for over four hours. I would be the butt of many jokes once Steve returned to the office to gossip this tale about.
Then my luck changed. A rusty old pick-up pulled alongside, and a weather face of an old woman looked out and asked If I needed help? Along with all those “SUGARS” I was also saying a few prayers and the Lord heard me. It was an old farmer and his wife returning from grocery shopping. They told me to put the gas can in the truck bed and climb in. The truck was a standard cab with a single bench seat. The farmer’s wife scooted to the middle and make room for me. They had purchased a large tub of fresh strawberries and were munching on them as the farmer’s wife removing the stems. They offered me several and nothing tasted better to my parched mouth that those juicy berries. I relayed my tale of woe to them and told them where my Tahoe sat. The farmer said, “ That must be your car we saw next to our farm when we pulled out of our driveway this morning. You should have just come down our road. I always keep a hundred-gallon tank full at the barn for the tractor”. When the farmer dropped me off at my Tahoe, I thanked him for his kindness. He then told me if I turned around and crossed over the intestate there was a gas station about a mile down the road…SUGAR!
I found Steve laying in the grassy field . He had fallen asleep waiting for me. He was upset with me and said a few SUGARS of his own, but as I looked at him, I started to snicker. He asked what was funny and I said , “Oh, nothing”, and let it drop. Steve had been asleep in that field a long time. He looked like the Batman villain, Two-Face. One half of his face was bright red and the other pale flesh.
I dreaded the next day when I called my client. I explained the details of the previous day leaving nothing out, and asked forgiveness for standing them up. There was dead silence on the other end of the phone, and I feared I lost one of my best customers. Then I hear a peal of laughter. My client said, “Charlie, that is the dandiest excuse I ever heard for missing a meeting. Come on up and see us today. We have an order waiting to place”. I don’t recommend anyone using this sales technique to get an order, but if you do, Good Luck With That!
Read more
by Erin Long | Jul 19, 2019 | Hidden from Archive
Grain dust is one of the biggest combustible dust hazards in the industry. OSHA doesn’t have a combustible dust rule for general industry, but they do have one for agriculture and food processing (1910.272) because of the high risk and number of accidents. The NFPA also has a special standard for this industry (Standard 61) to try to reduce the number of combustible grain dust explosion accidents.
Grain dust explosions increased in 2018 over previous years, with twelve explosions compared to seven the year before, according to Purdue University’s Department of Agricultural and Biological Engineering. However, injuries and fatalities decreased from five deaths and twelve injuries to one death and four injuries.
This statistic only considers reported grain dust explosion incidents, and explosions without injuries may not be reported. There are also many grain dust fires that are not reported but still cause significant property damage. Some companies with a reported explosion that caused injuries had a history of multiple smaller fires and explosions that weren’t reported.
In most of the reported incidents, the ignition source was unknown. This was usually because the area where the explosion occurred was too damaged to track down possible ignition sources. Known ignition sources included sparks from machinery and overheated bearings. The number of possible ignition sources is almost unlimited because grain dust is so easy to ignite.
OSHA has reported that since they started enforcing their standard in 1987, the number of explosions has decreased significantly. Prior to those regulations, grain dust fires and explosions were often considered to be an inevitable cost of handling and storing grain. With process hazard analysis now required, problems are more likely to be identified before there’s an accident.
Still, grain dust explosion accidents continue to happen. Often, the hazard has been identified but not addressed. An example would be allowing grain dust to accumulate around the facility. Often, the thought is that it’s never been a problem before. It may not be a problem until the dust is stirred up and the cloud finds an ignition source. The danger here is that the first cloud of stirred-up dust might be small and only cause a quick flash fire, but the force of this could disturb and ignite much larger amounts of dust. This is called a secondary explosion, and it is usually bigger and more destructive than the first one.
Major sources of accumulated grain dust are pieces of grain handling equipment, such as bucket elevators, conveyors, mixers, and grinders. Since grain is being moved around in these processes, a lot of dust often escapes unless there is a dust collection system there to capture and remove it.
Baghouses are popular for dust collection in the grain industry, but cartridge collectors can also be used. They are especially useful as spot collectors because they are small and can be located over a particular spot where dust is being produced. Baghouses are usually large because they need lots of bags to provide enough surface area for good filtration. A cartridge collector can be much smaller because the pleated cartridges have a much higher surface area than bags.
A dust hazard analysis will identify places such as grain elevators where dust is likely to be a problem. Before planning and installing dust collection or dust control measures, all the hazards should be identified. This includes any areas where a breakdown in normal processes could cause dust to build up or potential ignition sources that could develop, such as overheating machine parts. A dust hazard analysis is required by NFPA 652, the most recent combustible dust handling standard. NFPA 652 is not meant to replace NFPA 61 or other industry-specific standards, but anything in NFPA 652 that isn’t addressed in the industry standard still applies.
Deaths from grain dust explosions may have decreased, but they continue to occur. This happens even though the grain and agriculture industry has been one of the earliest officially regulated combustible dust hazards. Dust collection is an essential part of grain dust control and should be in use anywhere that dust can build up during the process.
Read more
by Erin Long | Jul 19, 2019 | Hidden from Archive
GEAPS (Grain Elevator and Processing Society) 2019 in New Orleans featured some of the largest Grain and Seed processing equipment companies. This year at GEAPS was the first year that we decided to bring some rather large equipment. We really wanted to show up and show off some of our new technology. Our booth featured our new BRF Medium Pressure baghouse. We built a 7 foot clean air plenum to demo the new cleaning system. We also had a CM002 Spot filter on display as well. Both of these items will be on display at our showroom.
The show had a little bit of everything to offer, from dump pits to rail cars to storage bins and engineering firms. Each company could have the need for dust collection in their facility as well as the grain companies that attended.
The show went well, and although not as big as Fabtech the show still pulled in the big names in the world of grain, seed, and food. During the show we would demonstrate the pulse cleaning system of our BRF-MP. If you have never heard this cleaning system in action, you have to imagine something similar to an air canon or spud gun being fired. This powerful blast is designed to clean off the dust that would build up on the bags. Eventually we had to shut that down due to the sudden blast scaring everyone that wasn’t paying attention. Fortunately, we could still show the moving arm and explain the auto calibrating pulsing system. We also had our CMAXX Spot Filter showing the different applications that would benefit any source capture grain process. Giving customers the opportunity to get hands on with our equipment is really when they see the difference. Our equipment visually has clean lines and looks great, while being able to see how heavy duty it is makes a difference. Not to mention the simplicity of the CMAXX filter changeout. You can really see people’s faces light up when they realize how much thought and care we put into our products.
New Orleans weather was a nice reprieve from the cold rain of western Pennsylvania. The city was colorful and we got to experience a little bit of the culture. We went to the French Quarter and got beignets and coffee and watched the street performers. We also had some of the local creole cuisine which was excellent. You can still see the aftermath of hurricane Katrina but it is obvious the city is rebuilding and moving forward.
All and all, GEAPS in New Orleans went well. We got to talk to great people from the grain industry as well as getting to see all of the equipment that services this industry. We got some great leads and gave the grain community a chance to see our equipment first hand.
Read more