by Greg | Apr 11, 2018 | Hidden from Archive
Q: You’ve been here at Imperial Systems pretty much since the beginning, right?
A: I started when we were still over in Grove City. Me, Russ, and Steve are the three still left from that original crew. I’ve been here twelve years. I started off doing welding and then did fabrication, and did a little bit of everything. In the past year I’ve been doing a lot of field work and traveling.
Q: How has the company grown since you started?
A: It’s grown like crazy. When I was in Grove City and we were moving to the Jackson Center place, I’d work ten-hour days all week and then go with Russ to Jackson Center and work on the new place. And it didn’t take long before we started to outgrow that.
Q: What do you think about the new building?
A: It was totally necessary for us to be able to grow. We’re already just about full. Since we moved in back in January things are starting to get settled in and they’re running a lot smoother.
Q: How much more do you see us growing?
A: The way things are growing I could see us outgrowing this building someday. We keep getting more and more orders for equipment.
Q: What are your favorite things to do here, since you do some of everything?
A: I like running the plasma table, and I like doing fitting and welding. I run the forklift, and now I do a lot of field work so I’m off traveling around a lot. You get to see some interesting things out there.
Q: What would you tell people about working here?
A: We have a lot of fun working here. Maybe a little too much sometimes. It’s a really good bunch of guys.
Q: And you’re still happy working here after twelve years?
A: Absolutely. It hasn’t been perfectly smooth sailing for the entire twelve years and we’ve had our ups and downs, but it’s a great place to work.
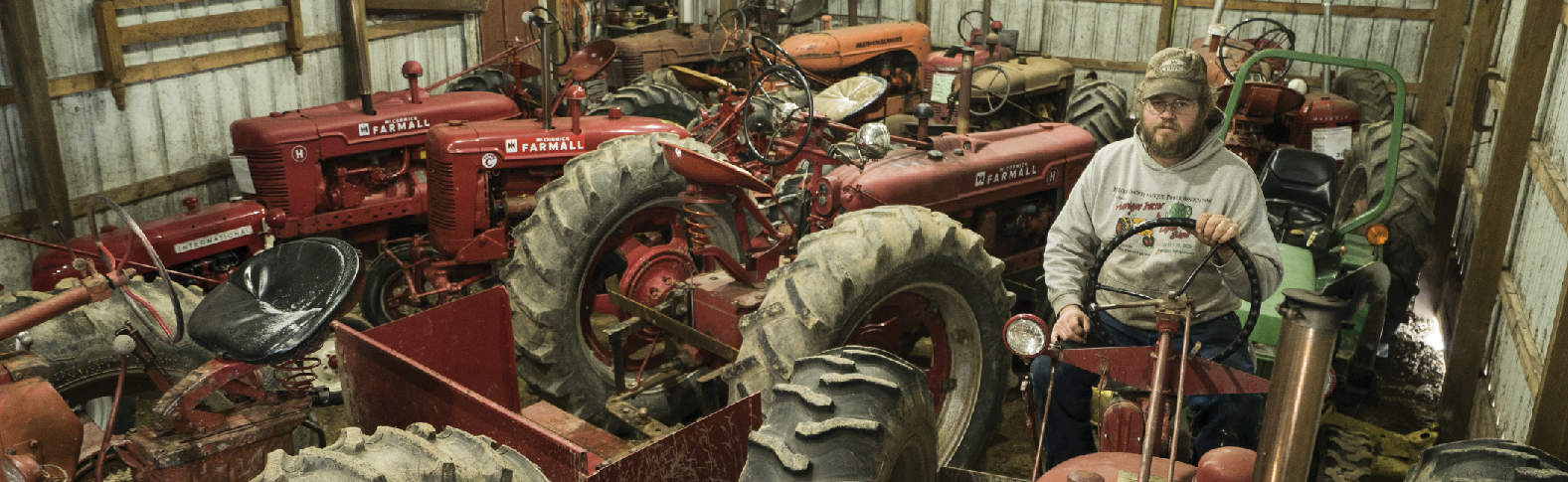
Q: And when you’re not here, you’re at your farm.
A: That’s right. My dad’s the third generation and I’m the fourth generation on that farm. I’ve worked there since I was a kid. We didn’t have sitters… we just went to the farm. If I’m not at work, that’s where I am.
Q: And you’ve got a lot going on there right now with all the baby goats, right?
A: We had triplets the other day. We’re bottle feeding one of them. We had eleven babies out of the five goats I bought on my last trip.
Q: What are you going to do with all these goats?
A: They’re meat goats, Boer goats. They originated in Africa. They can get up to 200 pounds. There’s a big demand for goat meat in some places.
Q: How many goats do you plan on having?
A: My dad and I are still talking about that one. A lot, I know that. My oldest kid, my nine-year-old, is starting 4H this year. He’s got two goats. The younger ones will start here pretty soon.
Q: So you’ve got ducks, chickens, horses, cows, goats, pigs…
A: And my dog, Molly. She’s a chocolate lab. She’s my farm dog. She minds me and no one else, and I love it.
Q: And you’ve got your tractors.
A: I’m into the Mercer County Antique Power Association, antique farm equipment, antique tractor pulls. I have a tattoo of my first tractor. Took a picture of it and took it in to them.
Q: So you’re passing on the farming tradition to the fifth generation?
A: Of course I am!
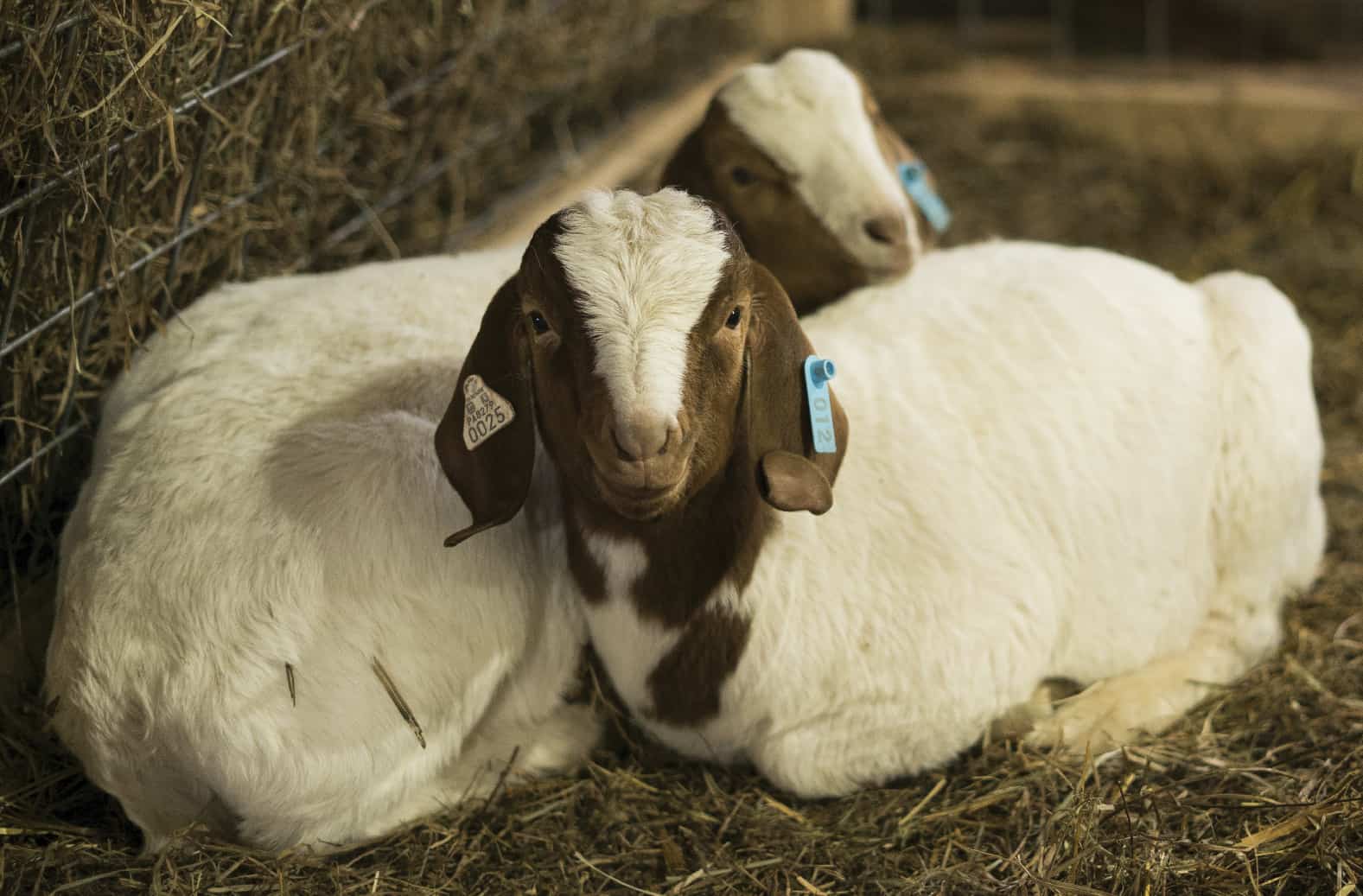
Read more
by Greg | Feb 8, 2018 | Uncategorized
The switch to powder coating is one of the most exciting changes about our move to our new building. The booth is big enough to accommodate our largest pieces of equipment. This equips us to powder coat everything that we produce.
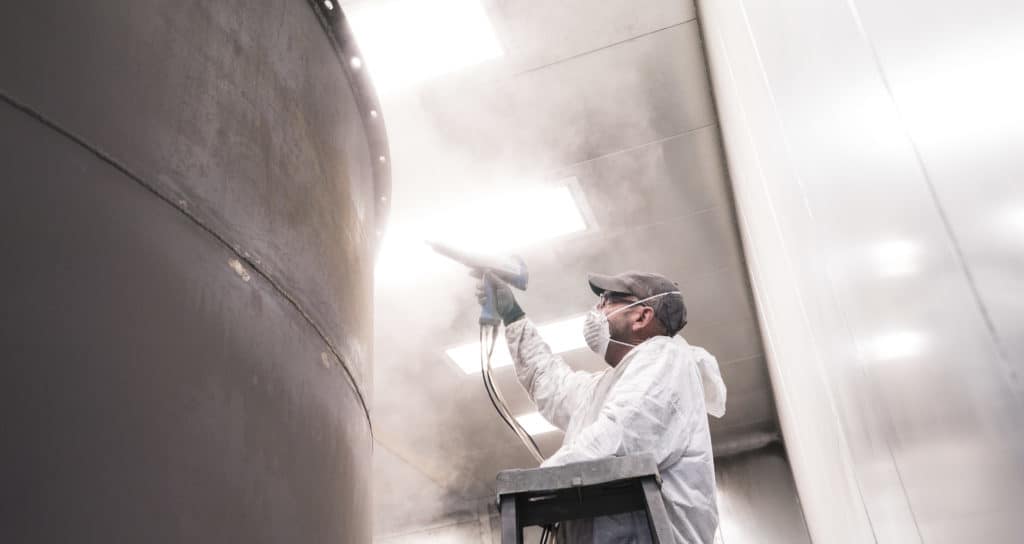
Why the switch to powder coating? There are so many reasons!
Going Green
This paint application technology is much healthier for people and the environment. Liquid paint contains solvents and volatile organic compounds (VOCs). Therefore, it creates many dangerous emissions that can damage the environment and harm people’s health. The powder coat process creates almost no pollution, so it’s a much greener process than solvent-based liquid paints. The EPA considers powder coating a much better option for environmental health.
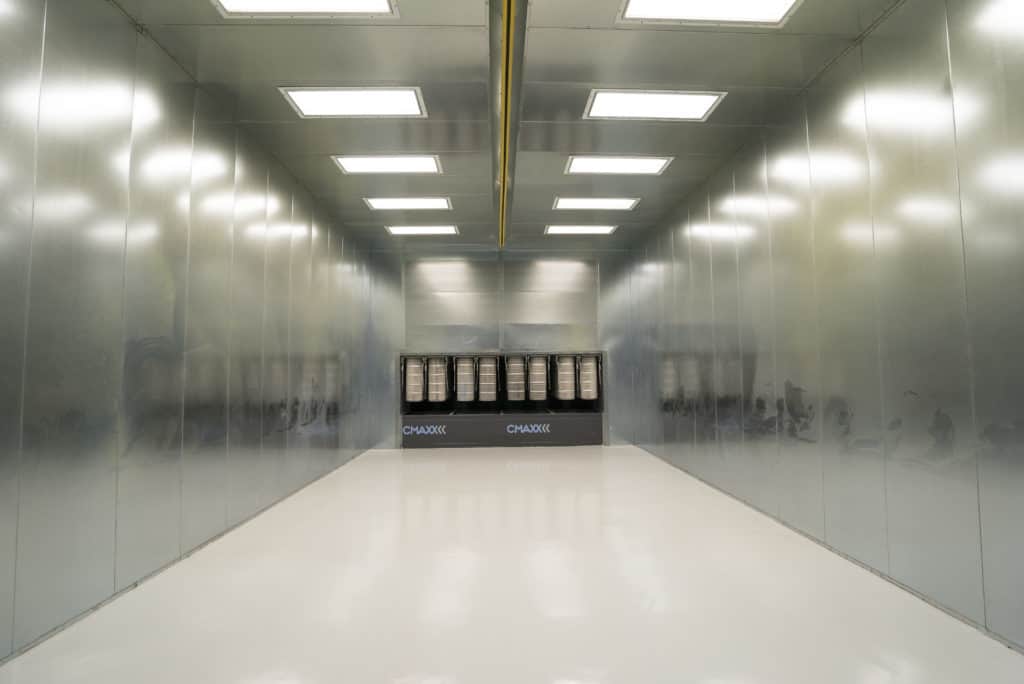
Efficiency
It is extremely efficient. The metal attracts the powder which adheres to it. Collect and reuse any powder that doesn’t stick. Because there are no produced VOCs, a powder coating booth does not require expensive, complicated air cleaning systems. The technique is faster and easier than many other processes. Also, temperature and humidity don’t affect the process as much. This means it’s easier for us to ship finished products regardless of the weather.
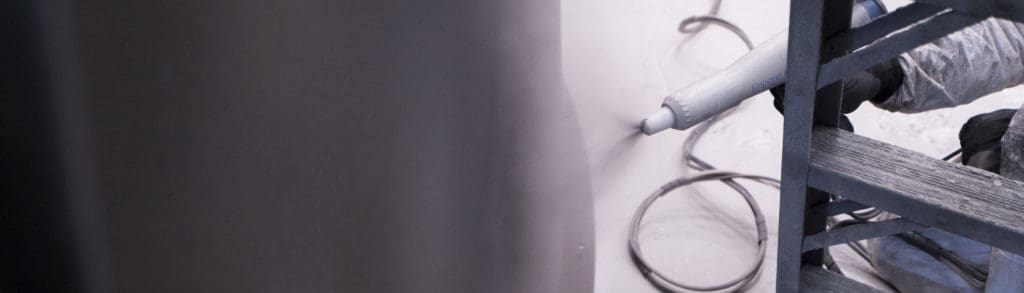
Durability
This process produces a durable, tough surface that’s resistant to scratches, chips, and rust. It is used on everything from household items to metal equipment that needs to last many years outdoors in all conditions. It will give our equipment a finish that makes it even more weather-resistant than before, and protect it from rust, scratches, and other damage. We are currently the only company in the USA powder coating a round baghouse, so if you want a collector that’s going to stand up to almost anything, ours is the one to go with.
Appearance
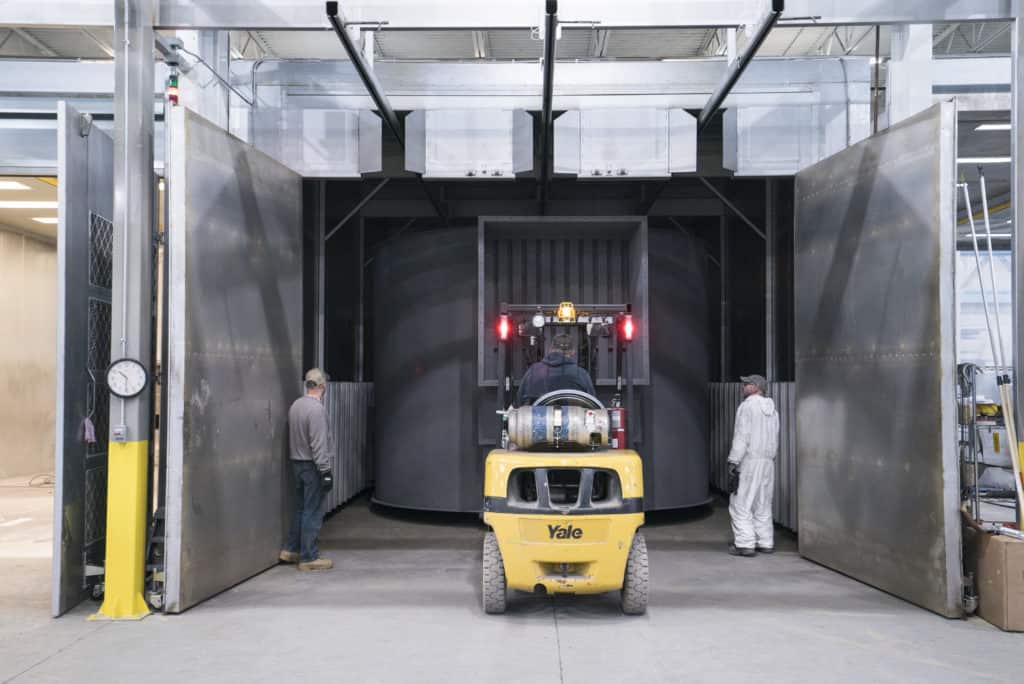
If you’re looking for an attractive finish, powder coating is definitely one of the best options. Because it coats evenly and doesn’t streak, run, or smear, it produces a smooth and good-looking finish. Items that are powder coated will look better and have a cleaner-looking surface than items painted with liquid paint. We want the appearance of our products to be as good as the performance, so getting a great finish is the perfect finishing touch.
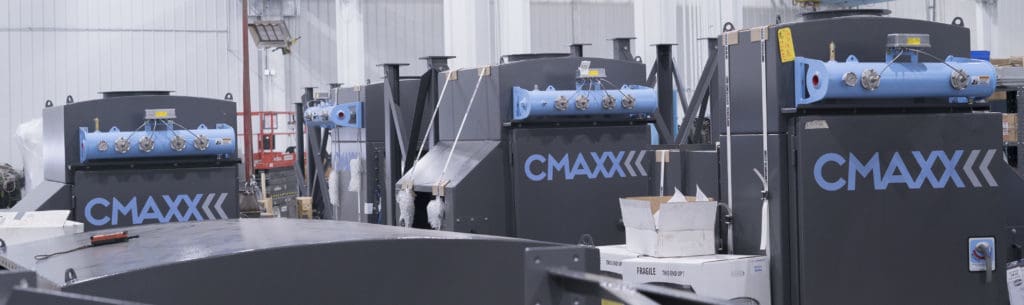
Freshly powder-coated CMAXX Dust and Fume Collectors are ready to be shipped out.
Read more
by Greg | Aug 15, 2016 | Case Studies
Product: Dust Collection System Filters
Application: Capture dust and fumes from powder coating process
Customer: Small powder coating shop in rural Alabama
The Challenge: Bobby, the owner of the company had concerns about static charges building up inside their dust collector. Powder coating is an electrostatic process and his equipment was causing small “flash” ignitions within the collector. This was an obvious safety issue and he knew he needed help in finding a cartridge filter that could be grounded. His current filter supplier was not able to solve the problem.
The Solution: He discovered Imperial Systems and discussed the issue with one of our Aftermarket team members. Once they understood Bobby’s concerns, they were able to determine the correct filter medium and other modifications to address the problem. A DeltaMAXXTM aluminum spunbond cartridge filter with a connected ground wire was the solution for this type of problem. Once the new filters were installed and grounded properly, the static discharge was alleviated. Bobby was very pleased with the results. “We’ve had no more problems with static and the filters are doing exactly what they’re supposed to do”.
He was very appreciative of our help and will definitely contact Imperial Systems for any future filter needs.
Read more
by Greg | Mar 27, 2016 | Case Studies
Case Study – Weld Smoke Extraction Problems at This Metal Fabrication Facility Solved with the CMAXXTM Dust and Fume Collector
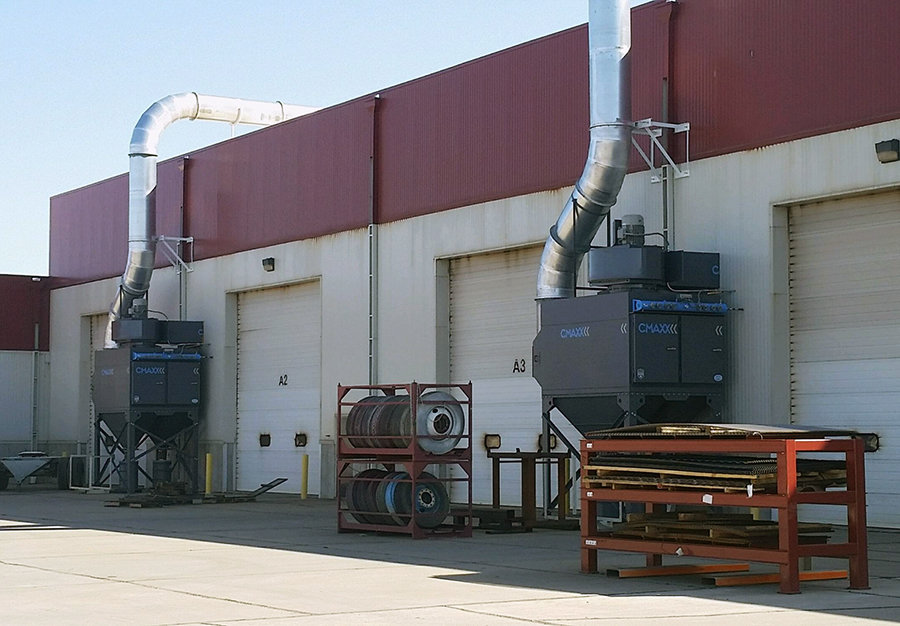
Product: CMAXXTM (CM020) Dust Collector (Total of 3 units)
Application: Capture weld smoke and fumes
Customer: Masaba, Metal Working Fabricator of Bulk Handling Equipment for Mining, Aggregate, Agriculture, etc.
The Challenge: Masaba’s manufacturing facility has a high ceiling that would become filled with smoke and fumes from their various welding bays. The old roof mounted system that was used to extract the weld smoke and fumes from the facility was not working properly. This system was a hybrid HVAC unit that incorporated industrial air filters. The weld smoke being produced during daily production proved to be too much for the current air extraction unit. The return air into the facility was not being filtered adequately, which defeated the purpose of the system altogether.
The Solution: The President of Masaba, Jerad Higman, was not satisfied with the current situation. As a business owner, he cared very much about his employee’s health and having a clean working environment. Though the air quality was good enough in the shop, Jerad wanted to make it even better and decided a new, more effective system design was needed. He called upon top industry dust collection manufacturers, Camfil Farr, Donaldson Torit, and Imperial Systems, Inc. to provide the best solution to his facilities’ air quality problems. He knew each company was capable of solving the problem, but after meeting with Imperial System’s President, Jeremiah Wann, and hearing his ideas about mitigating all the weld smoke issues, Jerad knew he had found the right company.
A relationship of trust quickly developed between Jerad and Jeremiah as they worked together on the design and layout for the new system. “I had a great experience in working with Jeremiah and Imperial Systems”, Jerad says. “I really liked the fact that they are an American owned company and were always available when we needed them.”
The installation of an ambient weld smoke system was the ultimate choice to clear Masaba’s facility of dirty air. Imperial Systems installed three exterior CMAXXTM (CM020) collector units and associated ductwork as part of the new system. Masaba manufactured the hoods that covered each welding bay. Once everything was connected, it didn’t take long after the system start-up to see the built up weld smoke dissipate. The new CMAXXTM system was moving and recycling the total air volume inside the shop six times per hour. The return air was being filtered properly by the DeltaMAXXTM filters, resulting in cleaner air and healthier environment.
Jerad Higman was amazed at the difference. “I was very impressed at how effective the CMAXX collectors were operating.” He goes on to say, “To this day, I have not experienced any problems with them and I would highly recommend Imperial Systems products to anyone that has issues with the air quality in their shop. Their level of expertise and service is just outstanding.”
For more information on how CMAXXTM Dust and Fume Collection systems can benefit your facility, call one of our experienced team members at 800-918-3013 or visit Imperial System’s website today.
Read more
by Greg | Feb 8, 2016 | Case Studies
Product: BRF Baghouse (8BRF 152-10 with after filter plenum)
Application: Capture dust and fumes from pulverizing PVC regrind
Customer: PVC recycling for door and window frame industry
The Challenge: Due to rigid air quality control guidelines set by the state of Nevada, our customer’s facility expansion plans, which included pulverizing PVC regrind that they produce, needed a solution to control dust and fumes created from that process.
The Solution: The customer never had to deal with such stringent air quality control guidelines before, and they needed a guarantee that a dust collection vendor could meet and exceed the Nevada requirements. After meeting with several companies, all of whom could not guarantee results, they contacted Imperial Systems. Upon traveling to their facility in Ohio, Imperial not only guaranteed results but proved it as well. How did they do this?
Jeremiah Wann, President and CEO of Imperial Systems, built a smaller version of the after filter plenum and asked to tie it into the discharge from two of their Pulverizers. “Our main concern was a blue smoke/mist that is created during this process,” says Kurt K., Director of West Coast Operations. Once the filter plenum was connected, Kurt was convinced. “There was no smoke or mist visible, and the odor was gone.”
They purchased a BRF (8BRF 152-10) to handle the collection of the dust and fumes created by the pulverization process. Due to Nevada law, a licensed mechanical contractor had to be used for installation. Imperial Systems sent a technical supervisor to oversee installation, and everything went extremely well.
As far as operation results? “It has performed exactly as we were told it would,” says Kurt. “The system has been in operation for over a year now, and there is no hint of dust or fumes from the system’s discharge.”
Kurt recommends Imperial Systems to anyone that has dust and fume issues. “Our collector has done exactly what Imperial said it would do, and in business, that is the bottom line.”
He also had this to say about the level of service he received from the Imperial Systems team. “I have been very satisfied. Everyone I had dealings with has been helpful, knowledgeable and pleasant. Imperial worked everything out to my satisfaction, which made it a good experience overall.”
Read more