by Greg | Jun 4, 2015 | Case Studies
Product: CMAXX (CM-016) Application: Cement
Download this Case Study
Imperial System’s CMAXX Dust Collection System helps out a nearby Automotive and Construction Chemical Plant.
The subject of this case study is one of the largest manufacturers of industrial, automotive, and construction specialty chemicals. The company focuses its products into markets such as: concrete, waterproofing, roofing, flooring, and industrial manufacturing. They distributes their chemicals to businesses such as Home Depot as well as contractors, auto manufacturers, and other industrial companies.
Challenge:
After experiencing industrial hygiene and reliability issues with the prior dust collection system, this company sought to find an industrial dust collection manufacturer the company could build trust with.
The goal was to find a responsive company that packages both great customer service as well as having a dust collector with reliability traits and easy to maintain service. Imperial Systems CMAXX Industrial Dust Collector fit the bill.
Solution:
Beginning their search with local distributors, they reached out to a few companies that ultimately did not have neither the knowledge nor the dust collector the company wanted to put their long term trust into. After reaching out to a mutual distributor that both Imperial Systems and them have a relationship with, the group was were blown away by Imperial System’s CMAXX Industrial Dust Collector.
Ultimately what sold the job was not only the design and style of the CMAXX Industrial Dust Collector, but the responsiveness and personal interactions that they valued so much.
Results & Benefits:
According to the plant engineer, the CMAXX is running flawlessly and has improved efficiency and air quality around the shop.
When asked “What the benefits they experienced from working with us is?” the response was simply, “Improved operations and an ongoing partner. The CMAXX is easy to use, reliable, and has saved us energy costs while enhancing our clean-air recovery”.
Read more
by Greg | Mar 3, 2015 | Case Studies
Product: CMAXX (CM-010) Application: Plasma Cutting
Download the Case Study
Fed up with their Horizontal Cartridge Collector, the World’s Largest Manufacturer of Sawmill Equipment Makes the Switch to a Vertical Cartridge Collector.
A few fires, poor production, and strict OSHA guidelines will cause any company to rethink their current dust collection and safety solutions. Thankfully, Imperial System’s CMAXX Dust Collector was able to live up to being one of the most user-friendly and advanced technological Industrial Dust Collector in the business.
As the world’s largest manufacturer of recycling and sawmill equipment, and a distributor to major national cities, logging and sawmill industries, the demand for equipment is constantly in the fast lane. The company manufactures 95% of its equipment in-house and employs over 350 welders to work shifts 10 hours a day/ 5 days a week.
Originally, Morbark had purchased a dust collector that housed horizontal cartridge filters to clean-up their shop’s plasma cutting and weld dust, but the horizontal filters had been trapping burning embers on the filter media; resulting in multiple fires.
Multiple dust collector fires and changing OSHA guidelines were the driving force behind the company seeking out a new, more advanced, dust extraction system for their plasma cutting table.
“When the rules changed and you were not allowed to blow plasma dust outside, we couldn’t use a water table because they did not work for our application. 95% of parts are manufactured in shop – so getting rid of the waste and scrap is one of the biggest challenges we have – we needed to get a dust collector that could work with our plasma cutting table.”
When researching multiple dust and fume extraction companies, Dave, the maintenance manager, had three main goals in-mind he wanted the company’s new dust collector to accomplish:
1. Reduce the tedious filter-change out process
2. Find a dust collector that would lower the chance of another fire.
3. Find an efficient dust collection solution that would help save the company money and reduce downtime.
After hearing about Imperial System’s through the company’s laser cutting table manufacturer, Dave knew Imperial could get the job done. Dave went ahead and purchased a CMAXX, model number CM-010, to clean-up his plasma cutting dust.
1. Simplicity of Maintenance
Using the CMAXX’s filter removal tool, as well as the system’s Even-Lock Technology, the maintenance manager has had a much cleaner and faster experience with changing filters in his new dust collector compared to the previous solution.
“When changing filters on our old dust collector, there were 12 different holes I had to unbolt just to change one filter. So simplicity of maintenance was huge and the CMAXX has delivered.”
2. Drastically Decrease the Chance of a Fire with Vertical Cartridge Design
The CMAXX’s vertical cartridge design and Pulse Distribution Technology allows for the dust to pulse off 100% of the filter media from the vertical cartridge filters and easily fall into the hopper.
3. Less downtime means more money
Due to the CMAXX’s simplicity of maintenance and 100% pulse cleaning on each filter, the CMAXX is able to clean more efficiently while drastically reducing the downtime of filter change-outs.
Imperial System’s vertical style CMAXX Dust Collector was able to get the job done at the manufacturing shop. In fact, to ensure there would be no chance of a fire, the company also purchased a Spark Arrestor from Imperial System’s to extinguish the sparks before ever entering the dust collector.
Read more
by Greg | Aug 5, 2014 | Case Studies
Imperial Helps a Large Recycling Paper Mill become NFPA compliant while creating a safer work environment.
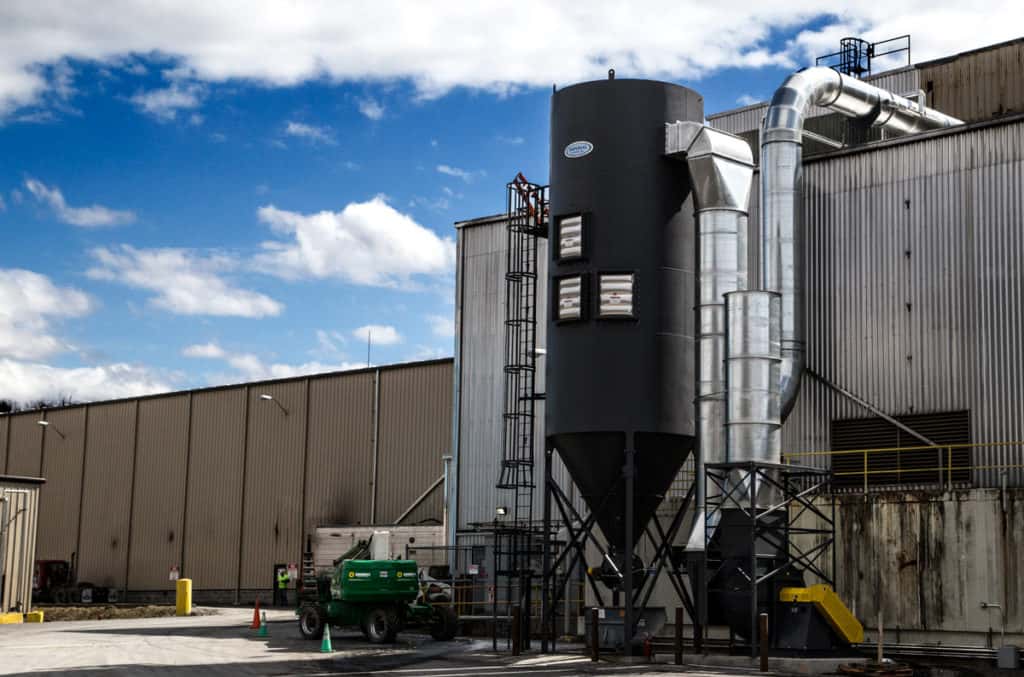
About the Company:
As a global leader in the forest products industry. The company owns and operates nearly 40 pulp and paper mills and wood product facilities in the United States, Canada, and South Korea.
The company makes and supplies leading publishers globally with top quality commercial printing paper and newsprint for magazines as well as direct mail, instruction manuals, maps, flyers, etc.
Not only does the company also produces 1.7 million metric tons of market pulp at seven different facilities in North America, they are also a major producer of lumber and other wood products for residential-construction and home-renovation markets.
This particular case takes place at one of the North American plants located in West Virginia.
Challenge:
The West Virginia located recycling paper mill is one of the largest in the USA. Production hours at the shop are virtually non-stop, running 24 hours a day and 365 days a year.
Though the wood dust is not toxic, the company was having trouble becoming NFPA compliant and the employees were dealing with plenty of extreme health, safety, and fire hazards including: airborne dust coming off the belt conveyers and constantly floating in the air, and up to 7 inches of dust collecting on the machines weekly – creating tremendous fire hazards.
The only safety measure to this point were employee dust masks.
“We were capturing 400-500 pounds of dust weekly, it was a huge problem,” says one plant manager.
The dust was getting bad enough that the employees were having respiratory infections as well as eye infections.
It was time to make a change.
Solution:
In January of 2014, while searching the internet for dust control solutions, the large recycling paper mill stumbled upon Imperial Systems, Inc. Because of Imperials’ great values as a family owned company, as well as being a true one source company, it was an easy decision for the recycling mill to go with Imperial.
“Imperial was a one-stop-shop and we really valued that when bidding out the job. Imperial took care of the entire process from the drawings, to the engineering, to the fabrication, and clear through installation. The communication between us and them was always thorough”, said plant manager G. Thomas.
The company purchased a Reverse-Air Baghouse Dust Collector and over half a million dollars in ductwork from Imperial Systems. The development and install process began at the end of January and the entire project was up and running by March of 2014.
According to plant manager G. Thomas, who supervised the entire project, the Imperial Systems’ installation team was not only extremely knowledgeable and efficient, but they were also extremely respectful, helpful, and easy to work with.
“The install crew was a pleasure to work with, the whole process was a pleasure actually. Imperial was very easy to work with, there was no lack of communication, and I know if I need something in the future, I can call-in and somebody from Imperial will be here as soon as possible.”
To this day, the West Virginia paper recycling mill has had no problems with their dust collector purchased form Imperial Systems. Since becoming NFPA compliant, the shop has been cleaned up tremendously. There is minimal to no wood dust in the shop creating a much healthier and fire resistant environment and operations are running at a much smoother pace.
About Imperial Systems:
Located just north of Pittsburgh, Pennsylvania in the small town of Jackson Center, Imperial Systems is among the top dust collection equipment manufacturing businesses in North America. Our values are built on designing and installing custom industrial dust collection systems with the strongest, most durable, fabrication to meet our customer’s needs.
Read more
by Greg | Apr 21, 2014 | Case Studies
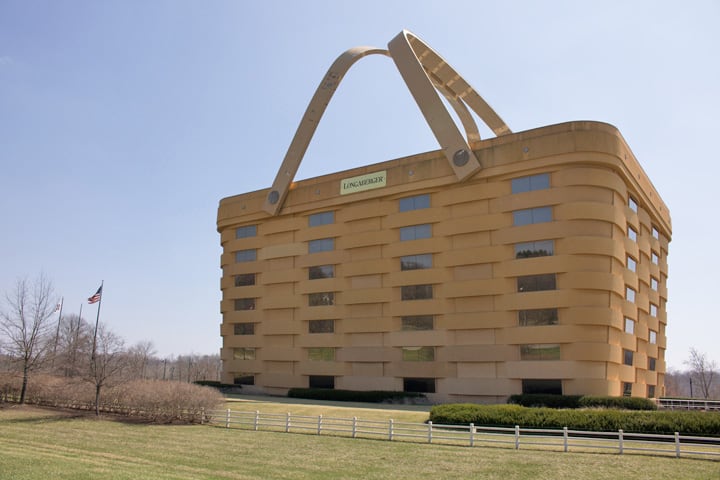
About the Company:
The Longaberger Company is a globally renowned manufacturer of handcrafted maple wood baskets and offers other home and lifestyle products, including pottery, wrought iron, fabric accessories, and specialty foods. Located in the heart of Ohio, it is a primary employer in the local area.
The company distributes their products to approximately 45,000 independent consultants located throughout the U.S.A.
The Longaberger corporate headquarters is a well-known landmark and a brilliant example of novelty architecture. Longaberger HQ is uniquely shaped as the basket product that the company is nationally recognized for.
Challenge:
Due to the decline in economy value, the Longaberger Company had just sold one of their bigger buildings to move across the industrial park into one of their smaller facilities.
The Duct and fitting on the building was roughly ten years old, so it was time for a modification project. The goal was to find a company with expert engineers that could help with cutting cost, efficiency, and manufacturing the desired ductwork.
After hearing about what Imperial Systems had to offer from the staff at an Air Systems plant in Indiana, the Longaberger Company decided to reach out to Jeremiah Wann (president/CEO) at Imperial Systems to discuss the upcoming duct and fitting installation.
The Longaberger Company decided to go with Imperial Systems because of cost and what the company had to offer as far as design, layout, and their expert knowledge as a complete systems manufacturer.
Solution:
The duct and fitting installation process began in January of 2014 and was separated into two phases. During the first phase, the Imperial Systems installation crew came and moved the existing cartridge collector and BRF to the new, down-sized, location. The second phase consisted of installing the duct and fittings.
“Imperial did a great job at looking at what our needs were and solving the issues that we had in the past. They helped us move from two big collectors down to one”, said Barry S., Longaberger plant mgr.
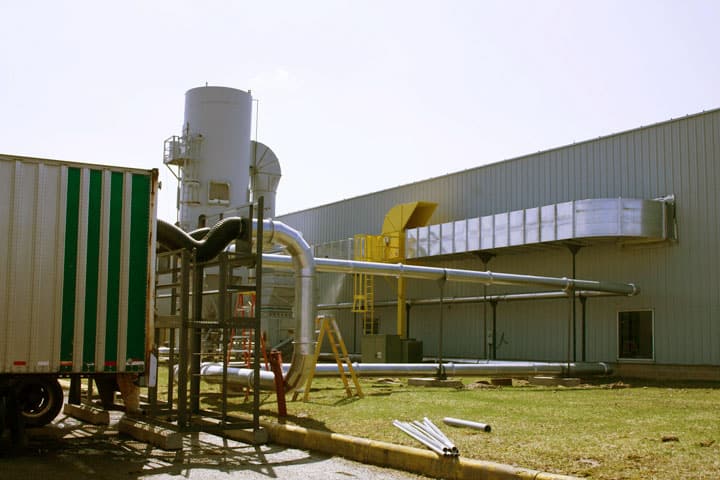
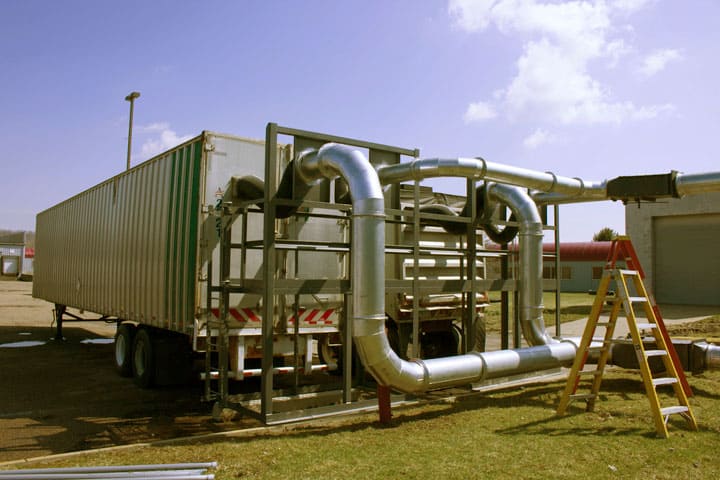
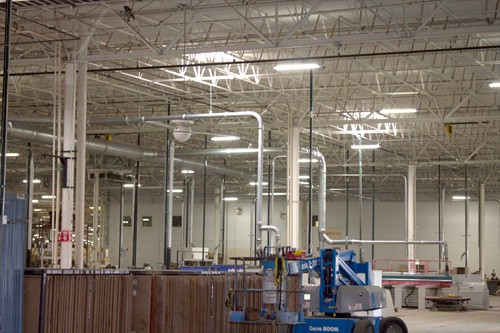
Read more
by Greg | Mar 31, 2014 | Case Studies
Located in northern Pennsylvania along the shores of Lake Erie, this company specializes in hard chrome and electroless nickel plating as well as polishing of molds, tools, and dies.
Challenge:
The company manufactures five days a week for 16 hours each day. Not only would the companies dust collectors pull in blasting materials, but they would also pull in an oily film that would foul the cartridge filters on a regular basis. As a result, the company would have to change their dust collector system’s filters at least three times a year. The goal for this company was to find a cartridge filter that would successfully defend against this material while also staying within the company’s budget.
Solution:
After doing a cold call to this company, the Imperial System’s aftermarket rep was able to land the company’s business.
“Imperial Systems reached out to me and recommended their Deltamaxx filters that have a nanofiber media and wow what a difference they made. Now we have filters in our dust collectors that last 4 times longer. Also, our cost in filters and down time are at their lowest”, said Scott G., a company representative.
Scott then went on to say, “I have been changing filters here in our plant for over 20 years and I wish I would have known about Deltamaxx filters years ago. I have a system here that I would change at least three times a year. Since we put the Deltamaxx filters in our dust collectors, I have not changed it yet and it’s been over a year. We run two shifts {8 hours} a day for 5 days a week. Thank you Imperial System for recommending the Deltamaxx nanofiber cartridge filters.”
Thank you Scott!
Read more