Greg Mar 17 2014 Case Studies
Located in the heart of central Pennsylvania, this fiberglass pultrusion manufacturing plant is one of the most established United States manufacturing companies. Founded in 1974, this fiberglass construction manufacturer is a global distributor specialized in replacing old steel, wood, and aluminum structures with lighter, sturdier, fiberglass reinforced plastic construction. Whether it is reinforcing the underwater structures of the fountains at the Bellagio Hotel and Casino, or protecting the many steel pipes inside the Hoover Dam; fiberglass pultrusion manufacturing has become a mainstay in the manufacturing industry and this company is at the top of it.
Challenge:
The company manufactures seven days a week and 24 hours a day. As a company that works all hours of the clock and uses many applications including CNC, Sanding, Blasting, and chop saws, an industrial dust collection system was more than necessary.
The combination of around the clock manufacturing with a variety of dust and fume producing applications had caused an enormous amount of dust build up in the manufacturing shop. Not only is the created dust and fume a fire hazard, but it is also a concerning health hazard for the company’s employees.
Solution:
After doing his research and ultimately finding Imperial Systems on a Google search for industrial dust collectors. Tom F., decided to purchase a CMAXX CM-024 dust collection system from Imperial Systems.
“I decided to do business with Imperial Systems because I liked the craftsmanship and quality of the dust collector systems that Imperial Systems manufacture.” said Tom
Since Imperial has a true systems background, which sets them apart from all of their competitors, the company was able to move quickly with the dust collector system installation. From the conceptual state, through quoting and design, and finally on through the installation, Imperial Systems was able to take care of anything and everything that had to do with the CMAXX- 024 dust collection system.
To this day, the system is running smoothly; according to Tom, things could not be better in the manufacturing shop. As a return customer for Imperial Systems, the company purchases Imperial’s own DeltaMAXX Replacement Cartridge Filters for their CMAXX Model.
Read more
Greg Dec 16 2013 Case Studies
DeltaMAXX Dust Collector Cartridge Filters Exceed Expectations at Welding Technology Program – Texas Community College
About The School: Located in northern Texas, the Community College offers comprehensive two-year educational programs – including welding technology. The school offers Associate of Art, Associate of Science, and Associate of Applied Science Degrees.
Challenge: The Welding Technology Program was interested in more cost effective cartridge filters for their Lincoln Statiflex 6000 dust collector.
Solution: In the summer of 2013, while making daily cold calls to businesses in the industrial realm, the Imperial Systems aftermarket member was able to strike a sale with the community college. While talking with the instructor of the Welding Technology Program, the aftermarket member found out that the school was shopping around for replacement dust collector cartridge filters for the upcoming school year. Due to the budget, it was a top priority that the filters were cost effective and reliable.
After reviewing the DeltaMAXX filter literature and cross-referencing the filters on Imperial System’s website, the welding technology instructor pulled the trigger and purchased four DeltaMAXX Replacement Cartridge filters for the upcoming school year.
Outcome: After running the filters in the dust collector for the fall semester, the welding school instructor was “really impressed” with the DeltaMAXX Replacement Dust Collector Filters.
“The System is running very smooth, not much back blow. When turning on the dust collector in the past we have had problems with smoke blowing out of the back. That problem went away when we installed the DeltaMAXX filters”, said the Texas welding school instructor.
“Imperial Systems’ dust collector filters are very durable and they are lasting much longer for us. My expectations were exceeded and you can count on us to be a returning customer.”
Read more
Greg Nov 8 2013 Woodworking
Imperial Systems’ BRF Replaces Leading Competitors at a Popular Woodworking Facility
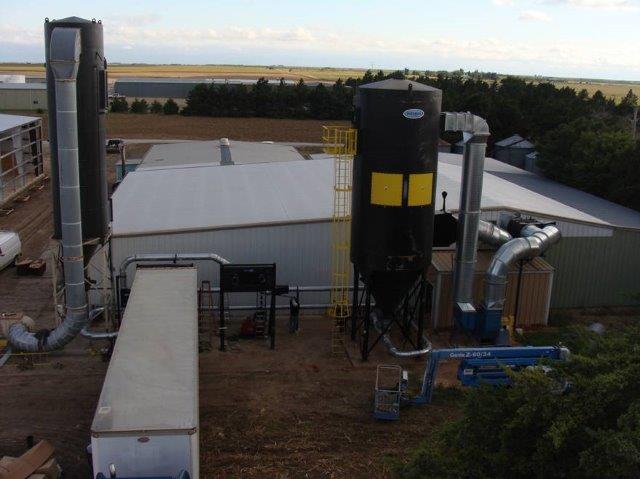
About the company:
A mid-market woodworking company that manufactures and distributes custom cabinets across the USA. The company uses a variety of tools such as: CNC turning equipment, table saws, planers, shapers, radial arm saws, jointers, and more.
Challenge:
In 2006, the company had purchased a 32-cartridge dust collector from a leading cartridge collector equipment manufacturer. Just a week after installation, the cartridge filters were plugging. The company tried to resolve the issue by using over bags and constant compressed air pulsing but nothing was working. The problem created serious downtime, constant maintenance on the cartridges, and excessive use of expensive compressed air. In the end, the problem was bad enough that the 32 cartridge collector was purchased back by the manufacturer and Westwind decided to head in another direction.
Solution:
Imperial Systems’ BRF cylindrical baghouse was chosen due to its forgiving design and its special characteristics built around the woodworking industry. The woodworking facility was impressed enough by Imperial Systems knowledge that they turned to Imperial later that year to purchase another system from them. By May of 2008, the 30,000 CFM BRF was officially installed. To this day, the BRF is still running extremely well and has relieved the company from their prior concerns.
“When considering wood dust extraction systems for any fibrous material, it is very important to consider dealing with a dust collection company that builds both bag style and cartridge style dust collectors. It is way too easy for a company that only builds one style to try and force it in all applications. This is just one of many stories where we have seen this unfortunate thing happen”, says Jeremiah Wann, President of Imperial Systems.
See also: Selecting an Industrial Dust Collector for Woodworking?
Read more
Greg Nov 8 2013 Case Studies
Sometimes, your search for the best solution can end in familiar territory.
Paul Arnold is the long-time Vice President of Operations for Keystone Ridge Designs in East Butler, Pennsylvania (keystoneridgdesigns.com). Since 1995, the company has supplied premium-quality steel trash receptacles, benches, bike racks, planters, and other heavy outdoor furniture to parks, campuses, municipalities, housing developments, and various retail establishments, including major shopping malls. All products are made solely in the United States, with all expert continuous-seam welding and powder coating done by hand.
“We have a sterling reputation, especially with landscape architects, for exceptionally durable, uniquely and contemporarily designed furniture that will hold up well in even the most challenging high-traffic outdoor areas,” says Arnold. “In short, we deliver great value over the life of a product. Not to mention, our look remains ‘current’ no matter how often a landscape might change – West Coast, East Coast, or wherever.”
Keystone Ridge Designs employs a continuous inseparable weld seam during its welding process. This step prevents corrosion from moisture over the life of the furniture. In addition, each bench, rack, or steel (composed of 25 percent or more recycled content) piece is protected from significant chipping, cracking, or sun damage by Keystone Ridge’s patented Keyshield® finish.
“The heart-and-soul of our fabrication excellence revolves around our powder-coating step,” claims Arnold. “After we sandblast our substrates to a white finish to remove all possible contaminants, we electrostatically apply a zinc-rich epoxy primer, followed by a coat of colored polyester powder. Both coats are oven-cured to ensure an optimal finish.”
But such elaborate production also yields a substantial amount of dust and fumes during manufacturing, particularly while workers, during two shifts per day, sandblast the substrate material.
“In any blasting environment, things get dirty and dusty in a huge way,” begins Justin Pyle, Shop Manager. “Sometimes, our worker can stay in the booth for no more than 20 minutes at a time due to the heat and dust generated. Not to mention, the refuse pot fills quickly and needs to be emptied.”
Keystone Ridge uses small dust collectors within its powder-coat booth…and had a much larger unit to remove air contaminants from the overall fabricating facility. However, Arnold, Pyle, and crew were not satisfied with the performance or some of the features of its prior larger system.
“Our basic issue was the horizontal positioning of the filters within our old collector,” begins Arnold. “The filters were literally on top of one another. That meant the top one would stay relatively clean – but would dump material, when purging, onto the filters below it, leading to what we thought was very premature filter failure throughout the system.”
Arnold then conducted a vast search into collectors that offered non-traditional vertically hanging filter placement. He also needed a unit that would fit nicely within a somewhat limited space on the firm’s property. He found the perfect – and familiar – solution not too far away.
“I kept hearing good things regarding the CMAXX® compact collector from Imperial Systems (isystemsweb.com),” says Arnold. “I then learned that one of my Grove City High School classmates, Jeremiah Wann, was president of the company.”
Wann and his installation crew soon performed an onsite inspection to ensure that the CMAXX unit would do the job for Keystone Ridge’s demanding conditions. They also needed to determine where the collector would best reside for maximum performance. Neither decision took long.
“Jeremiah made me extremely comfortable from the start,” says Arnold. “Imperial was willing – and able – to do whatever it took to meet our requirements. It also helped that I knew him. A purchase this large involves significant financial risk, obviously. But Jeremiah made me 100 percent confident that Imperial would stand behind its product.”
The CMAXX compact modular cartridge collector uses Imperial’s renowned DeltaMAXX™ vertically hanging filters with their unique NanoFiber Filtration Technology that incorporates a very fine surface layer of synthetic fibers to prevent particulates from embedding into the premier-quality media. As a result, the filters provide twice the service life versus competitive models, while yielding an extraordinary 15 ASHRAE MERV efficiency rating. In fact, the DeltaMAXX style pulses 94% less, and emits 97% less contaminant, when tested against other filters in its class.
“We installed our CMAXX unit and DeltaMAXX cartridge filters in September of 2012. In nine months, we have not had to change out a single filter,” begins Pyle. “Our air is remarkably clean throughout the blasting area – and the entire shop, in fact. The only maintenance I’ve had to do on the CMAXX is to apply some grease to a few screws around the compressor. And, best of all, material from one filter doesn’t fall down onto another filter because of the vertical positioning.”
None of the trouble-free operation of the Imperial products has been a surprise to Arnold, however. His thorough research had yielded only positive feedback regarding his former classmate’s company and offerings.
“A few of Imperial’s local installations were actually written about in our newspaper,” says Arnold. “All the press was completely favorable – and now you can add us to the list of completely satisfied users.”
The CMAXX dust collector has a unique Pulse Distribution technology that delivers 100% even pulsation across the DeltaMAXX filter wall – resulting in maximum dust-collection performance and filter life. It also comes with a 15-year warranty. Even though Keystone Ridge has yet to change filters, removal and replacement is fast and easy, when required.
In addition, the CMAXX dust collector has no external bolt holes. That’s especially critical for Keystone Ridge because the company’s unit is located outside.
“The CMAXX dust collector has amazing suction power…it draws air from everywhere,” states Arnold. “Its construction ensures that contaminants do not get back into the airstream and blown back at our workers. Plus, because there are no bolt holes, water cannot get into the unit to damage the filters.”
When Arnold and Pyle reflect on their Imperial purchase and brand experience, not a single negative enters the conversation:
“Consistency is the first descriptor that comes to mind,” begins Pyle. “Consistent and exceptional performance of the CMAXX collector, of the DeltaMAXX filters, and of the outstanding customer and technical support we receive from Imperial.”
Arnold connects all the key components and processes:
“We can fabricate the nicest park bench in the world…but if the finish is no good, then our final product is no good. The key to a perfect finish is proper substrate pre-treatment – leading to a superior powder topcoat. A first-class blast system is essential to such pre-treatment. Dust and fume collection is critical to keeping our blasting system operating at optimal levels. Bottom line: The Imperial products play an extremely important role in our overall production and ultimate success.”
Keystone Ridge Designs prides itself on continually exceeding customer and self-imposed expectations. It didn’t have to look far to find a partner with the same core values and reputation.
Read more
Greg Nov 6 2013 Case Studies
DeltaMAXX Replacement Cartridge Filters Prove their Worth in the Metal Working Industry
Product: DeltaMAXX Cartridge Filters
Application: Metal working
Customer: Major Lead Fabrication Products Manufacturer
About the Company
The largest fabricator of lead based products, besides batteries, in the United States. The company manufactures and sells its lead sheets and a variety of other lead based products, including drywall, plywood, lead strips, and discs, to a diverse industrial customer base.
Challenge
The contact has mentioned his cartridge filters, purchased from the manufacturer, were very poor quality. The cartridge filters were over-heating in the dust collector and the media was coming off in rock hard chunks. The inner metal fitting grate was melting the media on the inside of the filters after only a few months of use.
Solution
The lead product manufacturer was called from the office of the Imperial Systems After Market team. After an educated telephone conversation and researching the company and their DeltaMAXX cartridge filters, the prospect decided it was time to place an order and purchased Imperial System’s replacement DeltaMAXX Oval Filters in February of 2012.
The manufacturer is very pleased with the performance of the DeltaMAXX Replacement as well as the Imperial Systems’ aftermarket team. The lead based fabrication company is now a returning customer for Imperial Systems. The company has purchased a number of DeltaMAXX filters for their dust collectors since February of 2012.
“The cost has been great per unit when we compare to other companies. The cost has been more competitive and the quality has been much better. The cartridge itself is much more durable compared to what we were using in the past. Every time we have asked for a quote or response, we have always gotten a fast response. The information we got from Imperial about their DeltaMAXX filters has been as advertised. The product is less expensive and the quality is better.”
Read more