by Imperial Systems | Aug 4, 2016 | Uncategorized
Trade Schools Matter and This is Why They’re Struggling
Employers are looking for people with technical and vocational skills and training. Many blue-collar employees make more money than a lot of college graduates. So why are so many trade schools seeing funding cuts and falling enrollment?
Learning a skilled trade is a solid investment in a future career, and it allows many people to pursue jobs that they love. But in the United States, the importance of these careers is often overlooked. Many programs focus on preparing students for college. Some people will enjoy and achieve success in college. Others are looking for a different kind of education, want to start a career more quickly, or just want to pursue something they enjoy doing.
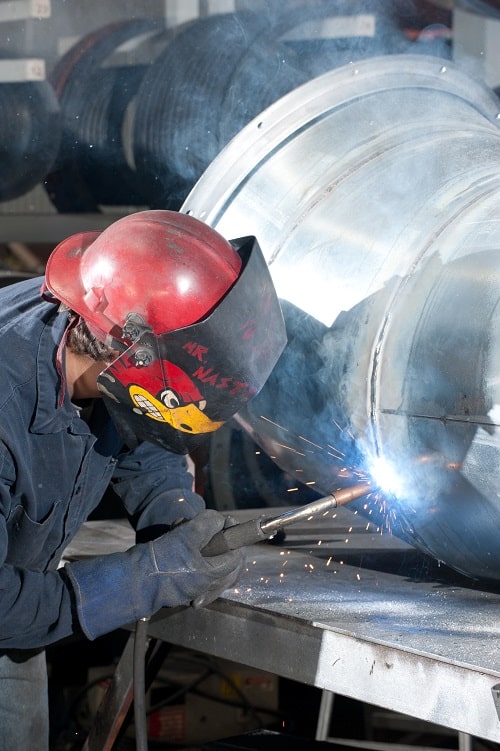
Trade schools prepare students for a future where there’s a need and they are valuable. Skilled employees with quality training continue to be in demand. Trade schools provide an option for people who want to jump-start a technical career. They offer job choices for individuals who might otherwise fall into in low-paying, unskilled work.
Targets for Budget Cuts
Unfortunately, education is always on the chopping block for budget cuts. Vocational programs and trade schools are often hit with these cuts since they are not considered “necessary.” (How many times have you ever used anything that you learned in most of your “necessary” high school classes?). Not everyone excels at typical college prep education, and they need and deserve other options.
In many countries, skilled trades are a valid career option and schools encourage interested students with educational programs and training. In the United States, however, attending college is often the definition of “success”, and many people treat vocational education as less valuable or only for people who can’t handle college. Neither of those things is true. The social status conferred by a college degree may not be worth the cost and time invested when there are so many opportunities in skilled trades. Many people invest money in a college education only to find that they can’t afford it, don’t enjoy it, or want to start a career sooner rather than later.
Hitting trade schools and vocational programs with budget cuts takes away the opportunity for many students to find careers, and also takes away skilled employees that businesses need. And while these programs have their budgets chopped, students struggle to find financial aid to help them afford them.
Our Perspective on Trade Schools
At Imperial Systems, we know that the success of our company depends on the hard work of our team, and nobody would be sitting in the offices if there weren’t skilled people working in the shop to make the products our reputation is built on. How many other companies in the United States rely on people with technical and vocational skills? If you’re reading this, there’s an excellent chance that your company probably does. If you want to make sure there’s a supply of well-trained employees for your company when you need them, the future of trade schools matters to you.
References:
https://www.washingtonpost.com/blogs/answer-sheet/post/why-we-need-vocational-education/2012/06/04/gJQA8jHbEV_blog.html
http://www.jff.org/blog/2014/02/26/importance-career-and-technical-education-expanding-opportunities
http://edlab.tc.columbia.edu/index.php?q=node/11936
Read more
by Imperial Systems | Aug 2, 2016 | Uncategorized
Whether you are a new manufacturing business or just branching out into new territory, if you are going to get into the metalworking field, addressing industrial dust control solutions demand some serious consideration. Not only do you have the safety of your work space to think about, but unchecked dust and fumes can also pose health hazards to those working in it. We’ve spent nearly 15 years considering the challenges of industrial dust accumulation and control, and we have developed the solutions our customers need. Discover the facts you need about dust control for your business so things run safely and smoothly.
Meet Safety Standards
An accumulation of dust in any industrial setting poses a threat to the health and safety of those working there. This is especially true in the world of metalworking where the fine dust particles may be especially toxic. In light of this threat, the Occupational Safety and Health Administration (OSHA) has established standards of safety that must be followed in any such industrial setting. These address not only inhaled dust but also the threat of combustibility through its accumulation. Check out the latest combustible dust update HERE. When you look for an industrial dust control system, begin by ensuring that it meets these and other industry standards.
Anticipate Dust And Fumes
As you consider a system to provide dust control for your workspace, make sure you take fumes into account as well. In many metalworking processes, noxious fumes are created which are more than unpleasant; they can be increasingly harmful when inhaled. Not all industrial dust control systems are created to handle this dual threat, so it is vital to choose a collector that can manage both dust and fume generated by metalwork manufacturing.
Your Industrial Dust Control Solutions Experts
Whether you need dust and fume filtration or just a dust collection system, Imperial Systems is your industrial dust control headquarters. We manufacture the most efficient, strongest, and longest-lasting systems and filters in the industry. Through these products, we have become well-known for our dedication to quality, value, and safety. Our outstanding line of equipment includes:
- CMAXX™ Dust Collector System
- DeltaMAXX™ Cartridge Filters
- CMAXX™ Laser Fume Extraction System
- Spark Arrestor
- Explosion Isolation Valve
- Custom Ductwork & Fittings
- Heavy Duty Abort Gates
- and more!
Most of our products are available to ship within 24 hours. For more information about our products and how we can support your metalworking business, contact us today.
Read more
by Imperial Systems | Jul 29, 2016 | Common Industrial Dust Collection System Problems, Uncategorized
Dust and Fume Collection: Some Industries That Might Not Know They Need It
Dust and fume collection in a manufacturing facility is important for many reasons. Here are the top five reasons you should consider:
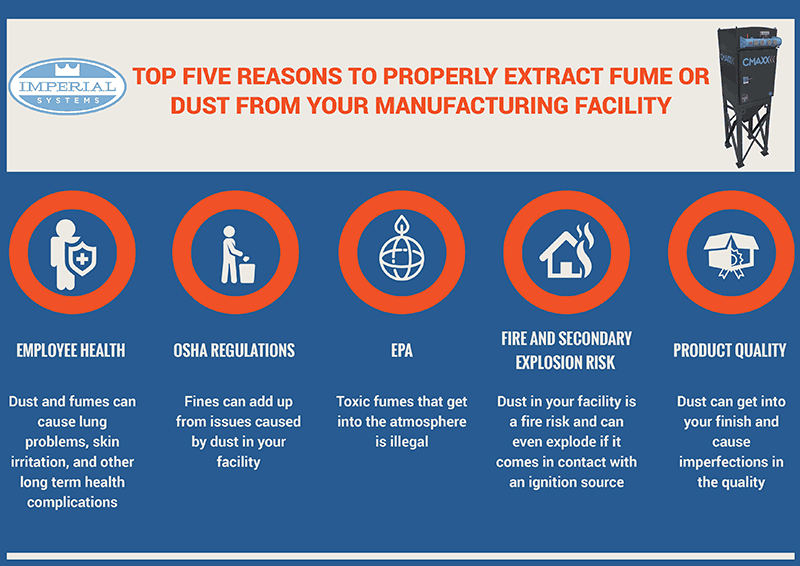
Not Convinced Yet?
Can you name the metal that causes cancer, damages skin, eyes, lungs, and kidneys, and is found in everything from stainless steel to dyes and pigments?
If you said this compound is Hexavalent Chromium (https://www.osha.gov/SLTC/hexavalentchromium/), you’re right.
Chromium is a component of stainless steel, added to make the steel more corrosion-resistant. Consequently, the fumes produced from welding, laser cutting, or plasma cutting stainless steel contain hexavalent chromium. While this form of chromium is known to cause cancer, it also directly attacks the lungs and kidneys and can cause severe eye and skin irritation.
Further, hexavalent chromium doesn’t just appear in welded or heated stainless steel. Electroplating with chrome also presents a hazard, and hexavalent chromium compounds are used as pigments in inks, paints, and many types of plastic. In fact, working on any material plated with chrome or coated with a chromium-containing material may release hexavalent chromium into the air.
Think hexavalent chromium isn’t something to worry about in your type of business? You certainly may need to reconsider. That’s because OSHA testing showed which types of facilities had detectable levels of this dangerous metal in their air. The following are some of the top offenders:
- Nonresidential building
- Highway, street, and bridge
- Foundation and structural materials
- Foundries
- Forging and stamping
- Architectural and structural metals
- Boiler, tank, and container
- Coating
- Engraving
- Heat-treating
- Agricultural machinery
- Mining machinery
- Ventilation and air-conditioning
- Aerospace products and parts
- Ship and boat building
- Automotive repair and maintenance
Any surprises on this list? If your facility is part of any of these industries, contact us at 800-918-3013 for an assessment of your dust and fume collection needs.
Related blog posts:
Read more
by Imperial Systems | Jul 26, 2016 | Uncategorized
Dust explosions are bad to begin with, but what do you know about secondary explosions? There are many factors that determine how likely a particular type of dust causes deflagration. When you think of combustible dust, do you think of the explosions you’ve heard about at grain handling facilities? Maybe you think of the explosive potential of aluminum dust.
Secondary Dust Explosion Incidents
Three dust explosions occurred in 2003. They demonstrate how many different types of production and manufacturing can produce a deflagration risk, including a secondary dust explosion. In a North Carolina plant, the application of a polyethylene coating to rubber caused accumulation of the dust. As the material dried, dust formed and accumulated above the work area. The work area was clean. But a layer of dust 1/4″ thick was enough to cause an explosion that killed six people. In this situation, a dust collection system in the production area could have captured the dust particles before they circulated through the facility.
The explosion in Kentucky was caused by combustible dust that resulted from a resin used to treat fiberglass. Workers were aware of the large quantities of dust. But cleaning processes often just caused more of the dust to become airborne. So, it accumulated in the ductwork and in dust collection equipment. There were no safeguards in place to prevent a flame front from traveling through the ductwork or getting into the dust collector. An abort gate with spark or flame detection could have identified and stopped the fire from spreading, and dust collectors designed to stop deflagration fronts could have prevented the dust collectors from becoming sites of secondary explosions.
Aluminum dust from scrap processing fueled the explosion in Indiana. The dust collector in this case was the source of the explosion. It did not have explosion vent panels, and instead of being directed safely, the explosion traveled back into the building and ignited dust in the ductwork. A secondary explosion occurred when dust accumulated on surfaces inside the facility ignited. A dust collector designed to isolate and redirect a deflagration could have prevented this accident.
NFPA Recommendations
The National Fire Protection Association, which establishes many of the codes and standards for handling potential fire hazards recommends that all dust collection systems should have explosion venting to redirect explosions and abort gates or other equipment to stop flame fronts from spreading. It also recommends improved housekeeping measures to prevent dust from accumulating. Accomplish this by collecting dust at the source so there’s no accumulation in difficult-to-reach places.
It’s often this accumulated dust, hidden on high surfaces, in corners, or inside ductwork, that ignites to cause a secondary explosion that’s far more dangerous than the original one. Witness reports of dust explosions often include descriptions of a smaller explosion followed by one or more larger ones; this is secondary ignition. Dust control throughout the facility, along with fire prevention equipment such as abort gates, spark arrestors, and explosion venting, can control a potential explosion and prevent a small fire from becoming a fatal disaster.
Read more
by Imperial Systems | Jul 22, 2016 | Uncategorized
Asking Questions About the Air You Breathe at Work
OSHA rules mandate that you have a right to know about any safety hazards that are present in your workplace, including the air you breathe. Most managers, supervisors, and owners certainly want their employees to be safe and want to avoid putting their employees in danger. But there may be workplace hazards they don’t know about. In addition, sometimes an employee’s questions can help them become aware of a situation.
For managers, supervisors, and other bosses, an employee’s concern about a safety issue is an opportunity. That is to say, it’s a chance for you to work on resolving the problem as a team. Consequently, the biggest OSHA fines go to employers who ignore safety issues. But employers who are working in good faith to resolve safety issues may receive recommendations from OSHA. But employers who have shown that they don’t care about fixing safety issues often receive gigantic fines.
Team Communication
The best way to avoid safety issues at work is for employees and bosses to communicate in a cooperative way. This benefits everyone. An employer who listens to and works to resolve the concerns of their workers will find that a reputation for being proactive and concerned about employee safety is good for business.
Since industrial dust and fume control is our business, making sure that workers are breathing clean, safe air is the aspect of safety we’re most concerned with. Many workplaces don’t know they need a dust or fume collector or don’t know when their collector isn’t working efficiently. Employees are sometimes concerned about what they might be breathing or exposed to in the air. A good employer should listen to those concerns and find answers to them.
Workers can be proactive in protecting their health. That’s by learning some important information about the materials they work with and what risks they might involve. For example, workers who are involved in cutting, welding, or otherwise producing fumes from stainless steel should have some awareness of hexavalent chromium. Further, workers who manufacture plastic products need to know about toxic elements like cadmium. Intended as stabilizers, they can also be hazards from the plastic itself. You may be uncertain about what hazards might be in your workplace. If so, you have a right to ask for more information about the air you breathe.
If employees have questions, OSHA has many options for safety training and awareness. An employer may be able to make concerned workers feel empowered and more knowledgeable by answering their questions and making sure they get the training they need. Employers must provide their employees with information about any hazards in their workplace. But sometimes those hazards may not be recognized until an employee asks a question.
Effective Discussions About the Air You Breathe
You have a right to ask your employer if you’re not sure what’s in the air you breathe at work. As an employer, it’s your job to check out your employee’s concerns. Then you can determine whether there is a health hazard to address. Proactively dealing with an employee’s concern shows respect for their needs and also a meaningful interest in employee safety and health.
If you feel that there’s a health risk in your workplace that you need to talk to your supervisor or employer about, you should know that OSHA regulations protect you from punishment or from any kind of retaliation, and your employer probably knows this.
The discussion will be more productive if a few points are kept in mind:
- The discussion is not an accusation. It is a question or issue that you would like more information about or are concerned about.
- The focus should be on making sure you and your coworkers are healthy and safe, because this is good for everyone and for the company.
- You have a right to ask for more information, more training, better protective equipment, or whatever you feel like you need to be safer. Being specific about how the problem could be solved helps people move forward with solutions.
- Be specific about your concerns and ask questions. If you feel like you don’t have enough information, talk to someone who can help you find what you need or look up some general information on the topic.
- Approach the discussion with the attitude that you and your employer have a mutual problem that you can work together to solve.
An example of how you might start a positive conversation:
1) I have a question about the welding fumes in the shop. It seems like some of the stations have a lot of fumes around them sometimes. Is there something we could do about that?
Or:
2) Some of us noticed that even though we do a lot of sweeping and cleaning up, there’s dust getting stuck up in places where we can’t reach it. What’s the safest way for us to deal with that?
Or:
3) I noticed there’s a sign up about (safety hazard), but I’m not sure we all know as much about it as we should. Is that something we could get some more information about?
Good ways for a supervisor or employer to respond to these might be:
1) We can definitely look at those stations and see if something needs to be done about the welding fumes. Are there places in the shop that are the biggest problem?
Or:
2) That’s a good question. We’ll have to figure it out. Does anybody out in the plant have any ideas for how to handle it?
Or:
3) Let me check out the OSHA website and see what they’ve got. I want to make sure you have all the information you need.
Of course, these things only matter if you follow up. Ignoring an employee’s safety concerns isn’t just disrespectful. It’s also a violation of OSHA regulations. And employees who aren’t comfortable talking to their supervisors about safety issues always have the right to contact OSHA for assistance. An employer who retaliates against, punishes, or fires an employee for reporting a safety concern to OSHA can face lawsuits and very large fines. Keeping the lines of communication open benefits everyone if a company can work as a team to identify and solve safety issues.
Read more