by Imperial Systems | Mar 1, 2016 | Uncategorized
Find out how metalworkers like you can address the need of a top-quality spark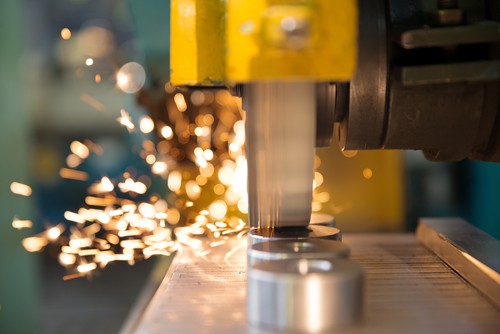
It’s no secret that the materials you work with everyday in the metalworking industry can create a serious risk for combustion. In fact, metals make up 20% of the materials involved in combustible dust incidents. And between 2008 and 2012, the United States Chemical Safety Board documented 50 combustible dust accidents, which led to a total of 29 fatalities and 161 injuries.
The spark trap is the solution to a very dangerous problem and the need to invest in the most advanced spark trap is clearly an essential safety decision that we at Imperial Systems take very seriously.
In fact, continuing customers rely on Imperial Systems when quality is of the utmost importance because they know Imperial engineers outstanding, high quality products to keep buyer’s employees and businesses safe from dust collection and the risks of combustion in the metalworking industry.
At Imperial Systems, we are dedicated to to helping metalworkers like you ensure the safety of your employees and efficiency of your workplace. We’ll discuss:
- Why a cutting-edge spark trap is of the utmost importance.
- The risks of an inefficient spark trap.
- Why the Imperial Systems spark trap keeps your employees safe from combustion hazards.
Why Invest in a Quality Spark Trap?
Designed primarily as a first line of defense to prevent ignition within a dust collection system, spark traps reduce the potential for fire hazard by capturing sparks before they reach the main containment unit, where dust or other flammable materials may be present.
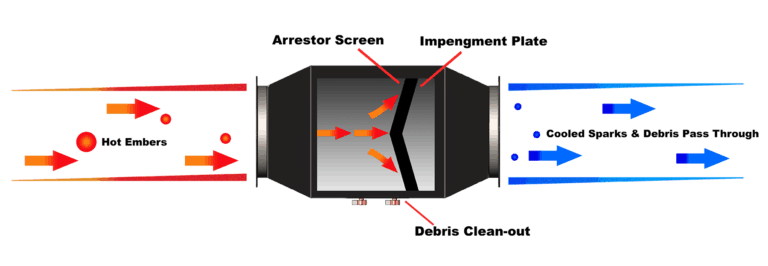
The risk associated with a spark trap that functions inefficiently to achieve the above scenario every time is that it only takes one small failure of the system to put your employees in a deadly situation.
Companies in the metalworking industry should consider implementing ways to control the elements of a combustible dust explosion. The NFPA recommends several practices and policies to prevent combustible dust explosions, including: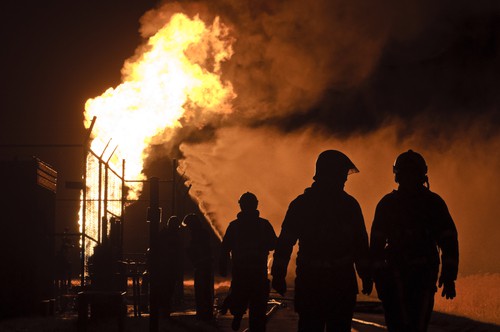
- use of dust collection systems and filters and surfaces that minimize dust collection
- use appropriate electric equipment and wiring methods
- controlling static electricity, smoking, open flames, sparks, and friction
- install and use spark/ember detection, extinguishing, sprinkling, and explosion protection systems
A spark trap, or spark arrestor, is an instrumental part of these methods, working to minimize risk by cooling and thus extinguishing sparks before they reach the filter surface. In the diagram above that shows the process of an Imperial Systems spark trap, note how the hot spark enters the arrestor which both cools and collects debris, before allowing the cooled ember to pass through.
The Cost of Procrastination: Why an Imperial Systems Spark Trap is Essential to Safety
An ineffective or entire lack of a proficient spark trap leads to an increased risk in danger associated with the metalworking industry. Without it, sparks can reach the main component, where dust and flammable materials fill the air, causing an explosion.
- A simple installation: Our unique spark trap system does not require upkeep from their providers, meaning they are hassle-free in addition to being simple to install and pre-wired. With tool-free filter access and change out, they do not require any moving parts or additional welding.
- Optional sizes and features: You can choose between a carbon and stainless steel finish. In addition, you can choose to include raw inlets, outlet edges, an integrated HEPA after filter, and more to your spark traps.
- Customized fit: With both horizontal and vertical configuration options, an Imperial Systems arrestor can be aligned to your collector without fail.
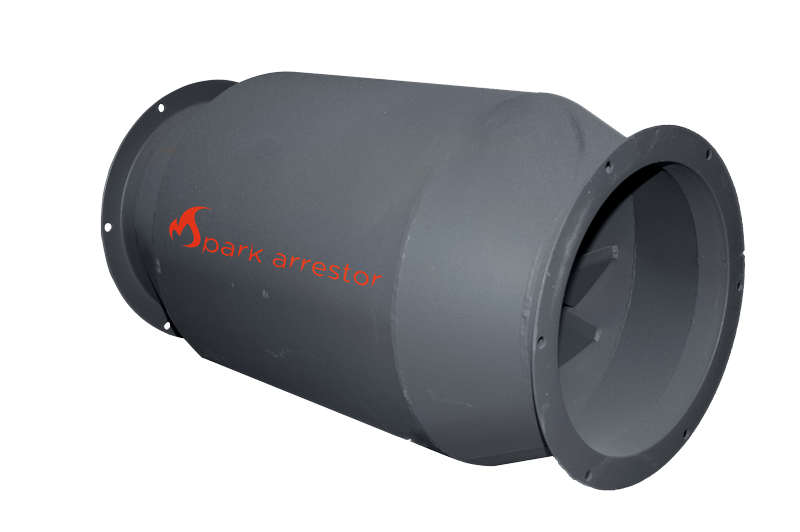
Your metalworking company is not like other businesses where the environment is at increased risk with the potentially explosive combination of combustible dust and sparks flying. It is vital that you act immediately to implement all of the required and recommended OSHA and NEPA safety equipment, including dust collection systems with sealed ductwork and an effective spark trap.
Choose Imperial Systems Today
https://www.isystemsweb.com/
If you haven’t yet decided on a spark extinguisher for your metalworking business, what is that procrastination costing you?
From 1996-2005, 106 explosions resulted in 16 fatalities, 126 injuries, and an estimated cost of $162.8 million in damages to the facilities.
As we know, sparks are a major cause of such explosions and an Imperial Systems spark trap is an essential piece of equipment that can mitigate the fears and risk of an explosion.
Contact Imperial Systems today at 800.918.3013 or learn more by emailing us at info@isystemsweb.com.
Read more
by Imperial Systems | Feb 16, 2016 | Uncategorized
Find out how metalworkers like you can address the issue of thermal spray fumes.
Enhancing the wear resistance of agricultural tools.
Protecting the elements of jet engines from high temperatures and oxidation.
Even providing electrical insulation for electronic devices.
These are just a few of the many uses of thermal spray coating technologies. Your own metalworking business probably has many other uses for the processes, ranging from large scale jobs to highly detailed ones. Although many different processes and uses fit within the category, they all share similar properties… and risks. Along with the versatility and usefulness of of thermal spray techniques come the dangers of ultraviolet light, fumes, dust, compressed air, gases. Are you protecting your operators sufficiently?
At Imperial Systems, we are dedicated to to helping metalworkers like you ensure the safety and efficiency of your workplace. In this blog, you will find:
- A clear outline of the risks associated with thermal spray
- A breakdown of OSHA safety recommendations
- A valuable solution to reduce the risks of fumes, dust, and gases
- An opportunity to collaborate with others in the industry about problems and solutions
Risks Associated With Thermal Spray Equipment And Use
As mentioned, there are countless uses for thermal spraying processes. To keep things simple, we’ll start by breaking them down into the different sorts of processes that fall within the category addressed in the blog. In the chart below, you can locate the process or processes used in your own workspace.
There are a number of distinct risks that are associated with each of these types of thermal spraying, including:
- Ultraviolet Light: Thermal spray systems product UV light, defined as non-ionizing radiation. The spectrum varies depending upon the type of process used. For example, flame spray processes produce such radiation in the UV-B or erythemal region of the electromagnetic spectrum. Plasma systems, on the other hand, operate with much greater intensity in the UV-C region. With prolonged exposure, such radiation can damage the eyes (flash burn), burn the skin, and cause changes in skin cell growth.
-
- Fumes and Dust: Another byproduct of the thermal spray process, dust and fumes created by atomized molten metals, can pose significant health and safety hazards. Not only do they form a potential combustion risk, but they are also hazardous if inhaled, causing a variety of negative reactions.
- Compressed Air: Aside from the well known danger when directed at unprotected skin or eyes, compressed air that is not properly regulated poses a number of other risks. Its noise levels can often cause hearing loss. Additionally, it is imperative to maintain the good condition of equipment, as damaged hoses can lead to explosion.
- Industrial Gases: The list of gases used in thermal spray processes is extensive, including: argon, helium, hydrogen, kerosene, and oxygen, among others. Each of these gases carries with it its own dangers. Many are flammable, corrosive, or pose the risk of combustion. Additionally, many are toxic when inhaled.
OSHA Safety Recommendations
Recognizing the numerous risks associated with thermal spray processes, the Occupational Safety & Health Administration has outlined a number of regulations and recommendations to keep you, your workers, and your workplaces safe.
First and foremost, owners and operators of such spraying equipment should understand and implement the operational procedures outlined by the product’s manufacturer. Additionally, all of OSHA’s standards on Welding, Cutting and Brazing should be heeded. Although they are numerous, the outline below will give you a basic idea of what steps can be taken to reduce this risks described above.
- Ultraviolet Light: Ensure that operators, assistants, and others in the vicinity of thermal spraying use the appropriate protection for their eyes and skin. This clothing should be tightly woven, including both gloves and coveralls. Additionally, tinted welding curtains and screens can reduce exposure to nearby workers.
- Fumes and Dust: To reduce the risk of various dangers associated with fumes and dust, make sure that you have a dust and fume collection system that is fitted to the necessary specifications. If you are working with toxic materials, HEPA filters may be necessary. In addition to an industrial dust collection system, it is also important to establish a respiratory protection program for workers, including proper fitting of respirators and regular medical screenings.
-
- Compressed Air: In addition to following manufacturer provided safety instructions for any compressed air, be sure to regularly inspect all of your equipment and follow the best practices for use. Not only will this promote safety for those using it, but it will also ensure the efficiency of the work being done.
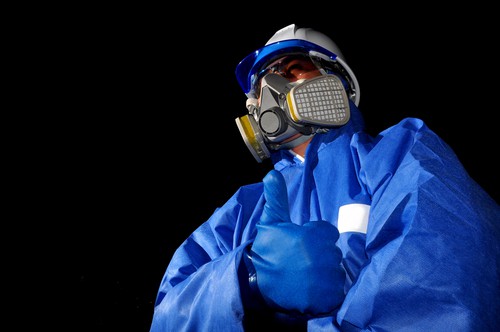
- Industrial Gases: Along with the safety precautions described for fumes and dust, it is also important to conduct regular air sampling to determine workers’ exposure to airborne contaminants. This is especially important when the gases being used in your manufacturing processes are potentially toxic; thermal metal spraying and practices like it can create fumes and gases at concentrations exceeding their Permissible Exposure Limits.
A Valuable Solution For Thermal Spraying Dusts, Fumes, and Gases
Although some safety precautions–such as eye protection and respirators– may be easy to address, an industrial dust collector is a very different kind of solution. A larger investment, such collectors require you to take a full assessment of your workplace to determine the specifications you will need. Not only do you have to consider the safety provided by this system, but you also need to think about its efficiency and ease of use.
At Imperial Systems, we had your needs in mind as we designed our CMAXX™ Cartridge Dust Collector, as well as the DeltaMAXX™ Cartridge Filters. This equipment ranks high in efficiency, while providing the outstanding protection you need. Just check out what the CMAXX™ has to offer:
- Best in Class Internal Velocities
- Vertical Cartridge Design for Longer Filter Life
- Tool-Free, Heavy Duty Filter Door to Reduce Service TIme
- Modular Design with No External Bolt Holes
- 100% Total Pulse Distribution
- Up to 40% More Cleaning Power Than The Industry Standard
This high performing dust collection system is designed to be used with our DeltaMAXX™ Replacement Cartridge Filters, which deliver the cleanest air and the longest filter life… meaning the greatest cost benefit to you. With the most Advanced NanoFiber Technology, it offers an impressive MERV 15 filtration efficiency.
Best of all, at Imperial Systems, we are dedicated to providing the best possible solution for metalworkers like you. So, if you aren’t sure what specifications are best for your shop, give us a call. One of our service engineers will help you make the best decision to keep your business running safely and efficiently.
Collaborating on Thermal Spray Solutions
Thermal spray equipment and processes have created major opportunities… and challenges. What problems have you encountered in your own work? Have you found a solution that works, or are you still searching?
Share your stories and questions in the comments section below to join the conversation on making thermal spraying processes as safe and efficient as possible.
Read more
by Imperial Systems | Feb 9, 2016 | Uncategorized
A quality dust collector for your plasma spray process is an investment in quality. Choose Imperial Systems.
Imperial Systems’ CMAXX™ Dust Collector is a truly versatile and cutting-edge machine that delivers the best system for mitigating fine dust particles from your facility. Across various industries, including those involved in plasma spray the CMAXX™ Dust Collector System has proven its advantages:
Space Saving – Low Profile Design, Small Footprint
- Vertical Cartridge Design – Longer Filter Life
- Best in Class – Internal Velocities are 20% Lower
- 15 Year Manufacturer’s Warranty
- Energy Efficient, High-Performance Manifold Mounted Pulse Valves – Increased Cleaning Power
- Tool-free, Heavy Duty Filter Door – Less Service Time
- Modular Design – No External Bolts on Dirty Air Plenum – Less Chance for Water and Air Leaks
- Heavy Duty 7 & 10 Gauge Construction; Nickel Plated Hardware
- Air Pressure Gauge on Compressed Air Manifold
- High Efficiency – Cleaner Plant Air
- PD Technology – Up to Twice the Filter Life
It’s imperative that companies invest in a quality dust and fine particle dust collector that is customizable for your plasma spray coating process. Safety and reliability should be non-negotiables in your OSHA and NFPA regulated plasma spray equipment.
Plasma Spray Solutions: The Imperial Way With the CMAXX™ Dust Collector
Properly ventilated work areas are a crucial part of the plasma spray process. A poorly ventilated area and low quality dust collection system can have a negative effect on both the worker and the process. Imperial System’s CMAXX™ Dust Collector System is the perfect modular dust collector system for thermal spray dust collection applications, including plasma spray. The atomization of molten materials produces a significant amount of dust and very fine fume particles.
The CMAXX™ dust collector system with DeltaMAXX™ Dust Collector Cartridge Filters will make any plasma spray fume collection process an easy task. Our equipment and systems are custom designed to fit into your existing operation with little or no downtime. We understand the risks associated with dust collection so we invest time and technology to making our equipment durable, safe, and reliable.
Contact Imperial Systems To Get Started With the Best Solutions for Plasma Spraying Processes
Our network of Imperial Systems Inc. representatives are all highly trained problem solvers with knowledgeable training in supporting our clients. If you’re convinced that Imperial Systems’ CMAXX™ dust collector is right for your plasma spray activities, we’d love to hear from you and guide you toward making a smart decision for your employees and your business.
If you’d like to request a quote or schedule an assessment based on your plasma spray needs for a hardworking, high-quality dust collector which is both OSHA and NFPA regulated, get in touch with us today at 724.662.2801 or by finding out more about us.
QUALITY. SAFETY. VALUE. Imperial Systems
Read more
by Imperial Systems | Feb 8, 2016 | Uncategorized
Don’t fall victim to lower quality dust collectors for plasma spraying. Invest in quality by choosing Imperial Systems.
You’ve done the research, searched through dozens of manufacturers and companies specializing in dust collectors for your plasma spraying process and now you’re ready to make a purchasing decision regarding a dust collection system that takes care of all processes of thermal spraying. Here’s why Imperial Systems is the right choice for cost-effective, time-saving, and innovative solutions.
You may already know that Imperial Systems prides itself on engineering outstanding, high quality products to keep buyer’s employees and businesses safe from dust collection and air pollution. With the current competitive economic environment, it’s imperative for businesses in the thermal spray industry to focus more on a dust collection system that lasts a long time.
When it comes to implementing safe and effective solutions for plasma spraying, Imperial Systems is highly regarded.
CMAXX™ Dust Collector As a Plasma Spraying Solution: The Imperial Way
Imperial System’s CMAXX™ Dust Collector System is the perfect modular dust collector system for thermal spray dust collection applications, including plasma spraying. The atomization of molten materials produces a significant amount of dust and very fine fume particles. Correctly ventilated work areas are a vital part of the plasma spraying process. A poorly ventilated area and collection system can have an adverse effect on both the worker and the process.
Typical Thermal Spray Technologies Include:
- Cold Spray
- Plasma Flame Spray
- Powder Spray
- Abrasive Blasting
- Combustion Spray
- Twin Wire Arc Spray
- High Velocity oxy-fuel coating spraying (HVOF)
The CMAXX™ is highly customizable and can be fitted for your unique dust collection needs including the above mentioned ones. The CMAXX™ dust collector system with DeltaMAXX™ Dust Collector Cartridge Filters will make any plasma spraying fume collection process an easy task. We understand the risks and concerns of handling combustible and toxic dusts from the thermal spray process. Our equipment and systems are custom designed to fit into your existing operation with little or no down time.
Reach Out to Imperial Systems Today
Convinced that Imperial Systems’ CMAXX™ dust collector is right for your plasma spraying activities? Our network of Imperial Systems Inc. representatives are all highly trained problem solvers with specialized training in supporting our clients.
If you’d like to request a quote or schedule an assessment based on your plasma spraying needs for a hardworking, high-quality dust collector which is both OSHA and NFPA regulated, get in touch with us today at 724.662.2801 or by finding out more about us.
Plasma Spraying | Spraying Plasma
Read more
by Imperial Systems | Jan 25, 2016 | Uncategorized
Protect your employees from the hazards of thermal spraying!
Thermal spraying is a coating process that combines a heat source and a coating material in powder or wire form, melts it, and sprays onto surfaces at a high velocity. There are many variations of thermal spraying such as:
Detonation Spraying
- Plasma Spraying
- Twin Wire Arc Spraying
- High Velocity Oxy-fuel Coating Spraying (HVOF)
- Warm Spraying
- Cold Spraying
- Flame Spraying
Thermal spraying provides wear resistant coatings to protect from erosion and abrasion, and provides different degrees of electrical conductivity. Thermal Spraying has been utilized by many industries such as: Transportation, steel mills, medical, military, computers, aerospace, and many more.
The benefits of thermal spraying are abundant, but execution of the process presents many hazards. The Fabricators & Manufacturers Association, Intl. says that thermal spraying creates toxic dust and fumes due to the atomization of molten metals, posing a dangerous environment for operators carrying out the process. The Occupational Safety & Health Administration (OSHA) has acknowledged the dangers of explosive gas and carcinogenic fumes from detonation spraying, and recommend implementing their safety standards. Implementation of a high quality dust and fume collection system and proper ventilation can provide a solution to this hazardous situation.
Solutions For Detonation Spraying Hazards
What can Imperial Systems offer the thermal spraying industry to improve the safety and security of their thermal spraying operators?
Imperial Systems is among the top dust collection equipment manufacturing businesses in North America. The high quality and efficiency of our CMAXX™ Dust Collection System is how we provide those in the thermal spraying industry with the safety and security they desire.
Our CMAXX™ Dust Collection Systems are designed with revolutionary PD Technology for maximum cleaning performance and has 10% more filter media than other same-sized vertical cartridge collectors, neutralizing and keeping the air clean while you work. The CMAXX™ dust collector system also allows for 20% more area around the cartridge filters which causes the dust to fall into the hopper before attaching to the filters. Our CMAXX™ dust collector offers these other features:
- Vertical Cartridge Design for a longer filter life
- Internal Velocities are 20% Lower – Best in Class
- Increased Cleaning power with an energy efficient and High-Performance Manifold Mounted Pulse Valves
- Fewer Internal Ledges for Material to Build Up
- Slanted Inlet Design that prevents water build up on the top of the 90° inlet
- Up to 40% More Cleaning Power – Up to Twice the Filter Life
- 15 Year Manufacturer’s Warranty
Combine our quality CMAXX™ dust collector system with our DeltaMAXX™ Replacement Cartridge Filters and you have the solutions to those safety hazard problems. Our DeltaMAXX™ Replacement Cartridge filters have nanofiber technology that stops submicron particles from embedding into the media, has the highest quality pleated media at a 99.9% efficiency, and are able to reduce the operational cost of your dust collector system with less pulse cleaning.
For more information on our CMAXX™ Dust Collector System and our DeltaMAXX™ Replacement Cartridge Filters contact Imperial Systems today!
Read more