by Imperial Systems | Nov 11, 2016 | Uncategorized
For some of us, FABTECH 2016 in Las Vegas is one of the biggest events of the year! Here’s a quick preview of the things you’ll see at our booth this year.
A CMAXXTM model CMoo8, fully operational and running, demonstrating a push-pull system:
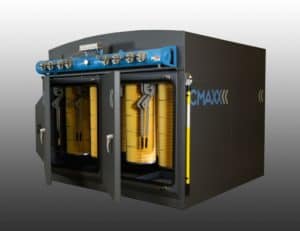
A Spark Arrestor, one of the simplest and most important components of a fire safety system:
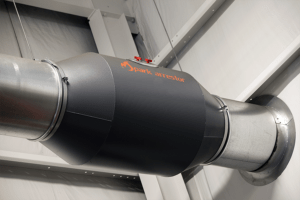
Spark Arrestor
Two CMAXXTM models (CM004), featuring our explosion venting and new FireTrace fire extinguishing system.
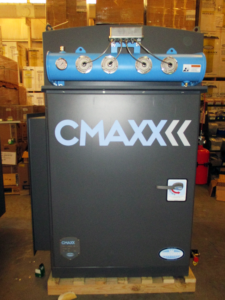
The official debut of our new portable dust and fume collector, the SHADOW:
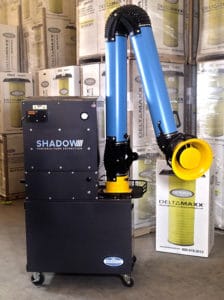
FABTECH 2016 Debut
Imperial’s superior MERV 15 nanofiber DeltaMAXXTM filters:
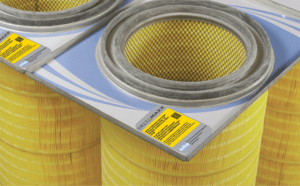
DeltaMAXX cartridge filters
FREE STUFF! Stop by and get a stylish Imperial Systems hat!
What happens in Las Vegas doesn’t have to stay in Vegas! We have 4 show specials that you can take with you!
Our three CMAXXTM Demos and the SHADOW Portable Collector are available for sale at the show. Stop by our booth and talk to an Imperial Representative to get the full details at the FABTECH 2016 show!
Visit us at booth N1825 and see why everybody at FABTECH 2016 is going to be talking about us!
Read more
by Imperial Systems | Nov 8, 2016 | Uncategorized
Your dust and fume collector can save you money on heating this winter. But to make the most of those savings, your system might need some winter maintenance. It’s that time of year when your dust collector system needs a little attention to make sure it’s ready for the demands of colder weather.
Winter Maintenance Checklist
Replace Those Filters
Winter maintenance means starting the new year with clean new filters… and you’re not going to want to change them in the middle of a snowstorm.
Changing the Magnahelic Gauge Filter
It’s easy to forget about this little filter, but it’s necessary to keep the gauge readings accurate. You should replace it whenever you replace your other filters.
Check for Accumulated Dust
If you’ve been working with the doors open during the warmer months and not running the dust collector as much, you might have dust accumulated, especially in high places or flat surfaces. For safety, try to remove as much of it as possible.
Check Airlock Wipers and Bearings
Usually, you should change airlock wipers once a year. Worn-out wipers don’t do their job properly. Winter maintenance is a good time to check them. When you replace wipers, you should also plan to replace the bearings.
Check Heaters on Pulse Valves
If you’re in a cold area and your pulse valves have heaters to keep them from freezing up, make sure they’re working. Frozen pulse valves are an inconvenience nobody needs to deal with in frigid weather.
Check Solenoid and Diaphragm Valves
Again, these are not things you want to have broken in the middle of nasty cold weather. A quick check and some preventative maintenance if necessary can save you a headache later during winter.
Check Compressed Air Hoses
Cold can make hoses more brittle and likely to break. If your compressed air hoses have any weak spots or look worn or damaged, now is a good time to make sure they get fixed or replaced.
Check Seals and Gaskets
As with the hoses, cold can make seals and gaskets crack or develop leaks. If needed, replacing them before the weather gets cold can save you from dealing with downtime from an unexpected leak.
Calibrate Differential Pressure Gauge
If you have the tools to do it, this is a good time to calibrate the differential pressure gauge and make sure you’re getting accurate readings. These gauges need to be calibrated occasionally to give you the most accurate information
Check Your Dust Collector Roof
If you’re a CMAXX owner, lucky you! Your domed CrownTech roof will keep snow or ice from piling up on top of the collector. If you don’t have a CMAXX, make sure you keep an eye on the amount of snow or ice buildup, since that can cause leaks into the collector.
Read more
by Imperial Systems | Oct 26, 2016 | Uncategorized
OSHA just released the first guidelines and recommended practices list in more than twenty years. Is it something you need to know about? Probably. But you probably don’t have a few hours to spend browsing their website for information. Save yourself some time. Here’s a summary of the important parts, and links to get you to the ones you want to know more about.
OSHA Guidelines and Recommended Practices
Getting Started
First off, here’s a quick guide to the process of implementing recommended practices:
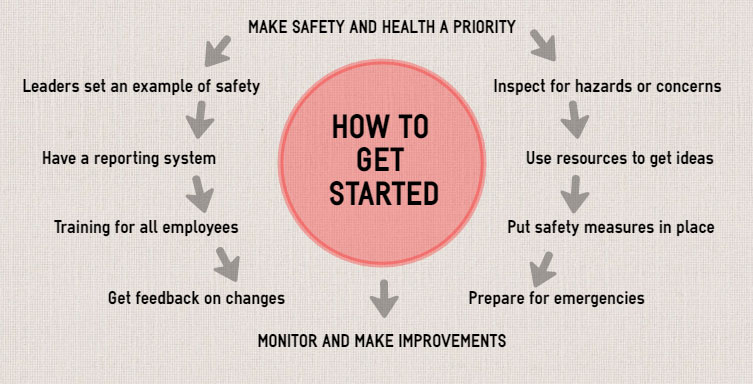
There are two areas of focus here: preparing and training people, and inspecting and improving facilities, equipment, and practices. If you need some more details, head to this link: https://www.osha.gov/shpguidelines/ten-easy-things.html
Getting Management to Work With You
You’re going to have a hard time getting a safety program off the ground if management isn’t buying in. The OSHA guidelines recommend four basic steps below to make sure they’re with you:
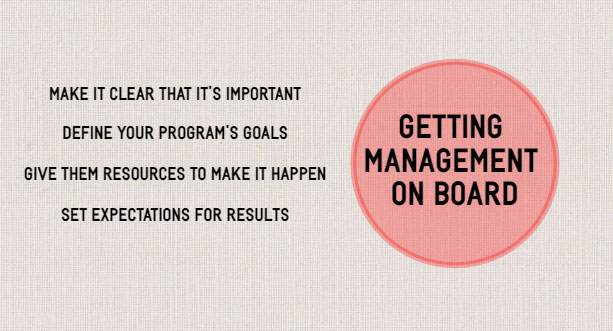
If you need more details about things you should do to get management and leadership engaged, this is your place to look: https://www.osha.gov/shpguidelines/management-leadership.html
Getting Workers Involved
If getting your workers to be involved and serious about your safety program is a concern, here are suggested steps in the OSHA guidelines to make sure you have genuine worker investment:
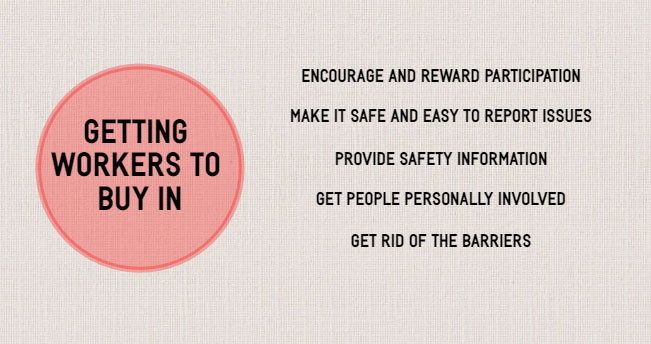
So what does it take to get workers to care about and want to participate in your safety program? And what are some of the barriers to their participation? If this is a topic you’re interested in, here’s the place to go: https://www.osha.gov/shpguidelines/worker-participation.html
Hazard Identification, Control, and Prevention
Before you can do anything about hazards in your workplace, you have to find them. Not just the obvious ones, either: there may be hazards that only people who use a particular machine or work in a particular area are aware of, for example.
Once you’ve identified the hazards that need to be addressed, what do you do about them? You look for ways to control them, starting with the most dangerous or the ones that can be easily eliminated. Getting workers involved in deciding what controls you’ll use is also a great step to get them more active in the program.
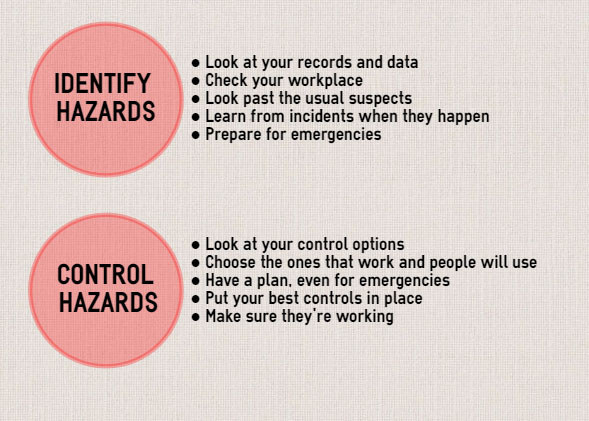
These are obviously the nuts and bolts of a safety program, but they don’t work if you haven’t gotten managers and workers on board and involved. Workers are probably the people most likely to know where the real hazards are and where things might go wrong, but they’re not likely to want to talk about it with management you’ve established a program where reporting a hazard is encouraged, not punished.
If hazard identification is your topic, check here: https://www.osha.gov/shpguidelines/hazard-Identification.html
If you’re moving past identification and ready to tackle prevention and control, this is your destination: https://www.osha.gov/shpguidelines/hazard-prevention.html
Education and Training
You can have a great program, but if nobody knows what to do or who should handle what part, you’re not going to get anywhere. Here’s the very basic breakdown:
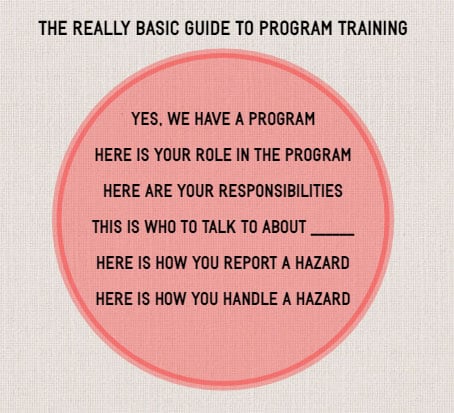
OK, you’re probably going to need to get a little more in-depth than this. Fortunately, OSHA has some handy resources available, including training tools to help people get better at spotting hazards: https://www.osha.gov/shpguidelines/education-training.html
Program Evaluation and Improvement
So you started a program, and you got everyone to participate, and things seem to be going really well. Or perhaps your program, for whatever reason, isn’t doing what you hoped it would do. Evaluation is the part where you figure out what’s going well and what’s not. And improvement is the part where you do more of what’s working and less of what isn’t.
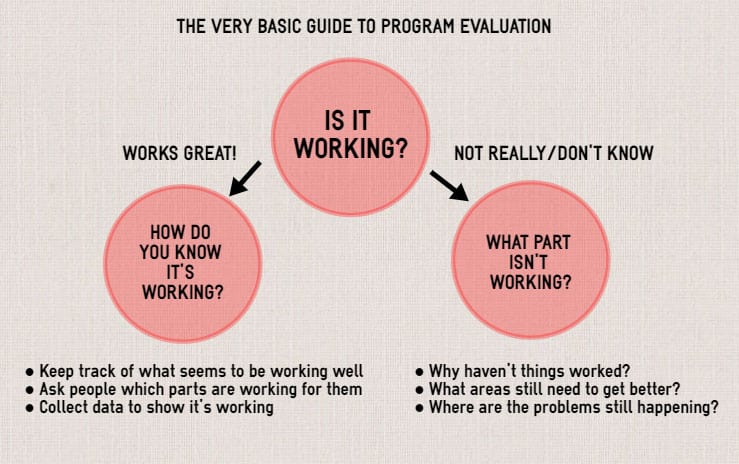
If you’re working on a safety program and need to be able to report on how it’s going and what it’s doing for the company, check out OSHA’s suggestions and tools for figuring it out: https://www.osha.gov/shpguidelines/program-evaluation.html
Additional OSHA Guidelines Information and Assistance
There’s your very quick summary of OSHA Guidelines and Recommended Practices! If you need lots and lots more information, OSHA makes sure you have tons of links and helpful tools to check out on their “additional resources” page here: https://www.osha.gov/shpguidelines/program-evaluation.html.
As always, if you are looking for dust and fume collection or fire and explosion safety controls, we are here to help you with any information you need. Using this equipment is a best practice for dealing with combustible dust, including spark arrestors, abort gates, and fire retardant dust collector filters.
DISCLAIMER: This guide is not intended to be used in place of OSHA guidelines or actual recommendations. We hope it helps you get an overview of what’s available, but while we are dust and fume collection experts, we defer to those more knowledgeable when it comes to safety program design.
Read more
by Imperial Systems | Oct 24, 2016 | Uncategorized
Extinguish the Threat of Explosions with a Spark Arrestor
It’s imperative that every metalworking facility have highly efficient dust collection systems. Also, it’s crucial that metalworking facilities utilize a spark arrestor to provide even greater protection from these combustible hazards. Here’s why a Spark Trap safety system by Imperial Systems is the best choice.
We have dedicated over 15 years to preventing and reducing fires and explosions in metalworking and manufacturing facilities. We also continually strive to meet and exceed the standards recommended by the Occupational Safety and Health Administration. Our company also meets NFPA guidelines with our highly efficient dust collection systems and replacement cartridge filters.
If you’re asking yourself if a spark arrestor is really necessary, the answer is yes! First of all, consider the findings of OSHA’s National Emphasis Program. It shows that metal dust accounts for 20% of explosions nationwide. Also, 7% of ignition sources are ignited by fabricated metals. Further, another 8% of ignition sources are caused by primary metals. So, if you want to reduce the possibility of an accident at your metalworking facility, you MUST invest in spark arrestors!
How can Spark Trap safety systems reduce explosions?
Adding a spark arrestor to your industrial dust collection system is like adding a security system to your home. That is, you already have the proper amount of protection with locks. But installing a security system in your home provides another line of defense. Above all, it keeps you and your family safe.
Our spark arrestor, named Spark Trap, is the first line of defense in protecting your metal fabricators and your metalworking facility from explosions. Spark Traps extinguish nearly every spark before it enters the main containment unit where combustible dust and other flammable material collect. When you choose our Spark Traps, you’ll receive a quality product. We make it with heavy-duty materials and it’s highly effective at keeping sparks from entering your industrial dust collector.
Here are some key features you’ll receive when you invest in our Spark Trap safety system:
- Maintenance free components
- Fully welded construction
- Easy install for any system
- No moving parts
- Available in carbon steel or stainless steel
- Can be installed in horizontal or vertical configurations
- Available in 6 to 40 inches
- Clean-out door
- Doesn’t require water
Spark Trap optional features include:
- Raw inlet and outlet edges
- A clamp together function for clamping duct
- Rolled angle flange for bolt-together duct
Want to know more about the Spark Trap? Check out our FAQ sheet to learn all of the benefits of our Spark Trap safety system.
Read more
by Imperial Systems | Oct 19, 2016 | Uncategorized
When Water Turns a Fire Into an Explosion
A combustible dust explosion is an ever-present danger for workers in many industries. These two examples show that despite increased awareness, explosive dust still puts lives at risk. One thing they both have in common: water may have actually made them much worse.
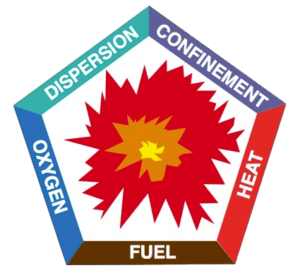
Case #1: Grain Dust
The first example shows how even things that seem like safe and practical fire-fighting measures can lead to disaster. In May, a grain dust explosion occurred in a silo. It injured a worker who was attempting to put out a dust fire with water.
Because the very fine dust was contained in the silo, all the criteria for an explosion were present… except for one. The dust provided fuel for a fire, and the open silo hatch provided oxygen. With the material confined in the closed space of the silo and an ignition source in the form of a grain dryer, the dust explosion danger was high.
Ironically, it was the worker spraying water onto the fire that created the explosion by adding the last element: dispersal of the dust. Water hitting the dust added more air and also raised a cloud of dust. Dust suspended in the air turns the situation from a fire into an explosion. In this case, it blew the roof off the silo and caused serious injuries.
Case #2: Fish Meal Dust
The second example is in some ways a classic industrial dust explosion, except that the material isn’t one you’d expect. In September, a seafood processing plant was seriously damaged and had to be shut down because of an explosion caused by the ignition of fish meal dust.
Fish meal is a fine, dry powder that manufacturers often make into fish food. A local official noted that this is the third time he knows of that fish meal has caused an explosion at a local plant. In this case, a burst pipe may have created an explosion by causing dust to become airborne.
While people don’t think of fish as being explosive, they usually don’t think of metal as being explosive either. Both of them pose an explosion danger when in dust form.
While we talk a lot about combustible metal dust and fumes because many of the industries we work with use metals, organic dusts like grain, spices, powdered milk and egg, sugar, tobacco, and yes, even fish are dangerously explosive if all the right elements are present.
Secondary Explosions from Airborne Dust
While many places that produce metal dust are aware of the risks, some places that produce organic dust don’t realize the danger it poses, or how important a dust collection system is for controlling and handling dust. The most catastrophic damage is often done by secondary explosions: a small dust explosion causes accumulated dust to be dispersed in the air, causing a much larger explosion. Spraying water on a dust fire can do the same thing, sending dust into the air.
Minimize Dust Explosion Danger
Removing dust from the facility and collecting it with a dust collection system designed to prevent or safely control explosions is an important safety strategy. Making sure that dust will not disperse in the air is another key to explosion prevention. In any situation with combustible dust, equip the system with safety features. Spark arrestors, explosion vent panels, and chemical suppressors can curtail the dust explosion danger in your factory.
Reference:
http://www.ktoo.org/2016/09/20/explosion-westward-seafoods-sparks-police-investigation/
http://www.adn.com/alaska-news/rural-alaska/2016/09/21/official-blames-fish-meal-dust-in-100k-explosion-at-dutch-harbor-seafood-plant/
https://www.commerce.wa.gov.au/sites/default/files/atoms/files/5-2016_grain_fire_and_dust_explosion_in_silo.pdf
http://content.safetyculture.com.au/news/index.php/10/safety-alert-issued-grain-fire-dust-explosion-silo/#.V_-WMugrKM-
Read more