by Erin Long | Jun 26, 2019 | Plasma Cutting
At Fabtech in Chicago, Lee Adams of Leeco Solutions met representatives from a metal fabrication company in Cincinnati, OH who were struggling with their dust collection system. The company operates two robotic plasma cutting booths, cutting holes in ½ inch pipe. The dust collector seemed to be removing the fumes well enough, but there was a problem.
Short Dust Collector Filter Life
Running 8 hours per day, the filters in the dust collector needed replacing after only 80 hours of operation. Many manufacturers get six months to a year out of their filters before changing them. This company was spending enough on replacement filters to pay for a new dust collector.
Lee visited the facility and measured the airflow at each of the plasma cutting booths. He discovered that the system could capture the fumes. However, it failed to keep the filters clean, causing them to stop functioning.
Filter Cleaning Efficiency Required for Plasma Cutting Fumes
Lee examined the existing dust collector, a CMAXX competitor, a 12-cartridge collector with vertical filters and reverse pulse cleaning. He suggested replacing this collector with a 12-cartridge CMAXX for the plasma cutting operation.
Lee’s contact at the company was skeptical. He needed a guarantee that the new dust collector would give him 2000 hours of filter life. Lee knew the CMAXX could do the job.
CMAXX Replaces Failing Competitive Unit
The competitor’s collector was replaced with a CM012. The new dust collector worked as planned, easily handling the fumes from both plasma cutting booths.
Now, the next step was to wait. Would filters that used to last a week be able to give the company the 2000 hours of operation that Lee had guaranteed them?
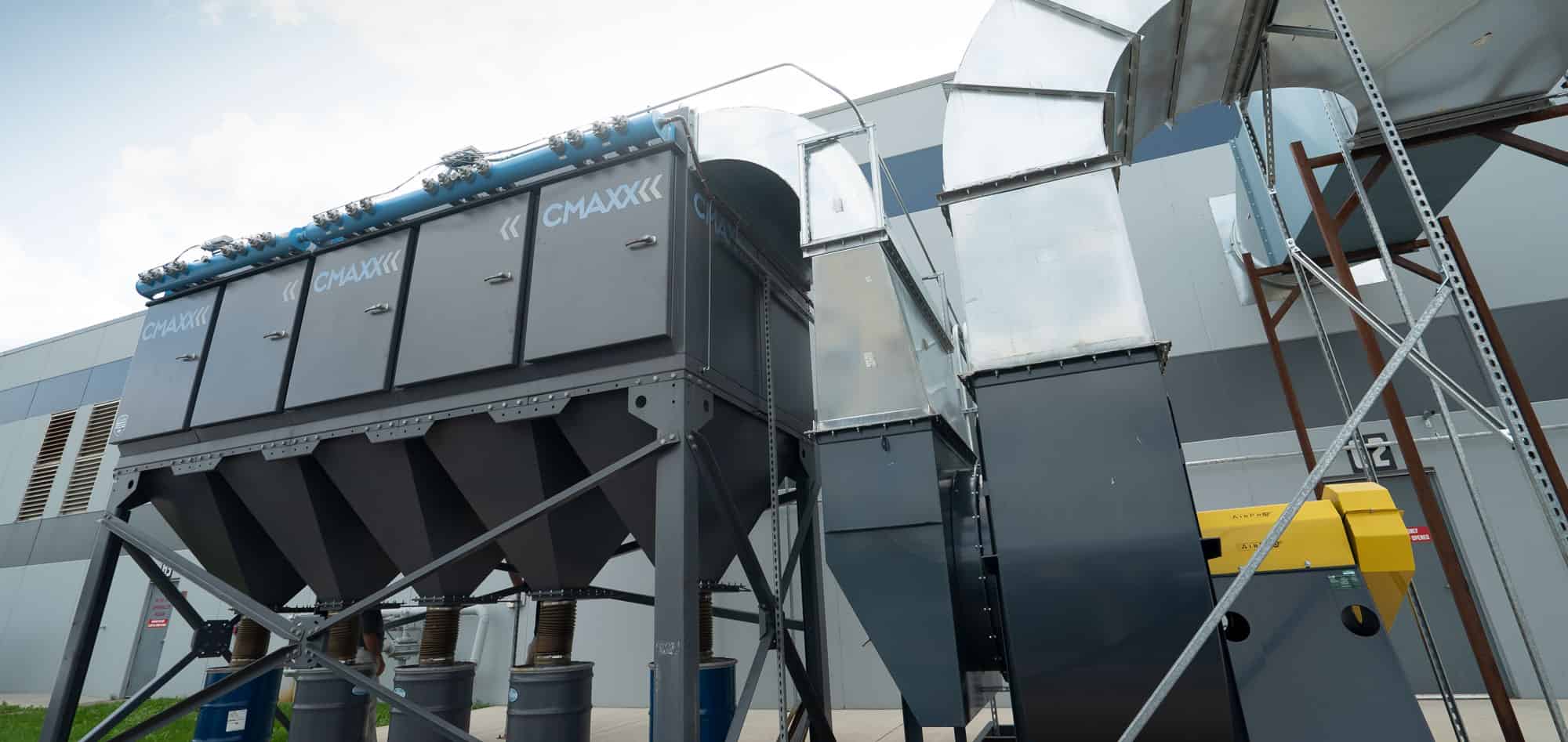
Success and Satisfaction for Plasma Cutting Booth Customer
The CMAXX system on the plasma cutting booths has currently been operating for an entire year. Lee’s contact at the company reports “It’s been running a year and is setting at 1.9″ WC. I’m going to get two years out of these filters!”
Instead of needing to be changed after a week, these filters are still going strong after a year. Differential pressure readings show that they’re not going to need changing any time soon.
This example proves that to solve a problem, you don’t always need a bigger dust collector. Sometimes you just need a better one. A superior product with a better cleaning system, the company’s new CMAXX left the competition in the dust.
Learn more about plasma cutting fume extraction.
Read our white paper on plasma cutting.
Read more
by Erin Long | Jun 5, 2019 | Case Studies
A sawmill company with facilities in Pennsylvania and New York had a challenging dust problem. Fine sawdust from their band mills was filling the air. The constant production of dust created an unpleasant work environment for employees. As a result, the facility needed a form of sawdust collection.
Ryan is responsible for creating a better, healthier environment for sawmill employees. But he wasn’t going to rush in with a hasty solution. He was going to take the time to do it right. So he would work with equipment suppliers to design the system his company needed.
In the process of designing a dust collection system, Ryan worked with Hermance Machine Company. Through them, he learned about Imperial Systems, Inc and their BRF baghouses. In addition to the BRF, he also looked at the products made by several competitors to compare them.
Ryan paid a visit to Imperial Systems. He got a chance to look at the BRF baghouse and the manufacturing process. “I saw a good product,” he says. He also liked the idea of working with a local company.
Ryan had been working on the air filtration project for several years. He planned out the ductwork, fans, and other details of the system. A significant part of the investment would be the baghouses. So it was important to choose the right company to build them.
Sawdust Collection Solution
Imperial Systems provided Ryan’s company with two reverse-air 14-foot BRF baghouses as well as airlocks, one for each of the two locations.
“Having this system has completely changed the environment of the sawmill,” Ryan says. “It’s gone from being a poor environment for employees to having crystal clear air.”
Ryan has succeeded in his goal of making the sawmills a better, healthier place to work for everyone. He says that the BRF baghouses are working exactly as he expected them to. He’s certainly satisfied with the help and service Imperial Systems has provided. This includes working with him through some glitches to make sure everything works the way he needs it to.
At Imperial Systems we take pride in working with our customers throughout the process, and our service doesn’t stop when the equipment install is complete. We’re there to work with you, iron out any bugs, and help you meet your air quality and safety goals. Sawdust collection is only one of many applications for which we have solutions. So contact us today about your challenging dust or fume problem.
Learn more about woodworking dust collection.
Read more
by Erin Long | Jun 4, 2019 | Abrasive Blasting
The Problem
Abrasive blast equipment operation continued to be a problem for a pipe manufacturer in Arkansas. The company produces pipe for water, gas, oil, and other industrial markets. They use abrasive blast cabinets in their production to clean the metal surfaces. Round steel shot is the abrasive blast media. However, this fugitive material accumulated in the facility. Their existing dust collector was also pulling it up into the ductwork. As a result, the weight strained the duct.
Further, the company required a system to handle multiple capture points on equipment like bucket elevators and hoppers. They needed to replace the existing dust collector. Initially, they received quotes from other companies who told them they needed a 9,000 CFM system. Unconvinced, the company chose to contact more experienced dust collection experts. They asked the specialists at Air Solutions to come in and review the situation. They wanted to eliminate their problems with a properly designed abrasive blast dust collector system.
The Solution
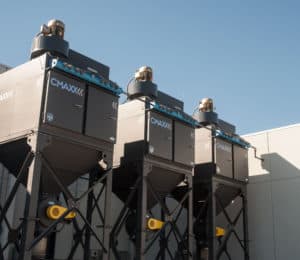
Air Solutions conducted a survey and decided that the system must be rated for 11,000 CFM. It also needed to have air bleed-in ports to keep the system from picking up the steel shot. This arrangement would allow the adjustment of airflow. The control measure ensures that the system picks up dust and other material but not the abrasive blast media.
The survey also determined that existing dust collection on capture points like bucket elevators and feed hoppers was inadequate. So the new system provided dust collection at these points as well as on all the abrasive blast cabinets.
Air Solutions installed a CMAXX dust and fume collection system. They designed an 11,000 CFM system to provide plenty of airflow to all the points of capture. Also, they incorporated air-bleed ports. Enabling adjustability of the airflow, these prevent the system from picking up heavier shot blast media.
Abrasive Blast Equipment No Longer a Concern
The new system certainly creates proper airflow to all capture points on the system. The company uses the bleed-in ports to adjust the amount of ambient air being pulled in. Airflow is now adjustable, helping to make sure they capture dust, not shot blast media.
Increasing the airflow from the proposed 9,000 CFM to 11,000 CFM was key. It makes sure the system is able to handle all the capture points. In addition, the bleed-in ports provide the option to control airflow at various points. The result is complete control over the system and a safer work environment.
Learn more about abrasive and shot blast dust collection.
Read more
by Erin Long | May 8, 2019 | Case Studies
Problem:
James is the senior industrial engineer at a company in Kansas. Recently, the company bought a pipe plasma cutting machine. At the time, James knew that plasma cutting would produce a lot of smoke and that he needed a dust and fume collector.
James and some of his coworkers had visited another Imperial Systems customer who already has a CMAXX doing fume collection on a pipe plasma cutting application.
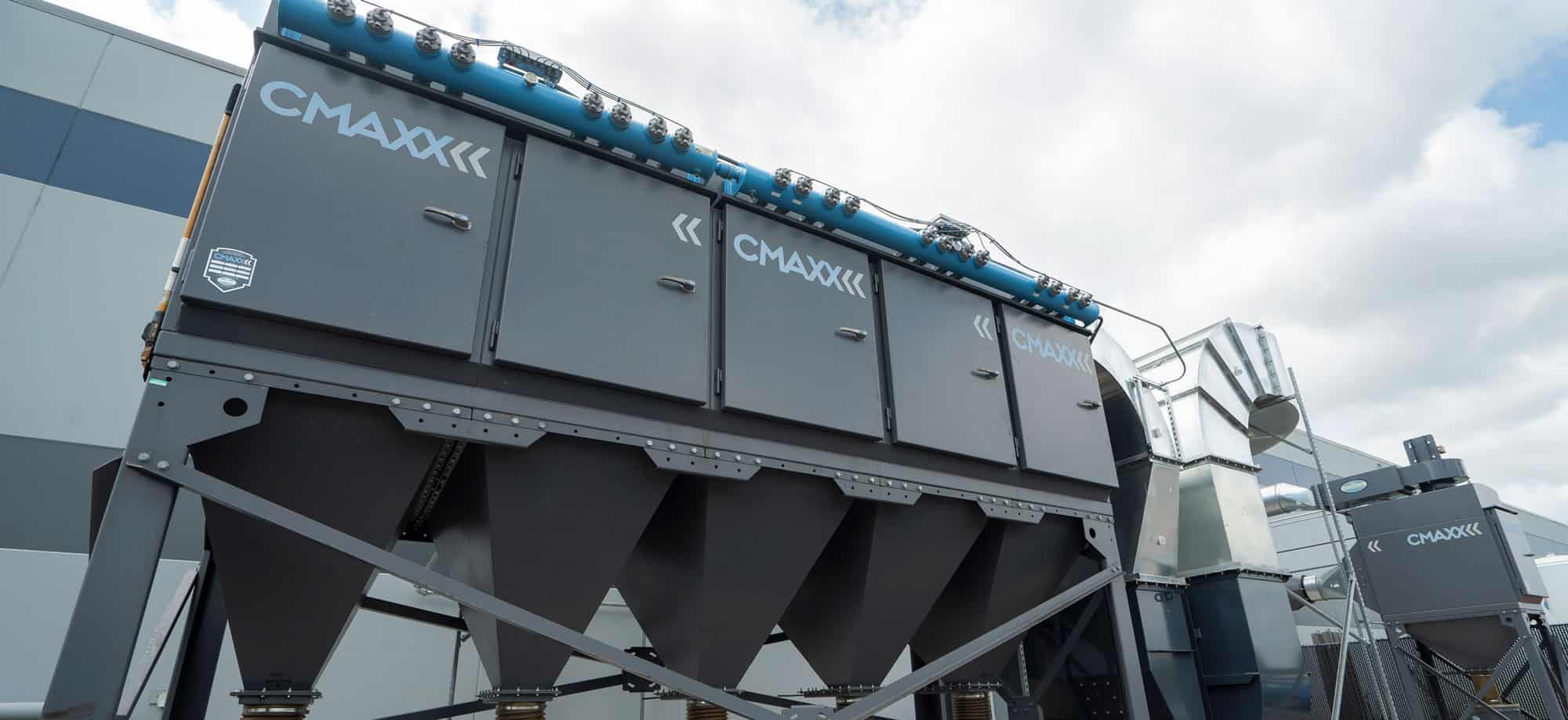
“They spoke really highly of you guys and your product, and even about buying the parts and filters,” James said. “That was certainly a big factor in choosing your company.”
Inquiring at Imperial Systems, James found himself working with salesperson Justin and engineer Troy to design a system for his application. Because he was warned about the amount of smoke a plasma cutter produces, he wanted to be prepared.
The new collector had to meet air quality standards and be able to capture the very fine smoke from plasma cutting. Imperial Systems provided the data showing that the CMAXX will do everything he needed it to do.
As for working with a company located in Pennsylvania while his company is in Kansas, James laughed. “Long distance relationships can be a little tricky, but we were able to work everything out. “
Pipe Plasma Cutting Solution:
The solution that James and his team at Imperial Systems agreed on was a CM008, an eight-cartridge collector. To achieve fine particulate capture, the collector uses DeltaMAXX nanofiber filters suitable for plasma smoke. The importance of air quality control means that fume collection from the pipe plasma cutting machine needs to be completely under control.
The new system performs as designed for fume collection for pipe plasma cutting. Some adjustments were made to the source capture point for cutting sheet metal, but the system is adaptable. As a result, by James being proactive with getting dust and fume collection for his new equipment, he prevented any air quality issues.
Feedback:
“The guys from Imperial System worked with me and were very helpful,” James said. “We also really like your hats. The guys in the shop love them. So we asked for more hats and Justin sent us more. But there still weren’t enough, though. The guys want more hats.”
Somewhere in Kansas, there’s a shop full of guys wearing Imperial Systems hats. We’re proud that our CMAXX, our service, and our hats have proved themselves in the field once again.
Read our white paper on plasma cutting smoke.
Read more about plasma cutting fume extraction.
Read more
by Erin Long | Apr 24, 2019 | Weld Fume
Problem: Welding Ventilation
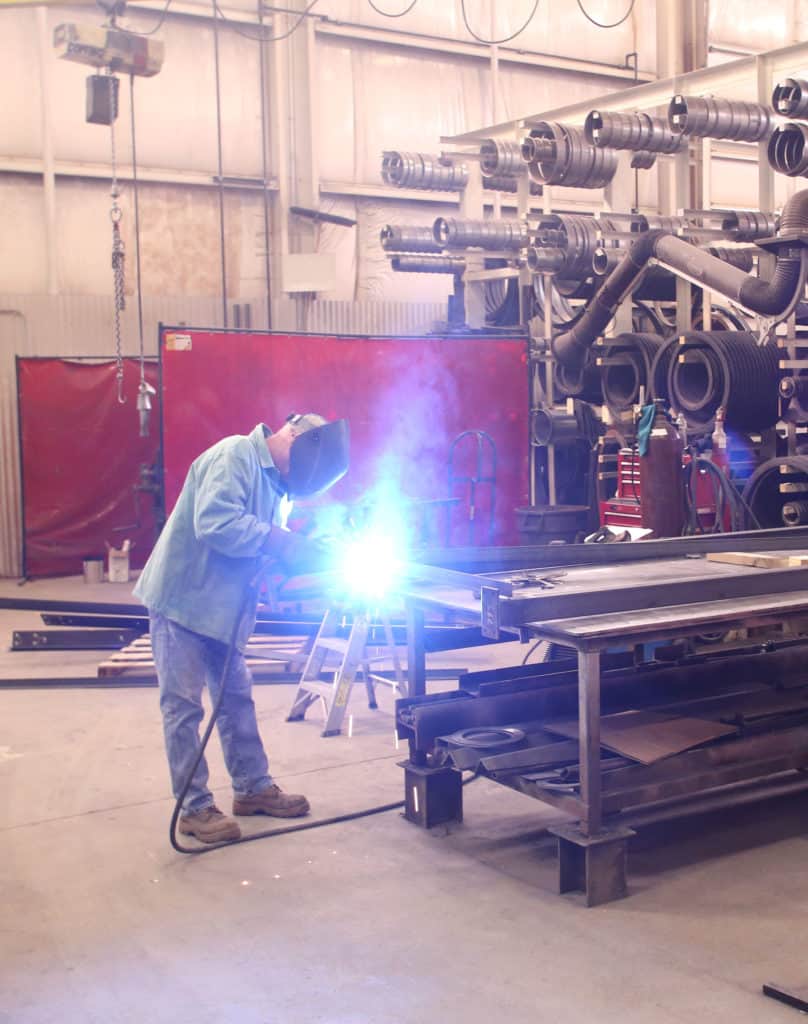
This company manufactures many types of metal parts for the power grid industry. They have several robotic weld cells and also a number of human welders. Between these two sources, the company produced a large amount of weld fumes. High production demand meant that the weld fume levels were a constant problem.
The company had a small fan moving air through the shop. Without proper welding ventilation, the fumes created a hazardous atmosphere in the workplace. Concerned about the safety of their workers, the company sought a solution to their weld fume problem.
Solution:
The company’s welding equipment dealer had worked with a company called Glacier Technology, Inc. The company contacted Glacier to design a welding ventilation system for their shop. The weld fume collector was an Imperial Systems CMAXX CM008. They laid out ductwork to provide direct ventilation to each area of the workplace.
The robotic weld cells had their own fume extraction hoods. In addition, an ambient system design provided clean air to the area where the human welders worked. Calibrating airflow to handle hoods and an ambient system together requires strong system knowledge.
The CMAXX arrived on time and as specified. Because the CMAXX is designed to be easy to install, the company was able to do the entire installation themselves. This took only one eight-hour work day and went smoothly.
Feedback:
Tom from Glacier Technology returned to the facility soon after install to adjust the electrical systems. Upon arrival, workers expressed how pleased they were with the new welding ventilation system.
“It took about five minutes to start clearing the shop out,” one worker told him.
In fact, when Tom had to shut down the collector for a few minutes to make some adjustments, the shop immediately filled with fumes. The workers demanded that he turn it back on as soon as possible. As soon as he restarted the system, the fumes began to clear again.
The customer reports that they had a very positive experience working with Glacier Technology and Imperial Systems. They appreciated the design of the system, the prompt delivery and easy install, and the customer service they received.
Imperial Systems and Glacier Technology partner to provide customers with the best equipment, efficiency, and expert service.
Read more
by Erin Long | Apr 2, 2019 | Weld Fume
About the School and Their Challenge
Located in northern Texas, the Community College offers comprehensive two-year educational programs – including a welding technology program. The school offers Associate of Art, Associate of Science, and Associate of Applied Science Degrees. The Welding Technology Program was interested in more cost-effective cartridge filters for welding fume in their Lincoln Statiflex 6000 dust collector.
Solution: DeltaMAXX Filters for Welding Fume
An Imperial Systems aftermarket member was making daily cold calls to businesses in the industrial realm. They struck a sale with the community college while talking with the instructor of the Welding Technology Program. The aftermarket member learned that the school was shopping around for replacement dust collector cartridge filters for the upcoming school year. Due to the budget, it was a top priority that the filters for welding fume were cost-effective and reliable.
After reviewing the DeltaMAXX filter literature and cross-referencing the filters on Imperial System’s website, the welding technology instructor purchased four DeltaMAXX replacement cartridge filters for the upcoming school year.
Results Beyond Customer Expectations
After running the filters in the dust collector for the fall semester, the welding school instructor was “really impressed” with the DeltaMAXX Replacement Dust Collector Filters.
“The System is running very smooth, not much back blow. When turning on the dust collector in the past we have had problems with smoke blowing out of the back. That problem went away when we installed the DeltaMAXX filters”, said the Texas welding school instructor.
“Imperial Systems’ dust collector filters for welding fume are very durable and they are lasting much longer for us. My expectations were exceeded and you can count on us to be a returning customer.”
Learn more about how Imperial Systems can provide better performing, long-lasting replacement cartridge filters for your existing dust collector. Contact us today.
Read more