by Greg | Aug 5, 2014 | Case Studies
Imperial Helps a Large Recycling Paper Mill become NFPA compliant while creating a safer work environment.
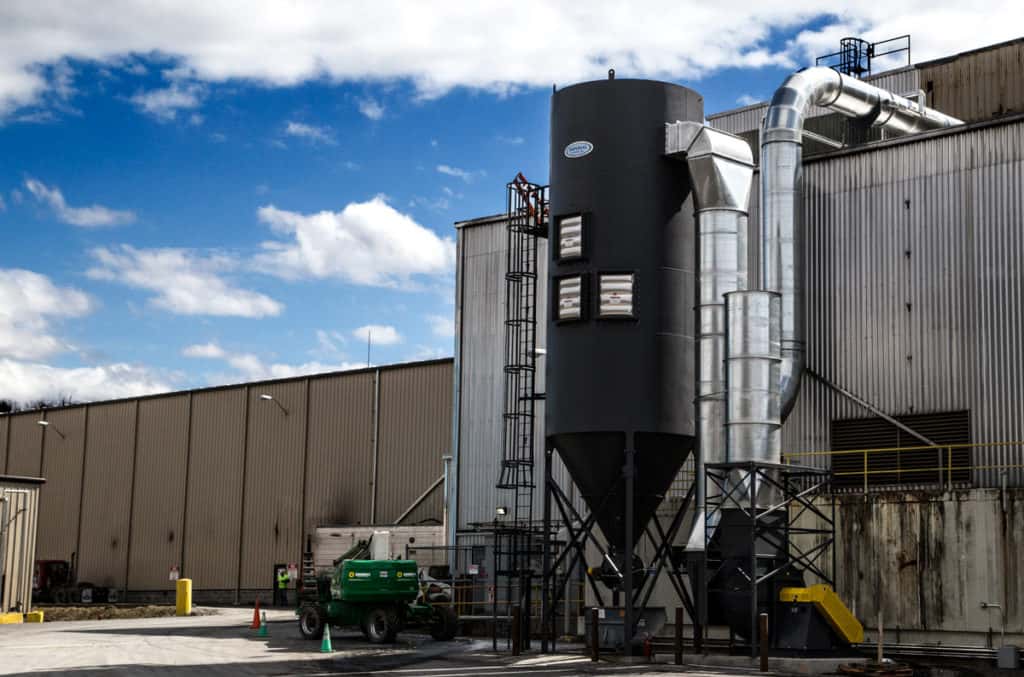
About the Company:
As a global leader in the forest products industry. The company owns and operates nearly 40 pulp and paper mills and wood product facilities in the United States, Canada, and South Korea.
The company makes and supplies leading publishers globally with top quality commercial printing paper and newsprint for magazines as well as direct mail, instruction manuals, maps, flyers, etc.
Not only does the company also produces 1.7 million metric tons of market pulp at seven different facilities in North America, they are also a major producer of lumber and other wood products for residential-construction and home-renovation markets.
This particular case takes place at one of the North American plants located in West Virginia.
Challenge:
The West Virginia located recycling paper mill is one of the largest in the USA. Production hours at the shop are virtually non-stop, running 24 hours a day and 365 days a year.
Though the wood dust is not toxic, the company was having trouble becoming NFPA compliant and the employees were dealing with plenty of extreme health, safety, and fire hazards including: airborne dust coming off the belt conveyers and constantly floating in the air, and up to 7 inches of dust collecting on the machines weekly – creating tremendous fire hazards.
The only safety measure to this point were employee dust masks.
“We were capturing 400-500 pounds of dust weekly, it was a huge problem,” says one plant manager.
The dust was getting bad enough that the employees were having respiratory infections as well as eye infections.
It was time to make a change.
Solution:
In January of 2014, while searching the internet for dust control solutions, the large recycling paper mill stumbled upon Imperial Systems, Inc. Because of Imperials’ great values as a family owned company, as well as being a true one source company, it was an easy decision for the recycling mill to go with Imperial.
“Imperial was a one-stop-shop and we really valued that when bidding out the job. Imperial took care of the entire process from the drawings, to the engineering, to the fabrication, and clear through installation. The communication between us and them was always thorough”, said plant manager G. Thomas.
The company purchased a Reverse-Air Baghouse Dust Collector and over half a million dollars in ductwork from Imperial Systems. The development and install process began at the end of January and the entire project was up and running by March of 2014.
According to plant manager G. Thomas, who supervised the entire project, the Imperial Systems’ installation team was not only extremely knowledgeable and efficient, but they were also extremely respectful, helpful, and easy to work with.
“The install crew was a pleasure to work with, the whole process was a pleasure actually. Imperial was very easy to work with, there was no lack of communication, and I know if I need something in the future, I can call-in and somebody from Imperial will be here as soon as possible.”
To this day, the West Virginia paper recycling mill has had no problems with their dust collector purchased form Imperial Systems. Since becoming NFPA compliant, the shop has been cleaned up tremendously. There is minimal to no wood dust in the shop creating a much healthier and fire resistant environment and operations are running at a much smoother pace.
About Imperial Systems:
Located just north of Pittsburgh, Pennsylvania in the small town of Jackson Center, Imperial Systems is among the top dust collection equipment manufacturing businesses in North America. Our values are built on designing and installing custom industrial dust collection systems with the strongest, most durable, fabrication to meet our customer’s needs.
Read more
by Greg | Apr 21, 2014 | Case Studies
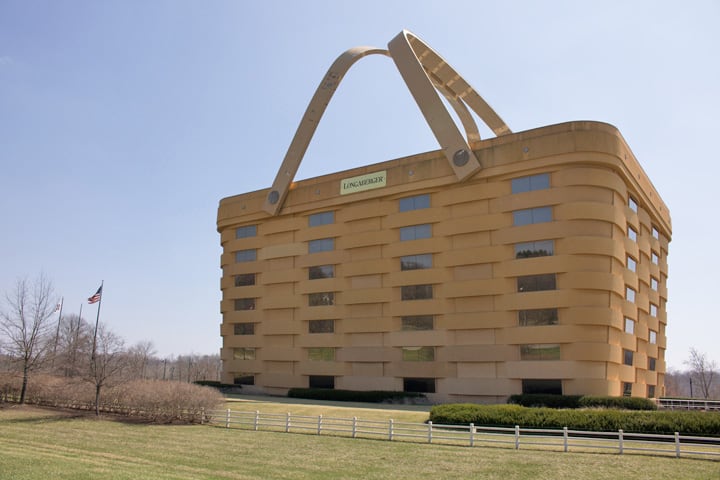
About the Company:
The Longaberger Company is a globally renowned manufacturer of handcrafted maple wood baskets and offers other home and lifestyle products, including pottery, wrought iron, fabric accessories, and specialty foods. Located in the heart of Ohio, it is a primary employer in the local area.
The company distributes their products to approximately 45,000 independent consultants located throughout the U.S.A.
The Longaberger corporate headquarters is a well-known landmark and a brilliant example of novelty architecture. Longaberger HQ is uniquely shaped as the basket product that the company is nationally recognized for.
Challenge:
Due to the decline in economy value, the Longaberger Company had just sold one of their bigger buildings to move across the industrial park into one of their smaller facilities.
The Duct and fitting on the building was roughly ten years old, so it was time for a modification project. The goal was to find a company with expert engineers that could help with cutting cost, efficiency, and manufacturing the desired ductwork.
After hearing about what Imperial Systems had to offer from the staff at an Air Systems plant in Indiana, the Longaberger Company decided to reach out to Jeremiah Wann (president/CEO) at Imperial Systems to discuss the upcoming duct and fitting installation.
The Longaberger Company decided to go with Imperial Systems because of cost and what the company had to offer as far as design, layout, and their expert knowledge as a complete systems manufacturer.
Solution:
The duct and fitting installation process began in January of 2014 and was separated into two phases. During the first phase, the Imperial Systems installation crew came and moved the existing cartridge collector and BRF to the new, down-sized, location. The second phase consisted of installing the duct and fittings.
“Imperial did a great job at looking at what our needs were and solving the issues that we had in the past. They helped us move from two big collectors down to one”, said Barry S., Longaberger plant mgr.
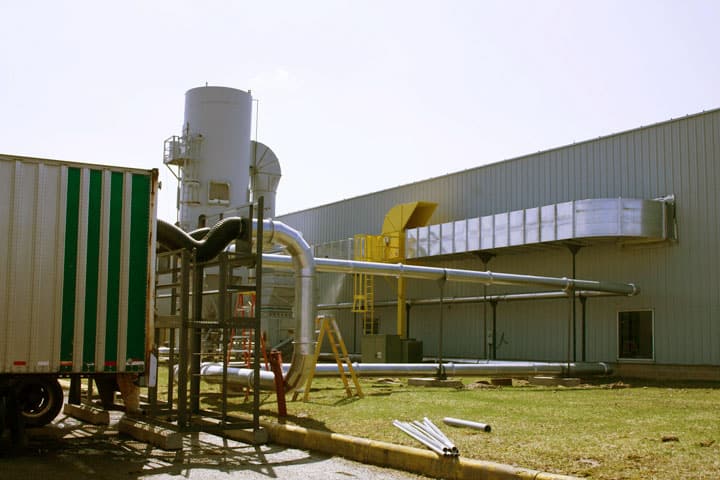
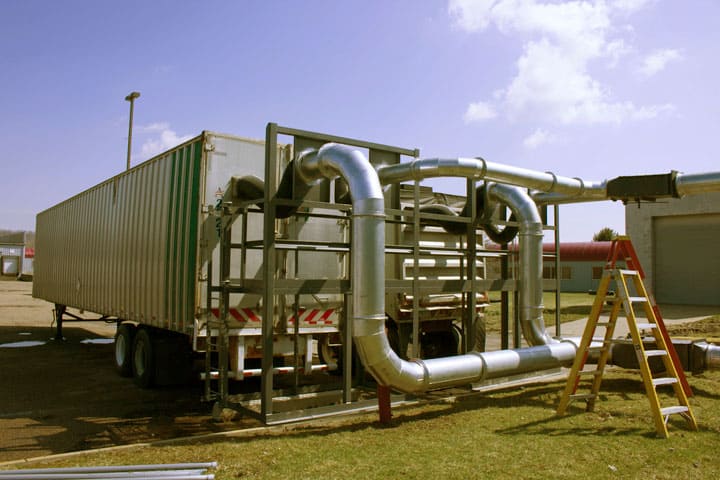
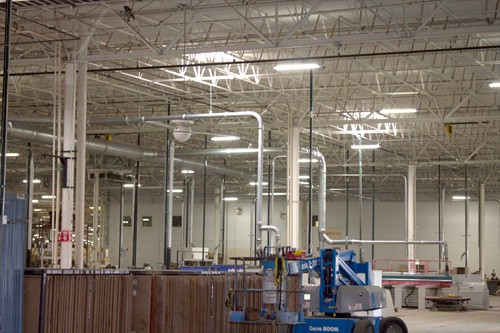
Read more
by Greg | Mar 31, 2014 | Case Studies
Located in northern Pennsylvania along the shores of Lake Erie, this company specializes in hard chrome and electroless nickel plating as well as polishing of molds, tools, and dies.
Challenge:
The company manufactures five days a week for 16 hours each day. Not only would the companies dust collectors pull in blasting materials, but they would also pull in an oily film that would foul the cartridge filters on a regular basis. As a result, the company would have to change their dust collector system’s filters at least three times a year. The goal for this company was to find a cartridge filter that would successfully defend against this material while also staying within the company’s budget.
Solution:
After doing a cold call to this company, the Imperial System’s aftermarket rep was able to land the company’s business.
“Imperial Systems reached out to me and recommended their Deltamaxx filters that have a nanofiber media and wow what a difference they made. Now we have filters in our dust collectors that last 4 times longer. Also, our cost in filters and down time are at their lowest”, said Scott G., a company representative.
Scott then went on to say, “I have been changing filters here in our plant for over 20 years and I wish I would have known about Deltamaxx filters years ago. I have a system here that I would change at least three times a year. Since we put the Deltamaxx filters in our dust collectors, I have not changed it yet and it’s been over a year. We run two shifts {8 hours} a day for 5 days a week. Thank you Imperial System for recommending the Deltamaxx nanofiber cartridge filters.”
Thank you Scott!
Read more
by Greg | Mar 17, 2014 | Case Studies
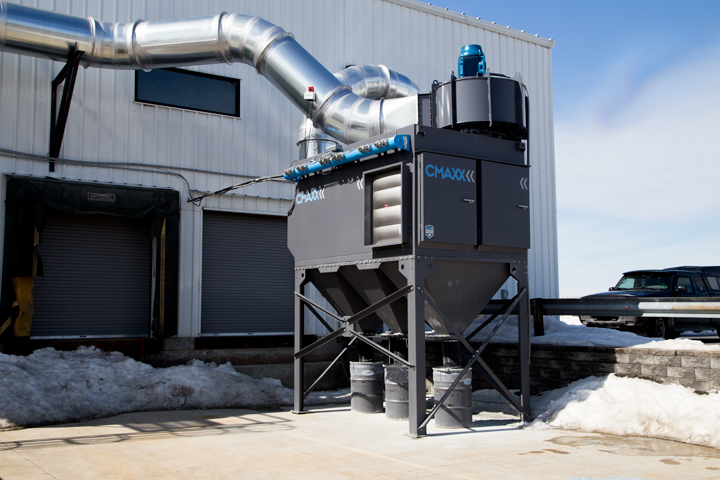
Located in the heart of central Pennsylvania, this fiberglass pultrusion manufacturing plant is one of the most established United States manufacturing companies. Founded in 1974, this fiberglass construction manufacturer is a global distributor specialized in replacing old steel, wood, and aluminum structures with lighter, sturdier, fiberglass reinforced plastic construction. Whether it is reinforcing the underwater structures of the fountains at the Bellagio Hotel and Casino, or protecting the many steel pipes inside the Hoover Dam; fiberglass pultrusion manufacturing has become a mainstay in the manufacturing industry and this company is at the top of it.
Challenge:
The company manufactures seven days a week and 24 hours a day. As a company that works all hours of the clock and uses many applications including CNC, Sanding, Blasting, and chop saws, an industrial dust collection system was more than necessary.
The combination of around the clock manufacturing with a variety of dust and fume producing applications had caused an enormous amount of dust build up in the manufacturing shop. Not only is the created dust and fume a fire hazard, but it is also a concerning health hazard for the company’s employees.
Solution:
After doing his research and ultimately finding Imperial Systems on a Google search for industrial dust collectors. Tom F., decided to purchase a CMAXX CM-024 dust collection system from Imperial Systems.
“I decided to do business with Imperial Systems because I liked the craftsmanship and quality of the dust collector systems that Imperial Systems manufacture.” said Tom
Since Imperial has a true systems background, which sets them apart from all of their competitors, the company was able to move quickly with the dust collector system installation. From the conceptual state, through quoting and design, and finally on through the installation, Imperial Systems was able to take care of anything and everything that had to do with the CMAXX- 024 dust collection system.
To this day, the system is running smoothly; according to Tom, things could not be better in the manufacturing shop. As a return customer for Imperial Systems, the company purchases Imperial’s own DeltaMAXX Replacement Cartridge Filters for their CMAXX Model.
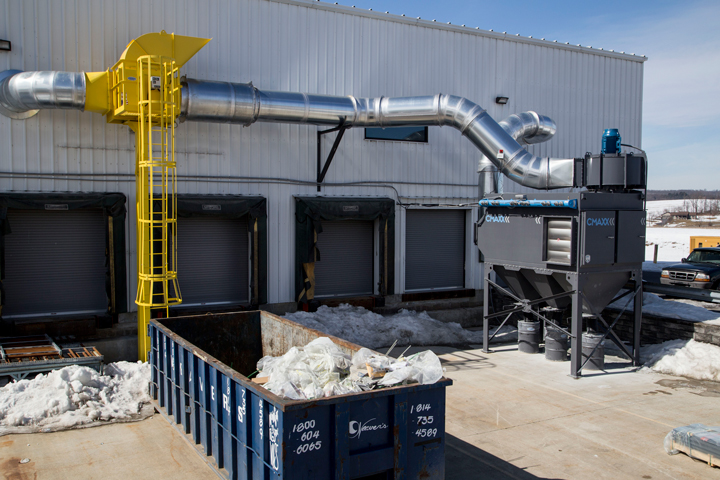
Read more
by Greg | Dec 16, 2013 | Case Studies
DeltaMAXX Dust Collector Cartridge Filters Exceed Expectations at Welding Technology Program – Texas Community College
About The School: Located in northern Texas, the Community College offers comprehensive two-year educational programs – including welding technology. The school offers Associate of Art, Associate of Science, and Associate of Applied Science Degrees.
Challenge: The Welding Technology Program was interested in more cost effective cartridge filters for their Lincoln Statiflex 6000 dust collector.
Solution: In the summer of 2013, while making daily cold calls to businesses in the industrial realm, the Imperial Systems aftermarket member was able to strike a sale with the community college. While talking with the instructor of the Welding Technology Program, the aftermarket member found out that the school was shopping around for replacement dust collector cartridge filters for the upcoming school year. Due to the budget, it was a top priority that the filters were cost effective and reliable.
After reviewing the DeltaMAXX filter literature and cross-referencing the filters on Imperial System’s website, the welding technology instructor pulled the trigger and purchased four DeltaMAXX Replacement Cartridge filters for the upcoming school year.
Outcome: After running the filters in the dust collector for the fall semester, the welding school instructor was “really impressed” with the DeltaMAXX Replacement Dust Collector Filters.
“The System is running very smooth, not much back blow. When turning on the dust collector in the past we have had problems with smoke blowing out of the back. That problem went away when we installed the DeltaMAXX filters”, said the Texas welding school instructor.
“Imperial Systems’ dust collector filters are very durable and they are lasting much longer for us. My expectations were exceeded and you can count on us to be a returning customer.”
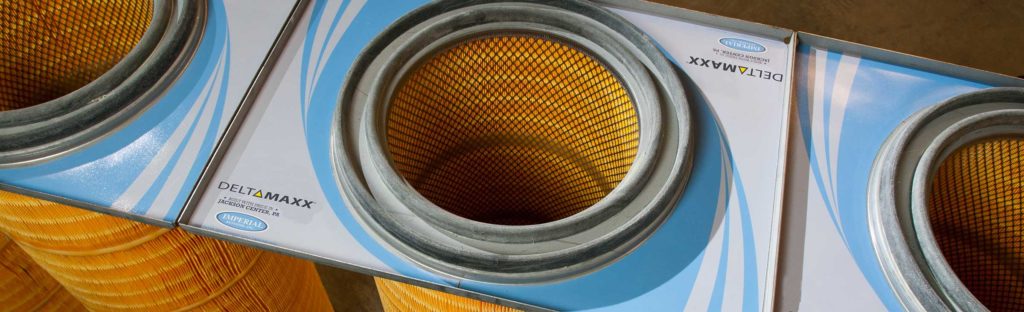
Read more
by Greg | Nov 8, 2013 | Woodworking
Imperial Systems’ BRF Replaces Leading Competitors at a Popular Woodworking Facility
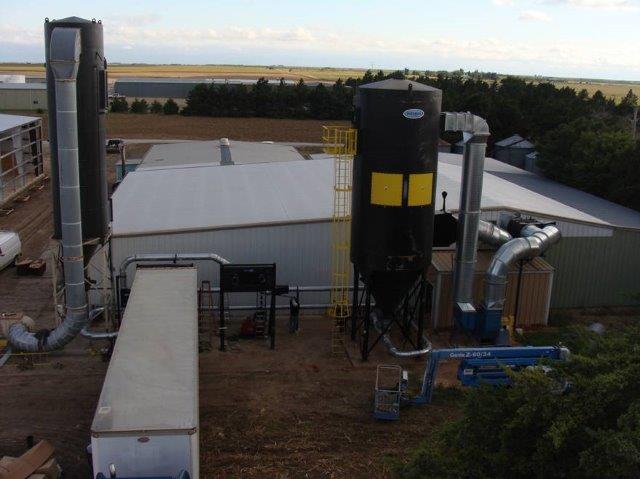
About the company:
A mid-market woodworking company that manufactures and distributes custom cabinets across the USA. The company uses a variety of tools such as: CNC turning equipment, table saws, planers, shapers, radial arm saws, jointers, and more.
Challenge:
In 2006, the company had purchased a 32-cartridge dust collector from a leading cartridge collector equipment manufacturer. Just a week after installation, the cartridge filters were plugging. The company tried to resolve the issue by using over bags and constant compressed air pulsing but nothing was working. The problem created serious downtime, constant maintenance on the cartridges, and excessive use of expensive compressed air. In the end, the problem was bad enough that the 32 cartridge collector was purchased back by the manufacturer and Westwind decided to head in another direction.
Solution:
Imperial Systems’ BRF cylindrical baghouse was chosen due to its forgiving design and its special characteristics built around the woodworking industry. The woodworking facility was impressed enough by Imperial Systems knowledge that they turned to Imperial later that year to purchase another system from them. By May of 2008, the 30,000 CFM BRF was officially installed. To this day, the BRF is still running extremely well and has relieved the company from their prior concerns.
“When considering wood dust extraction systems for any fibrous material, it is very important to consider dealing with a dust collection company that builds both bag style and cartridge style dust collectors. It is way too easy for a company that only builds one style to try and force it in all applications. This is just one of many stories where we have seen this unfortunate thing happen”, says Jeremiah Wann, President of Imperial Systems.
See also: Selecting an Industrial Dust Collector for Woodworking?
Read more