by Imperial Systems | Jul 29, 2016 | Common Industrial Dust Collection System Problems, Uncategorized
Dust and Fume Collection: Some Industries That Might Not Know They Need It
Dust and fume collection in a manufacturing facility is important for many reasons. Here are the top five reasons you should consider:
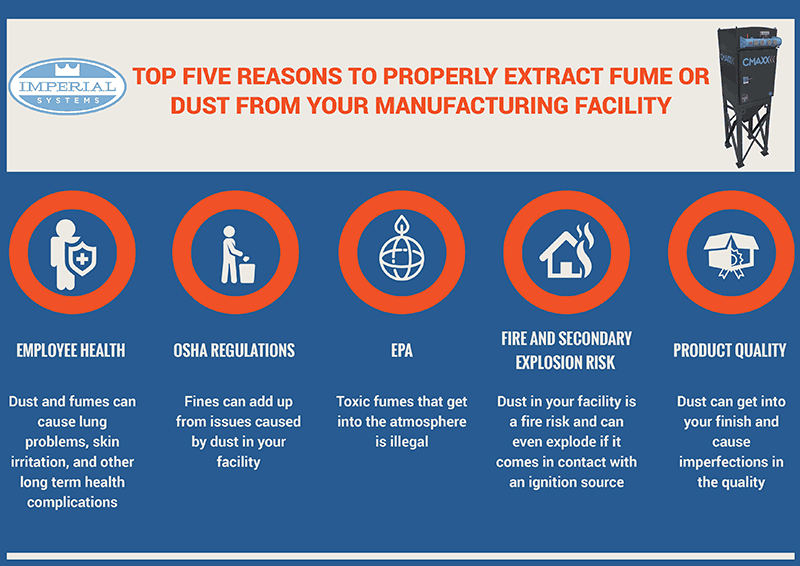
Not Convinced Yet?
Can you name the metal that causes cancer, damages skin, eyes, lungs, and kidneys, and is found in everything from stainless steel to dyes and pigments?
If you said this compound is Hexavalent Chromium (https://www.osha.gov/SLTC/hexavalentchromium/), you’re right.
Chromium is a component of stainless steel, added to make the steel more corrosion-resistant. Consequently, the fumes produced from welding, laser cutting, or plasma cutting stainless steel contain hexavalent chromium. While this form of chromium is known to cause cancer, it also directly attacks the lungs and kidneys and can cause severe eye and skin irritation.
Further, hexavalent chromium doesn’t just appear in welded or heated stainless steel. Electroplating with chrome also presents a hazard, and hexavalent chromium compounds are used as pigments in inks, paints, and many types of plastic. In fact, working on any material plated with chrome or coated with a chromium-containing material may release hexavalent chromium into the air.
Think hexavalent chromium isn’t something to worry about in your type of business? You certainly may need to reconsider. That’s because OSHA testing showed which types of facilities had detectable levels of this dangerous metal in their air. The following are some of the top offenders:
- Nonresidential building
- Highway, street, and bridge
- Foundation and structural materials
- Foundries
- Forging and stamping
- Architectural and structural metals
- Boiler, tank, and container
- Coating
- Engraving
- Heat-treating
- Agricultural machinery
- Mining machinery
- Ventilation and air-conditioning
- Aerospace products and parts
- Ship and boat building
- Automotive repair and maintenance
Any surprises on this list? If your facility is part of any of these industries, contact us at 800-918-3013 for an assessment of your dust and fume collection needs.
Related blog posts:
Read more
by Imperial Systems | May 5, 2016 | Common Industrial Dust Collection System Problems
Within the metalworking industry, the demands for diverse material coatings are on the rise, and the development of application processes that address environmental concerns is an ever-growing field. Thermal spraying provides an attractive coating technique because it offers a wide selection of materials that have a reduced environmental impact as compared to conventional methods. Imperial Systems meets today’s top market needs by offering solutions that address problems from plasma, flame wire, flame powder, warm spraying, and cold spraying. We commit to helping you better prepare and protect your facility as your processes evolve and expand.
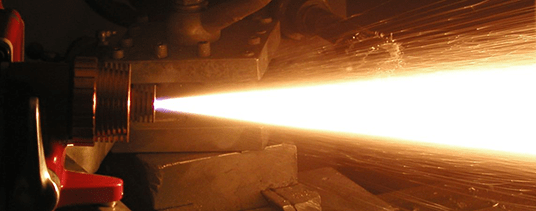
There are advantages to thermal spray coating techniques because they tackle the many problems of wear, corrosion and thermal degradation by engineering surfaces with customized coatings. Thermal spraying offers greater thickness capacity than traditional surface modification processes with minimal hazardous waste and no size restriction for parts.
High velocity oxy-fuel (HVOF) spraying is a thermal spray system based on the combustion of gases or a liquid fuel. The resulting high velocity propels the coating particles at near supersonic speeds before impact onto the surface, which generates high coating quality. One of the key benefits of this system’s high velocity is the extremely high coating density and low oxide content.
Cold spraying is an emerging form of High Velocity Oxygen Fuel (HVOF) technology intended as a greener alternative that will satisfy increasingly rigorous environmental and health safety regulations. A number of materials have already proven to be suitable for cold spray including decorative, biomedical, automotive, industrial, and space exploration materials. The cold spraying process has huge potential of growth with more applications in new areas developing constantly.
Cold spraying need not be a dangerous process if the equipment is treated with care, and if correct spraying practices are followed. Ideally, equipment should operate automatically in enclosures specially engineered to extract fumes, reduce noise levels, and prevent direct contact with the spraying head. In addition, OSHA recommends that every metalworking facility be fitted with the appropriate dust and fume extraction system to reduce the risks associated with such processes, such as exposure to air pollutants and combustion susceptibility.
The Imperial Systems CMAXXTM Dust Collector System is specially designed with PD technology that allows for maximum Indoor Environmental Quality (IEQ) in your facility. Some of its features and benefits include:
- Increased cleaning power and energy efficiency with high-performance manifold mounted pulse valves.
- 10% More filter media than other same-sized vertical cartridge collectors.
- Vertical cartridge design for a longer filter life.
- 100% Total pulse distribution.
- Best in class internal velocities.
- 15 Year manufacturer warranty
At Imperial Systems, we know the hazards that metalworkers face each day, and we continue to reach above and beyond the safety standards set by OSHA and the NFPA. If you’re looking for equipment that offers real solutions, delivers the cleanest air and provides you with the greatest cost savings, then contact Imperial Systems today at 800-918-3013. We’ll match your facility with dust collectors and filters that will improve your facility’s readiness for cold spraying, and any other new metalworking technology developments that may come along!
Read more
by Imperial Systems | May 4, 2016 | Common Industrial Dust Collection System Problems, Uncategorized
The metalworking industry is compromised many different aspects of metal fabrication encompassing welding, thermal spraying, sanding and shot blasting, and plasma cutting. Thermal spraying is is used for repairing damaged surfaces, temperature/oxidation protection, corrosion protection, crankshaft reconditioning and conditioning, and altering thermal conductivity. The process of thermal spraying comes in many applications from cold spraying, plasma spraying, wide arc spraying, high velocity oxygen fuel spraying, and warm spraying. While there may be variations in the applications of thermal spraying they all have similar risks.
Because the process of thermal spraying involves the atomization of molten metals, this produces large amounts of combustible dust and toxic fumes according to the publication of the Fabricators & Manufacturers Association, Intl. Other dangers involved with warm spraying are the fine metal particles that are possibly pyrophoric and can be very harmful when accumulated in the body, and the constant inhalation of highly toxic metal dust particles. The constant exposure to these fumes and vapors can produce serious respiratory diseases such as a coughs, pulmonary edema, asthma, or contact dermatitis. Some metals that are used such as nickel, chromium, or cobalt are considered to be potentially carcinogenic to humans.
In order to avoid or limit any of these hazards, there are certains standards and guidelines set by the Occupational Safety and Health Administration. Safety being the priority, OSHA suggests your metalworking facility be fitted with the appropriate dust and fume extraction system to avoid any explosions and reduce metal fabricators exposure to metal air pollutants.
The Solution to Thermal Spraying Hazards
Imperial Systems CMAXX™ Dust Collector System can provide your metalworking facility with the protection it needs because our dust collector systems are designed for our DeltaMAXX™ Replacement Cartridge Filters. Our DeltaMAXX™ Replacement Cartridge Filters have the longest filter lifer, provide you with a greater cost in savings, and the cleanest air for your facility. Here are more outstanding features the CMAXX™ Dust Collector System can provide for your metal facility:
- Vertical cartridge design for a longer filter life.
- 100% Total pulse distribution.
- Best in class internal velocities.
- Increased cleaning power with an energy efficient and high-performance manifold mounted pulse valves.
- 15 Year manufacturer warranty
- 10% More filter media than other same-sized vertical cartridge collectors.
At Imperial Systems, we know the hazards that metalworkers face each day, and we continue to go above and beyond the standards set by OSHA and the NFPA.
Contact us today, and let us help you get fitted with the CMAXX™ Dust Collector System to combat the hazards of thermal spraying.
Read more
by Imperial Systems | Mar 16, 2016 | Common Industrial Dust Collection System Problems
Don’t choose sub-standard sheet metal duct fittings for your metalworking business. Save time and money by choosing Imperial Systems.
When the company first began back in 2001, Imperial Systems was strictly a fabricator of custom sheet metal duct fittings. Although Imperial Systems is now considered a manufacturer of industrial dust collectors, we are also still experts in custom duct and fitting jobs. Our pride in developing custom sheet metal duct fittings has always remained intact as we feel we are the best and most experienced in the industry with these custom jobs.
Why Choose Imperial For Custom Sheet Metal Duct Fittings?
Paired with our outstanding customer service, we manufacture only the highest quality products that are reliable, durable, and guaranteed to last. Below are a few reasons why you should consider replacing your current duct and fittings with Imperial Systems:
- Your current sheet metal duct fittings are in disrepair. Don’t let dust and fumes escape, causing your employees to be sick. Even more serious is the risk of combustion in the workplace.
- You’ve noticed your employees getting sick more often. The cause may be leaky ducts and fittings. Look into replacing your current system with Imperial Systems’ trusted products.
- Poor customer service. If you find that your current provider for sheet metal duct fittings is lacking in quality customer service, find out why Imperial Systems maintains trustworthy business relationships with our clients.
- Your system is outdated. With an updated system regulated by OSHA and NFPA standards, you can save time and money. You may also reduce a risk of an accident or hazard.
We are often called upon to take jobs focused on ducting and sheet metal in addition to the dust collection systems we are best known for. Our standard of quality applies not only to dust collection but to the sheet metal duct fittings that enhance your current system so you know you’re in good hands.
When making a purchase decision in the metalworking industry, you must take into consideration both the quality of the product being purchased as well as the effectiveness and safety for the end-user–your employees. Today’s advances in dust collection systems have lessened replacement costs and injury or death due to faulty equipment.
Ready for Sheet Metal Duct Fitting Solutions From Imperial?
Don’t let your employees risk their health due to the fine dust particles that is a common byproduct in the metalworking industry. Keep your employees healthy and your environment safe with our quality sheet metal duct design work. Our ducts and fittings can be added to any current system you have, or we can replace your system with one of our highly demanded CMAXX™ Dust Collector Systems.
If you’d like to request a quote or schedule an assessment based on your needs for a hardworking, high-quality sheet metal duct fitting which is both OSHA and NFPA regulated, get in touch with us today at 724.662.2801 or by finding out more about us.
At Imperial Systems, we specialize in advanced safety solutions you can count on.
Read more
by Imperial Systems | Jan 7, 2016 | Common Industrial Dust Collection System Problems
Delaying your decision to install a dust collector spark arrestor may cost you. We can help you reduce the risk.
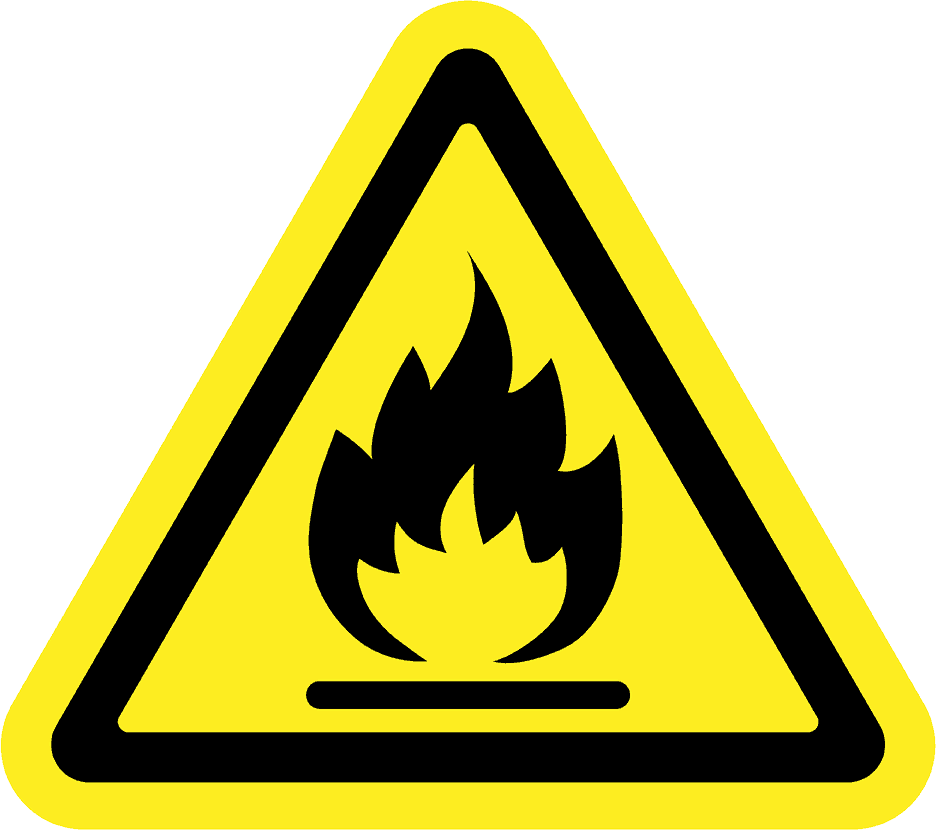
How much is your procrastination costing you? In some industries, putting decisions or actions off for a later date can have negative, if relatively mild, consequences. For instance, you’ll miss a deadline or lose an opportunity. You also may even disappoint a client or partner. While these consequences may be difficult for those having to deal with them, they pale in the face of the cost of procrastination within the metalworking industry. We’re talking about your dust collector spark arrestor here.
Unlike other businesses, your metalworking company is a high-stakes situation every single day. Specifically, you have the potentially explosive combination of combustible dust and sparks flying. So, it’s imperative that you act immediately to implement all of the required and recommended safety equipment. This certainly includes dust collection systems with sealed ductwork and an effective spark arrestor.
Of course, each of these pieces of equipment represents a major investment for your business. Therefore, it is important to do your homework and decide which one is the best fit for your business. However, letting that pending decision intimidate or hold you could be a serious hazard.
In this post, we will lead you through:
- Understanding the Risks of Combustible Dust and Sparks
- The Role of a Dust Collector Spark Arrestor in Risk Prevention
- Features and Benefits of Imperial’s Spark Arrestor
Understanding The Risk of Combustible Dust and Sparks
In metalworking, it’s no secret that materials you work with daily can create a serious risk for combustion. In fact, metals make up 20% of the materials involved in combustible dust incidents. Further, between 2008 and 2012 the United States Chemical Safety Board documented 50 combustible dust accidents. These led to a total of 29 fatalities and 161 injuries.
Unfortunately, as of 2014, metals and manufacturing were among the top industries being cited by OSHA for combustible dust, flammable dust, and other explosible dust hazards. This tells us that, although the risk is clear, it may not be clearly understood by those in the industry.
Five simple elements will cause combustion to occur:
- Heat
- Fuel
- Oxygen
- Dispersion
- Confinement
With each of these factors occurring effortlessly within most metalworking shops, tragedy lurks only a moment away. This is why, in 2006, the US Chemical Safety Board recommended a comprehensive combustible dust regulatory standard for all industries be added atop the initial regulations, which were developed in the grain industry in 1987.
Clearly, the risks are both real and nearly ubiquitous. All within the affected industries must take them seriously. One of the best ways to do this is to evaluate your workspace and ensure that it has all of the equipment necessary to meet OSHA, NFPA, and other regulations. Additionally, you should regularly evaluate your equipment to ensure that it is in good working order.
The Role of A Dust Collector Spark Arrestor in Risk Prevention
At its most basic, the role of a spark arrestor is to prevent the emission of flammable materials from combustion. Sparks, in various forms, are the major cause of combustion in combustible dust accidents:
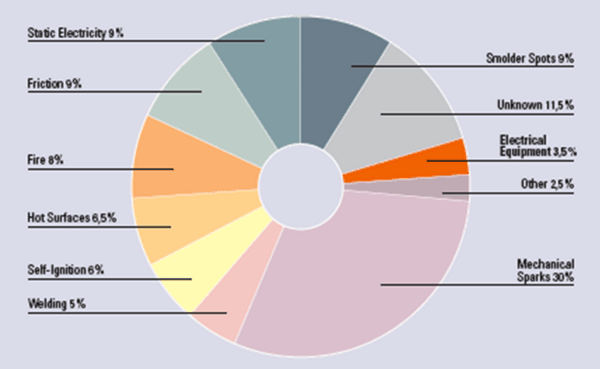
Because a spark is often carried along through the exhaust gas stream, it has not cooled from its temperature of 600 degrees Fahrenheit by the time it arrives at the solids separator. At this point, it can be deposited onto the filter element surface, positioned as a glowing risk of combustion. The filter element surface is at high risk for combustion, no matter what material it is made of. This is because of its role in collecting tiny metal particles and dust that are produced by nearly every manufacturing and metalworking process. Even a simple spark is enough to insight disaster.
This is why OSHA’s ignition control recommendations regarding combustible dust include the following:
- Control smoking, open flames, and sparks
- Control mechanical sparks and friction
Use separator devices to remove foreign materials capable of igniting combustibles from process materials
- Separate heated surfaces from dusts
- Use an equipment preventive maintenance program.
OSHA’s injury and damage control methods also include:
- Separation of the hazard (isolate with distance)
- Segregation of the hazard (isolate with a barrier)
- Deflagration isolation/venting
- Specialized fire suppression systems
- Explosion protection systems
A Spark Arrestor is an instrumental part of these methods, working to minimize risk by cooling and thus extinguishing sparks before they reach the filter surface. In the diagram below, note how the hot spark enters the arrestor which both cools and collects debris, before allowing the cooled ember to pass through.
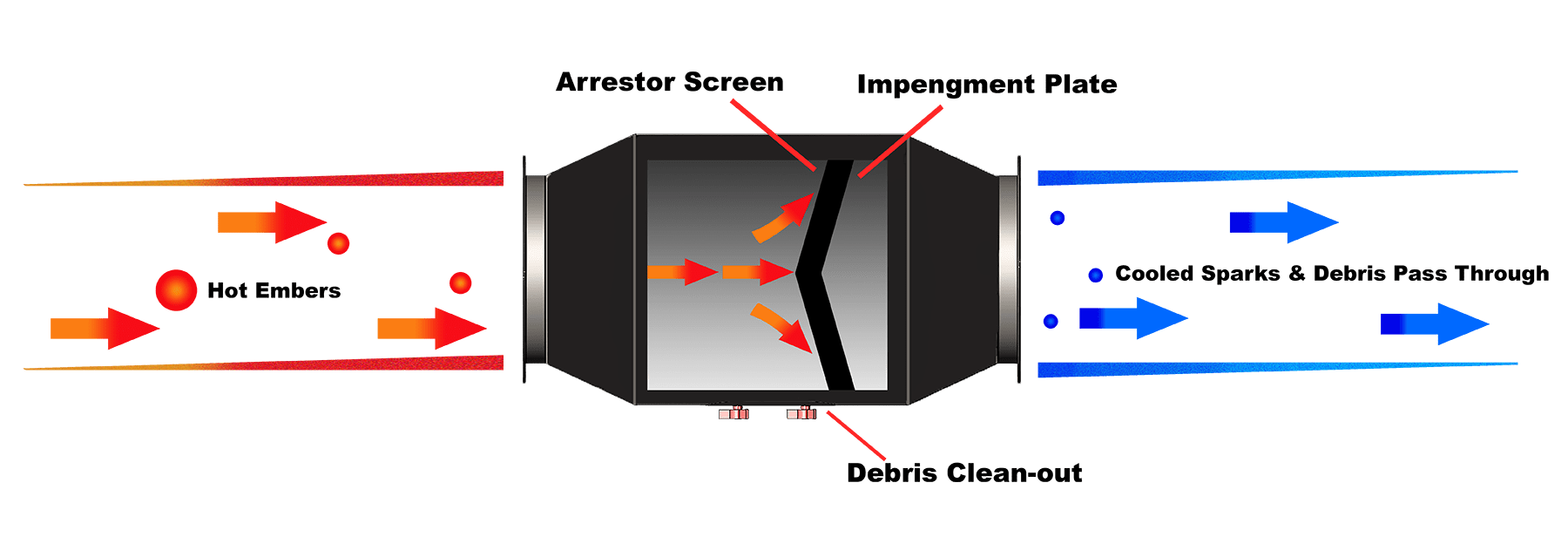
The spark arrestor fits within the full dust collection system as the first line of defense. They take up little or no extra space, but provide powerful results.
Features and Benefits of Imperial’s Spark Arrestor
At Imperial Systems, our highest priority is to provide the best solutions in dust collection and air pollution. We are determined to provide the best protection for your workers, your plant, and the environment. For over a decade, we have been serving metalworking businesses like yours all over the United States and Canada.
In an effort to provide fully comprehensive dust collection equipment, we have debuted our own spark arrestor named Spark Trap. It’s standard features include:
- Heavy duty construction
- No maintenance
- Clean-out door
- Fully welded construction
- Easy install into any system
- Can be installed in horizontal or vertical configurations
- No moving parts
- Carbon steel or stainless steel available
- No water required
- Available in sizes: 6 in. to 40 in.
Additionally, you can opt for raw inlet/outlet edges, rolled angle flange for bolt-together ducts, or clamp together for clamping duct.
As with all Imperial Systems’ products, you can count on the highest quality materials, top safety features, and unbeatable value.
The Cost of Procrastination
So back to our original question. If you haven’t yet decided on a spark extinguisher for your metalworking business, what is that procrastination costing you? Let’s take a look at the numbers:
From 1996-2005, 106 explosions resulted in 16 fatalities, 126 injuries, and an estimated cost of $162.8 million in damages to the facilities.
We know from previously cited studies that sparks are a major cause of such explosions. Will you absolutely face a combustible dust explosion if you put off your decision about a spark extinguisher? Perhaps not. But is it really worth the risk?
If you are ready to take the next step towards improving the safety of your workplace with a spark arrestor for your industrial dust collector, contact us today.
Read more
by Imperial Systems | Oct 8, 2015 | Common Industrial Dust Collection System Problems
Did you know that 30,000 US manufacturing facilities are considered at-risk for explosion by OSHA?
The Structure of a Dome: What’s to Like?
A domed roof design has been called “the king of all roofs”, and they support that name by covering many of the world’s most important and famous buildings. What is a dome? Domes have a curved structure, without corners, angles, or supporting columns. The design options for domes are many. You may see a dome on private homes, commercial buildings, or governmental and religious edifices.
Lightweight yet self-supporting, the dome provides a focal point and a natural attraction. In buildings, the airy dome structure creates an atmosphere evocative of pre-historic civilizations. Indeed, the dome’s deeply rooted origins in many cultures of the ancient world brings an air of richness and sophistication.
Design, quality and function combine to make this architectural structure a winner no matter where or what you’re building. And these observations hold true not just for buildings, but also for technology. What we refer to is industrial manufacturing. In many industries, the domed roof design has been shown to provide many benefits in the building. At Imperial Systems, we wanted to take the ingenuity of the domed system just one step further. For a quintessential dust collection system, we offer dust cartridge collectors with a superior domed roof design, providing industrial manufacturers with the many benefits of a long-lasting and safe instrument.
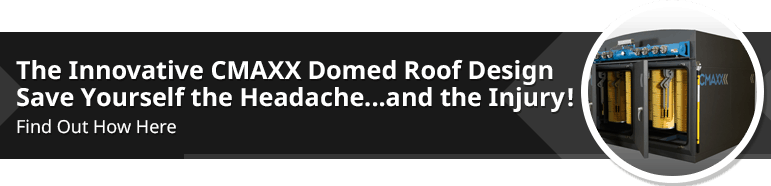
CMAXX Offer a Superior Domed Roof Design
CMAXX offers a superior domed roof design for cartridge dust collectors, providing a solid roof to increase efficiency. The roof on the CMAXX has a domed structure to make water run off and to improve the strength of the unit. These changes mean that the CMAXX is the only dust collector equipment that does not require external bolt holes. What does it include?
CMAXX domed roof design = NO bolt holds; NO individual panels; and NO roof seams!
How CMAXX Stays Ahead of the Competition
Industrial manufacturing requires instruments that can endure tough conditions, lasting for years and producing a high-quality material, all the while maintaining safety for those who use these instruments. That’s a tall order. At Imperial Systems we are interested in producing the best technologies, using scientific innovations as well as lessons from the past to create an equipment that will hold up to the pressures of your work. Safety equipment, such as cartridge dust collectors, must especially be designed to endure harsh environments.
Compared to the competition, the CMAXX domed structure excels in every way. If you research a similar unit without the domed roof design, you’ll discover a 16-cartridge dust collector with about 160 bolt holes and 1000 holes spaced throughout the collector. This design represents the old style of industrial fabrication, and the bolted panels hold water, leading to leaks and rusting and freezing. All these conditions signify damaged equipment for you.
But check out our the alternative!
Domed Roof Dust Collector Technology: A Challenge to the Status Quo
We know already that weather can be the most unpredictable and difficult element to control when it comes to producing safely and efficiently. At Imperial Systems, we’re not content to until we can provide you with the best for your manufacturing needs. The harsh external elements have resulted in warping, rust, leaks, and other problems for many metalworking and other industrial manufacturers. But your livelihood and the success of your business depends upon decreasing the instances of these types of problems. And the best way to eliminate the flaws in your production is to go back to its source: equipment.
The defects produced by your equipment can compromise the integrity of your unit. This undermines the safe environment you are seeking to create! Thus, we suggest that you confront these problems using a new and reformed dust collection system technology. We use four features to guarantee your protection against leaking and water damage.
- Positive Bow. The shape allows debris to run off more easily with water so that the unit becomes easier to clean. This inhibits pooled-up water from freezing on top of the unit, causing damage.
- One-piece Roof. Eliminating the individual-panel design, the one-piece roof offers a design that will be strong against leaking and warping.
- Zero Bolt Holes. The system is sealed because we have eliminated the external bolt holes altogether. Now, you can rest assured that you will not have to deal with rusty bolts, leaks, and breaking parts.
- A Strong Frame. The 3/16” roof is thick, fully welded, and the welds have been ground smooth. And, 1/4’” plate internal stiffeners offer the additional benefit of a reinforced structure.
What are the Biggest Threats to Dust Efficiency?
We believe that our domed dust collector structure presents a solution to the biggest challenges in the manufacturing business. The above-described features account for the major problems that will confront every industrial manufacturer: combustion, exposure, and pollution.
- Combustion. Fire explosion is a primary hazard that can only be avoided by preventing the build-up of dust particles. Employees should also be aware of the locations of the nearest fire extinguishers and the exit protocol in case of an emergency. While new OSHA guidelines have decreased the number of fires occurring in industrial plants in the U.S. it is estimated that there are still 30,000 facilities at risk for dust combustion.
- Exposure. According to the Vision Council, 61% of reported eye injuries occur in trade, manufacturing, and construction jobs. The eyes are exposed to chemical fumes, metal, dust, concrete, and other particles that can be injurious to the worker. Besides affecting the eyes, chemical exposure is also dangerous to the nervous, reproductive, and urinary systems. For these reasons, employees should always wear their personal protective equipment such as eye goggles and dust masks. A well-built dust collector decreases these risks by decreasing the amount of material that can exit the system.
- Pollution. When there is a high concentration of dust, smokes, and particles in the air, this affects the ability to breath. Inhalation of such particles can cause damage to the major organs and cause other health problems. Dust in particular can cause breathing problems, injuring the lungs and aggravating any health conditions the worker may already have. The presence of dust in the air is also a predictor of accidents, as the worker is less able to see in these environments.
Invest in Quality.
The domed roof design dust collector provides a one-piece structure that protects your workers against leakage and damage. With many risks at stake, it’s important to consider the best options for your company so that you can avoid being another explosion statistic! For more information or questions, please talk to us at Imperial Systems. We are available to help you decide the best dust collector for your current needs.
Read more