by Scott Stearns | Jul 2, 2018 | Uncategorized
Imperial Systems is one of the fastest growing and most respected Industrial Dust and Fume collection companies in North America. To supplement this growth, we welcome Tomm Frungillo to our leading group of sales professionals to help take this company to the next level.
Tomm comes to Imperial Systems Inc. from an extensive career in Industrial Dust and Fume Collection Equipment. Tomm most recently held the position of Director of Sales at The Systems Group and was charged with growing sales globally. Prior to The Systems Group he led many divisions of Camfil APC including Vice President of the Americas.
Prior to serving as Vice President Tomm led teams in charge of growing the Latin America mining market, creating the strategy and equipment for the pharmaceutical and biotechnology market, and growing the thermal spray market for the APC Division. With his 25 years of experience in the industry “We are looking forward to Tomm Joining us by bringing his skill and knowledge to take us to the next level” Says Jeremiah Wann, Owner/CEO Imperial Systems Inc.
Imperial Systems’ growing popularity stems from a reputation of producing the best Dust and Fume Collection Equipment which is backed by an industry-leading 15-year warranty. We believe that Tomm’s experience growing a company through focus on specific market segments will help Imperial Systems continue its path of profitable growth.
Read more
by Scott Stearns | Jun 25, 2018 | Uncategorized
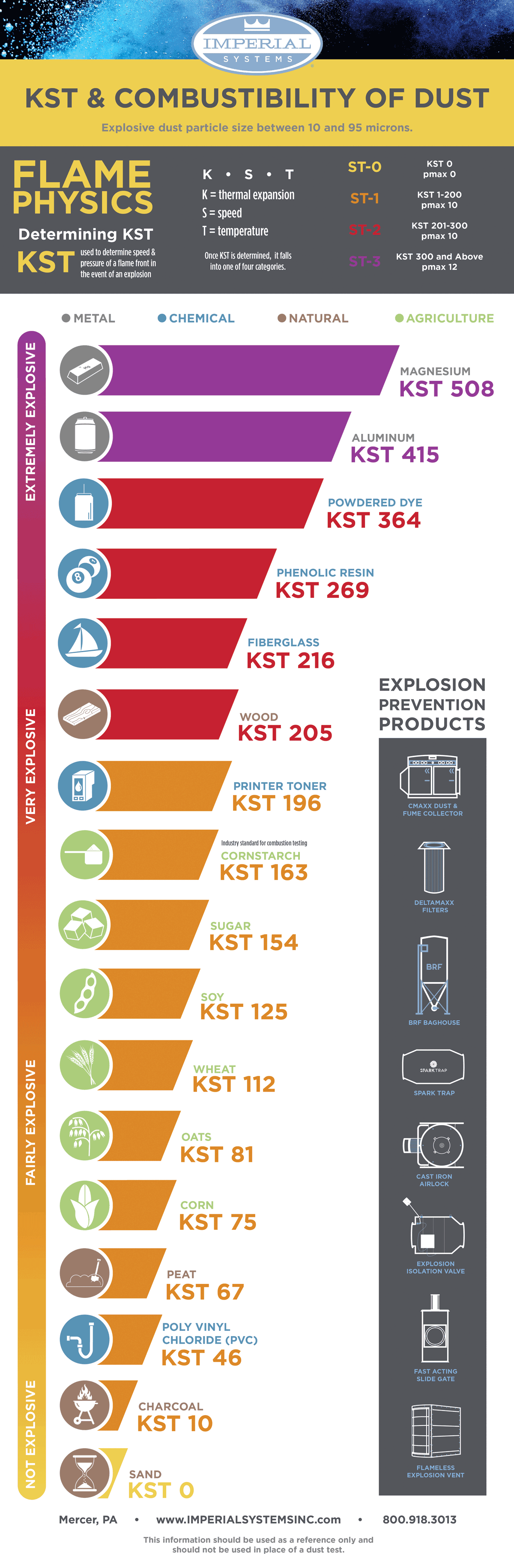
This infographic identifies the KST values of common metal, chemical, natural, and agricultural dusts found in manufacturing processes. KST is a general measurement of explosiveness and is a standard measurement for dust collection system design purposes. The explosive dust particle size range is between 10 and 95 microns.
Flame Physics
KST is used to determine the speed and pressure of a flame front in the event of an explosion. To calculate the KST values of these common dusts, thermal expansion (K), speed (S), and temperature (T) are used. Once KST is determined, it falls into one of four categories:
- ST-0: Kst 0, Pmax 10
- ST-1: Kst 1-200, Pmax 10
- ST-2: Kst 201-300, Pmax 10
- ST-3: Kst 300 and above, Pmax 12
Descending KST Values of Common Dusts
These common dusts are listed in decreasing order of their KST values. The higher the KST number, the more explosive the dust is. Note that Magnesium dust and Aluminum dust with KST values of 508 and 415, respectively, are extremely explosive. Whereas, Poly Vinyl Chloride (PVC) and Charcoal with KST values of 46 and 10, respectively, are not very explosive. For reference, Sand with a KST value of 0 is not explosive at all. Please note that this information should be used as a reference only and should not be used in place of a dust test.
Explosion Prevention Products
Imperial Systems offers dust collection systems and accessories that help prevent an explosion in your factory. The CMAXX dust and fume collector is certified as an In-Line Deflagration Arrester with DeltaMAXX IDA filters. It has been proven to isolate a deflagration and stop a flame front. We also offer the Spark Trap, an Explosion Isolation Valve, a fast-acting slide gate, and a flameless explosion vent. Our Cast Iron Rotary Airlocks and Rhino Drum explosion-tested drum kit can be used on the discharge of CMAXX or the BRF Baghouse dust collector.
Read more
by Scott Stearns | Jun 21, 2018 | Uncategorized
At Imperial Systems we’re very proud of our products and our company, and now they’re finally going to have the website they deserve! The new Imperial Systems website is expected to launch in June, and we think you’ll find many benefits to the new design.
We’ve made our new website easier than ever to navigate, with more streamlined menu options and better navigational tools. You’ll be able to find what you’re looking for more easily than ever. Our new website will also offer:
- Updated product descriptions
- More illustrations and images
- Higher quality graphic design
- New format highlighting key features
- Easy-to-use tools at your fingertips
The new website will offer more images, text, and guidance about each of our products, helping you to find the best options for you and answer your questions more easily. It will continue to feature the same great tools, such as our airflow calculator.
You’ll have easier access to all of our case studies, so you’ll be able to find out more about companies using a process or solving a problem similar to yours and see how the CMAXX or BRF became a key part of one of our customers’ businesses. You’ll also have easier access to all of our blog posts, where you can find information about everything from filters to ductwork to trouble-shooting to company events and stories. Don’t forget to read through our Imperial Systems Quarterly Newsletters to stay up to date on the most exciting and important events happening with the company!
With lots more images, a streamlined design, and a new, cleaner look, we hope you’ll find the new website everything you’d expect from Imperial Systems. From the company that makes the sharpest and cleanest-looking dust collector on the market, you’d expect a website that looks just as good.
Please enjoy our new website and contact us with any questions or comments. We will be working out any bugs during the website’s debut, so please don’t hesitate to let us know if you find anything we need to improve upon!
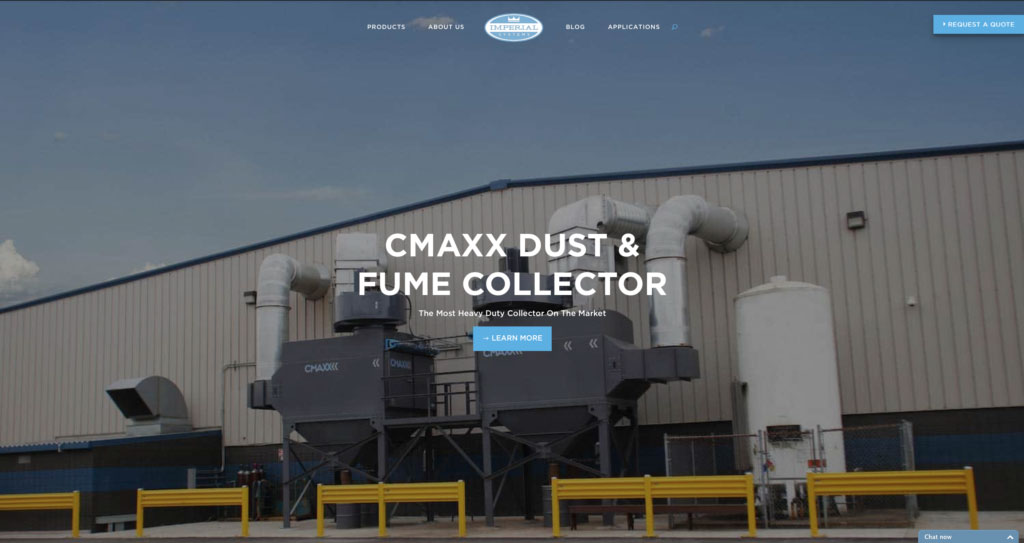
Read more
by Imperial Systems | May 16, 2018 | Uncategorized
Sometimes it’s necessary to cut or weld, or hot work in the vicinity of your dust collector. However, this can be extremely dangerous if your dust is explosive. A dust collector, after all, is an accumulation of dust. If that material is combustible, careless hot work could lead to a catastrophic explosion.
“Hot work” is defined by OSHA as “welding, brazing, cutting, soldering, thawing pipes, using heat guns, torch applied roofing and chipping operations, or the use of spark-producing power tools, such as drilling or grinding”. Most of us would think twice about welding or cutting in near a dust collector or any other combustible dust. But some tools, even ones that shouldn’t produce sparks, may have faulty wiring. This can lead to a fire or explosion.
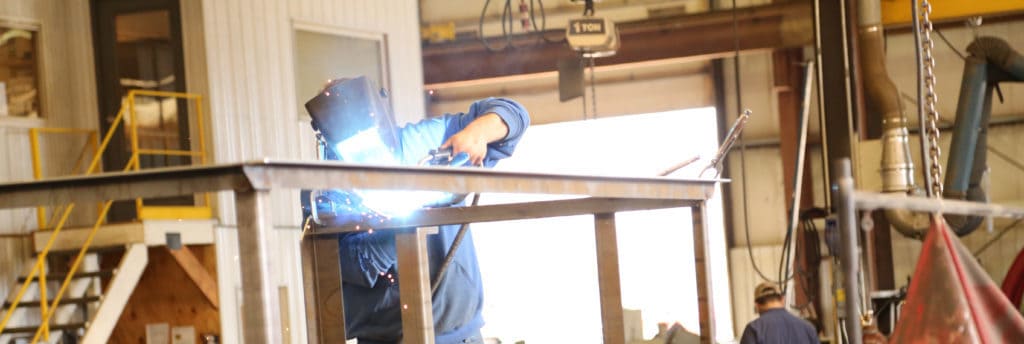
Hot Work Procedures
No hot work should be done near the dust collector without the correct procedures (see NFPA 51B). This NFPA standard specifically defines the procedures for conducting this type of work anywhere that it might cause an explosion.
Hot work near or on a dust collector might include repairs or adding/removing a piece of equipment or ductwork. It may include any number of other projects. Before doing this kind of work around the dust collector, you must have a hot work procedure IN WRITING:
- Shall be in writing and available to anyone conducting hot work in the area
- It must require an inspection of the work area before the work starts
- Must have a permit signed to show that all phases of the work have been inspected and approved
The program should assess safety equipment in the area. On a dust collector that might include a spark arrestor, spark detector, fire suppression or sprinkler system, abort gate, explosion venting, or other types of fire and explosion safety devices.
Hot work may require completely blocking the ductwork to the dust collector, or if the work is on or close to the collector, may require removing the filters, emptying or removing the hoppers, and thoroughly cleaning the entire dirty air side of the dust collector. a strong g recommendation is that a fire suppression system is in place before hot work begins. This will suppress any fire that might start. Further, remove as much of the dust as possible if it is explosively combustible.
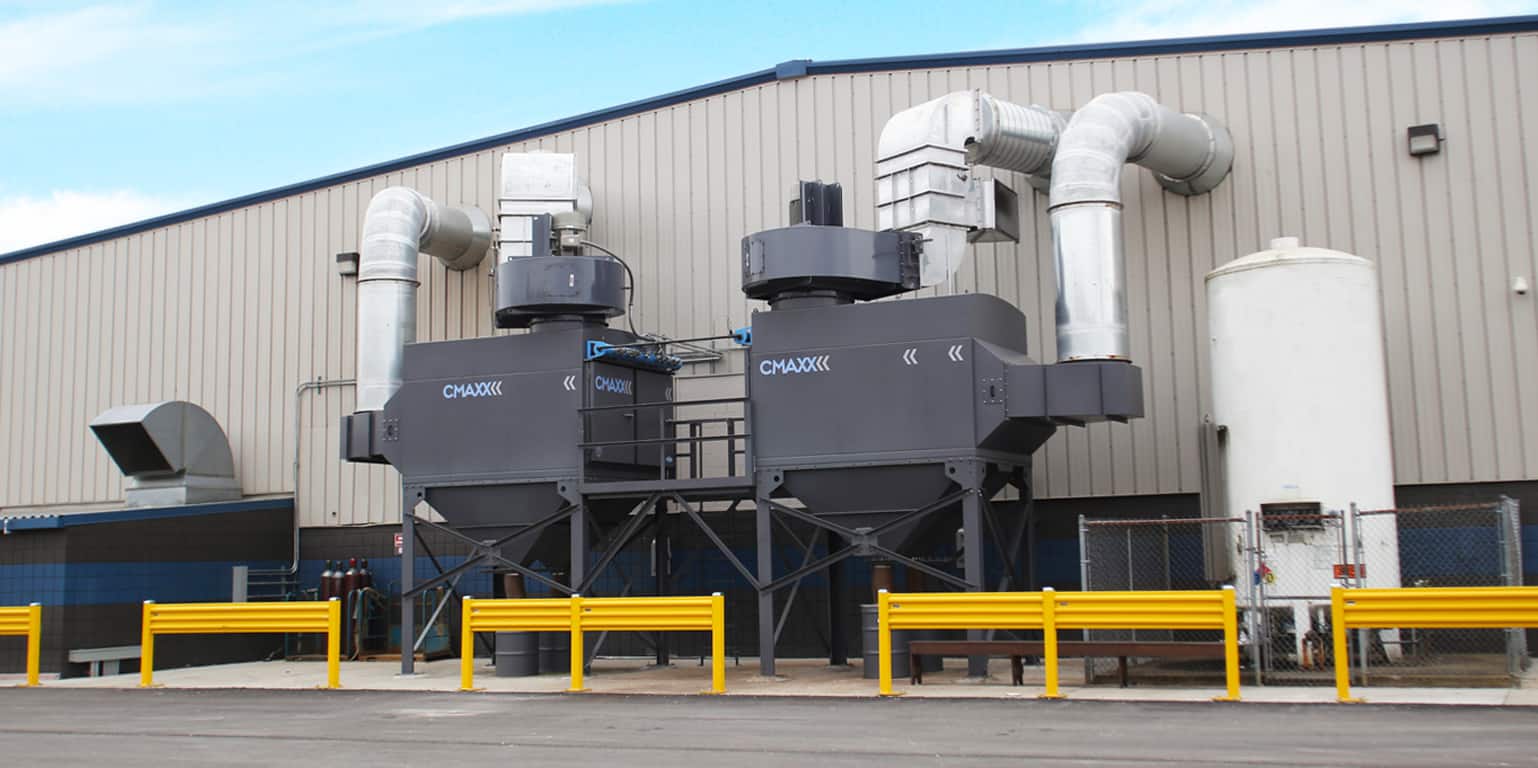
Permits Ensure Safety
NFPA 51B specifies that the company safety specialist will issue a permit for work to proceed once achieving an inspection and determination of safety for hot work. It’s the job of this designated safety specialist to inspect the area of hazards. The specialist ensures the removal of all combustible dust. They confirm the isolation of all sparks and heat and establish safety procedures in the event of a fire.
No one should be allowed to perform ANY type of hot work, including the use of spark-producing power tools, in the vicinity of the dust collector without a permit. However, it happens all the time and puts lives at risk if the dust is combustible. Take the time to assess this hazard in your own workplace. If the hazard exists, your safety professional should set up hot work procedures to make sure no one puts themselves or the facility at risk.
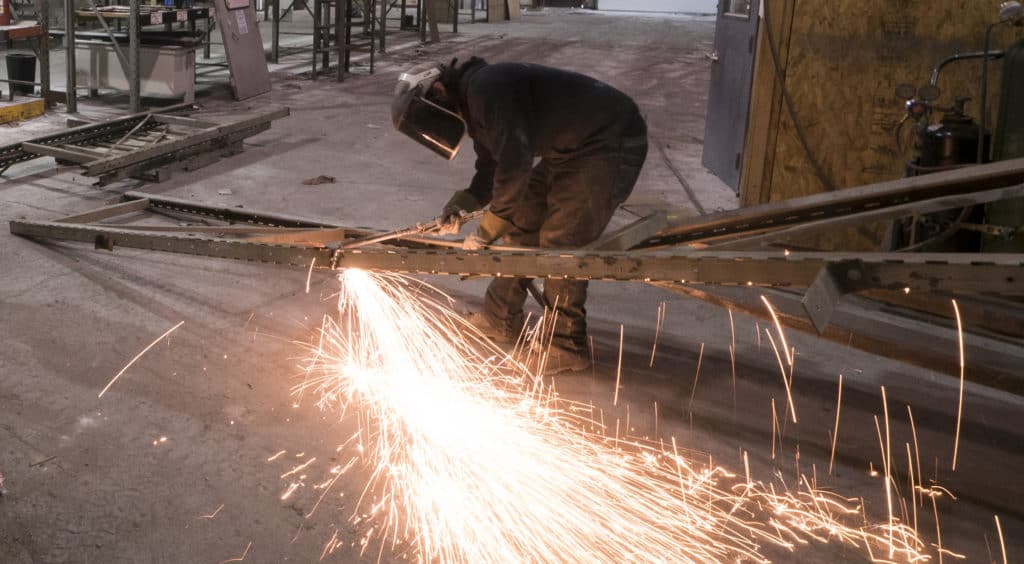
Read more
by Imperial Systems | May 9, 2018 | Uncategorized
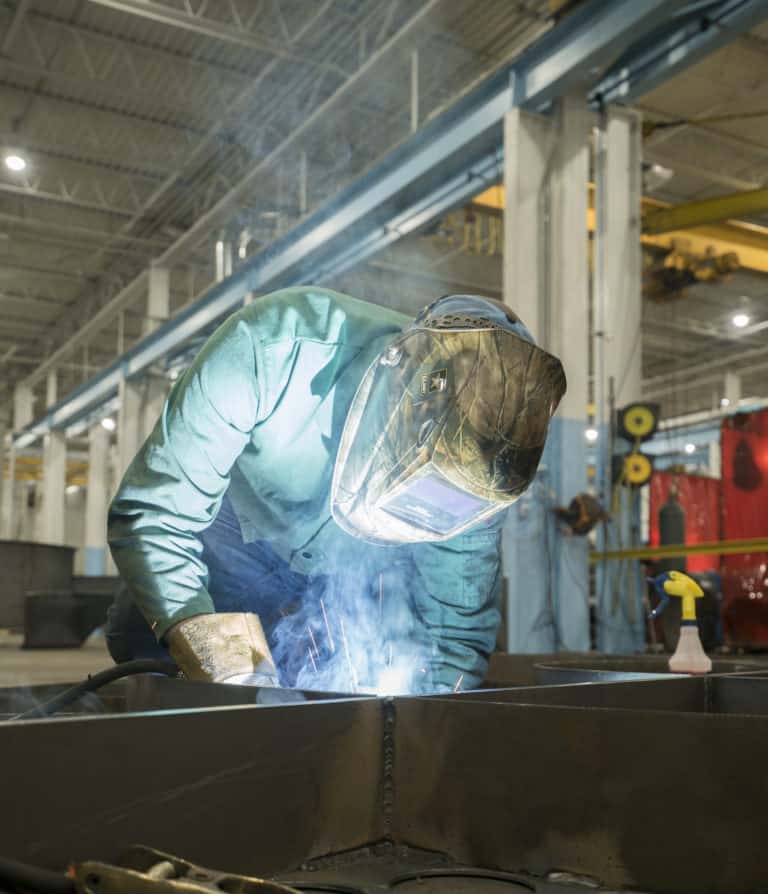
Like many companies in the USA, Imperial Systems wouldn’t exist without our skilled tradespeople. Making a quality product comes from training and experience. Right now we’re lucky enough to have a young man enrolled in a local trade school. He has come here for both of those things.
Garrett is a student at our local Mercer High School and participates in the Mercer County Career Center Vo-Tech trade school program. Every morning he comes to work at Imperial Systems, welding CMAXX and BRF collectors. He’s learning from our experienced team and getting great real-world experience.
Garrett knew about Imperial Systems from a friend who works here in the summer. He chose us for his Vo-Tech worksite and told us about how much he’d learned already. He shared the difference between welding in school and working from blueprints here. There’s additional motivation in working on projects that are actually going out to customers. Fortunately, he is eager to learn and enthusiastic about his work.
He’s also enthusiastic about welding in general. This is demonstrated by the artwork he created for a trade school skilled trades art show. He got to take his work as far as state competition in Hershey, PA. In school, he plays football, wrestles, and participates in show choir.
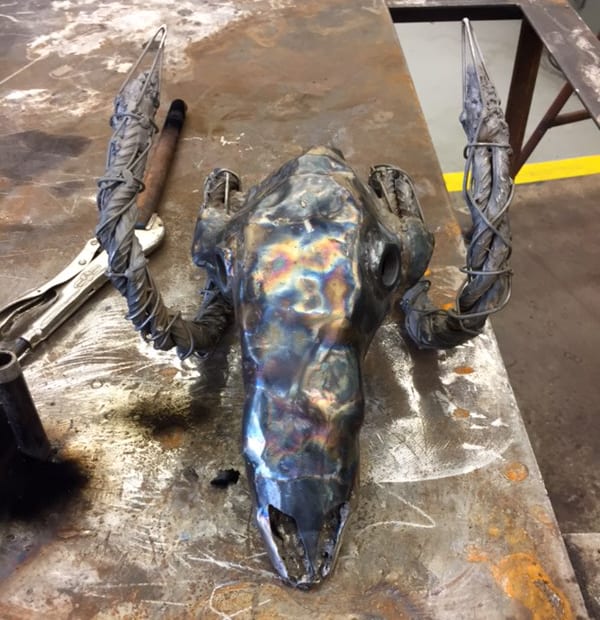
Talented and Versatile Trade School Student
While show choir might seem like an unexpected hobby for a welding student, Garrett is an intelligent and well-rounded person, and our conversation ranged from his project on World War II propaganda to the deficit of skilled tradespeople and the over-abundance of college graduates with useless degrees. He has clearly thought a lot about his future and has a good understanding of the need for welders in the workforce and how it has affected his career choices.
He can also tell you from first-hand experience how under-funded trade schools struggle to attract and support students. The demand for skilled tradespeople dwarfs the budget that trade schools have to bring in and train these people. As a result, a future shortage of welders and similarly skilled tradespeople looms, and trade schools continue to be neglected as a source of solid, well-paying careers for many young people who don’t see college (or the accompanying debt) in their future.
The school year is almost over, and Garrett has plans for his future in the skilled trades: he has enlisted in the army and plans to work in one of their metalworking divisions. He’s not sure whether he’ll stay in the military as a career, but he knows we have several veterans working here now, so he’d be in good company if he decides to come back.
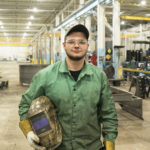
Read more
by Imperial Systems | May 2, 2018 | Uncategorized
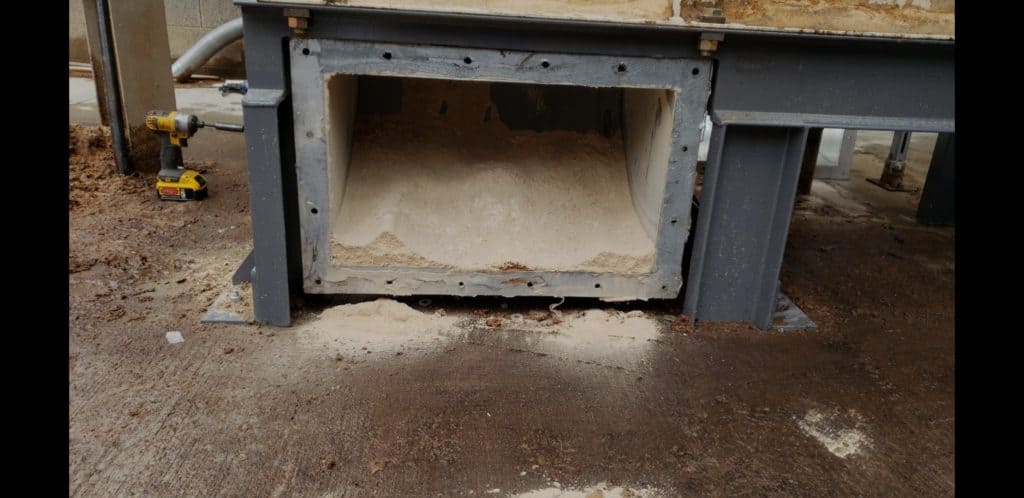
1. What information do we need to start designing a system and what are the considerations for ductwork?
- First, you need to know about your dust. Important details: how it’s being generated, how toxic or hazardous it is, what exposure levels OSHA considers to be too high, whether it is combustible and/or explosive, particulate size, physical characteristics.
- Combustible dust will certainly require special precautions in the system design to protect the facility and workers from deflagration or explosion. Dust testing can determine how explosive dust is and the needed precautions.
- A general layout of the facility and each location generating dust.
- A sketch of the ductwork layout, including the location of the dust collector, fans, and ductwork branches.
- A plan for the type of hood to use at each of the dust capture locations. Also, how much CFM each one will require.
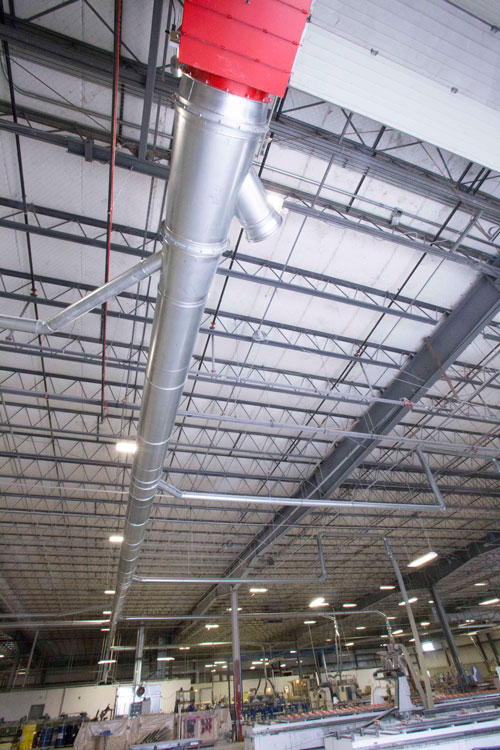
2. What are the basic components of a dust collection system?
- Hoods: must be the correct design for each type of machine. They must also be efficient at removing the produced dust by that machine.
- Ducts: must be the correct size to allow proper airflow and keep air moving. They also must not have too many bends or elbows to slow down the airflow. This can allow particulates to drop out of the airflow. It can also create a point for wear and tear on the ductwork.
- Fan: the fan must be powerful enough to keep air moving through all the ductwork at a high enough velocity. Drops in velocity or not enough velocity can allow dust to fall out of the air stream.
- Collector: must be the correct size for the system. It must have an air-to-cloth ratio that makes it able to filter all the air coming into the collector. Must have correct filter material to handle the size and type of particulate. This could be DeltaMAXX nanofiber for most applications, or spunbond, PTFE, or other specialized filters for particular applications. Further, filters must be fire-retardant if the dust is flammable.
- Fire Prevention: devices such as spark arrestors can help keep sparks from entering the dust collector. A water or chemical fire suppression system can extinguish sparks or flame when a sensor detects them.
- Venting/Exhaust: If returning air to the building, it must be clean enough to meet all health and safety standards. If dust is toxic, it may necessitate an extra layer of safety in the form of HEPA filters. A backdraft damper can prevent backdrafts from allowing dust back into the system. An abort gate with spark detector can sense a spark or flame, diverting the flame in a safe direction.
3. What is the process for designing a ductwork system?
- System design should start with identifying each place that a hood or other source capture point needs to go. In other words, anywhere that generates dust.
- Use appropriate calculations to figure out how much CFM you need at each of these points
- Determine the minimum duct velocity. This is based on the transport velocity (the airflow needed to keep your particular dust moving in the air stream).
- Calculate the size of duct for each branch. This is based on the CFM and the transport velocity and will be different for different spots along the ductwork.
- Increase duct velocity at each branch to maintain transport velocity until all branches are connected to the main duct.
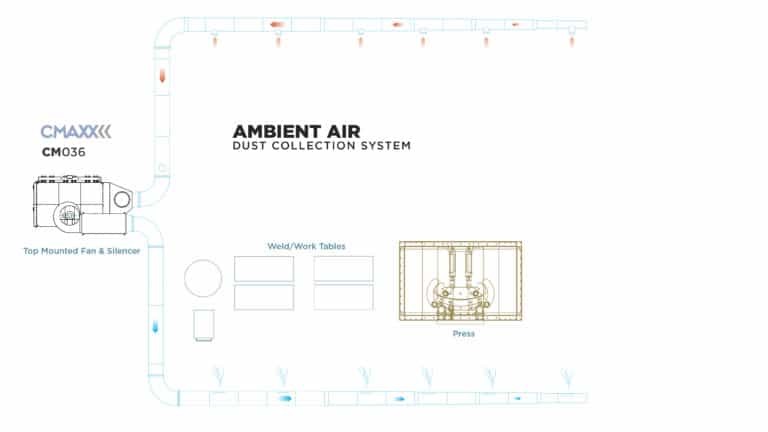
4. Will this be an ambient system or source capture system?
- Ambient system: removes air from the entire work area. It filters and recirculates it back into the area, diluting contaminated air with clean air.
- Air changes per hour: the number of times per hour that the total amount of air in the area changes. This is from old/contaminated air to new/clean. The calculation is made with the cubic volume of the work area and the number of required air changes to maintain air quality.
- Source capture/close capture: captures generated dust at each point throughout the facility.
- This type of system must have properly designed hoods at every capture point. Perform and double-check your airflow calculations. Specialty hoods can be designed for almost any application.
- Static pressure in these systems is an algebraic formula. It includes a loss at hoods, flex ducts, transitions, and straight ductwork runs. Minimal use of elbows and flex ducts in the ductwork runs will greatly improve system efficiency.
- For dangerous or toxic dust where exposure must be kept to an absolute minimum, a close capture system will keep the material from entering the air of the general workplace.
We hope this set of articles about ductwork help to answer some of your questions. Please thank the knowledgeable and experienced Charlie Miller for providing so much valuable information and sharing his wisdom.
Read more