by Imperial Systems | Sep 1, 2017 | Uncategorized
If you’ve stopped by our website, you’ve probably seen the little box pop up asking if you’d like any help. And you probably assume it’s a little website robot that’s going to be about as helpful as your ATM.
That’s not a robot monitoring that box, though. It’s one of our hard-working staff. The name is a real name attached to a real person. So if your box says you’re talking to Rebecca Wescott, this is who’s on the other end of the line:
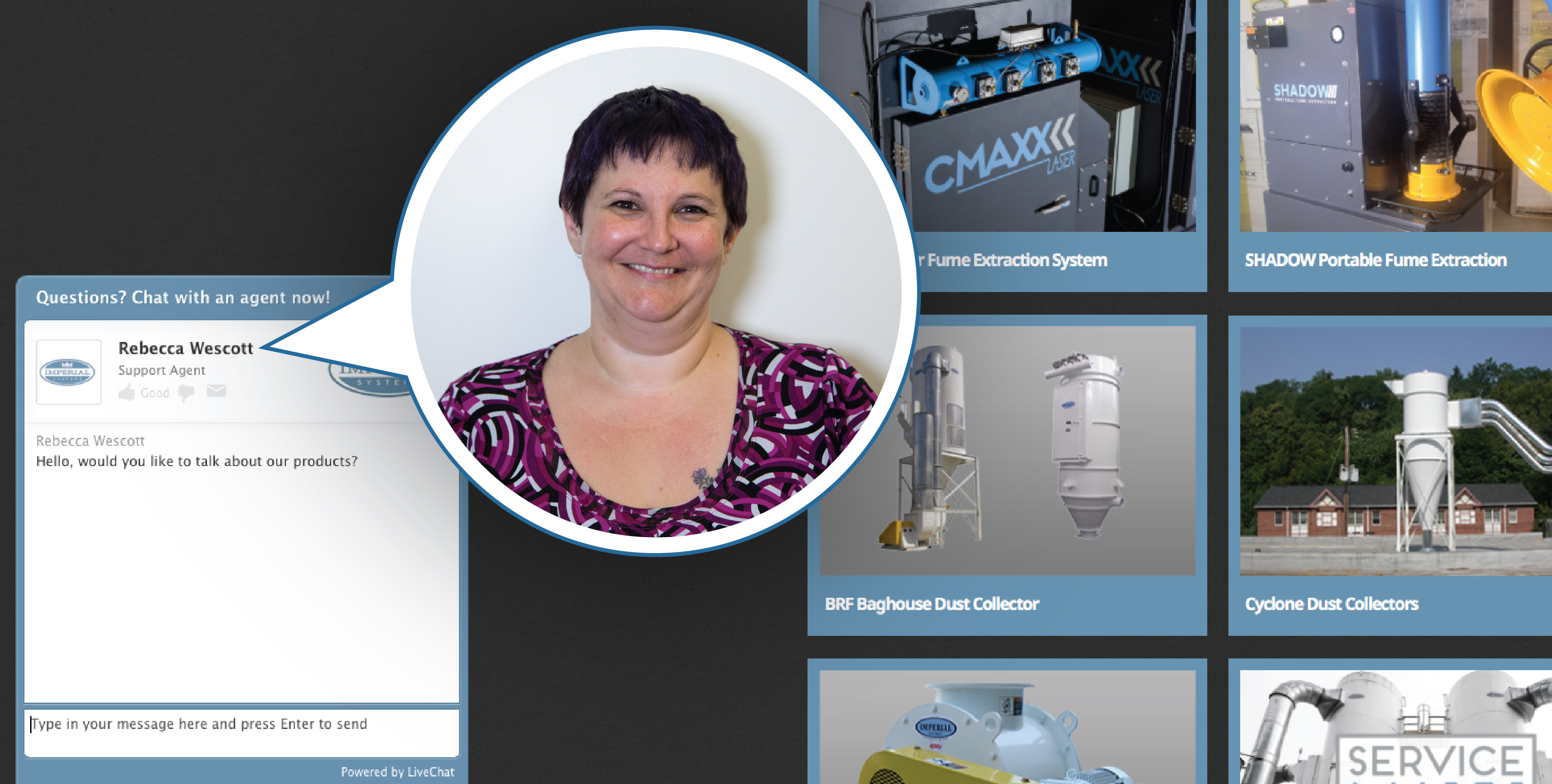
Think LiveChat is just for… well, chatting? We can do a lot more than that. Here are ten things we can do for you to solve your problem with just one website visit:
- Upload information for you about products like spark arrestors, abort gates, airlocks, and fire suppression systems
- Answer your questions about how a piece of equipment works, how it’s used, or whether it might work for you
- Link you to a post or article that answers your question in detail (exactly how a baghouse works, health risks of plasma cutting, combustible dust management, etc)
- Upload an owner’s manual or other technical information for you if you’ve lost yours (or your customer has)
- Find out what kind of product you need and who might be the best person to help you, so you don’t get transferred around
- Give you a “request for quote” form to fill out so our sales engineers can contact you and know exactly how to help you
- Answer your questions about our filters and check our cross reference for matching part numbers
- Put you straight through to your own personal equipment or aftermarket team member for personal service
- Walk you through any problems you’re having and get you to the person who can solve them as quickly as possible
- Ask questions to help get you where you need to go, quickly and without hassle, or assign someone to follow up with you right away
Want to find out If it’s really Rebecca (or Zach, or Justin, or another one of our staff)? Stop by our website and say hello! That little box is an invitation for you to start getting the help you need right now… no phone call, no clicking around the website, just fast and easy assistance from a real human.
Read more
by Imperial Systems | Aug 18, 2017 | Uncategorized
The CMAXX is a modular dust and weld fume collector that can be sized for any application. What you may not know is that the CMAXX is also a modular ambient system. With two CMAXX collectors, one pulling air from inside the facility and the other pushing air in as a “push-pull” system, continuous ambient airflow is achieved. What happens, though, if you have multiple areas where you need dust and weld fume collection, or if you add onto your facility or equipment? With other types of systems, you would need to get rid of your current collector and buy a bigger one to handle increased airflow, then run lengths of ductwork to cover the whole space. With a modular CMAXX system, it’s easy to add another set of “push-pull” CMAXX collectors to create more ambient dust and weld fume collection. Since the system is modular, your original CMAXX system can stay in place while new units are added on to meet your changing needs.
The idea for this modular system was developed by president and CEO Jeremiah Wann as Imperial Systems Inc prepared for its transition to a new, larger building. Here, he found that we faced some challenges many other companies will be familiar with: a much larger space than the previous building, with equipment in new locations, and also with unused space for anticipated growth.
An option for dust and fume collection for the company might have been to build a huge CMAXX collector big enough to create ambient capture through the entire building, even the parts not being used yet. A collector of this size would have a lot of ductwork and need to move a very large volume of air, increasing costs.
Instead, the company hit upon a better solution: the modular CMAXX ambient system. CMAXX collectors will be installed in the parts of the building where needed, with one providing the air “push” and the other the air “pull” to keep clean air circulating. When new equipment is added, or when the company expands into the unused parts of the building, the modular CMAXX system will allow them to just add two more small CMAXX collectors to create the “push-pull” airflow in that area.
Any company can have changes in their facility, whether it’s moving things around the shop, expanding, or increased dust or fume production. Instead of buying a whole new dust and fume collector or installing a lot of new ductwork to handle your changing needs, consider the option of the CMAXX modular system: always ready for you to add on or adapt to your changing needs.
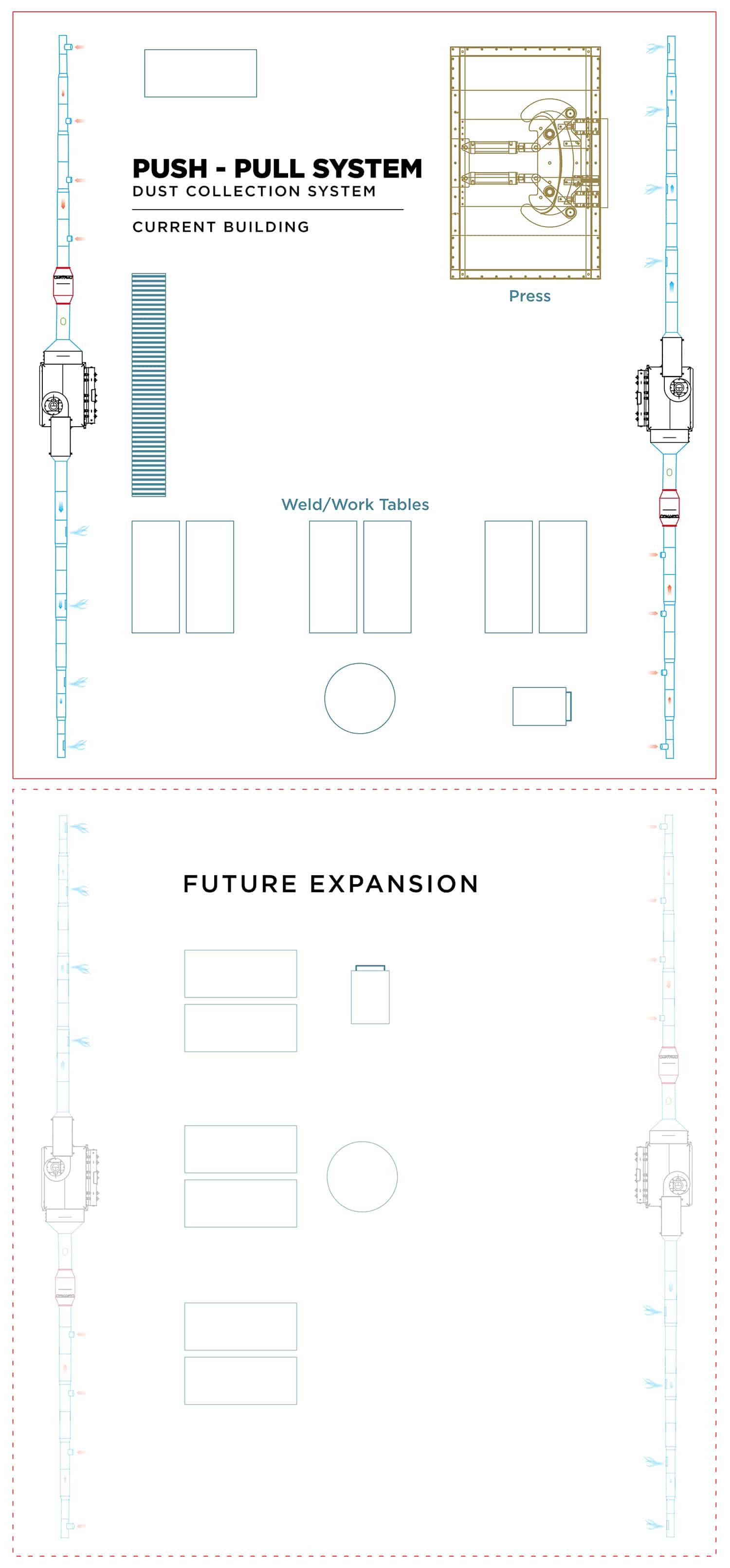
Read more
by Imperial Systems | Aug 7, 2017 | Uncategorized
With a CNC plasma cutting table, it’s essential to have some way of controlling the dust and fumes from the cutting process. One solution is a water table, where the metal being cut is underneath a layer of water that prevents it from generating fumes. The other solution is a downdraft table, where air flows down through the table and pulls dust and fumes away from the cutting area.
We have worked with customers who are using both of these types of dust and fume control on their CNC plasma tables, and we’re discovered some serious issues that people encounter with the water tables. While the water table may be a lower up-front cost than a downdraft table with a dust collection system, many people find that the ongoing costs and problems with water tables make them a bad long-term investment.
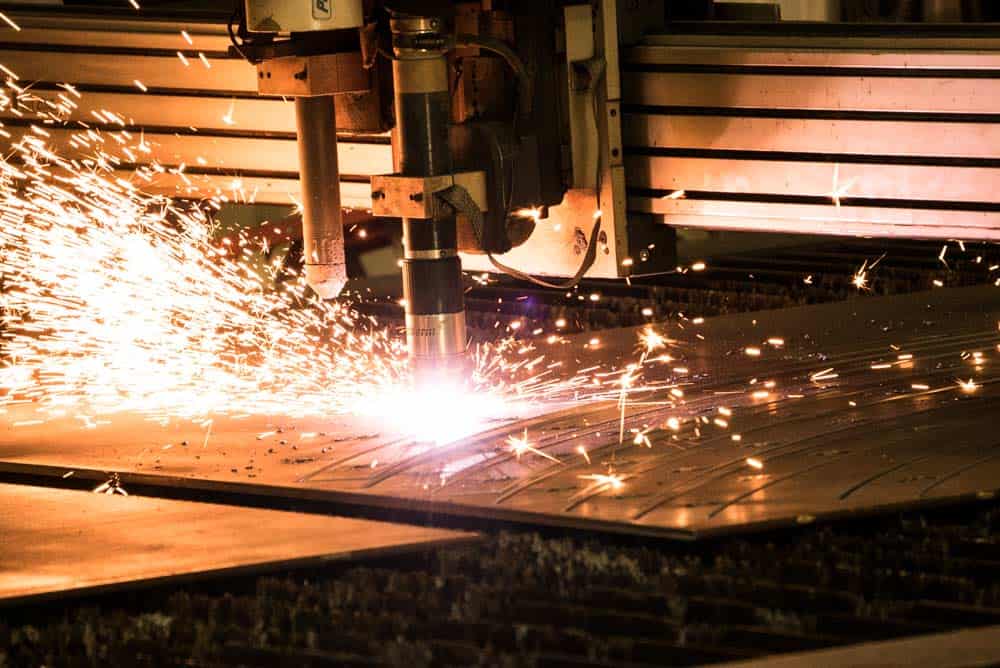
Here are some of the primary issues our customers have experienced with water tables:
“We waste a lot of time adjusting the water levels. Whenever the water level isn’t correct, you get a lot of smoke and steam in the building.”
“If the sheet isn’t sitting perfectly flat, the water doesn’t always cover it and there are a lot of fumes released from that. Also, if there’s any warping, this can create a real problem with smoke and fumes.”
“Disposing of the water is a major issue. It’s contaminated with all kinds of things, and it has to be pumped out of the machine. Then it has to be processed before we can dispose of it.”
“Once you pump out the water you have to handle all the sludge. It’s a mess to clean out, takes up a lot of time, and nobody likes dealing with it.”
“With galvanized metal, we get ‘white rust’ corrosion from cutting on the water table. It can cause some serious damage to the parts.”
“When wet parts come off the table, they can’t just be sent off to the fabrication area. We have to have a space to set them out to dry, and they can’t be used till they’ve dried off.”
“We’ve had issues with the table overflowing or leaking, and then we’ve got dirty water all over the shop floor, and it’s a hazard and a mess.”
“Our wet table creates steam and splashes of hot water. There’s the potential for someone to get burned. We’re also concerned about water or steam damaging the cutter’s computer.”
“The water and steam evaporating off the water table puts so much humidity into the air that we’re starting to see rust on our tools and equipment, which we’re not happy about.”
ADVANTAGES OF A DOWNDRAFT TABLE:
- Almost no adjustment is needed once the system is in operation. No water levels ever need checked or refilled.
- Consistent airflow pulls fumes away from the CNC plasma cutter even if the metal isn’t flat to the table or if it warps during cutting.
- Dust is usually collected in a drum or hopper for easy disposal. No pumping, no sludge, and no figuring out how to dispose of contaminated water.
- Maintenance is minimal compared to a water table. The dust collector will require filter changes (the average is about once a year, depending on use). Changing filters is a simple process and will involve much less down time for the CNC plasma cutter than pumping water and cleaning out sludge.
- Parts come off the table ready to go. There is no wasted time letting them dry, and no wasted space for parts to sit and dry off.
- A downdraft table fully contains dust and removes it from the work area. There is no leaking or spilling water to create a hazard, and no dust or fume particulate escapes into the work area.
- The air flowing through a downdraft table produces no steam and no splashing of hot water. All sparks and hot materials are pulled down and away from the work area safely.
- A zoned downdraft table collects fumes and dust only where they are being produced, which is efficient and keeps all fumes contained to a small area for removal.
Over time, a downdraft table for your CNC plasma cutting system will save you time and money. Up-front cost is lower on a water table, but a company doesn’t buy a CNC plasma cutting system for short-term use. You’re going to have this table for a long time. And over time, our customers have consistently found that the water table costs them much more in maintenance costs, time, and potential safety hazards.
Cost is important, but one of the most important things for you is probably the quality of your product. Companies that manufacture CNC plasma cutting equipment will tell you that a downdraft table produces a cleaner cut and a higher quality product than a water table. If they tell you that a water table produces equal or better quality, you can bet they want to sell you a water table. The industry knows that if you want the cleanest CNC plasma cuts, a downdraft table is the way to go.
Read our white paper on cutting tables.
Read more
by Imperial Systems | Jul 26, 2017 | Uncategorized
Part of the Trump administration’s push to support American manufacturers has involved cutting back on regulations. Several OSHA regulations in progress, including the new silica and beryllium exposure limits, have had their start dates pushed back so they can be reviewed. For industries that deal with the risk of combustible dust, one of the biggest changes may be that the administration has removed the proposed combustible dust regulations from OSHA’s agenda.
What was the plan for combustible dust regulations?
The delayed silica and beryllium regulations had already been put in place before the Trump administration requested review of them, and you can expect that they will still be implemented at some point. The combustible dust regulations, though, had been discussed, debated, and delayed for a long time before the current president took office.
The Chemical Safety Board (CSB) is an independent federal agency that investigates industrial accidents, including dust explosions. They have been pushing for combustible dust regulations for years, with one major push coming after the disastrous Imperial Sugar dust explosion in 2008, where one smaller explosion ignited sugar dust that had accumulated all over the building, killing 14 people and completely destroying the facility.
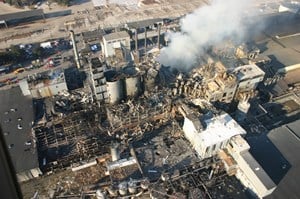
Another incident that prompted the CSB to push for combustible dust regulations was a titanium dust explosion in West Virginia that killed three workers in 2010. Throughout the next several years, the CSB kept combustible dust regulations on its “most wanted list” of new rules it considered necessary to prevent industrial accidents and deaths.
There are already combustible dust regulations for the grain industry, where explosions from dust in silos, elevators, conveyors, and mills is a constant hazard. The CSB and other safety organizations hoped to push this type of regulation to cover all types of combustible dust.
What kept the combustible dust regulations from happening?
Every year OSHA reviews laws and regulations they want to work on. Combustible dust regulations have been on that list for several years, but have been delayed or not decided on. The main problem is that such a regulation would affect nearly any industry that produces dust, since almost all dust is potentially explosive, and every process that causes dust to be produced.
With uncountable numbers of different types of dust and different processes, making combustible dust regulations that could cover all of these was a very difficult task from the beginning. This kind of regulation would have to cover industries from food to metalworking to plastics to pharmaceuticals. It would be a huge job to figure it all out and make it enforceable.
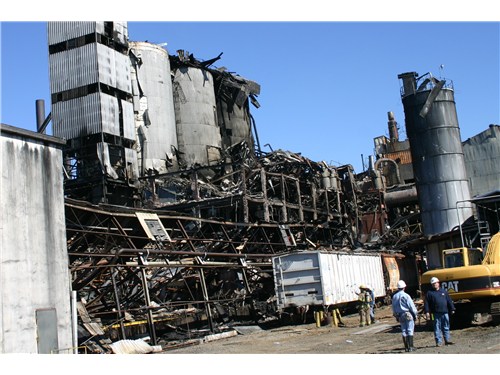
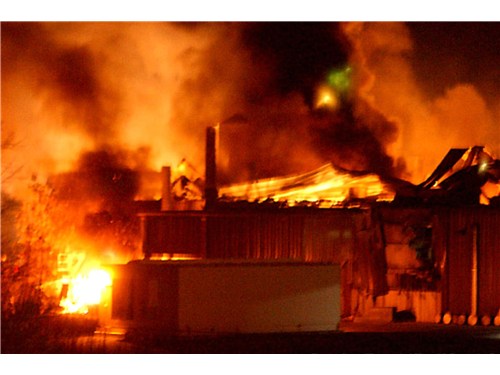
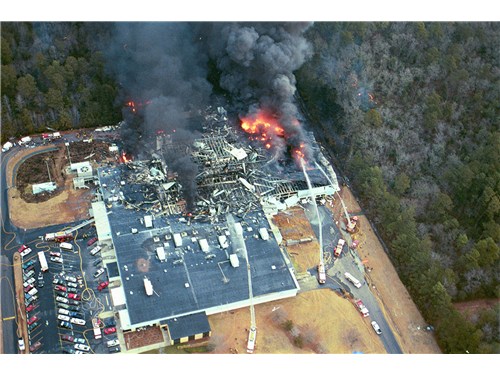
Does that mean OSHA can’t fine you for combustible dust problems?
Except for the grain industry, OSHA does not have combustible dust regulations that they can use to fine violators. However, they have issued many guidelines and recommendations for combustible dust safety. These are not enforceable. However, that does not mean combustible dust can be ignored. OSHA does have enforceable regulations for fire protection, ventilation, general environmental controls, and hazardous materials. Uncontrolled dust in your facility may be a violation of any of these.
In addition to these rules, OSHA can enforce serious fines in situations where workers are injured or killed on the job because employers did not correct a dangerous situation. In the event of a combustible dust explosion with injuries or deaths, serious penalties could be enforced for letting a hazardous situation occur.
Even without concern for combustible dust regulations, lawsuits against a company for injuries or deaths in a dust explosion are quite likely, and they could cost much more than any OSHA fine.
What guidelines should you follow to prevent combustible dust hazards?
The National Fire Protection Association (NFPA) does not make combustible dust regulations. However, they do set standards for managing combustible dust and preventing dust fires and explosions. NFPA standards are often considered the industry standard, and many local and state building codes require that facilities meet NFPA standards. NFPA 652 and 645 deal specifically with combustible dust.
Even though OSHA does not have combustible dust regulations, state and local safety administrations or building codes may have regulations that are much stricter than OSHA’s. NFPA standards are the gold standard by which many state and local governments set their safety regulations.
Why are engineering controls such as dust collectors so important?
The only good way to keep combustible dust from creating an explosion hazard is to get it out of your facility. Since blowing industrial waste into the surrounding atmosphere tends to be frowned upon, a dust collection system that filters the combustible particles out of the air can be the best solution.
Even if a fire does occur in a dust collector, properly designed systems will have safety features such as fire suppression, explosion venting, and abort gates to safely control or divert a combustible dust explosion. While OSHA does not have a regulation to enforce dust collectors for combustible dust, they do strongly recommend them, and the NFPA also strongly recommends a well-designed dust control system as a key safety feature.
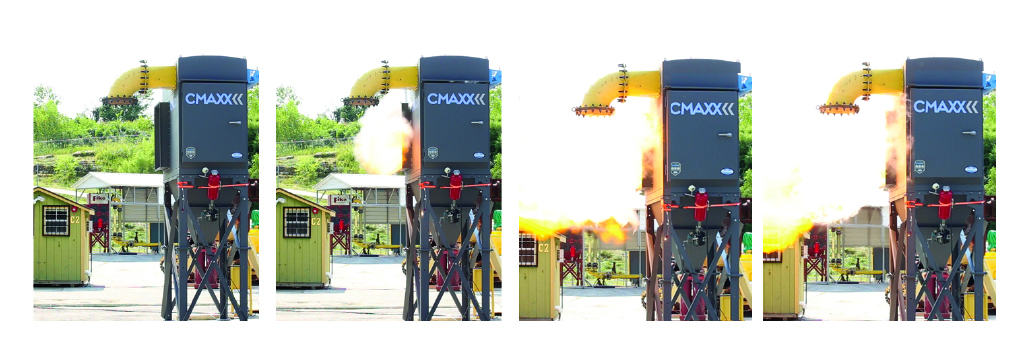
Read more
by Imperial Systems | Jul 5, 2017 | Uncategorized
If your company is following the principles of lean manufacturing, is your dust collection system keeping up? Lean is everywhere, eliminating waste and improving processes. However, many companies trying to find lean solutions haven’t taken a look at that ancient baghouse rusting away behind the building. Can you apply any of these lean solutions for dust collection?
In our last post we talked about an efficiently running dust collection system, and how this reduces waste and saves time and money. This time, we’re going to look at the system design and see whether yours is as lean as it could be.
SITUATION 1:
You have several pieces of equipment in your building that generate dust. The equipment doesn’t move around, and most of the dust or fume is generated at a particular point. Examples can be a plasma or laser cutting table, a blast booth, a mixing machine, or many others.
The leanest solution for this situation would usually be source capture. Hoods can be located directly over the equipment, or the equipment can be designed with dust collection built in. An example of this is a downdraft system on a plasma cutting table. These lean solutions for dust collection make sure the dust generated at certain spots doesn’t get out into the rest of the area.
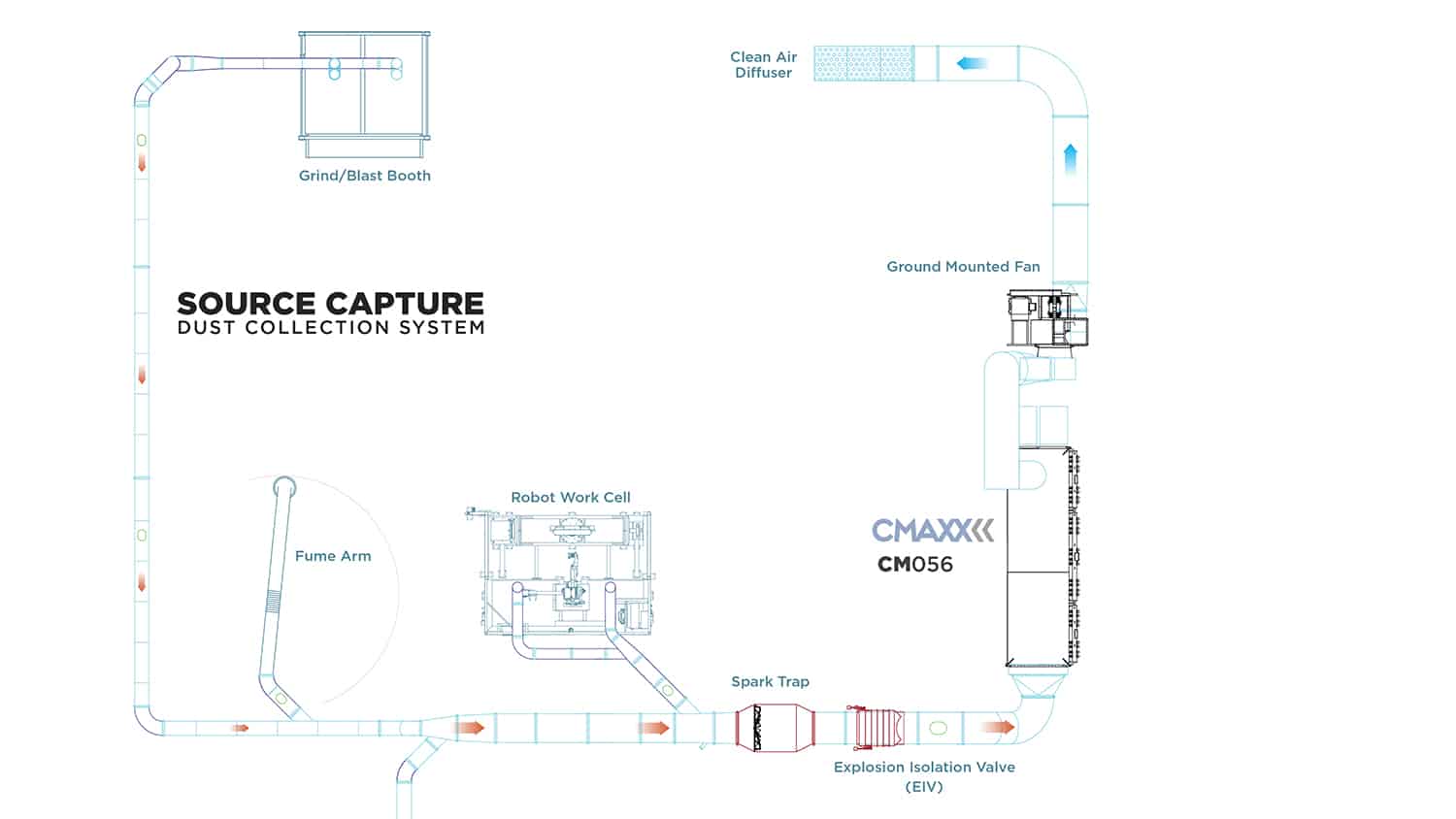
SITUATION 2:
In your facility, welders and fabricators work on assembly of large steel items. The workers usually move around the piece they’re working on. It’s not practical to put hoods over the entire area: the sources of the dust and fumes are moving around, and you would need too many hoods. This would require a huge amount of air flow and huge fans, which is not efficient.
In this situation, the best lean solution for dust collection might be an ambient system. This type of system filters the air in the entire area. It is designed to change over all of the air inside that space within a certain period of time. As it does this, it removes dust and fumes, even if the sources are moving around and can’t be put under a hood. It will keep all the air clean, not just the air around particular machines or work areas.
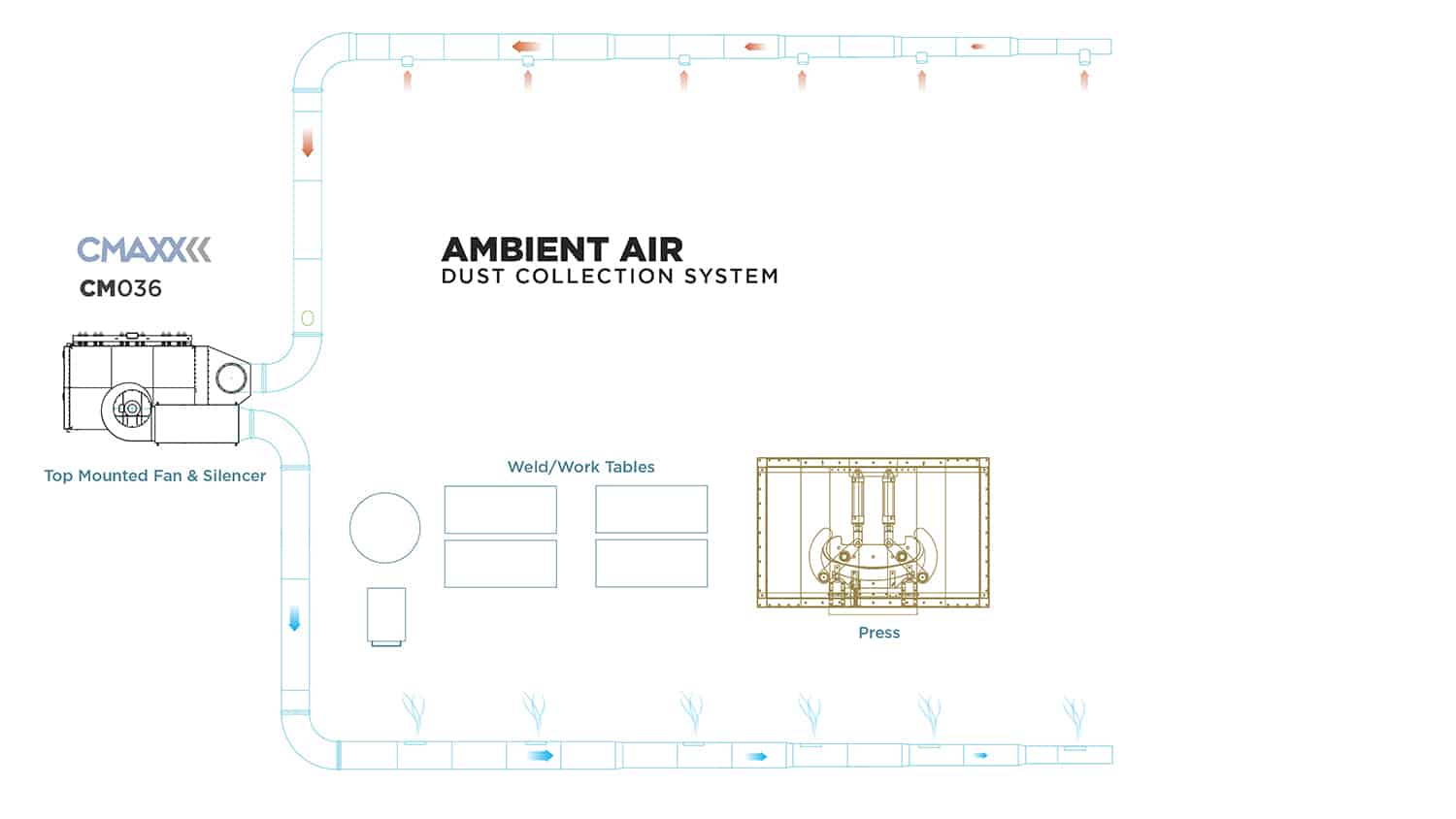
SITUATION 3:
You have a machine shop with welders and fabricators working on different equipment at different times. Some of the machines might have hoods over them, and the cutting table might have a downdraft system on it. These are examples of source capture.
Another type of source capture often used in these situations is a fume arm. This flexible arm is situated near the welder, and he adjusts it as he works to capture the fumes. He needs to keep the hood of the arm positioned correctly so it’s catching the plume coming from the welding.
While in theory this is an effective method of source capture, it is not a lean solution for dust collection. Time is spent repositioning the hood. Welders deal with the issue of having the hood in the way of the work area, slowing down the process. It is difficult to position the hood correctly for maximum efficiency. These all create wasted time, worker frustration, and inefficient fume collection. The end result: the fume arms don’t get used, and your system is wasting airflow because it’s not collecting anything at those points. Check out the article where Imperial Systems Inc. President Jeremiah Wann tackles this issue directly. Click Here.
In this situation, your system may be able to do double duty as an ambient and source capture system. You can still have the dust collector attached to the cutting table for downdraft fume collection, and hoods over stationary work areas. However, you need a lean solution for dust collection from your welding or similar work areas.
Having ambient dust collection makes sure that the air in the entire facility is clean. It’s often said in lean manufacturing that the best solution is the one people will actually use. Considering that fume arms are often used wrong or not used at all, they’re not the best lean solution.
For each company or workplace, there are lean solutions for dust collection, but they are different for each situation. Contact us to talk to one of our systems specialists and figure out the leanest way to handle your dust collection.
Read more
by Imperial Systems | Jun 22, 2017 | Uncategorized
The Second Issue of Dusty Jobs Newsletter. Articles include How to Troubleshoot a defective filter and a story about the different people at Trade Shows and how they score free gear.Dusty Jobs Newsletter Issue 2-1
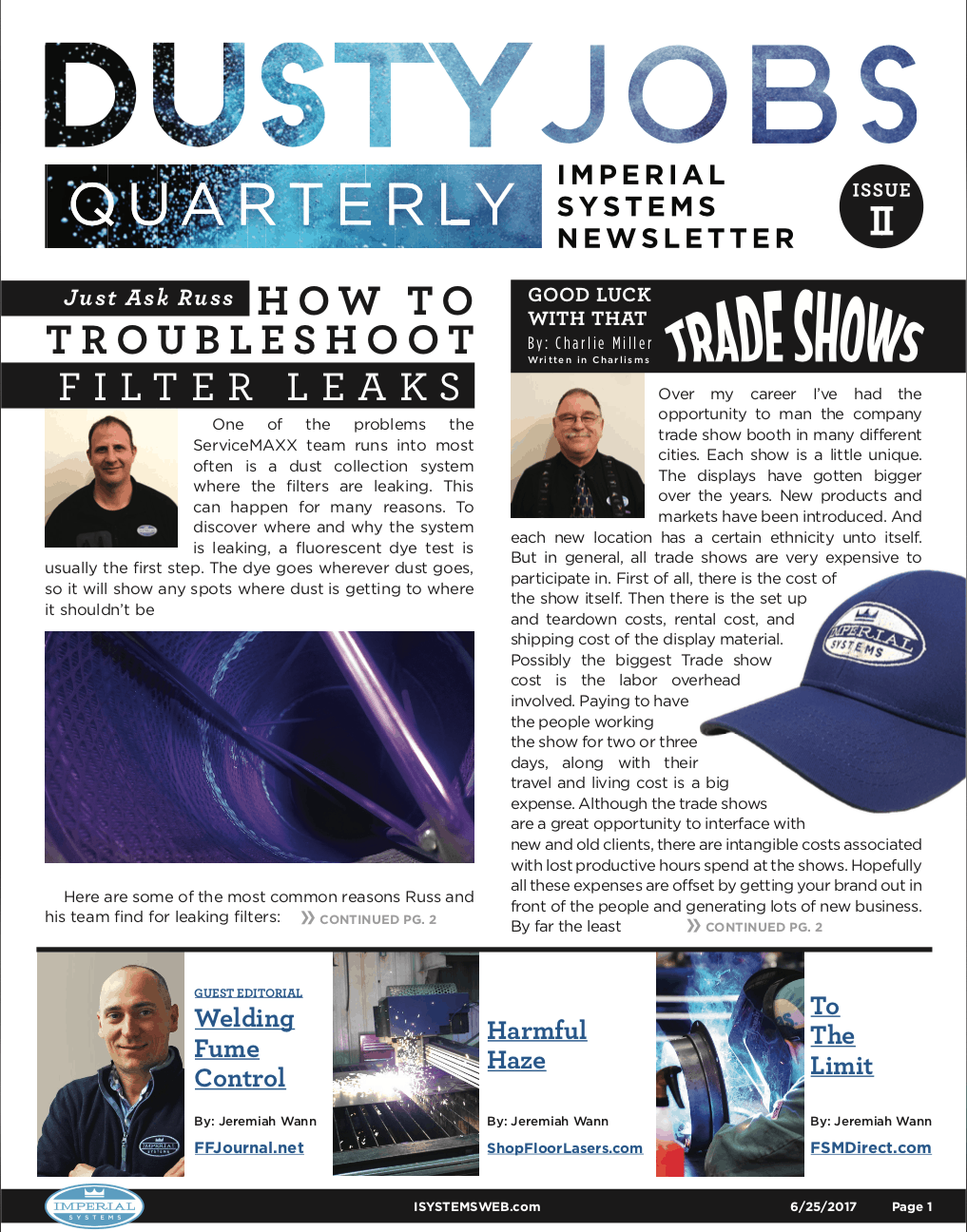
Download DUSTY JOBS | Issue 2 PDF
Read more