by Imperial Systems | Apr 4, 2017 | Uncategorized
Installing a robotic welding cell collector above a robotic welder might seem like a great idea. After all, it will quickly remove all the fumes produced by the robot. Also, the collector doesn’t take up any space on your crowded shop floor. What could possibly be wrong with this setup?
Collector Installation Location
A robotic welder is an expensive piece of equipment. It’s certainly a big investment for any company. So the last thing you want to do is put it near anything that might damage it, right?
How about putting it right underneath something that might damage it?
Installing a welding fume collector above a robotic welder does save floor space. Since you mount it above the welder, it’s completely out of the way. There are some hazards with this arrangement, though, and we’ve seen them in action.
Weld fumes are almost always combustible. If the fume collector is located at some distance from the robotic welder, a deflagration that happens inside the collector will not damage the robot and will be contained in the collector. On the other hand, if you have a robotic welding cell collector mounted directly overhead, the deflagration is going to happen right above your very expensive piece of equipment.
Safeguard Your Robotic Welding Cell
A properly designed dust collection system will handle and safely vent an explosion. If the collector is outside the building, there will be minimal risk to people or property. The length of ductwork between the welder and the fume collector gives hot air and sparks time to cool down before they reach the collector.
When robotic welding cell collectors are in use, they’re inside the building and mounted overhead. There is almost no space between the source of fumes and the collector. This greatly increases the risk of a deflagration inside the collector.
This could be a disaster for your robotic welder. First of all, burning material or debris could fall on it and damage it. Also, a fire suppression system could shower your welder with water or fire extinguishing chemicals. You may have to remove your robot welder from service for costly repairs. Some events could even destroy it.
The floor space saved by mounting an extractor above the welder isn’t worth the cost of repairing or replacing a robotic welder. A robotic welding cell fume extraction system with hoods can effectively control fumes from the welder without the risk of damaging it.
Learn more about Robotic Weld Cell Fume Extraction.
Read more
by Imperial Systems | Mar 27, 2017 | Uncategorized
It’s no secret here that we love vertical dust collectors. They’re better than horizontal collectors in just about every way, which we discussed in our last post. Not all vertical dust collectors are created equal, however. Today, we’re sharing a customer’s experience with a competitor’s vertical dust collectors and why he’s choosing a CMAXX this time.
Competitive Design Prone to Corrosion
A manufacturing company approached us recently, looking to replace their current vertical cartridge collector. Since they purchased it, they’ve experienced many of the problems we often see with other dust collector brands. They even sent us these pictures to show us what they were dealing with.

Rust is a major factor for any piece of metal equipment that’s going to be outside. Exposure to the elements will occur for many years. Most vertical dust collectors that competitors such as Camfil Farr manufacture bolt together from the outside. Every external bolt hole is an opportunity for rust. In the photos, it’s easy to see where the bolt holes have rusted. Consequently, rust continues to form all over the collector.
The customer told us that they prefer the CMAXX design specifically because of experiencing this problem with their current collector. There are no external bolt holes on the CMAXX, so this is one problem they won’t have to worry about.
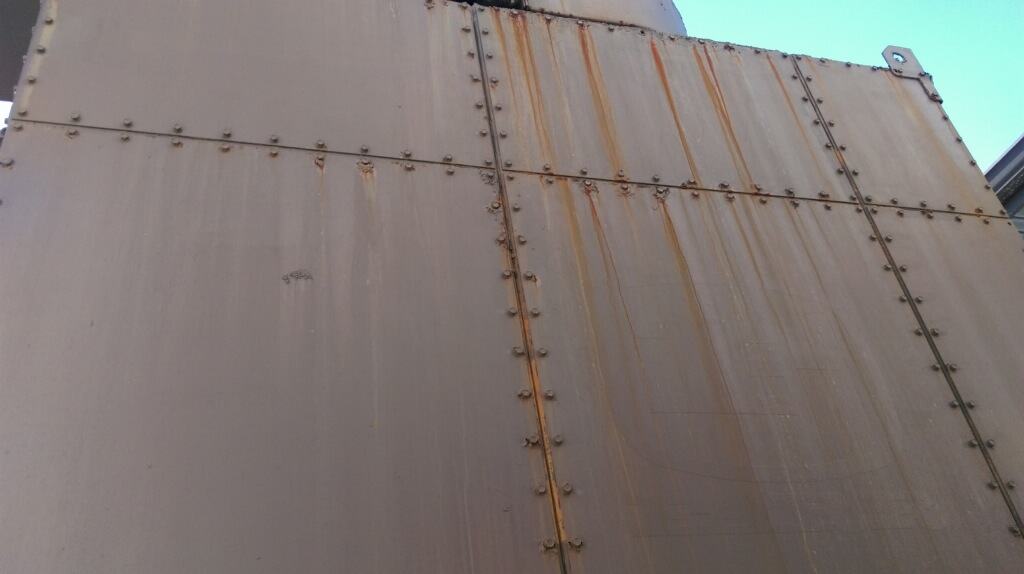
Another problem the customer has experienced with their current vertical dust collector is the roof. They have had to repaint it three times just to keep it from rusting through completely. This is a major issue because a hole in the roof allows water to get inside, wetting the cartridges. This will ruin them. The customer has had serious concerns about the roof of this collector for years. They have been struggling to keep the rust problem under control.
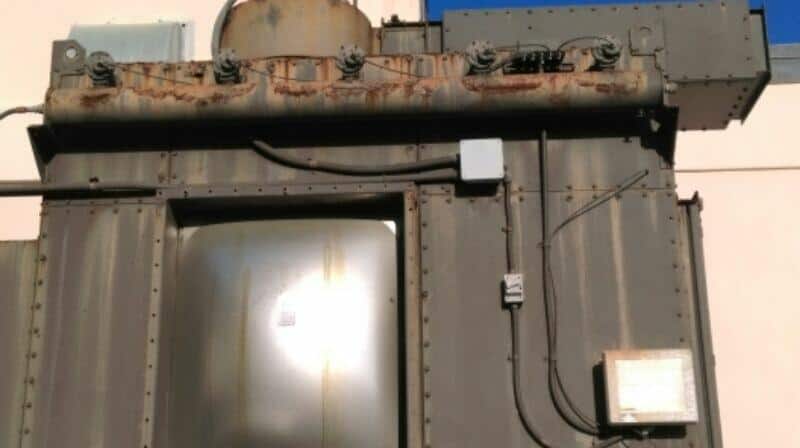
CMAXX Vertical Dust Collector Dons Crown
The customer liked the domed CrownTech roof of the CMAXX, which allows snow, water, and debris to slide off the roof instead of sitting on top. Unlike any of our competitors in the vertical dust collector market, the CMAXX is specifically designed to solve the problem of rusting on the collector roof. On a Camfil Farr or any other vertical dust collector brand, everything that falls onto the roof sits on it. Over time, this causes the roof to rust and fail.
When you choose a dust collector, you’re making a major investment. Like our customer, you’re expecting this purchase to last for many years. You know you’ll have to replace filters. You’re expecting that certain parts, like valves, may need maintenance occasionally. This is typical maintenance you’ll perform on any vertical dust collector, whether it’s a CMAXX, Camfil Farr, or any other brand. However, repairing holes in a rusting roof is something you probably didn’t plan to do. With the CMAXX design, you won’t have to.
Our customer sent us these photographs of their current collector to show us the concerns they had with it, especially the issue of rust on the roof and around external bolts. They are switching to CMAXX because its design doesn’t have these problems. With no external bolt holes and a domed roof to protect it from the weather, their new collector will give them many years of rust-free service.
Read more
by Imperial Systems | Mar 20, 2017 | Uncategorized
Horizontal dust collectors are popular. They can fit a lot of filters into a fairly small footprint. Manufacturers will tell you that they work better. In reality, horizontal filters and dust collectors have some serious design issues. Donaldson Torit may be one of the biggest names in dust collection. But there are some serious flaws in their collectors. As many owners have found out, it’s a design prone to failure.
Filters in Horizontal Dust Collectors
Donaldson knows well that there’s a major problem with having horizontal filters on top of each other in a collector. They’ve tried everything, from suggesting you rotate the horizontal filters to designing new and weird filter shapes. But they can’t get around one basic problem. It’s the fact that dust that pulses off a filter will land on the filter underneath it. With each compressed air pulse, a shower of dust falls directly down on the next layer of filters.
This problem blinds off a large part of the horizontal filter. To try to decrease the area that blinds, Donaldson has produced oval and now triangle-shaped cartridges with less surface area facing upwards. This still doesn’t solve the basic design problem. It doesn’t make sense to filter dust just to drop piles of dust on top of your filters.
Filters in a horizontal collector cannot work at full efficiency because dust from the layer above them is always partially covering them. Some horizontal collector manufacturers recommend you rotate their filters to keep the side that’s facing up from blinding… but do you want to get into your collector and rotate dust-covered filters on a regular basis?
Yokes and Gaskets
In a horizontal dust collector, metal yokes support the filters. These yokes bolt to the tube sheet on one end. As you put the filters on the yoke, the first one presses back against the tube sheet. The last filter to go in presses against the door when it closes.
There are several places for this arrangement to go wrong.
- The yokes can easily bend while putting filters on or taking them off
- Yokes can pull away from the tube sheet, causing the gasket to leak
- Weight on the yokes can pull on and warp the tube sheet itself, causing more leaks
- The gasket sealing the filter to the door can fail if the yoke is bent
- The gaskets on the door and tube sheet ends, as well as the ones between the filters, provide multiple points of failure and leaks
Doors and Access
If you look at a horizontal dust collector, the first thing you’ll see is an array of doors. They’re usually round, only a little wider than the horizontal filter that goes in them. There are usually many of them as well.
Changing filters, or accessing anything inside the collector, means trying to work through these small round doors. Filters must be pulled off the yoke, and the ones in the back are difficult to reach. There isn’t that much room to reach in or access anything through these small doors.
Comparing a horizontal and a vertical collector, it’s easy to see how all of those small, round doors are a serious design problem. A vertical collector will usually have either one or two doors. When these doors are open, they give access to the entire space inside the collector.
With the doors of a vertical collector open, you can clearly see down into the hopper, and it’s easy to inspect for problems such as bridging. With the small round doors, it’s nearly impossible to see down into the hopper.
Clean Air Plenum Access
Because of the design of a Donaldson collector, there is no direct access to the clean air plenum. There are several reasons this can be a serious problem:
- You can’t reach a leak occurring on the clean air side for repairs
- No way to do routine maintenance or checks in this space
- If a leak lets dust into the clean air plenum, there is no way to access it for cleaning
If one of the yokes gets bent, or for some other reason a gasket seal on the tube sheet fails, dust will get into the clean air plenum.
On a vertical collector like the CMAXX, it’s easy to open the doors, access the clean air plenum, and get rid of the dust.
In a Donaldson or other horizontal dust collector, accessing the clean air plenum often requires a crane to remove ductwork so you can get in and cut an access panel.
If you can’t do that, the dust in the clean air plenum will continue to get blown back into your facility over time. If it’s a health or fire hazard, this is a major issue.
What are the Advantages of Horizontal Dust Collectors?
The major advantage of a horizontal dust collector is the ability to stack filters on top of each other. This can save floor space by making the collector taller instead of wider. This is one of the major selling points of Donaldson Torit and other horizontal collectors.
Besides size, the other advantages usually listed are higher efficiency and less maintenance. These vague statements don’t really tell you much: the horizontal filters in a horizontal collector lose efficiency more quickly than in a vertical one because the tops of the filters blind off.
Also, anyone who has ever dealt with the many gaskets, easily damaged yokes, and tiny access doors might argue about the “less maintenance”. There is less to maintain on a horizontal dust collector because you cannot access most of the collector to do maintenance on it. If you do need to do maintenance or troubleshooting on the hopper or clean air plenum, you won’t have an easy time doing it.
Choosing the CMAXX
A vertical collector like the CMAXX has none of the design flaws of Donaldson Torit and similar collectors. The single gasket where the filter meets the tube sheet greatly decreases the number of places you can get a leak. The clean air plenum and hopper are easy to access.
Everything in a vertical collector is easy to access: with a large door that opens to let you reach all the filters at once, you can easily get to every part of the collector. Filters are supported by sturdy lift rails that hold the filters securely against the tube sheet.
Because the filters in a CMAXX are not stacked on top of each other, dust that is pulsed off drops straight down into the hopper, instead of landing on other filters. The filters maintain a higher efficiency over time.
With all the advantages of a CMAXX, it seems clear that it’s a better choice. The people who may appreciate it the most are the people who have to maintain the system. After all, if you’re trying to fix a problem, you’d probably rather do it through one wide-open access door than through a whole bunch of little round doors not much wider than a filter.
Read more
by Imperial Systems | Mar 6, 2017 | Uncategorized
Check out our first Issue of Dusty Jobs Newsletter. Articles include How to Troubleshoot a Diaphragm Valve Leak and story about a “greenhorn” draftsman.
[pdf-embedder url=”https://www.isystemsweb.com/wp-content/uploads/2017/03/Dusty-Jobs-Newsletter-Issue-1.pdf” title=”Dusty Jobs Newsletter Issue 1″]
Download DUSTY JOBS | Issue 1 PDF
Read more
by Imperial Systems | Feb 16, 2017 | Uncategorized
Hydraulic fracturing (“fracking”) is a process used to extract oil and gas by high-pressure fracturing of rock or shale. Exposure to respirable crystalline silica is a major hazard in this industry. Massive amounts of sand are used in the process, and silica exposure is a constant issue.
NIOSH has identified silica exposure as the single biggest health issue in hydraulic fracturing. Their research also demonstrated that silica levels on these sites are so high that standard respirators are not sufficient for protection. With a 2018 deadline for hydraulic fracturing sites to comply with new OSHA limits for silica exposure, new tactics for silica dust control are needed.
SILICA IN THE HYDRAULIC FRACTURING PROCESS
The hydraulic fracking industry uses huge amounts of sand (silica). Most grains are 2 mm or smaller in size. By some estimates, the average site requires somewhere between 1 and 7 million pounds of sand over its lifetime.
After high-pressure water and chemicals are pumped into the rocks to create fractures, the spaces must be filled with sand to keep them open and allow oil and gas to flow. So much sand is used in this industry that mining and production of “frac sand” has become a major industry of its own.
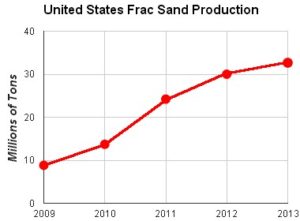
(Frac sand production: This chart illustrates the spectacular rise in the production of frac sand in the United States. Data from the United States Geological Survey Minerals Yearbook, Silica, 2011)
AREAS OF HIGH SILICA EXPOSURE
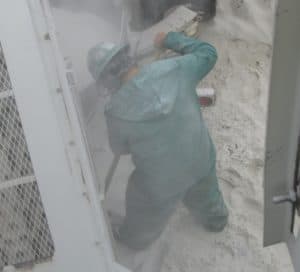
image: National Institute for Occupational Safety and Health/Centers for Disease Control and Prevention/OSHA/CDC
Massive amounts of silica move around a hydraulic fracturing site. NIOSH has identified several points in the silica moving process that create the largest amount of silica dust. These areas are:
- Open hatches on sand movers
- Through side ports on sand movers during refilling
- Depositing sand onto transfer belts
- Sand moving on transfer belts between movers, hoppers, and blenders
- Blender hoppers that mix sand
- Accumulated dust stirred up by vehicles driving around the site
NIOSH strongly recommends that engineering controls be put in place to control silica exposure at these points. They emphasize that the silica exposure at these points in the process is so heavy that respirators do not provide enough protection.
HYDRAULIC FRACTURING SILICA EXPOSURE; CONTROLLING DUST ON SITE
In some situations, newer equipment has been designed to minimize silica dust release. In other situations, older equipment can be modified or rebuilt to these designs.
For many companies, especially with the industry still recovering from the severe drop in oil prices several years ago, these expensive modifications aren’t reasonable.
Another option is to install dust collectors directly on the equipment. A collector specially designed for hydraulic fracturing equipment can be fitted on sand movers, transfer belts, and blenders. With these systems installed, the amount of silica dust released is much lower.
Controlling silica release at these points of capture can decrease silica exposure all over the site. With less silica dust escaping, the overall amount of fugitive silica dust around the site is more manageable. This helps with the amount of dust raised by vehicles or wind all over the site.
https://blogs.cdc.gov/niosh-science-blog/2012/05/23/silica-fracking/
http://geology.com/articles/frac-sand/
https://www.osha.gov/dts/hazardalerts/hydraulic_frac_hazard_alert.html
Read more
by Imperial Systems | Feb 8, 2017 | Uncategorized
Lung disease from inhaling sand or rock dust is one of the oldest occupational hazards. The health risks of silica were identified as early as 1700. Silicosis, the incurable lung disease caused by inhaling silica dust, causes hundreds of deaths every year. Other health effects also include liver and immune system diseases. OSHA concluded that the current silica exposure limits were too high after studying the research. So, they needed to set a new silica exposure limit to protect workers.
Some silica exposure still comes from well-known occupations like stone cutting, mining, and drilling. Abrasive blasting with sand is especially dangerous. However, newer industries have created new sources of exposure. One example of this is hydraulic fracturing, or fracking, for oil and gas. Another example is the popularity of natural and manufactured stone countertops. All of these industries must achieve compliance with OSHA’s new silica law to keep workers safe.
How does silica hurt you?
Silica is one of the most common elements on earth. It makes up a major part of sand, rocks, and all products made from those things, like concrete.
The major health risks of silica happen when one inhales it into the lungs. Silica that is small enough to be inhaled is called “respirable crystalline silica” in formal OSHA language. Drilling or grinding creates fine silica dust, and sand is already a form of crystalline silica that can become airborne, especially during blasting or fracking operations.
Developing Silicosis
Silicosis is a disease that causes the biggest concern with silica. The American Lung Association warns about the permanent lung damage that happens with this disease.
Silicosis happens when silica dust damages the lining of the tiny air sacs in the lungs. This injury causes scarring and makes it harder for the air sacs to get oxygen into your body.
Acute silicosis can occur within weeks or months of very heavy exposure. In this case, the lungs respond to the injury by swelling up and filling with fluid. This can be very dangerous and make it very hard to breathe.
Chronic silicosis is the most common kind. The swelling and scarring of the lungs happen over years. Symptoms include coughing, chest pain, and sometimes tiredness and weight loss. The scarring can progress to a condition called progressive massive fibrosis, where the lungs become stiff and full of scar tissue. When the disease is severe, people may need oxygen support to be able to breathe. Silicosis can cause death.
The health risks of silica include other deadly conditions. Silica is a known carcinogen, meaning it causes lung cancer. It also makes you more likely to get lung diseases like emphysema, tuberculosis or bronchitis. NIOSH, the research arm of OSHA, reviewed all of the studies on silica exposure and wrote a detailed report on it.
How can the health risks of silica be controlled?
OSHA recommends that the first line of defense is replacing silica with safer materials. This isn’t always an option. Replacement products may be expensive or just not available. Silica is common, cheap, and stable, which makes it hard to replace.
The second line of defense, and usually the best option when possible, is using engineering controls. A popular engineering control is a dust collector. A dust collection system removes silica dust from the work area and safely captures it for reuse or disposal. Just venting the dust out of the work area means that it ends up somewhere else, and that can be a problem.
A dust collector filters silica dust from the air. The dust drops into a hopper for safe handling. The air can be returned to the work area. The system can clean a large area and keep an entire facility free of silica dust.
Dust collectors can also be installed on equipment such as sand trucks or conveyors to control silica dust when moving sand around. This is important in fracking applications.
In situations like construction or drilling, the best solution may be a NIOSH-certified respirator. Because respirators are uncomfortable and difficult to fit correctly, they are not the ideal solution. Sometimes, though, they are the only option. If you must wear a respirator to protect you from the health risks of silica, make sure it is NIOSH-certified for the job you’re doing, and make sure it fits correctly.
Read more