by Imperial Systems | Sep 29, 2016 | Uncategorized
The Surprising OSHA Game That’s Actually Fun
You might actually find yourself playing this just to try for a high score. I’m not kidding. For the sake of accurate reporting, I forced myself to test out this OSHA Hazard Identification Training Tool. I even forced myself to test it more than once after I managed to crash my profits on the first try. This was solely for testing purposes and had nothing to do with being annoyed about losing.
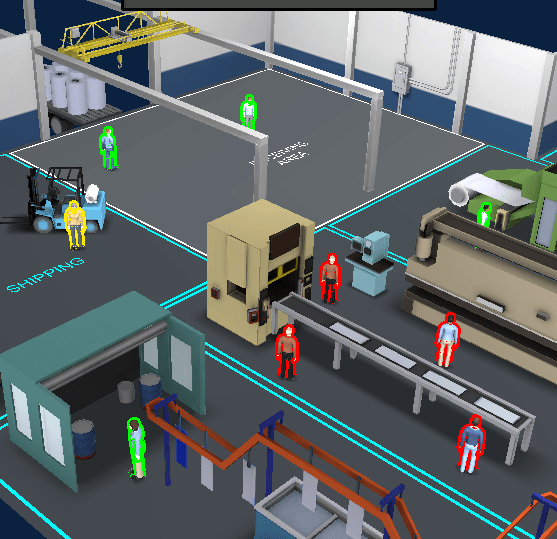
Apparently, someone at OSHA is a fan of farm or city management games, because their Hazard Identification Training Tool is really a time and resource game. This OSHA training tool focuses on three different workplaces: construction, manufacturing, and an emergency room. Most relevant for most of the companies we work with would be manufacturing, which allows you to play as either an owner or a worker in a facility that manufactures metal parts.
OSHA Training Tool Simulates Realistic Company Challenges
In the game… err, OSHA training tool … you are challenged to balance profit and safety. You have a certain number of points to spend each week on safety tasks like inspecting machines, interviewing workers, and doing research. Any points you do not use contribute to your profit. However, major safety failures also wreck your profits, so you have to make your safety investments wisely.
Wait a minute. A government agency actually recognizes that companies have to balance their safety efforts with trying to make a living?
Yes, it seems like they do. And this game provides a lot of information, with each safety step you choose getting a rating of the hazard and a choice of whether or not to spend safety points fixing it. Since there are far more possible hazards than you have safety points for each week, you have no choice but to prioritize which safety issues to deal with first and which can probably wait.
Wait another minute. They’re not telling you that you have to fix all the hazards right this minute?
No. This OSHA training tool requires you to budget both time and money. It sounds almost like real life. Fixing hazards will cost money. An incident because of a safety hazard you didn’t fix will also cost money.
Keep Safety in the Green
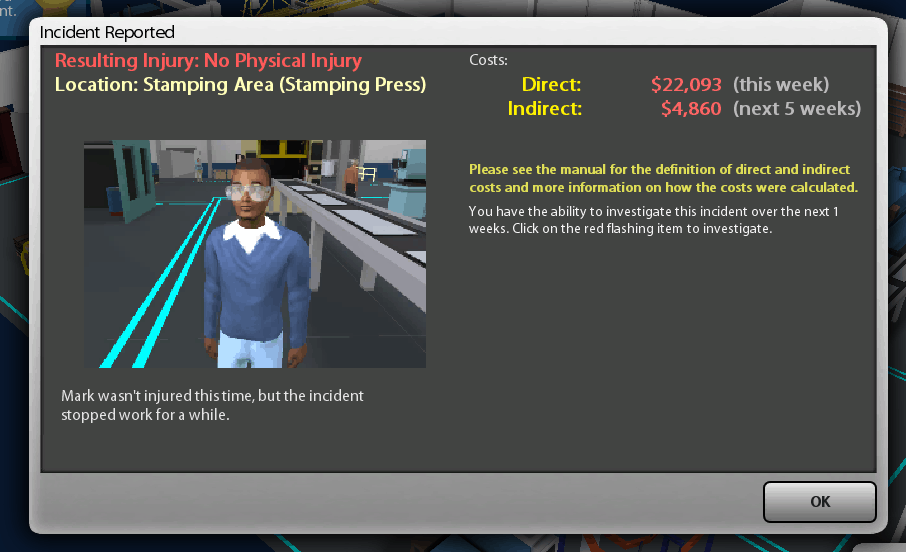
(Mark made it out OK this time, but it still took a chunk out of my profits.)
Some safety issues you’re presented with in the game are very simple to fix, like rearranging power cords so they’re not where people can trip over them. Others are more complicated, like installing machine guards, and some go all the way up to replacing broken machinery or installing engineering controls (such as a dust and fume collection system).
The best choices keep both your safety rating and your profit margin in the green. And some of them even make your job easier.
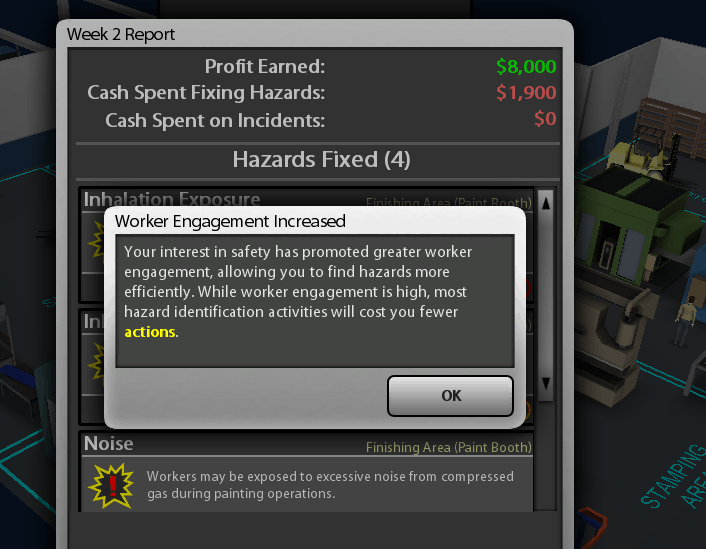
Talking to workers about the things they’re concerned about makes you better at finding hazards, so you can turn more points into profit. Workers will even report things to you so you can fix them, which is easier than finding them yourself.
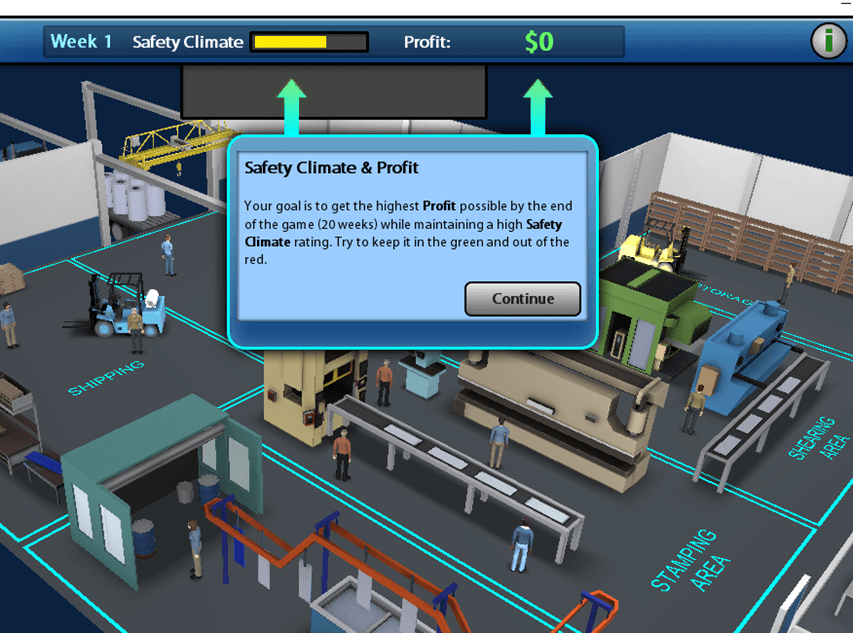
(Uh-oh… there’s apparently a hazard in the stamping area. The folks in the receiving area are pretty happy, though.)
Some of the hazards you find are minor, and some aren’t. Each of them costs money to fix but improves your safety rating. You can visually inspect a machine, watch people using it, or check the owner’s manual. You spend your money repairing exposed electrical wiring, putting up new shelving to store boxes properly, or fixing the air quality control in the paint booth. Or you can just tell them to quit playing football in the loading dock.
And best of all, how can anyone complain that OSHA training on hazard assessment is a waste of time? Clearly, this is valuable information.
Now, if they’d just improve the graphics a little… Find it here: https://www.osha.gov/hazfinder/
Read more
by Imperial Systems | Sep 27, 2016 | Uncategorized
WILL A 500% TARIFF ON CHINESE STEEL HELP OR HURT AMERICAN JOBS?
There are no easy answers. We work with many companies in the steel industry, but we also work with many companies that use steel in their manufacturing. We manufacture our own CMAXX dust and fume collectors with steel, so things that affect these industries affect us directly and indirectly. We feel that it’s important to understand all sides of this issue, since many of our customers are impacted by it.
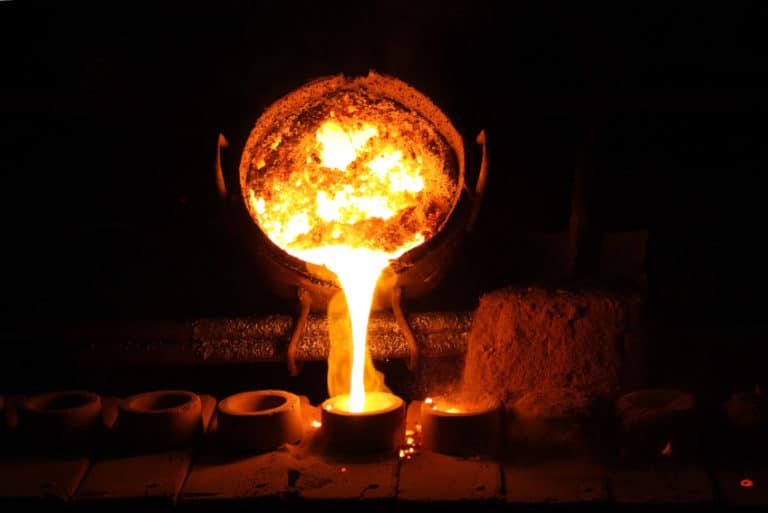
In the struggle to help American steel compete against cheaper foreign imports, the government has imposed tariffs and taxes on steel imports. With rising tensions between the US and China, the tariff on some types of imported Chinese steel has been raised to nearly 500%. It’s another round in a fight that’s been going on for decades.
When steel from overseas is made more expensive, American-made steel can be more competitive. This allows the steel industry to keep jobs that might otherwise have been lost.
On the other hand, this makes steel more expensive for industries that buy and use it. Many companies argue that while jobs in the steel production industry have been saved, more jobs in the manufacturing and construction industries may be lost due to higher costs.
It’s this conflict that led the Wall Street Journal to call the tariffs “a double-edged sword”. The steel industry supports them. Other industries, such as automotive manufacturers, feel that raising the price of steel hurts US jobs and makes products more expensive for consumers. If overseas companies have access to cheaper steel, they can make cheaper products.
It’s not just the US imposing these tariffs. The European Union did the same when China and Russia “dumped” steel into the international market, selling it at an artificially low cost to drive market prices down. The EU imposed tariffs on China, Russia, South Korea, and several other countries in response to what some people have called economic warfare.
How can China afford to “dump” steel into the market at such low prices?
China manufactures a huge chunk of the world’s steel supply. While their economy was growing and needed steel to sustain that growth, they produced a lot of steel. With the economy slowing down, China found itself producing more steel than it could use. Their solution has been to flood the market, forcing other countries to either cut production or cut prices.
Automotive manufacturers and representatives of other industries that buy and use steel have to pay more as prices go up. Representatives argue that driving up the cost of steel hurts companies and forces them to cut jobs or close their doors. The Consuming Industries Trade Action Coalition Steel Task Force announced in 2002 that the US economy lost $4 billion in jobs and wages over a ten-month period because of increased steel prices due to tariffs. The long-term effects of the more recent tariffs remain to be seen, but many are concerned that more job losses are coming. Small businesses struggle more than larger ones to handle increased costs, and many jobs lost are from this area.
The steel industry, however, needs this economic protection in order to save jobs, both in the United States and in Europe. U.S. Steel lost $1.5 billion in 2015, and there are hopes that the new tariffs will help the company and others survive. People who support the tariffs argue that prices were only low before because of the over-production of steel internationally, and that the tariffs stabilize prices where they should be.
There is not one simple answer for these problems. In a global economy, there’s no way to escape the constantly changing forces of supply and demand. If there is more steel in the worldwide market than the market demands, prices drop and countries where production is cheaper often have an advantage. Protecting jobs is a challenge when competing with countries around the world, and there isn’t one clear solution to the problem.
http://www.bloomberg.com/news/articles/2016-08-04/china-russia-hit-with-5-year-eu-anti-dumping-tariffs-on-steel
http://www.wsj.com/articles/u-s-steel-tariffs-create-a-double-edged-sword-1464740256
http://money.cnn.com/2016/03/30/news/economy/tata-steel-china/?iid=EL
http://money.cnn.com/2016/05/18/news/us-steel-china-trade/
http://www.cnbc.com/2016/05/20/china-steel-overcapacity-war.html
http://triblive.com/business/headlines/10263460-74/steel-workers-salaried
Read more
by Imperial Systems | Sep 20, 2016 | Uncategorized
NIOSH HAZARD EVALUATION: NO,YOU SHOULDN’T BREATHE POWDERED SHARK CARTILAGE
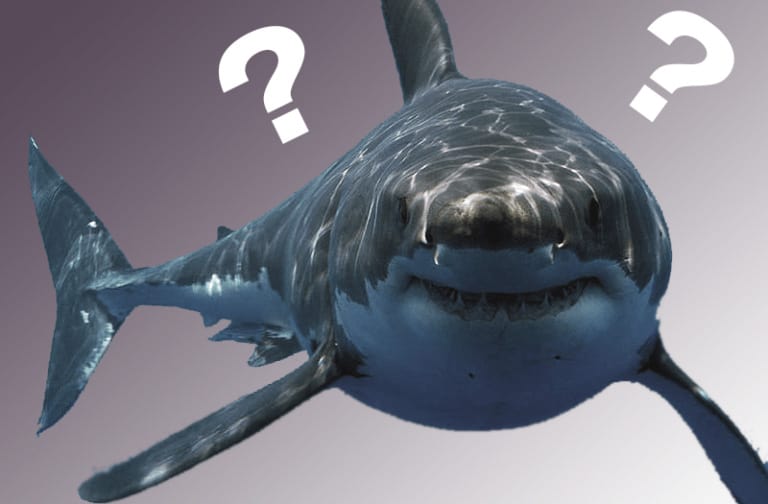
Most people would prefer to avoid having health inspectors show up at their workplace. So why were there 194 requests for health hazard evaluations in 2015 (one of which involved a facility where the concern was dust from powdered shark cartilage)?
These health hazard evaluations (HHE’s) are conducted by representatives from NIOSH. If trying to keep track of all the acronyms makes your head spin, you’re not alone, but the short answer is that NIOSH is the research and recommendation cousin of OSHA. They were both created by the same law (passed by Richard Nixon), but unlike OSHA, which makes and enforces laws, NIOSH is part of the Centers for Disease control. They do the testing and research that OSHA uses to develop regulations, but they do not have the authority to punish or fine anyone.
The fact that NIOSH does research and makes recommendations instead of punishment is why many companies are willing to work with them, and some even invite them to do a health hazard evaluation (it helps that the evaluation, including all of the testing, is free). They’re being proactive, and instead of getting fined for not addressing a problem, they’re showing everyone involved that they’re taking all efforts to solve it.
So who requests these evaluations? According to the CDC, there were 194 requests in 2015. The top three sectors requesting them were services, manufacturing, and wholesale and retail. 54% were requested by employees, 29% by management, 10% by unions, and the remaining 8% by others.
What kinds of things do these people evaluate? In industries we work with, their evaluations have included:
- Testing levels of respirable dust from an unusual source: powdered shark cartilage (while OSHA does not set a safe exposure level for powdered shark cartilage, NIOSH determined that it contained materials that cause allergic reactions)
- Testing for 31 different metals and other materials in the metal dust and fumes at a caster/slitter facility in Indiana (recommendations included sealing gaps in ventilation and providing education about respirator use)
- Assessing noise levels, poor lighting, and possible metal dust exposure in a company making wire rope in Missouri (recommendations included improved lighting and a hearing conservation program; they found that the levels of metal dust were not a problem)
- Determining exposure to styrene dust in wind turbine manufacturing (levels were higher than they should be, and changes in the process were recommended, including hoods and air quality control systems)
- Evaluating wood dust in a sawmill in Colorado (exposures to wood dust were found to be at safe levels, but noise levels were high in some areas)
These different recommendations show that NIOSH hazard evaluations aren’t targeting companies to punish them. Most of their recommendations aren’t too difficult to follow. If simple things like better lighting, hearing protection, and air quality control can keep people healthy and avoid fines at the same time, it’s information that’s worth having.
Sometimes employees or others request an evaluation because they are concerned that they’re being exposed to health risks. Sometimes a NIOSH evaluation finds that the employer needs to take steps to improve health and safety… but sometimes they find that the employees are not being exposed at unsafe levels or that the current PPE is sufficient to protect them, which can reassure them that their health is not in danger. Since the evaluation is at no cost to the company, this reassurance can be valuable for an employer as well.
This is why almost 30% of the requests for HHE’s come from management. What about the 54% that were requested by employees? An employer might not be thrilled about a visit from NIOSH, but considering that they’re there to collect data and recommend solutions, it’s not a bad thing. As long as those recommendations are followed, the HHE can serve as proof that a company cares about employee health.
http://www.cdc.gov/niosh/hhe/pdf/2015annualreport-508.pdf
https://www.cdc.gov/niosh/hhe/
https://www.cdc.gov/niosh/hhe/reports/pdfs/2008-0091-3118.pdf
https://www.cdc.gov/niosh/hhe/reports/pdfs/1998-0072-2762.pdf
https://www.cdc.gov/niosh/hhe/reports/pdfs/1993-0700-2335.pdf
Read more
by Imperial Systems | Sep 15, 2016 | Uncategorized
Correctly using PPE (personal protective equipment) can be very effective. So why does OSHA consider it a “last resort” for health and safety? Let’s take a look at PPE and engineering controls and explore what is practical for certain situations.
Viable Risk Protection
While PPE is often essential, it should only be used to protect people from risks that cannot be controlled in any other reasonable way. For example, a helmet with a face shield is often the only reasonable way to protect a welder’s face and eyes because they are often very close to the welded metal. On the other hand, a respirator is much more difficult to wear and use correctly than a welding helmet, so welding fumes are better handled by engineering controls.
Engineering controls, such as dust and fume collection, and safe work practices are more effective and protect everyone, not just the people wearing PPE.
There are a lot of reasons why PPE shouldn’t be the first line of defense in keeping people safe. Some of them are listed here: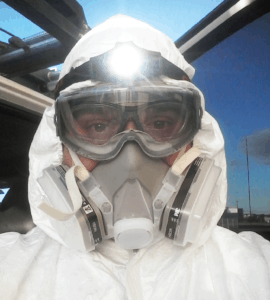
- instructions for use not given or not followed
- not fitted correctly
- appropriate PPE not provided
- is uncomfortable, hot, blocks vision, or other problems
- faces must be clean-shaven for respirators to fit properly
- makes moving around and doing job difficult
- takes too long to put on and take off
- is dirty, worn out, or otherwise not functioning as it should
- only protects the person using the PPE, not people around them
- loses, breaks, or damages the PPE
Realistically, people often don’t like PPE. It can be awkward and uncomfortable (especially in the heat) and can restrict vision and movement, make tasks more difficult, and take up a lot of time. Problems like this may keep people from using PPE, or keep them from using it as much as they should. And that’s assuming that proper PPE is always available… which it isn’t.
Engineering Controls Considered Best Workplace Strategy
Engineering controls are often the first line of defense that OSHA recommends for many exposures and other safety hazards. Basically, engineering controls modify the workplace to reduce or eliminate health and safety risks. This may include adding safety devices, enclosing equipment, source capture of dust and fumes, switching to a less dangerous chemical or process, or changing the layout of a facility. OSHA considers these to be “the first and best strategy” for health and safety in the workplace.
Dust collectors are a good example. If a process is creating dust or fumes that could harm employees, a dust collection system can remove those materials from the air completely. This reduces or eliminates the need for respirators, and the dust never has an opportunity to spread through the workplace and affect people in other areas. Dust collection systems can provide source capture at specific work areas. They can also filter the air throughout the facility, depending on the type of required system to capture the dust or fumes. Dust and fume collectors can serve an important role in overall engineering controls for safety.
References:
http://www.hsa.ie/eng/Topics/Personal_Protective_Equipment_-_PPE/PPE_-FAQs/Personal_Protective_Equipment_FAQ_Responses.html
https://www.linkedin.com/pulse/your-ppe-last-resort-has-real-limitations-terry-penney
http://www.healthyworkinglives.com/advice/work-equipment/ppe
https://www.newpig.com/expertadvice/why-osha-demands-engineering-control-first-ppe-last/
Read more
by Imperial Systems | Sep 12, 2016 | Uncategorized
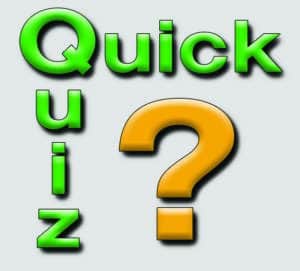
Do You Know Which Is The Rarest Metal?
The most common metal on this list – and the most common metal in Earth’s crust – is aluminum. But it’s not the rarest metal. It is the 3rd most common element in the Earth’s crust, after oxygen and silicon. There is more iron than aluminum on Earth, but a lot of the iron is in the planet’s core. Extracting aluminum from its common ore, bauxite, is a process that requires a lot of energy.
The second most common metal on the list is titanium. While it sounds somewhat exotic, it is the 9th most common element in the Earth’s crust. Most minerals have some amount of titanium in them. However, the amount is usually small, and getting a useful amount of titanium out of them is a complex process, which is why this very common metal is fairly expensive.
The third most common metal of these four is zirconium. You’ll find this metal mainly in the mineral zircon. It’s often used instead of pure metal. Using the mineral in high-temperature, corrosive applications where its resistance to damage makes it especially useful. Like titanium, you’ll find it mixed in with other minerals, and getting it out is a difficult process.
The RAREST Metal on the List is Tin
Surprised? Tin seems like the very boring metal responsible for such ordinary things as tin cans and tin foil (manufacturers don’t make these from tin anymore. The cans are steel and the foil is aluminum.). How could this element be rarer than zirconium but so much cheaper?
The reason is the cost of production. Tin can be extracted from its ore in a furnace with technology that has been in use since 3000 BC. Extracting aluminum from bauxite wasn’t economically possible until the late 1800s, and the Kroll process that is used to extract titanium and zirconium wasn’t developed until the 1920s. Because it’s very easy to get tin by itself and so difficult to separate the others, tin is rarer in Earth’s crust but much less difficult to get to.
For those concerned with combustible dust, tin is also the least explosive metal on the list (although it will burn if exposed to sparks or flame). Aluminum fires are common since aluminum dust is a byproduct of so many processes. Titanium dust is dangerously explosive, and zirconium is even more hazardous. Proper dust control and handling of scrap and dust is essential to working with these metals safely. Allowing them to accumulate can be an explosion hazard as well as a health risk.
Reference: http://www.daviddarling.info/encyclopedia/E/elterr.html
Read more
by Imperial Systems | Sep 6, 2016 | Uncategorized
Weld Smoke and Fume Dangers
Weld smoke is a direct cause of Pneumosiderosis, also known as welder’s lung. Inhaling iron dust or fumes, usually from welding, is a serious health issue. While it’s one of the most common occupational lung diseases of welders, it’s not the only one. Welders are also at risk of chronic bronchitis and cancer. Fortunately, a properly designed dust and fume collector, like our CMAXX™, can prevent these problems.
A case study from the publication Cases Journal gives an example of how welder’s lung can occur. It follows the case of a 64-year-old man who went to his doctor with a cough. He had worked as a welder in an automobile factory for 15 years, welding steel frames. The work area was small and enclosed, without a proper dust collection system to remove weld smoke and fumes.
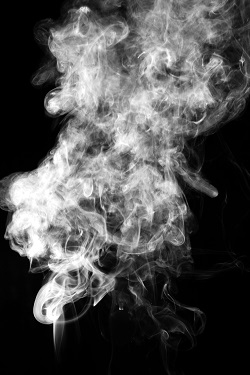
The man’s doctor found that his lung X-ray was abnormal. Tests showed that his lungs contained many white blood cells full of iron. White blood cells remove things from your lungs that don’t belong there, but large amounts of inhaled iron are too much for them to handle. This buildup of iron causes coughing, shortness of breath, and eventually chronic lung disease.
They advised the man to stop working as a welder. His doctor treated him for his symptoms, and after some time his lung function returned to normal. However, he remains at an increased risk of lung cancer as a result of his long exposure to hexavalent chromium present in the steel.
Along with welder’s lung, inhaled welding dust or fumes also causes an increased risk of cancer. Hexavalent chromium, found in the steel the man in the case study worked on, is a known carcinogen. Welding, in general, increases cancer risk.
How Do You Prevent These Risks?
Because the fumes and smoke from welding contain iron and other metals in very, very small particles, inhalation deep into the lungs is easy. Because these particles are so small, our DeltaMAXX™ nanofiber filters are efficient at removing dust as small as .3 microns, making them an excellent choice for welding and other metalworking applications.
While pneumosiderosis most often affects welders because they are usually very close to the materials they’re working with, the same problem can affect people who are exposed to fumes from laser or plasma cutting. Dust from these applications also may contain hexavalent chromium and other health hazards. Our CMAXX™ system for cutting tables can remove fumes from the air before employees are exposed to them.
The most basic way to prevent welder’s lung is to remove weld smoke and fumes from the air that welders are breathing. A dust and fume collection system like the CMAXX™ can be designed to capture fumes from individual welding stations or from the ambient air. Our systems work with you to keep welders safe and healthy. Learn more about welding fumes and cancer.
References:
www.casesjournal.biomedcentral.com
www.oem.bmj.com
www.onlinelibrary.wiley.com
www.sjweh.fi
Read more