by Imperial Systems | May 2, 2018 | Uncategorized
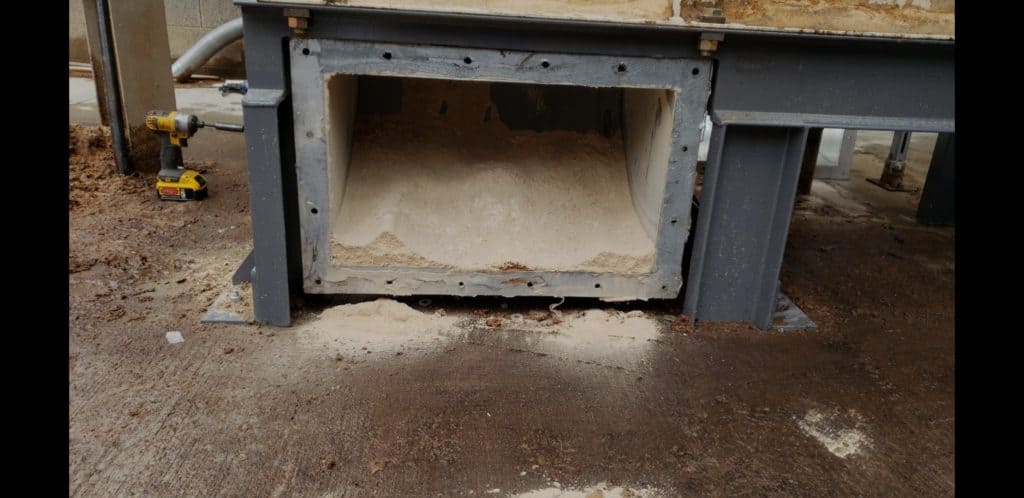
1. What information do we need to start designing a system and what are the considerations for ductwork?
- First, you need to know about your dust. Important details: how it’s being generated, how toxic or hazardous it is, what exposure levels OSHA considers to be too high, whether it is combustible and/or explosive, particulate size, physical characteristics.
- Combustible dust will certainly require special precautions in the system design to protect the facility and workers from deflagration or explosion. Dust testing can determine how explosive dust is and the needed precautions.
- A general layout of the facility and each location generating dust.
- A sketch of the ductwork layout, including the location of the dust collector, fans, and ductwork branches.
- A plan for the type of hood to use at each of the dust capture locations. Also, how much CFM each one will require.
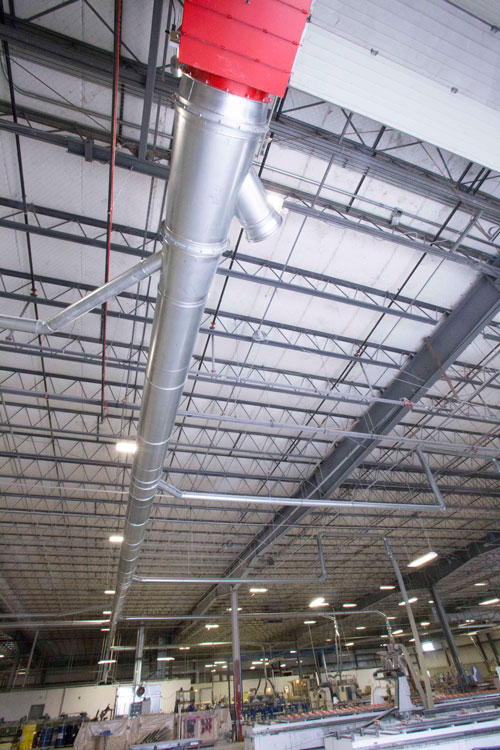
2. What are the basic components of a dust collection system?
- Hoods: must be the correct design for each type of machine. They must also be efficient at removing the produced dust by that machine.
- Ducts: must be the correct size to allow proper airflow and keep air moving. They also must not have too many bends or elbows to slow down the airflow. This can allow particulates to drop out of the airflow. It can also create a point for wear and tear on the ductwork.
- Fan: the fan must be powerful enough to keep air moving through all the ductwork at a high enough velocity. Drops in velocity or not enough velocity can allow dust to fall out of the air stream.
- Collector: must be the correct size for the system. It must have an air-to-cloth ratio that makes it able to filter all the air coming into the collector. Must have correct filter material to handle the size and type of particulate. This could be DeltaMAXX nanofiber for most applications, or spunbond, PTFE, or other specialized filters for particular applications. Further, filters must be fire-retardant if the dust is flammable.
- Fire Prevention: devices such as spark arrestors can help keep sparks from entering the dust collector. A water or chemical fire suppression system can extinguish sparks or flame when a sensor detects them.
- Venting/Exhaust: If returning air to the building, it must be clean enough to meet all health and safety standards. If dust is toxic, it may necessitate an extra layer of safety in the form of HEPA filters. A backdraft damper can prevent backdrafts from allowing dust back into the system. An abort gate with spark detector can sense a spark or flame, diverting the flame in a safe direction.
3. What is the process for designing a ductwork system?
- System design should start with identifying each place that a hood or other source capture point needs to go. In other words, anywhere that generates dust.
- Use appropriate calculations to figure out how much CFM you need at each of these points
- Determine the minimum duct velocity. This is based on the transport velocity (the airflow needed to keep your particular dust moving in the air stream).
- Calculate the size of duct for each branch. This is based on the CFM and the transport velocity and will be different for different spots along the ductwork.
- Increase duct velocity at each branch to maintain transport velocity until all branches are connected to the main duct.
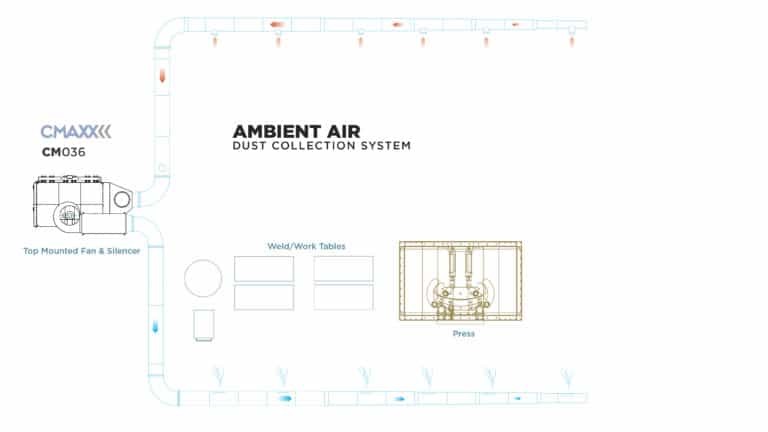
4. Will this be an ambient system or source capture system?
- Ambient system: removes air from the entire work area. It filters and recirculates it back into the area, diluting contaminated air with clean air.
- Air changes per hour: the number of times per hour that the total amount of air in the area changes. This is from old/contaminated air to new/clean. The calculation is made with the cubic volume of the work area and the number of required air changes to maintain air quality.
- Source capture/close capture: captures generated dust at each point throughout the facility.
- This type of system must have properly designed hoods at every capture point. Perform and double-check your airflow calculations. Specialty hoods can be designed for almost any application.
- Static pressure in these systems is an algebraic formula. It includes a loss at hoods, flex ducts, transitions, and straight ductwork runs. Minimal use of elbows and flex ducts in the ductwork runs will greatly improve system efficiency.
- For dangerous or toxic dust where exposure must be kept to an absolute minimum, a close capture system will keep the material from entering the air of the general workplace.
We hope this set of articles about ductwork help to answer some of your questions. Please thank the knowledgeable and experienced Charlie Miller for providing so much valuable information and sharing his wisdom.
Read more
by Imperial Systems | Apr 18, 2018 | Uncategorized
In the agricultural industry, grain dust explosions are a hazard that must be addressed. According to a report from Purdue University, grain dust explosions have occurred at a constant rate over the last ten years, with little change in the number of explosions, injuries, and fatalities. They report an average of 9.3 explosions each year over the past decade.
Since OSHA instituted Standard 29 CFR in 1988, which specifically details safety in grain handling facilities, there has been a focus on the control of what OSHA refers to as “fugitive grain dust”. Preventing grain dust explosions was a focus, including regulations on any type of “hot work” occurring in the vicinity of grain dust. The standard requires testing for combustible dust presence in all storage containers (silos, tanks, bins). It also requires thorough housekeeping procedures to keep dust from accumulating on surfaces.
Grain dust collection systems are strongly recommended, and they must be designed to resist an explosion or deflagration. Correctly designed systems can prevent an explosion from happening or prevent it from causing damage or injury.
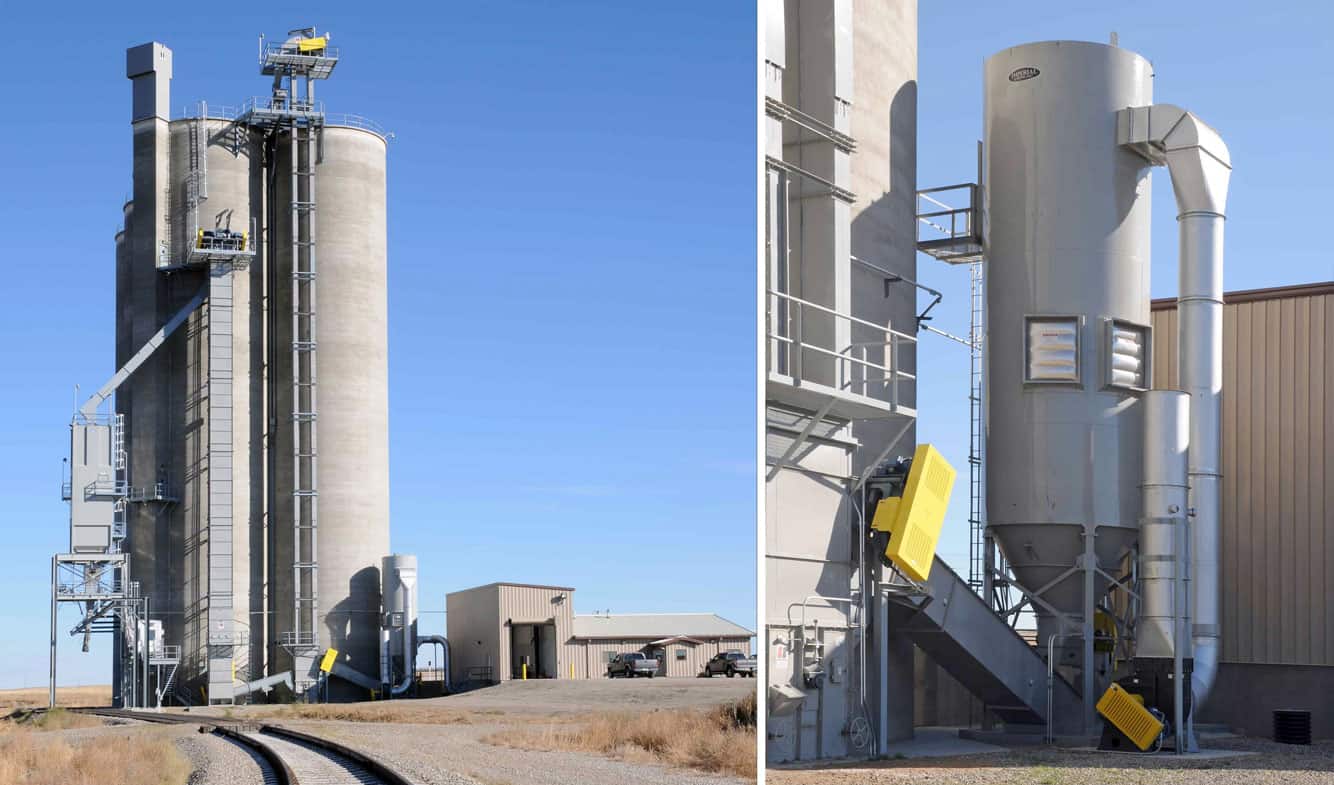
Purdue University’s report examines the number of grain dust explosions that occur each year. From 1995 to 1998 the number of explosions was high, reaching 18 grain dust explosions in 1998. Numbers stayed below the ten-year average until 2005, with 13 explosions, and then in 2008, with 19 explosions.
The most common months for grain dust explosions, according to the report, are April, August, and September. The report suggests that during these months, there is increased handling and moving of grain.
What’s causing these explosions? Some facilities think that they don’t need to worry about a little accumulated dust as long as there’s no ignition source. As our own Charlie Miller would say, “good luck with that”… in 67.8% of incidents, the ignition source was unknown. Only 6% could be related to fire, with less than 4% related to sparks or mechanical failures. Most of the time, nobody knows what triggered the explosion, which makes it very difficult to prevent an explosion when fugitive dust is present.
The high percentage of unknown ignition sources should be proof that the only prevention for grain dust explosion is to keep fugitive grain dust under control in all parts of the facility at all times. A dust collection system is essential to this, and can include a baghouse, a cartridge collector, or spot filters located at specific grain handling points.
Some other interesting statistics related to combustible dust explosions in the grain industry:
From 2007 to 2016, there were 91 dust explosions, and 52 of those were caused by corn dust. The second most hazardous type was mixed feed, which probably includes corn quite often, with 19 explosions. 20 explosions out of 91 were caused by other types of dust.
In 2017, there were 7 grain dust explosions, slightly below the ten-year average of 9. The locations included a pet food plant, a grain mill, and 5 grain elevators. Grain elevators move large quantities of grain and create a high risk of explosion.
In the last ten years, there have been 101 injuries and 15 fatalities due to grain dust explosions. 55 of the explosions occurred in grain elevators, with feed mills a distant second at 18.
If grain elevators are so hazardous, how can the risk be decreased? Spot filters are often a very good solution for dust control on these facilities. They can be placed almost anywhere that dust is generated and are self-cleaning, requiring only occasional maintenance. They do not require confined space permits to work in and can control fugitive grain at the source.
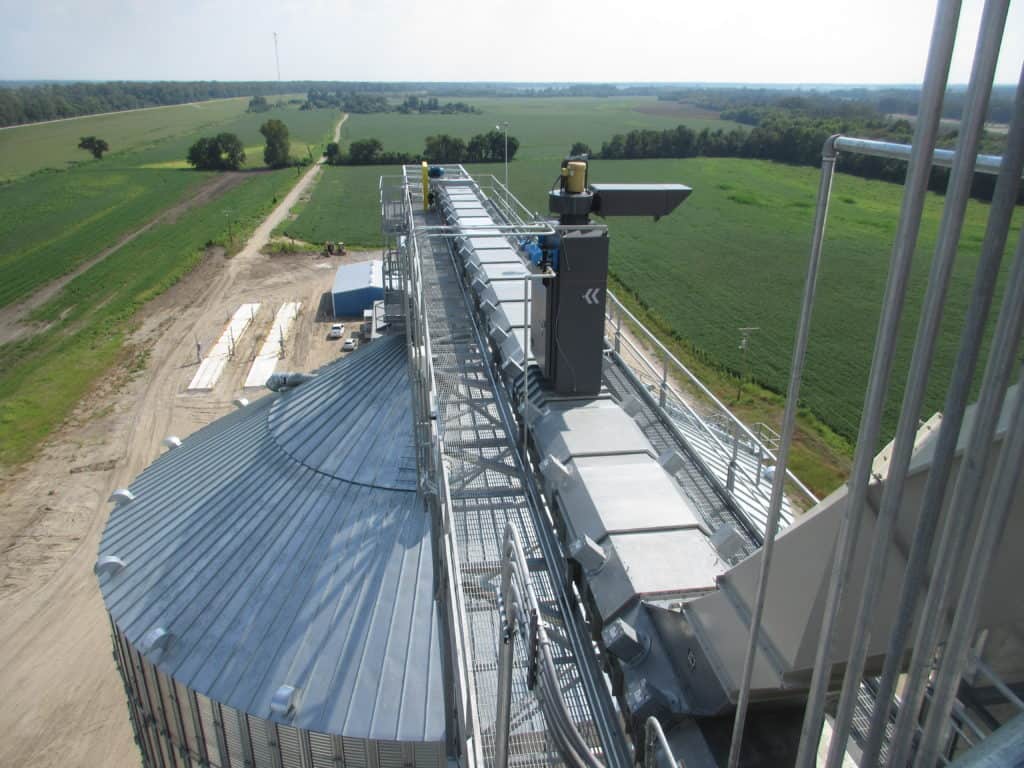
https://engineering.purdue.edu/FFP/research/dust-explosions/Grain_Dust_Explosions_2017.pdf
Read more
by Imperial Systems | Aug 29, 2016 | Uncategorized
Read these 5 odd metal facts about Tin that you never thought about…and will always remember:
- TIN PEST: At around -20 degrees F, tin will transform itself from a shiny, flexible metal to a dull, brittle powder. This is called “tin pest” and can cause things made of tin to crumble to dust when the weather gets very cold.
- WHISKERS: Pure tin used in electronics is known to grow “whiskers”. These whiskers, which form for unknown reasons, cause havoc in systems where they can act like a tiny antenna, damage delicate parts, or cause short circuits.
- TIN CANS: Tin cans aren’t made of tin. They are made of steel. The steel is sometimes coated with tin to improve corrosion resistance, but cans made out of tin were not only more expensive but also subject to “tin pest”, which made the cans brittle and breakable.
- TIN CRY: There’s a distinctive whining cry that is heard when a piece of tin is bent. This “tin cry” happens because the metal is made up of very tiny crystals, and bending the metal causes the crystals to scrape against each other.
- THE BRONZE AGE: Two thousand years before iron came into common use, bronze was the metal that revolutionized weapons, art, and civilization. This alloy of copper and tin was so superior to any other metal in use at the time that its discovery ushered in the Bronze Age.
http://periodic.lanl.gov/50.shtml
http://www.lenntech.com/periodic/elements/sn.htm
Read more